Expert Metal Injection Molding Aluminum Services | Precision & Quality Manufacturing
In today’s highly competitive manufacturing landscape, finding the right technology and supplier for your metal components is crucial. Metal injection molding (MIM) has emerged as a groundbreaking process for producing high-quality, complex aluminum parts with precision. As industries continue to evolve, the demand for lightweight and durable components has made aluminum a preferred material. Welleshaft, a leader in global manufacturing, offers expert metal injection molding aluminum services, combining precision and quality to meet the exacting demands of various industries.
Section 1: What is Metal Injection Molding Aluminum?
Metal Injection Molding (MIM) is an advanced manufacturing process that allows for the production of intricate and high-strength metal parts by injecting a metal powder and binder mixture into a mold. This process is particularly effective for producing aluminum components, as it allows for complex geometries and fine details that are challenging to achieve with traditional methods.
1.1. Key Advantages of Metal Injection Molding Aluminum
- Precision:MIM allows for the production of aluminum parts with tight tolerances and fine details, making it ideal for complex components.
- Material Efficiency:The process minimizes material waste, making it a cost-effective solution for high-volume production.
- Versatility:MIM can be used to produce parts for various industries, including automotive, aerospace, medical devices, and electronics.
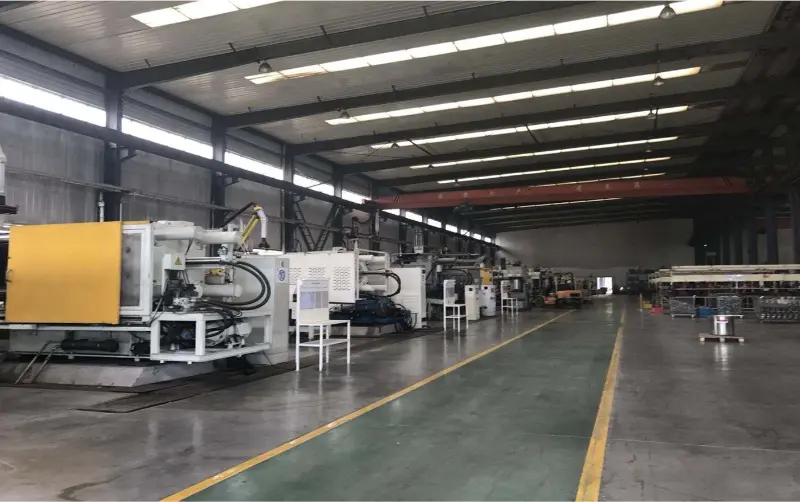
Section 2: Thixomolding Aluminum: A Revolutionary Process
The manufacturing industry is constantly evolving, seeking new methods to enhance the quality, efficiency, and sustainability of materials used in various applications. One such breakthrough is thixomolding aluminum, a revolutionary process that combines the best aspects of plastic injection molding with the unique properties of semi-solid metals.
2.1. What is Thixomolding?
Thixomolding is a manufacturing process that involves injecting semi-solid metal alloys into a mold, similar to plastic injection molding. The term “thixo” refers to the thixotropic behavior of materials, where they become less viscous when sheared or stirred. In the context of aluminum, thixomolding involves heating the metal alloy to a semi-solid state, where it exhibits both solid and liquid characteristics. This unique state allows the material to be molded with high precision and minimal waste.
2.2. The Thixomolding Process
2.2.1. Material Preparation:
The process begins with the selection of a suitable aluminum alloy, which is then heated to a temperature where it becomes partially liquid and partially solid. This temperature is carefully controlled to ensure the material remains in a semi-solid state.
2.2.2. Injection Molding:
The semi-solid aluminum is then injected into a mold using specialized thixomolding machines. These machines are designed to handle the unique properties of semi-solid metals, allowing for precise control over the injection process.
2.2.3. Solidification and Cooling:
Once the aluminum is injected into the mold, it quickly solidifies, forming a dense and high-quality part. The cooling process is faster than traditional casting methods, reducing cycle times and increasing production efficiency.
