Section 1: Introduction to Metal Sintering
Metal sintering is a pivotal process in manufacturing precision components, utilizing powdered metals to create durable and complex parts. This article explores the various facets of metal sintering, highlighting its applications, benefits, and the expertise offered by Welleshaft as a leading global supplier in this field.
1.1. Understanding the Metal Sintering Process
Metal sintering involves compacting and forming metal powders under controlled temperatures and pressures. This process results in sintered metal parts that exhibit high strength, precision, and often intricate geometries that are difficult to achieve through traditional manufacturing methods.
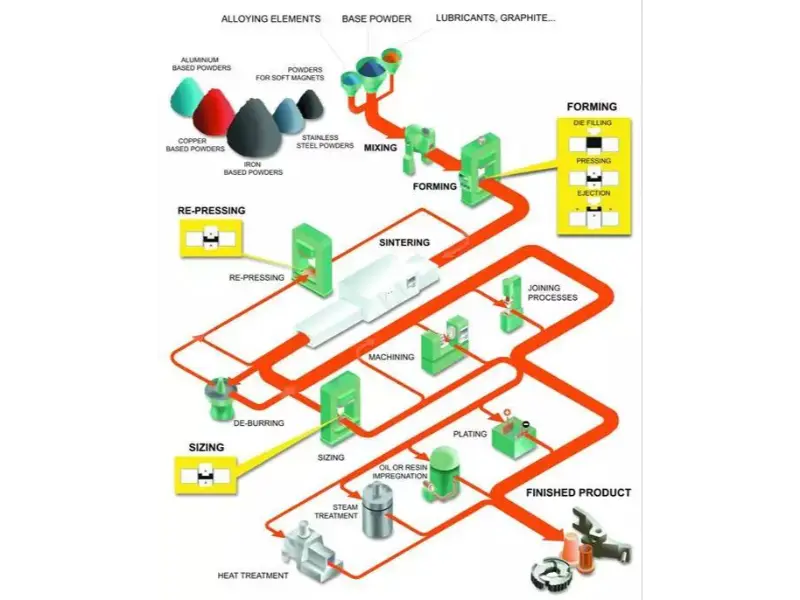
Section 2: Types of Metal Sintering Processes
Metal sintering encompasses various methods, each suited to different applications and requirements. Understanding these processes can help in selecting the most appropriate technique for your specific needs. Here are the primary types of metal sintering processes:
2.1. Powder Bed Laser Sintering (PLS)
Powder Bed Laser Sintering involves using a high-powered laser to selectively fuse metal powders layer by layer according to a digital 3D model. This additive manufacturing technique is highly precise and suitable for creating complex geometries and intricate designs that would be challenging to achieve through traditional methods.
Key Features:
Precision: Capable of producing components with intricate details and high dimensional accuracy.
Customization: Ideal for custom parts and prototypes due to its flexibility and rapid iteration capabilities.
Applications: Widely used in aerospace, medical devices, and high-performance automotive components.
2.2. Loose Powder Sintering
Loose Powder Sintering is a process where metal powders are compacted into molds and then heated to a temperature below their melting point. The heat causes the powder particles to fuse together, forming a solid piece.
Key Features:
Simplicity: Easier to set up compared to other sintering processes and less equipment-intensive.
Material Efficiency: Minimizes waste by using powder efficiently and creating dense, durable parts.
Applications: Commonly used for producing components like gears, filters, and structural elements in various industries.
2.3. Powder Injection Molding (PIM)
Powder Injection Molding combines metal powders with a binder to create a feedstock that can be injected into molds. After molding, the binder is removed, and the remaining metal component is sintered.
Key Features:
Complex Shapes: Allows for the creation of complex geometries and detailed designs.
High Production Rates: Suitable for high-volume production due to its efficiency in molding and sintering.
Applications: Often used in consumer goods, automotive parts, and electronics.
2.4. Hot Isostatic Pressing (HIP)
Hot Isostatic Pressing involves placing the metal powder in a sealed container and subjecting it to high temperature and pressure simultaneously. This process densifies the powder and eliminates porosity, resulting in high-strength, uniform components.
Key Features:
Density and Strength: Produces components with superior mechanical properties and minimal porosity.
Uniformity: Ensures consistent material properties throughout the part.
Applications: Frequently used for critical components in aerospace, defense, and medical industries.
2.5. Sinter-HIP (SHHIP)
Sinter-HIP combines sintering and HIP in a single step, offering the benefits of both processes. The component is sintered in an atmosphere-controlled furnace and then subjected to high pressure and temperature in a HIP chamber.
Key Features:
Enhanced Properties: Combines the benefits of sintering and HIP to produce parts with excellent mechanical properties and minimal defects.
Efficiency: Reduces production time by integrating two processes into one.
Applications: Suitable for high-performance applications where both precision and strength are critical.
