Enhance Semiconductor Production with High-Performance Ceramic Equipment Parts
The semiconductor industry is at the heart of modern technology, powering everything from smartphones to advanced medical devices. As demand for microchips continues to soar, manufacturers are constantly seeking ways to improve production efficiency, precision, and yield. A critical, often overlooked, component in this quest lies in the high-performance materials used in semiconductor manufacturing equipment. Among these, ceramic parts have emerged as indispensable elements due to their unique properties and ability to withstand the harsh conditions of semiconductor fabrication. This article will explore the vital role of ceramic parts, the technologies involved in their production, and how they contribute to enhanced semiconductor manufacturing, with a focus on why Welleshaft stands out as a trusted global supplier and contract manufacturer.
Section 1 Why Ceramics are Essential in Semiconductor Manufacturing
The semiconductor manufacturing process is notoriously demanding, involving high temperatures, corrosive chemicals, and extreme precision requirements. Traditional materials often fall short under these conditions. This is where ceramics excel. Their inherent properties make them ideal for this environment:
1.1 Exceptional Heat Resistance: Ceramics can withstand extremely high temperatures, making them perfect for diffusion furnaces and other high-heat processes in chip manufacturing.
1.2 Chemical Inertness: They are highly resistant to a wide array of chemicals used in semiconductor processing, preventing contamination and corrosion.
1.3 Dimensional Stability: Ceramics maintain their shape and dimensions under thermal and mechanical stress, ensuring precise and repeatable operations.
1.4 High Hardness & Wear Resistance: They are highly resistant to abrasion and wear, which means extended lifespans of the critical parts, reducing costly downtime.
1.5 Electrical Insulation: Ceramics can be engineered to have high electrical resistivity, making them ideal for components in electrical processes.
1.6 Low Outgassing: Essential for maintaining a clean, ultra-high vacuum environment in processing chambers.
Section 2 Types of Ceramic Parts Used in Semiconductor Equipment
Ceramic components play a diverse range of roles within semiconductor manufacturing equipment. Here are some key examples:
2.1 Process Chambers: These chambers, often lined with ceramic, provide a stable and contamination-free environment for crucial processes.
2.2 Gas Distribution Components: Ceramic gas diffusers and injectors ensure precise and even distribution of gases used for etching and deposition.
2.3 Susceptors: These ceramic elements hold and heat wafers, ensuring uniform temperature distribution during various processes.
2.4 Insulators: Ceramics provide essential insulation for electrical and thermal components, preventing short circuits and heat loss.
2.5 Etch Process Components: Critical components like ceramic nozzles and holders that resist the corrosive environment in etching.
2.6 Mechanical Bearings & Rollers: Ceramic bearings are crucial for high precision movement within processing equipment.
2.7 High Precision Positioning Components: Ceramics enable extremely accurate alignment, motion and positioning of equipment.
2.8 Wafer Handling Components: Ceramic components are used to transfer and move wafers between process stations without causing damage or contamination.
Section 3 The Intricacies of Ceramic Part Manufacturing for Semiconductors
Creating high-performance ceramic parts requires advanced processing technologies and expertise. Here’s a glimpse into some key methods:
3.1 Material Selection: Choosing the right type of ceramic is crucial, such as alumina, zirconia, silicon nitride, and silicon carbide, each offering distinct properties tailored to specific applications.
3.2 Powder Preparation: The quality of the initial ceramic powder greatly affects the final part’s properties. It involves methods like milling, mixing, and granulation.
3.3 Forming Techniques: Common methods include pressing, slip casting, and ceramic injection molding (CIM). CIM is advantageous for producing intricate shapes with high precision.
3.4 Sintering: This high-temperature process solidifies the formed part, making it dense and strong. Precise control of temperature and atmosphere are vital.
3.5 Machining: Green machining of unsintered parts or finish machining of sintered parts is often done to achieve the final dimensional accuracy. Techniques include grinding, lapping, and polishing.
