Introduction
When it comes to construction, manufacturing, or any project requiring durable connections, fasteners play a crucial role. From holding together bridges to securing pipelines, the choice of Exotic Alloy and High Performance Fastener Alloys Grades can significantly impact the integrity and longevity of the structure. Among the myriad of fastener options available, exotic alloy and high-performance alloy fasteners stand out for their exceptional properties and suitability for demanding applications.
Exotic Alloy Fasteners
Exotic alloys are materials that exhibit unique properties compared to traditional metals like steel or aluminum. These Exotic Alloy and High Performance Fastener Alloys Grades are often characterized by outstanding strength, corrosion resistance, and high-temperature stability.
- Titanium: Titanium fasteners (such as Grade 5) offer a high strength-to-weight ratio, excellent corrosion resistance, and biocompatibility. Commonly used in aerospace, marine, and medical industries.
- Inconel: Inconel fasteners (such as Alloy 625) provide exceptional resistance to extreme temperatures, oxidation, and corrosion. Widely used in chemical processing, aerospace, and marine environments.
- Monel: Monel fasteners (such as Alloy 400) exhibit superior resistance to corrosion from acids, alkalis, and saltwater. Ideal for marine engineering, chemical processing, and oil refining applications.
- Hastelloy: Hastelloy fasteners (such as C-276) offer resistance to a wide range of corrosive chemicals and high-temperature environments. Commonly used in chemical processing plants, pollution control systems, and marine environments.
High Performance Alloy Fasteners
High-performance alloy fasteners are engineered to withstand harsh conditions while maintaining structural integrity and reliability. These Exotic Alloy and High Performance Fastener Alloys Grades are composed of specialized alloys designed to offer superior mechanical properties and corrosion resistance.
- Alloy Steel: Alloy steel fasteners ( such as ASTM A193 Grade B7) are heat-treated for high strength and toughness. Used in heavy-duty applications such as construction, automotive, and machinery.
- Stainless Steel: Stainless steel fasteners (such as Type 316) offer excellent corrosion resistance and aesthetics. Popular in architectural, marine, and food processing industries.
- Nickel Alloy: Nickel alloy fasteners (such as Alloy 718) combine high strength with exceptional corrosion resistance. Ideal for chemical processing, petrochemical, and power generation applications.
- Other Alloys: Aluminum alloy, Copper alloy, Brass, Bronze, Zirconium, and Tantalum fasteners are available, each offering unique properties suited for specific applications.
Main Processing and Coating Capabilities for these Alloy materials
Titanium Fasteners:
- Machining Process: Titanium is machined using conventional methods such as milling, turning, drilling, and tapping.Cold forging for some applications.
- Special Considerations: Titanium has poor thermal conductivity, so coolant usage and tool selection are crucial to prevent overheating and tool wear.
- Common Surface Coatings: Titanium fasteners may be anodized for enhanced corrosion resistance or coated with specialized coatings for improved wear resistance.
Inconel Fasteners:
- Machining Process: Inconel is machined using conventional methods but requires high cutting speeds and feed rates due to its high strength and work-hardening tendency.
- Special Considerations: Carbide tooling with a positive rake angle is often used to minimize cutting forces and heat generation.
- Common Surface Coatings: Inconel fasteners may be coated with specialized coatings such as thermal spray coatings or PVD coatings to improve wear resistance and reduce galling.
Monel Fasteners:
- Machining Process: Monel is machined using conventional methods similar to stainless steel machining, Cold forging for some applications.
- Special Considerations: Monel work-hardens quickly, so sharp cutting tools and proper coolant usage are essential to maintain cutting efficiency.
- Common Surface Coatings: Monel fasteners may be coated with nickel plating or passivated to enhance corrosion resistance.
Hastelloy Fasteners:
-
Machining Process:Machine Hastelloy using conventional methods. Use carbide tools with high cutting speeds and feeds due to its high work hardening rate. Apply cold forging for some applications.
-
Special Considerations:Hastelloy work hardens quickly and generates heat. Use adequate cooling and lubrication to extend tool life.
-
Common Surface Coatings:Apply electroless nickel plating or PVD coatings to enhance corrosion resistance and surface hardness on Hastelloy fasteners.
Alloy Steel Fasteners:
-
Machining Process:Machine alloy steel with conventional methods. Use carbide tools and high cutting speeds due to its hardness. Apply cold or hot forging for high-strength applications.
-
Special Considerations:Perform proper heat treatment after machining to achieve desired mechanical properties.
-
Common Surface Coatings:Coat alloy steel fasteners with zinc plating, black oxide, or phosphate to enhance corrosion resistance and appearance.
Stainless Steel Fasteners:
-
Machining Process:Machine stainless steel with conventional methods using slower cutting speeds and feeds due to work hardening. Use cold heading or cold forming for smaller sizes.
-
Special Considerations:Prevent galling by applying lubricants or coatings like PTFE (Teflon).
-
Common Surface Coatings:Passivate stainless steel fasteners or electroplate with chrome or zinc. Apply organic coatings to improve corrosion resistance.
-
Heat Treatment:Use annealing, solution treatment, or precipitation hardening to enhance mechanical properties.
Nickel Alloy Fasteners:
-
Machining Process:Machine nickel alloys using conventional methods. Use carbide tools and high cutting speeds due to high strength and work hardening. Apply cold or hot forging for high-strength parts.
-
Special Considerations:Control heat buildup with proper cooling and lubrication during machining.
-
Common Surface Coatings:Coat nickel alloy fasteners with electroless nickel plating or PVD to improve corrosion and wear resistance.
Aluminum Alloy Fasteners:
- Machining Process: Aluminum alloys are machined using conventional methods, but sharp cutting tools and high cutting speeds are necessary to prevent built-up edge and achieve smooth finishes.Cold heading or cold forming for smaller sizes.