2.3. Why Choose Thixomolding for Aluminum Components?
2.3.1. Enhanced Mechanical Properties:
Thixomolded aluminum parts exhibit superior mechanical properties compared to those produced through traditional casting or forging. The semi-solid state of the material allows for a more uniform grain structure, resulting in higher strength and better durability.
2.3.2. Precision and Complexity:
Thixomolding enables the production of complex and intricate parts with tight tolerances. The process allows for the creation of thin-walled sections, intricate geometries, and fine details that would be difficult or impossible to achieve with conventional methods.
2.3.3. Reduced Waste and Environmental Impact:
The thixomolding process is highly efficient, with minimal material waste. Since the aluminum is injected in a semi-solid state, there is less shrinkage and fewer defects, reducing the need for secondary machining. Additionally, the process is energy-efficient, contributing to a lower carbon footprint.
2.3.4. Cost-Effective Production:
Thixomolding can be more cost-effective than traditional methods, especially for high-volume production runs. The ability to produce complex parts in a single step reduces the need for multiple manufacturing processes, leading to lower labor and material costs.
2.4. Applications of Thixomolded Aluminum
Thixomolding aluminum is used in a wide range of industries, including automotive, aerospace, electronics, and medical devices. Its ability to produce lightweight, strong, and precise components makes it ideal for applications where performance and reliability are critical.
2.4.1. Automotive Industry:
Thixomolded aluminum parts are used in various automotive components, such as engine blocks, transmission housings, and suspension parts. The process allows for the production of lightweight yet durable parts that contribute to improved fuel efficiency and vehicle performance.
2.4.2. Aerospace Industry:
In the aerospace industry, thixomolded aluminum is used to create components that require high strength-to-weight ratios, such as structural parts and brackets. The precision and reliability of thixomolding make it an ideal choice for aerospace applications.
2.4.3. Electronics and Medical Devices:
Thixomolding is also employed in the production of electronic housings, connectors, and medical device components. The process allows for the creation of parts with intricate details and thin walls, which are essential for these industries.
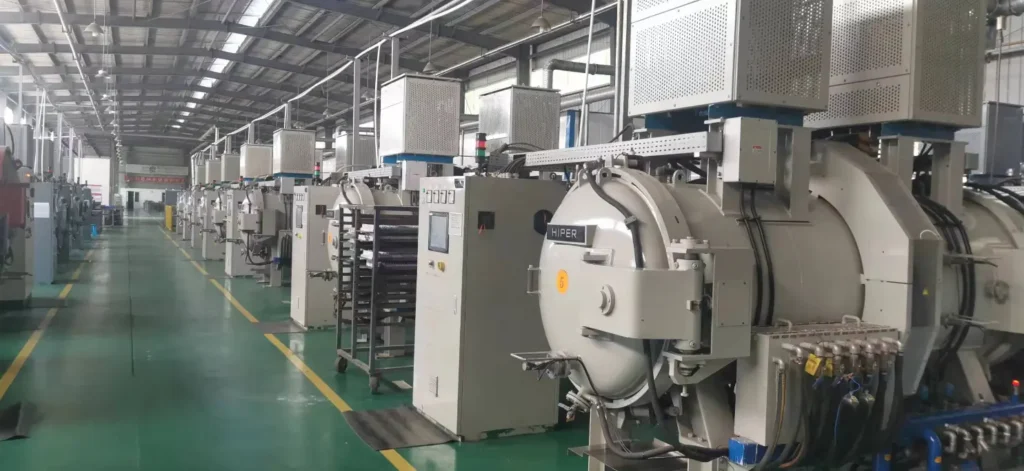
Section 3: Injection Casting Aluminum: Combining the Best of Both Worlds
Injection casting is another process that combines the benefits of traditional casting with injection molding techniques. It involves injecting molten aluminum into a mold to create parts with high precision and minimal waste.
