Ceramic Rollers for Printing & Conveying: Durable and Accurate for Optimal Results
Section 1 Introduction
In the world of industrial manufacturing and printing, precision and reliability are paramount. The efficiency and quality of processes like conveying and printing often hinge on the performance of seemingly simple components: rollers. While various materials are used in roller construction, ceramic rollers have emerged as a superior choice for applications demanding durability, accuracy, and consistent performance. This article explores the advantages of ceramic rollers, specifically within the context of printing and conveying systems, and highlights why choosing the right supplier, like Welleshaft, is crucial for achieving optimal results.
Section 2 The Superiority of Ceramic Rollers
Ceramic rollers have gained prominence due to their exceptional combination of properties. They offer a wide range of advantages over conventional materials, including:
2.1 High Hardness & Wear Resistance: Ceramic materials are exceptionally hard, allowing them to withstand abrasive materials and heavy loads. This dramatically reduces wear and tear, extending the lifespan of the rollers and minimizing downtime.
2.2 Corrosion Resistance: Many ceramic materials are chemically inert, meaning they are highly resistant to corrosion and degradation from chemicals commonly used in industrial settings.
2.3 High-Temperature Stability: Ceramics maintain their structural integrity and mechanical properties even at elevated temperatures, making them ideal for high-temperature applications.
2.4 Low Thermal Expansion: This allows for highly precise and consistent operation with minimal distortion during temperature fluctuations.
2.5 Smooth Surface Finish: Precisely manufactured ceramic rollers can be polished to incredibly smooth finishes, crucial for applications requiring precise and gentle contact.
2.6 Low Friction Coefficient: This attribute reduces energy consumption and heat generation, ensuring efficient material movement.
2.7 Precise Dimensional Accuracy: With meticulous manufacturing processes, ceramic rollers can achieve tight tolerances, critical for precision applications.
Section 3 Types of Ceramic Rollers
The versatility of ceramic rollers allows for a wide range of specialized types. Here’s a breakdown of some common categories, many of which were in your provided image:
Sheet Table of Ceramic Roller Types and Related Information
Type | Processing Technology | Application Field | Material Properties |
Ceramic Guide Roller | Isostatic Pressing, Precision Grinding | Guiding and controlling the movement of materials in printing, textile, and film processing | High wear resistance, excellent surface finish, low friction |
Ceramic Conveyor Roller | Slip Casting, Precision Grinding, HIP | Transporting materials on conveyor systems in packaging, food processing, and logistics | High load capacity, chemical resistance, dimensional stability |
Ceramic Support Roller | Isostatic Pressing, Precision Grinding, Sintering | Supporting and stabilizing materials in manufacturing, metalworking, and glass processing | High hardness, high compressive strength, high temperature resistance |
Ceramic Idler Roller | Cold Isostatic Pressing, Precision Grinding | Minimizing friction and facilitating smooth movement in conveying systems | Low friction, high wear resistance, corrosion resistance |
Ceramic Cylinders | Extrusion, Precision Grinding, Sintering | Various industrial applications, including machine components, seals, and piston elements | High strength, thermal stability, chemical resistance |
Ceramic Bearing Roller | Precision Machining, Sintering | Supporting and facilitating rotational movement in machinery and equipment | High precision, low friction, good chemical inertness |
Precision Ceramic Roller | High Precision Grinding, Lapping | High-accuracy applications requiring tight tolerances in printing, coating, and converting | Extreme dimensional accuracy, smooth surface finish, minimal run-out |
Alumina Ceramic Roller | Extrusion, Slip Casting, Sintering | General-purpose industrial applications, offering good wear resistance and thermal stability | Good wear resistance, high temperature stability, cost-effective |
Zirconia Ceramic Roller | Isostatic Pressing, Precision Grinding, Sintering | High-stress applications, offering exceptional toughness and durability in printing and conveying, metalworking | High strength, high wear resistance, good chemical inertness |
Silicon Carbide Ceramic Roller | Reaction Bonding, Sintering | High-temperature and corrosive environments, offering exceptional resistance in chemical, glass and other high-demanding applications. | Very high hardness, excellent high-temperature resistance, exceptional wear resistance. |
Silicon Nitride Ceramic Roller | Hot Pressing, Sintering | High-speed applications requiring extreme performance and resistance to heat and wear, aerospace. | High strength at elevated temperatures, low friction, exceptional fracture toughness |