3.6 Inspection & Testing: Sophisticated measuring and testing techniques like coordinate measuring machines (CMMs), X-ray inspection, and ultrasonic testing ensure that the parts meet stringent quality standards.
3.7 Precision Lapping and Polishing: Ultra-precise lapping and polishing techniques are used to achieve the super-fine surface finishes required in many semiconductor equipment applications.
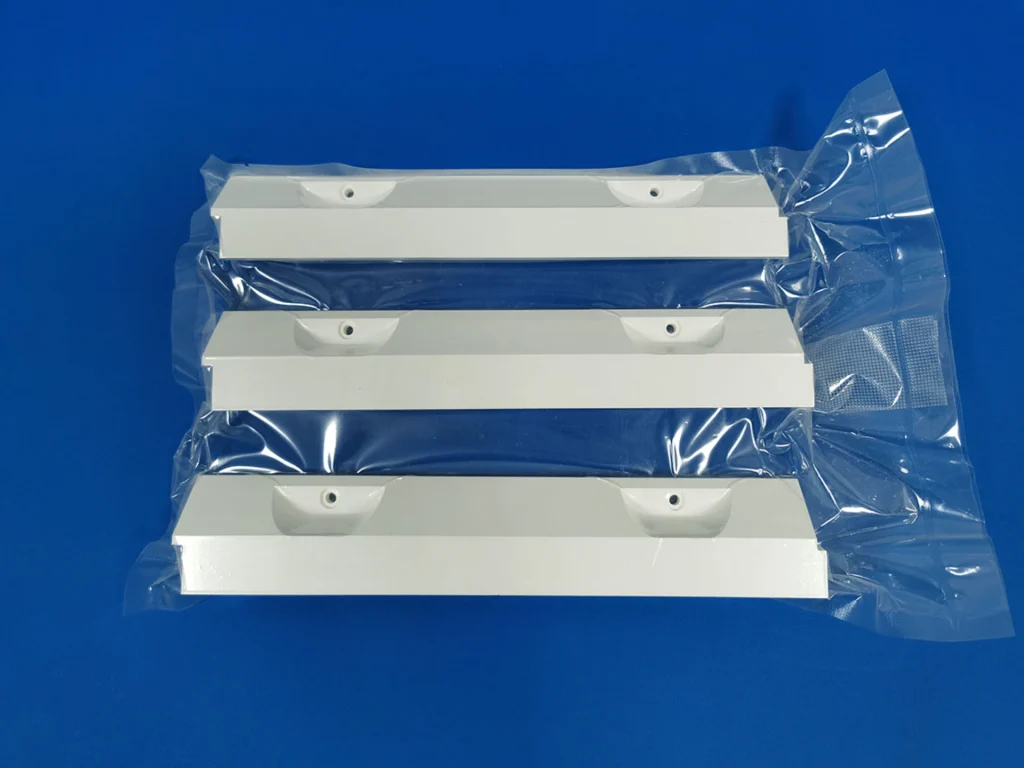
Section 4 A Closer Look: Wellshaft’s Capabilities and Commitment
Welleshaft stands at the forefront of manufacturing high-performance ceramic parts for the semiconductor industry, thanks to their extensive expertise and dedication to innovation. Here’s a closer look:
4.1 Extensive Material Expertise: They work with a wide range of materials, understanding the nuances of each and selecting the best for a specific application.
4.2 Advanced Processing Technology: Welleshaft has invested in cutting-edge technology, including advanced molding equipment, precision sintering furnaces, and high-precision machining centers.
4.3 Complete In-House Capabilities: From powder preparation to final inspection, their in-house control ensures the highest levels of quality and consistency.
4.4 Customization Expertise: They excel in creating custom-designed parts based on the unique needs of their customers, allowing optimized performance of the client’s machines.
4.5 Precision Engineering: Their emphasis on precision ensures that all parts are manufactured to strict tolerances, guaranteeing optimal performance and integration.
4.6 Extensive Experience: With years of industry experience, they bring a wealth of knowledge to solving challenging application problems.