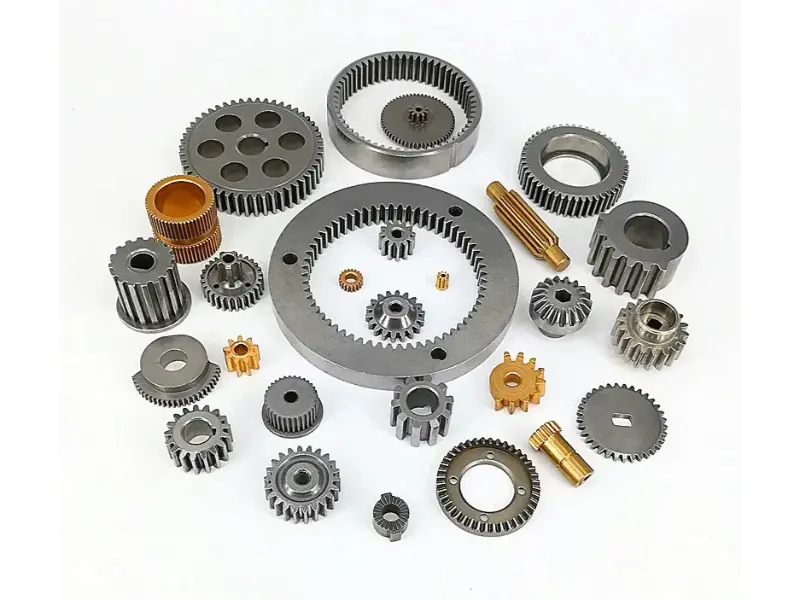
Section 3: Sintering Temperature and Control
The success of the metal sintering process heavily relies on precise temperature control. Sintering temperature is a critical factor that influences the quality and properties of the final component. Here’s an in-depth look at how sintering temperature is managed and its impact on the final product.
3.1. Understanding Sintering Temperature
Sintering Temperature is the specific heat level at which metal powders are heated to bond together without melting. This temperature is typically just below the metal’s melting point. Properly managing this temperature ensures that the metal particles fuse together to form a dense, solid material while avoiding excessive melting that could deform the part or degrade its properties.
Key Aspects:
- Temperature Range: The optimal sintering temperature depends on the type of metal or alloy being used. For example, steel powders are often sintered at temperatures between 1100°C and 1250°C, while high-temperature materials like tungsten may require even higher temperatures.
- Material-Specific Needs:Different metals and alloys have unique sintering requirements. For instance, copper-based powders may require lower sintering temperatures compared to iron-based powders.
3.2. Temperature Control Mechanisms
Effective temperature control is essential to achieve the desired properties in sintered metal components. Here are some mechanisms and practices used to maintain precise temperature control:
3.2.1. Furnace Temperature Control
Modern sintering furnaces are equipped with advanced temperature control systems that monitor and regulate the temperature throughout the sintering cycle. These systems ensure that the furnace maintains a consistent temperature profile, crucial for achieving uniform sintering results.
Features:
Thermocouples: Sensors that measure the temperature inside the furnace and provide real-time data for adjustments.
PID Controllers: Proportional-Integral-Derivative controllers that adjust the furnace heating elements based on temperature feedback to maintain stability.
3.2.2. Atmosphere Control
The sintering process often requires specific atmospheric conditions to prevent oxidation and other chemical reactions. Controlling the atmosphere inside the furnace is crucial for producing high-quality components.
Atmosphere Types:
Inert Gases: Such as argon or nitrogen, used to prevent oxidation of the metal powders during sintering.
Reducing Atmospheres: Such as hydrogen, used for metals like copper to remove oxides and enhance bonding.
3.2.3. Heating Rate and Soaking Time
The rate at which the temperature increases and the duration at which it is maintained (soaking time) are important for achieving optimal sintering. Gradual heating helps prevent thermal shock and ensures uniform powder bonding.
Considerations:
Heating Rate: Slow and controlled heating rates are preferred to allow for uniform thermal expansion and reduce the risk of defects.
Soaking Time: Maintaining the sintering temperature for an adequate period allows for complete bonding and densification of the metal powders.
3.3. Impact of Sintering Temperature on Metal Properties
The sintering temperature directly affects the mechanical and physical properties of the final product. Here’s how:
3.3.1. Density and Strength:
Higher sintering temperatures generally result in greater density and strength of the final component. However, excessive temperatures can lead to over-sintering, which might cause deformation or loss of desired material properties.
3.3.2. Porosity:
Properly controlled sintering temperatures help reduce porosity by ensuring that metal particles fuse effectively without creating voids. High porosity can weaken the component and affect its performance.
3.3.3. Microstructure:
Sintering temperature influences the microstructure of the sintered metal, including grain size and phase distribution. Achieving the correct temperature is crucial for optimizing these microstructural characteristics to meet specific application requirements.
Section 4: Benefits of Metal Sintering
4.1.Precision and Complexity
Metal sintering enables the creation of intricate designs and complex geometries that are otherwise challenging with traditional machining methods. This capability reduces assembly requirements and enhances product performance.
4.2.Material Efficiency
Sintering minimizes material waste by utilizing powdered metals efficiently. This eco-friendly aspect of the process aligns with sustainable manufacturing practices, reducing overall production costs.