- Special Considerations: Aluminum alloys have a low melting point, so coolant usage is essential to prevent thermal damage to the workpiece and cutting tool.
- Common Surface Coatings: Aluminum alloy fasteners may be anodized for improved corrosion resistance and decorative purposes.
Copper Alloy Fasteners:
- Machining Process: Copper alloys are machined using conventional methods, but carbide tools with high cutting speeds and feeds are recommended due to their high thermal conductivity.Cold forging or hot forging for high-strength applications.
- Special Considerations: Copper alloys are prone to galling, so using lubricants or coatings such as PTFE (Teflon) is recommended.
- Common Surface Coatings: Copper alloy fasteners may be coated with nickel plating or passivated to enhance corrosion resistance and improve appearance.
- Heat treatment (annealing) for improving ductility.
Brass Fasteners:
- Machining Process: Brass is machined using conventional methods, but sharp cutting tools and low cutting speeds are typically used to prevent work hardening and achieve smooth finishes.Cold heading or cold forming for smaller sizes.
- Special Considerations: Brass has good machinability but is prone to burr formation, so proper tool geometry and cutting parameters are essential.
- Common Surface Coatings: Brass fasteners may be coated with nickel plating or passivated to improve corrosion resistance and enhance appearance.
Bronze Fasteners:
- Machining Process: Bronze is machined using conventional methods similar to brass machining.Sand casting or investment casting for complex shapes.
- Special Considerations: Bronze has good machinability but may generate burrs, so proper tool selection and cutting parameters are crucial.
- Common Surface Coatings: Bronze fasteners may be coated with nickel plating or passivated to improve corrosion resistance and surface finish.
Zirconium Fasteners:
- Machining Process: Zirconium is machined using conventional methods, but carbide tools with high cutting speeds and feeds are recommended due to its high strength and hardness.Sand casting or investment casting for complex shapes.
- Special Considerations: Zirconium is highly reactive with oxygen, so machining should be conducted in an inert atmosphere or under vacuum to prevent oxidation.
- Common Surface Coatings: Zirconium fasteners may be coated with specialized coatings such as ceramic or thermal spray coatings for enhanced wear resistance and corrosion protection.
Tantalum Fasteners:
- Machining Process: Tantalum is machined using conventional methods, but carbide tools with low cutting speeds and feeds are recommended due to its low thermal conductivity and high ductility.Cold forging for some applications
- Special Considerations: Tantalum is highly resistant to corrosion, so machining should be conducted using non-contaminating lubricants and coolants to prevent contamination.
- Common Surface Coatings: Tantalum fasteners typically do not require surface coatings due to their inherent corrosion resistance.
Choosing the Right Fastener Grade for Your Application
Worldwide Equivalent Grades (ISO/GB/DIN/AISI/ASTM/UNS/EU/BS/NF)
Selecting the appropriate fastener grade is essential to ensure the longevity and performance of a structure or equipment. Factors to consider include environmental conditions, load requirements, installation method, and regulatory standards. Consulting with fastener experts or engineers can provide valuable insights into selecting the right grade for your specific application, ensuring optimal performance and longevity.
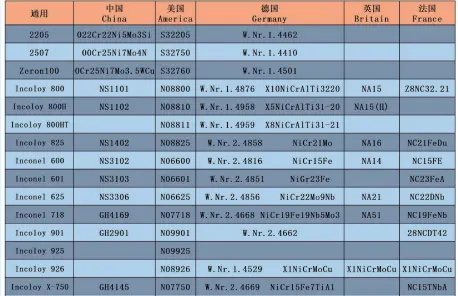
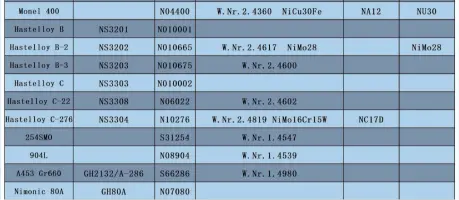
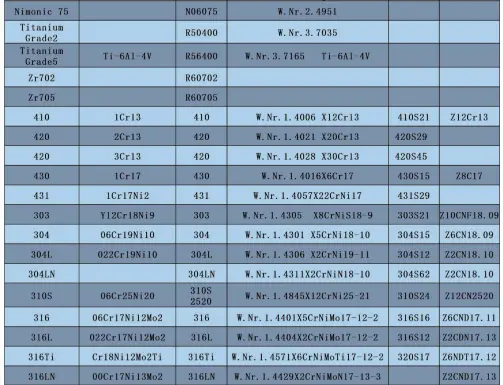
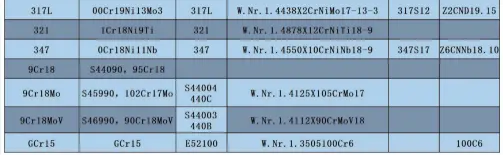
High-performance alloy and Exotic alloy material fasteners market trends
The market for exotic alloy and high-performance alloy fasteners is witnessing steady growth, driven by increasing demand from industries such as aerospace, automotive, chemical processing, and oil and gas. As industries continue to push the boundaries of performance and durability, there is a growing preference for materials that offer superior mechanical properties and corrosion resistance. Advancements in manufacturing technologies, such as additive manufacturing (3D printing), are also expanding the possibilities for designing and producing complex fastener shapes with exotic alloys.
At Welleshaft, we offer a wide range of custom fasteners tailored to our customers’ part drawing requirements, including specifications, materials, surface coatings, and more. Whether you need exotic alloy fasteners, high-performance alloy fasteners, or custom solutions, our team of experts is dedicated to providing the best fasteners for your specific needs. Contact us today to learn more about our products and services.