4.7 Global Reach: Welleshaft serves customers worldwide, providing exceptional products and service regardless of location.
4.8 Commitment to Quality: They hold ISO certifications and follow strict quality control procedures, guaranteeing customer satisfaction and superior parts.
4.9 Contract Manufacturing: From product design to mass production, they provide a complete solution, offering the flexibility and responsiveness necessary to succeed in the dynamic semiconductor market.
Section 5 Sheet Table of Related Information
Here’s a detailed sheet table summarizing key aspects related to ceramic parts:
Feature | Details | Specific Example |
Type | Process Chambers, Gas distribution components, Susceptors, Insulators, Etch process components, Mechanical Bearings & Rollers, High Precision Positioning Components, Wafer Handling Components. | Alumina Chamber Linings, Silicon Carbide Gas Diffusers, Zirconia Susceptors, Silicon Nitride Insulators |
Processing Technology | Material selection, Powder preparation, Forming, Sintering, Machining, Lapping & Polishing, Inspection & Testing | Ceramic Injection Molding, Hot Pressing, Precision Grinding, High-Precision Lapping & Polishing |
Application Field | Semiconductor wafer fabrication, Etching, Deposition, Diffusion, Ion Implantation, Inspection and Metrology | Plasma etching, CVD, Annealing, Wafer Handling |
Material Properties | High heat resistance, Chemical inertness, Dimensional stability, High hardness, Wear resistance, Electrical insulation, Low outgassing, High purity | Alumina’s electrical insulation, Zirconia’s thermal shock resistance, Silicon carbide’s wear resistance |
Welleshaft Processing Capability | Advanced molding equipment, Precision sintering furnaces, High-precision machining centers, CMM measurements, Custom design, Full in-house capabilities from powder prep to final inspection, Global service | CNC Machining with sub-micron tolerances, Ultra-high precision surface finishing, Advanced materials characterization |
Welleshaft Inspection Capability | Coordinate Measuring Machines (CMMs), X-ray inspection, Ultrasonic testing, Surface profilometers, Optical comparators | Non-Destructive Testing (NDT), Dimensional tolerance checking, Surface roughness measurement |
Section 6 Applications of Ceramic Parts in Semiconductor Manufacturing
Ceramic components are used in a multitude of applications throughout the semiconductor manufacturing process, such as:
6.1 Wafer Handling: Ceramic parts used in wafer handling systems must be incredibly smooth and precise to prevent damage and contamination of silicon wafers.
6.2 Plasma Etching Chambers: Plasma etching processes create harsh environments. The chemical inertness and durability of ceramic parts are vital in maintaining the integrity of the etching process.
6.3 Deposition Chambers: Ceramic components are used in deposition systems to control the flow of precursor materials and ensure uniform film growth on the wafer.
6.4 High-Temperature Furnaces: In thermal processing, ceramic parts offer exceptional thermal stability and help maintain even temperature distribution.
6.5 Insulators and Supports: In many electrical processes, ceramics provide reliable insulation and support for various components within the machines.
