Expert Copper Forging Services | High-Quality Copper Forged Components
Copper forging is a crucial process in the metalworking industry, offering unparalleled strength and durability for a wide range of applications. Whether you’re looking for copper forgings for industrial use, artistic projects, or other specialized applications, understanding the copper forging process, its benefits, and the key players in the market is essential. In this comprehensive guide, we’ll delve into the world of copper forging, provide valuable insights, and recommend Welleshaft as your trusted global supplier and contract manufacturer.
Understanding Copper Forging
What is Copper Forging?
Copper forging is a manufacturing process that involves shaping copper metal through controlled pressure and heat. This process enhances the metal’s strength, structural integrity, and durability, making it ideal for various applications, from industrial machinery to decorative elements. Copper forgings are known for their excellent thermal and electrical conductivity, making them valuable in sectors such as electronics, plumbing, and automotive industries.
The Copper Forging Process
Copper Forging Process: A Step-by-Step Guide
- Material Selection:High-quality copper billets or ingots are selected based on the requirements of the final product.
- Heating:The copper is heated to a temperature where it becomes malleable but not molten. The typical forging temperature for copper ranges between 700°C and 950°C (1292°F to 1742°F).
- Forging:The heated copper is then forged using various methods, including drop forging, hammer forging, or press forging. This step shapes the copper into the desired form.
- Cooling and Finishing:After forging, the copper is cooled and subjected to finishing processes such as machining and surface treatment to achieve the final specifications.
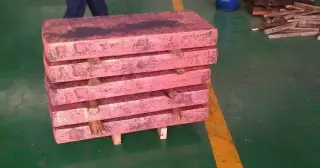
Key Considerations in Copper Forging
Copper Forging Temperature and Melting Point
- Copper Melting Point:Copper melts at approximately 1,984°F (1,085°C). However, for forging, copper is heated to a lower temperature where it becomes workable without melting.
- Forging Temperature:The ideal temperature for forging copper is between 700°C and 950°C (1292°F to 1742°F). This range allows the copper to maintain its integrity while being shaped effectively.
Copper Forging Materials and Equipment
- Copper Forging Material:High-purity copper is used to ensure the final product has the desired properties, such as conductivity and strength.
- Copper Forging Machine:Modern copper forging is often performed using automated machinery, including hydraulic presses and forging hammers, to achieve precise results.
- Copper Forging Hammer:A traditional tool used in copper forging, the hammer applies pressure to shape the copper, especially in artisanal or small-scale operations.
Types of Copper Forgings
Copper Forging, Brass Forging, and Bronze Forging
- Copper Forging:Produces components with high conductivity and corrosion resistance, suitable for electrical and plumbing applications.
- Brass Forging:Involves forging brass, an alloy of copper and zinc, which offers enhanced strength and machinability. Brass is often used in decorative items and mechanical parts.
- Bronze Forging:Bronze, an alloy of copper and tin, is forged for applications requiring higher strength and wear resistance, such as marine components and sculptures.
Copper Forging Applications
Machined Products – Copper and Brass Forgings
Copper and brass forgings are used in various machined products, including fittings, connectors, and custom components for industries like aerospace, automotive, and electronics. Their excellent conductivity and workability make them ideal for critical applications.
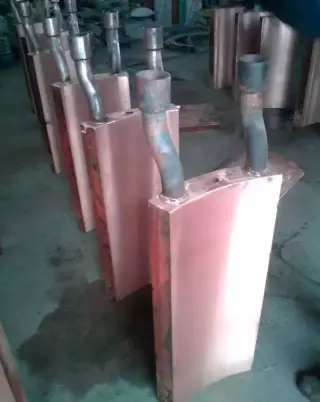
Global Copper Forging Market
1. Copper Forging in India & China
India and China are significant players in the global copper forging market. Both countries have advanced forging technologies and large-scale production capabilities, making them key suppliers of copper forgings worldwide.
2. Copper Forging Manufacturers
Leading copper forging manufacturers offer a range of products and services, including custom solutions tailored to specific industry needs. These manufacturers invest in advanced technology and quality control to deliver high-performance components.
Is Copper Good for Forging?
Is Copper Good for Forging?
Yes, copper is an excellent material for forging due to its high ductility, good thermal and electrical conductivity, and resistance to corrosion. These properties make forged copper ideal for various applications requiring reliable performance and durability.
Can Copper Be Cold Forged?
Can Copper Be Cold Forged?
While copper can be cold forged, it is more commonly hot forged due to its workability at elevated temperatures. Cold forging can be used for certain applications where high precision and surface finish are required, but it generally involves more specialized equipment and techniques.
Choosing the Right Copper Forging Supplier
Copper Forging Companies and Welleshaft
When selecting a copper forging supplier, it’s essential to choose a company with a strong reputation for quality and reliability. Welleshaft stands out as a trusted global supplier and contract manufacturer, known for its expertise in copper forging and commitment to excellence. Their advanced technology, skilled workforce, and rigorous quality control ensure that you receive high-quality copper forgings that meet your exact specifications.
Conclusion
Copper forging is a vital process that enhances the strength, durability, and functionality of copper components. Understanding the copper forging process, its benefits, and the key considerations can help you make informed decisions for your projects. Whether you need copper forgings for industrial applications or custom solutions, Welleshaft offers the expertise and reliability you need as a global supplier and contract manufacturer.
For more information on copper forgings and to explore how Welleshaft can support your needs, visit Welleshaft’s website or contact their team of experts today.