3.1. What is Injection Casting?
Injection casting is a hybrid manufacturing process that integrates the principles of die casting and injection molding. It involves injecting molten aluminum into a mold under high pressure, similar to the injection molding of plastics. The process is designed to produce high-quality parts with complex geometries, tight tolerances, and excellent surface finishes.
3.2. Injection Casting Aluminum vs. Metal Injection Molding
Cost: Metal injection molding aluminum cost can be higher than injection casting due to the precision and material efficiency involved.
Applications: Injection casting is often used for larger, simpler components, while MIM is preferred for smaller, more complex parts.
Surface Finish: MIM typically produces a smoother surface finish, reducing the need for post-processing.
Section 4: Understanding the Metal Injection Molding Aluminum Price
The cost of metal injection molding aluminum parts depends on several factors, including the complexity of the design, the volume of production, and the material grade used. While MIM may have a higher initial cost compared to other manufacturing methods, the long-term benefits, such as reduced material waste and high precision, often outweigh the initial investment.
4.1. Factors Influencing Metal Injection Molding Aluminum Cost
Design Complexity: More intricate designs may require more complex molds, increasing the overall cost.
Material Grade: The grade of aluminum used can significantly impact the price, with higher grades typically costing more.
Production Volume: Higher production volumes can reduce the per-unit cost, making MIM a cost-effective solution for large-scale manufacturing.
4.2. Cost Comparison: MIM Aluminum vs. Other Manufacturing Processes
When evaluating the cost of MIM aluminum, it’s important to compare it with other manufacturing processes like die casting, CNC machining, or traditional powder metallurgy.
4.2.1. Die Casting:
Cost Efficiency: Die casting can be more cost-effective for large-volume production of simpler parts. However, MIM aluminum offers better precision and the ability to produce more complex geometries without the need for extensive machining.
Material Waste: MIM typically results in less material waste compared to die casting, which can be a cost-saving factor, especially for high-value aluminum alloys.
4.2.2. CNC Machining:
High Precision: CNC machining is known for its precision and versatility, but it can be costly for producing small, complex parts, especially in high volumes. MIM aluminum offers a more cost-effective solution for intricate designs that would be expensive to machine.
Material Utilization: MIM has better material utilization compared to CNC machining, where significant material may be lost as chips during the machining process.
4.2.3. Traditional Powder Metallurgy:
Complexity: While traditional powder metallurgy is cost-effective for simple parts, it falls short in producing complex geometries with the same precision as MIM. For complex aluminum parts, MIM offers better value despite the higher initial costs.
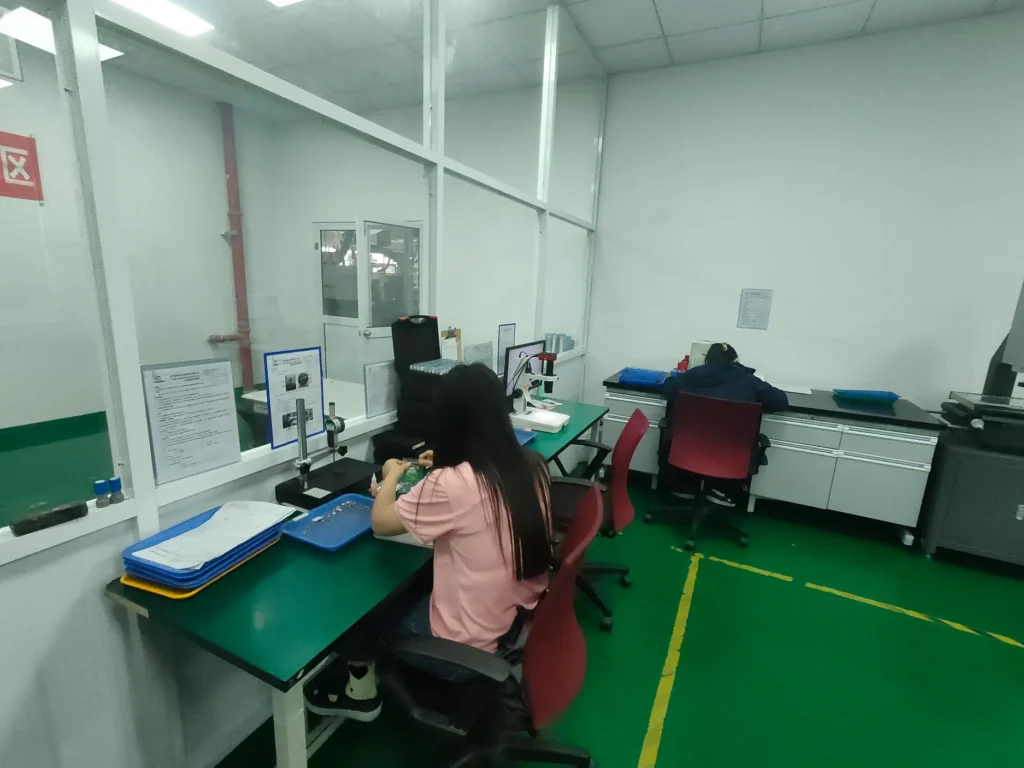
Section 5: Metal Injection Molding Aluminum Suppliers: Why Choose Welleshaft?