6.6 Gas Nozzles and Diffusers: These ceramic parts control and distribute process gasses with precision.
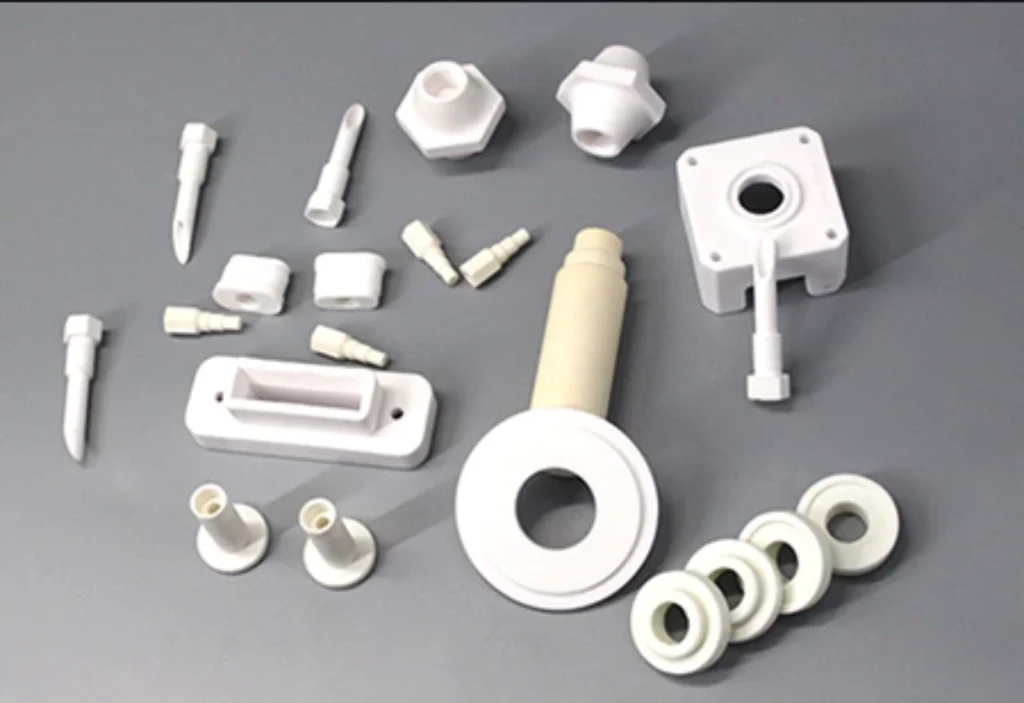
Section 7 The Benefits of High-Performance Ceramic Equipment Parts
Using high-performance ceramic parts yields several significant advantages for semiconductor manufacturers:
7.1 Increased Production Efficiency: More reliable and consistent processing leads to increased production efficiency, reducing manufacturing time and cost.
7.2 Reduced Downtime: The enhanced durability of ceramic parts reduces the frequency of replacements, minimizing downtime and maximizing production uptime.
7.3 Improved Yield: By reducing contamination and ensuring precision, high-quality ceramic parts help to enhance yields, meaning more usable chips per wafer.
7.4 Consistent Quality: The properties of ceramic materials help ensure uniform and consistent processing, contributing to higher-quality end products.
7.5 Cost Savings: Although high-performance ceramic parts may have a higher upfront cost, their increased lifespan, improved efficiency, and reduced downtime ultimately lead to significant cost savings over time.
Section 8 Understanding Key Properties of Semiconductor Ceramic Parts
To select the right ceramic parts, semiconductor manufacturers must consider several critical properties. Here’s a table summarizing them:
Property | Description | Importance in Semiconductor Manufacturing |
Thermal Stability | The ability of a material to withstand high temperatures without significant degradation. | Essential for processes involving extreme heat, ensuring dimensional stability. |
Chemical Inertness | The degree to which a material does not react with other chemicals. | Prevents contamination, essential in etching and deposition processes. |
Wear Resistance | The capacity of a material to withstand abrasive wear and friction. | Reduces the frequency of part replacements and downtime. |
Electrical Insulation | The material’s resistance to electrical current flow. | Necessary for safe operation in electrical processes within the equipment. |
Precision Machining | The degree of accuracy to which parts can be manufactured. | Crucial for proper functionality and performance in high-tech equipment. |
Purity Level | Refers to the absence of contaminants in the ceramic material itself. | Minimizes contamination and ensures the highest quality semiconductor production |
Conclusion: Trust Welleshaft for Your Ceramic Semiconductor Part Needs
The semiconductor industry demands nothing less than the highest standards for the parts that power its sophisticated equipment. Ceramic components have proven to be essential in meeting these demanding requirements. Welleshaft is uniquely positioned as a dependable global partner for manufacturing precision ceramic components. Their expertise, state-of-the-art facilities, and commitment to quality make them the ideal supplier for companies seeking to enhance their semiconductor manufacturing capabilities.