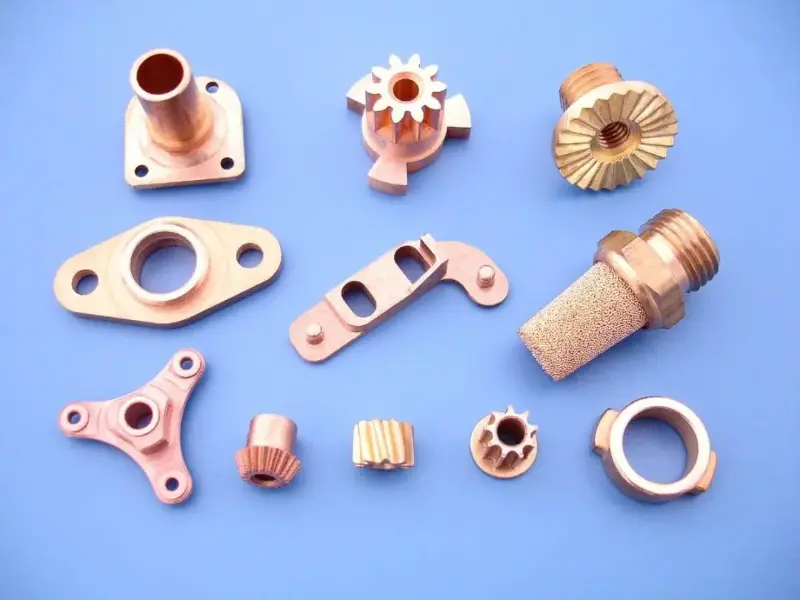
Section 5: Examples of Sintered Metals
Sintered metals are used across various industries due to their unique properties and manufacturing advantages. Here are some common examples of sintered metals and their applications:
5.1. Stainless Steel
Stainless Steel is one of the most widely used sintered metals, known for its corrosion resistance, strength, and durability. Sintered stainless steel components are often used in environments where high strength and resistance to harsh conditions are required.
Applications:
Automotive Components: Such as gears, bearings, and exhaust system parts.
Medical Devices: Including surgical instruments and implants.
Industrial Equipment: Like filters, pumps, and valve seats.
5.2. Tungsten Carbide
Tungsten Carbide is a high-performance sintered metal known for its exceptional hardness and wear resistance. This material is ideal for applications where extreme hardness and durability are essential.
Applications:
Cutting Tools: Including drill bits, milling cutters, and inserts for machining.
Mining Tools: Such as rock drills and cutting surfaces for excavation equipment.
Jewelry: Particularly in high-end rings and other wear-resistant accessories.
5.3. Copper-Based Alloys
Copper-Based Alloys, including bronze and brass, are sintered to create components with excellent thermal and electrical conductivity. These alloys are used in various applications where high conductivity and machinability are important.
Applications:
Electrical Connectors: Such as terminals and connectors used in electronic devices.
Heat Exchangers: Components that require efficient heat transfer.
Industrial Machinery: Including gears, bearings, and bushings.
5.4. Iron-Based Alloys
Iron-Based Alloys, including various grades of steel, are commonly sintered for their good mechanical properties and cost-effectiveness. These alloys are used in a wide range of applications due to their strength and versatility.
Applications:
Automotive Parts: Such as clutch plates, transmission gears, and brake components.
Home Appliances: Including parts for washing machines, dryers, and refrigerators.
Industrial Tools: Like hand tools and cutting tools.
5.5. Aluminum Alloys
Aluminum Alloys are sintered to produce lightweight components with good strength and resistance to corrosion. Sintered aluminum parts are valued for their reduced weight and ease of machining.
Applications:
Aerospace Components: Including structural parts and fittings where weight reduction is critical.
Consumer Electronics: Such as housings for laptops and smartphones.
Automotive Parts: Including lightweight structural components and engine parts.
5.6. Nickel-Based Superalloys
Nickel-Based Superalloys are sintered for applications requiring exceptional resistance to high temperatures and corrosive environments. These alloys are used in extreme conditions where standard materials would fail.
Applications:
Gas Turbines: Components such as blades and vanes in aircraft engines.
Power Generation: Parts used in high-temperature sections of power generation turbines.
Chemical Processing: Components exposed to harsh chemical environments.
Welleshaft: Your Trusted Partner in Metal Sintering
Welleshaft is renowned for its expertise in delivering high-quality sintered metal components tailored to precise customer specifications. With over 13 years of experience, Welleshaft offers comprehensive solutions from design optimization to final production, ensuring superior performance and reliability in every component.
Conclusion
In conclusion, metal sintering is a transformative manufacturing process that continues to revolutionize industries by producing durable and intricate components. Welleshaft’s commitment to excellence and innovation makes them a preferred choice for businesses seeking reliable metal sintering solutions globally.
Great article! I really appreciate the clear and detailed insights you’ve provided on this topic. It’s always refreshing to read content that breaks things down so well, making it easy for readers to grasp even complex ideas. I also found the practical tips you’ve shared to be very helpful. Looking forward to more informative posts like this! Keep up the good work!