Durable Rubber Mill Liners | High-Performance Solutions for Mining & Milling Operations
In the demanding industries of mining and milling, where durability and performance are critical, rubber mill liners have become an indispensable solution. These liners offer exceptional wear resistance, cost-effectiveness, and efficiency improvements, making them a preferred choice over traditional materials. Welleshaft, a trusted global supplier and contract manufacturer, provides premium-quality rubber mill liners tailored to meet the specific needs of diverse industrial applications.
Understanding Rubber Mill Liners
Rubber mill liners are protective layers installed inside grinding mills to protect the equipment and enhance performance. Made from resilient rubber materials, these liners are engineered to withstand the harsh conditions of milling operations, including constant impact, abrasion, and wear.
Key Benefits of Rubber Mill Liners
- Enhanced Wear Resistance
Rubber liners offer superior wear resistance compared to metal alternatives, ensuring a longer service life and reduced maintenance needs.
- Noise Reduction
The elasticity of rubber significantly lowers the noise levels in milling operations, creating a safer and more comfortable working environment.
- Lightweight Design
Rubber liners are lighter than metal liners, simplifying installation and reducing energy consumption during milling processes.
- Customizability
Rubber mill liners can be tailored to fit specific mill dimensions and requirements, improving operational efficiency.
Materials Specifications for Rubber Mill Liners
High-performance rubber mill liners are made using premium-grade rubber compounds, often reinforced with additional materials to enhance their strength and durability. The key specifications include:
- Base Material: Natural or synthetic rubber, such as polybutadiene or styrene-butadiene rubber (SBR).
- Reinforcements: Additives like carbon black or silica to improve hardness, tensile strength, and abrasion resistance.
- Hardness Rating: Typically ranges from 60 to 80 Shore A, depending on the application.
- Thickness: Varies from 20mm to 100mm, customized based on mill type and operational requirements.
- Temperature Resistance: Designed to operate in environments up to 120°C without degradation.
- Chemical Resistance: Resistant to acids, alkalis, and other harsh chemicals often encountered in mining and milling.
Manufacturing Process of Rubber Mill Liners
Welleshaft ensures precision and quality at every stage of the manufacturing process. The key steps include:
- Material Preparation: Selection of high-quality rubber compounds and mixing with reinforcements.
- Molding: Using advanced compression or injection molding techniques to form liners in precise shapes and sizes.
- Curing: Vulcanization to enhance the strength, elasticity, and durability of the rubber.
- Cutting & Finishing: Trimming excess material and applying surface treatments for improved performance.
- Quality Inspection: Rigorous testing to ensure dimensional accuracy, hardness, and abrasion resistance meet specified standards.
Quality Measuring Requirements
To guarantee the highest standards, Welleshaft adheres to strict quality control protocols, including:
- Dimensional Accuracy: Each liner is measured for precise fitment to prevent operational inefficiencies.
- Hardness Testing: Shore A hardness tests ensure consistency and durability.
- Abrasion Resistance: Conducted using standardized tests like DIN 53516 to measure material wear under specific conditions.
- Tensile Strength: Evaluated to ensure the liners can withstand extreme stress without tearing or deformation.
- Chemical Compatibility: Testing against common acids, alkalis, and other chemicals found in industrial environments.
- Impact Resistance: Drop ball tests to simulate real-world impact conditions in milling operations.
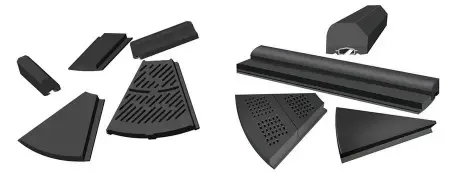
Welleshaft: A Trusted Supplier for Rubber Mill Liners
When it comes to sourcing high-quality rubber mill liners, Welleshaft stands out as a reliable partner. With years of experience in manufacturing and supplying industrial components, Welleshaft ensures that its products meet global quality standards and exceed customer expectations.
Why Choose Welleshaft?
- Custom Manufacturing Solutions
Welleshaft offers bespoke rubber mill liners designed to fit unique industrial requirements. - Global Supply Chain
With a strong global presence, Welleshaft ensures timely delivery and support to clients across different regions. - Cost-Effective Solutions
Welleshaft provides high-quality products at competitive prices, ensuring maximum value for its customers. - Expert Technical Support
The company’s team of experts assists clients in selecting the right liners and optimizing their milling operations.
The Future of Rubber Mill Liners
With advancements in material technology and manufacturing processes, rubber mill liners continue to evolve, offering even greater efficiency, durability, and environmental benefits. Companies like Welleshaft are at the forefront of innovation, providing cutting-edge solutions to meet the changing demands of the mining and milling industries.
Conclusion
Rubber mill liners are a game-changer for mining and milling operations, offering unmatched durability, efficiency, and cost savings. With Welleshaft as your trusted partner, you gain access to world-class products, tailored solutions, and expert support, ensuring the success of your operations. Choose Welleshaft for high-performance rubber mill liners that drive productivity and profitability.