Selecting the right supplier is crucial to ensuring the success of your manufacturing project. Welleshaft stands out as a trusted global supplier and contract manufacturer, offering expert metal injection molding aluminum services.
Why Partner with Welleshaft?
- Experience and Expertise: With years of experience in the industry, Welleshaft has the technical expertise to handle even the most complex projects.
- Quality Assurance: Welleshaft adheres to strict quality control measures, ensuring that every part meets the highest standards of precision and durability.
- Global Reach: As a global supplier, Welleshaft has the resources and capabilities to serve clients around the world, delivering high-quality aluminum components on time and within budget.
Section 6: Metal Injection Molding vs. Die Casting: Which is Right for You?
When deciding between metal injection molding and die casting, it’s essential to consider the specific requirements of your project. Both processes have their advantages, but they are suited to different applications.
6.1. Metal Injection Molding Aluminum
Precision: Ideal for producing small, complex parts with tight tolerances.
Material Efficiency: Minimizes waste, making it a more sustainable option for high-volume production.
Surface Finish: Typically results in a smoother surface finish, reducing the need for additional processing.
6.2. Die Casting
Cost-Effective for Larger Parts: Die casting is often more cost-effective for producing larger components.
Faster Production Times: Die casting can produce parts more quickly, making it suitable for high-speed production environments.
Suitable for Simpler Designs: While die casting can produce complex parts, it is generally more suitable for simpler designs with fewer intricate details.
Section 7: Frequently Asked Questions (FAQs)
1.Can Aluminum Be Metal Injection Molded?
Yes, aluminum can be metal injection molded. The process involves mixing aluminum powder with a binder, injecting it into a mold, and then sintering it to form a solid component. This allows for the production of complex and high-strength aluminum parts.
2.Can You Injection Mold Aluminum?
Yes, aluminum can be injection molded using processes like metal injection molding and thixomolding. These processes allow for the production of intricate aluminum parts with high precision.
3.What Grade of Aluminum is Used for Injection Molding?
Various grades of aluminum can be used for injection molding, depending on the application. Common grades include 6061 and 7075, which offer a good balance of strength, machinability, and corrosion resistance.
4.What Materials Can Be Metal Injection Molded?
In addition to aluminum, several other metals can be metal injection molded, including stainless steel, titanium, and copper. The choice of material depends on the specific requirements of the application, such as strength, weight, and corrosion resistance.
Conclusion: Partner with Welleshaft for Precision and Quality
When it comes to metal injection molding aluminum, Welleshaft is your trusted partner. With a commitment to precision, quality, and customer satisfaction, Welleshaft delivers top-notch aluminum components that meet the demands of various industries. Whether you’re looking for metal injection molding, thixomolding, or injection casting services, Welleshaft has the expertise and resources to bring your project to life.
Contact Welleshaft today to learn more about how our expert metal injection molding aluminum services can benefit your next manufacturing project.