Ceramic Support Rolls | Isostatic Pressing, Precision Grinding, Sintering | Supporting and guiding materials in various industrial processes, such as laminating and coating machines | High hardness, high compressive strength, chemical resistance |
Industrial Ceramic Guidance Rolls | Isostatic Pressing, Precision Grinding | Precise guiding and controlling of materials in industrial settings like web handling and processing. | High wear resistance, excellent surface finish, low friction |
Wear-Resistant Ceramic Contact Rollers | Isostatic Pressing, Precision Grinding | Material contact points in high-wear and abrasion environments, increasing life expectancy and quality | Exceptional wear resistance, high hardness, smooth surface finish |
Precision Ceramic Sleeves | Precision Grinding, Lapping | Components for rotary systems, providing stability and precision in various applications | Extreme dimensional accuracy, smooth surface finish, high concentricity |
Hard Ceramic Rotary Components | Precision Machining, Sintering | Key components in systems requiring rotational movement with high precision and durability. | High precision, exceptional hardness, chemical resistance |
Specialty Ceramic Conveyor Rollers | Isostatic Pressing, Precision Grinding | Tailored to specific needs in various industrial conveying applications | Application-specific material properties with customized dimensions and functionality |
Ceramic Anilox Rollers | Precision Engraving, Sintering | Precise ink transfer in printing applications, typically in flexographic processes. | High cell volume consistency, controlled ink transfer, exceptional wear resistance |
Bearing Rollers made from Silicon Nitride Ceramics | Hot Pressing, Precision Machining | High-speed, high-precision bearing applications in aerospace, automotive, and industrial equipment | High strength at elevated temperatures, low friction, exceptional fracture toughness |
Ceramic Coated Rollers | Coating processes | Rollers with enhanced surface characteristics, depending on coating type and application | Wear resistance, corrosion resistance, customized surface properties |
**Siliconized Silicon Carbide | Ceramic Rollers | Shapes** | Silicon infiltration process |
Solid Ceramic Rollers | Isostatic Pressing, Sintering, Grinding | Load-bearing applications where a high strength and integrity are crucial. | High strength, wear resistance, high-temperature stability, dimensional stability |
High-Temperature Ceramic Roller | Isostatic Pressing, Precision Machining, Sintering | Designed to perform in extreme temperature environments, such as furnaces, ovens, and other heat-intensive processes. | High thermal resistance, dimensional stability at elevated temperatures, chemical inertness. |
Abrasion-Resistance Ceramic Conveyor Belt Roller | Isostatic Pressing, Sintering, Grinding | Particularly suited for high abrasion environments where a roller has to endure much wear and tear. | High hardness, high wear resistance, corrosion resistance. |

Section 4 Choosing the Right Ceramic Roller: Key Considerations
Selecting the correct ceramic roller requires careful consideration of several factors:
4.1 Material Grade: Different ceramic materials offer varying properties. Choosing the right grade based on your application is critical (e.g., alumina for wear resistance, zirconia for impact resistance).
4.2 Surface Finish: The required surface finish will depend on the application. Precision printing may need an extremely smooth finish, while conveying applications might need some degree of texture.
4.3 Dimensions and Tolerances: Ensure that the rollers are manufactured to the exact dimensions and tolerances required by your system.
4.4 Application-Specific Requirements: Consider factors like operating temperature, chemical exposure, and loads the rollers will endure.
Section 5 Applications of Ceramic Rollers in Printing and Conveying
The unique properties of ceramic rollers make them ideal for a wide range of applications, particularly in printing and conveying processes:
5.1 Printing:
5.1.1 Flexographic Printing: Ceramic anilox rollers are essential for precise ink transfer, ensuring consistent and high-quality printing.
5.1.2 Offset Printing: Ceramic rollers provide smooth and even distribution of ink, enabling crisp and clear prints.
5.1.3 Digital Printing: Ceramic rollers facilitate accurate substrate handling and feeding, crucial for consistent digital prints.
5.2 Conveying:
5.2.1 Material Handling: Ceramic conveyor rollers offer smooth and reliable movement of goods across production lines, reducing friction and wear.
5.2.2 Food Processing: The non-reactive nature of ceramics makes them ideal for food handling, preventing contamination and ensuring hygiene.
5.2.3 Textile Manufacturing: Ceramic rollers ensure smooth and precise fabric movement, reducing friction and wear.
5.2.4 Packaging: Ceramic rollers are used in packaging machinery for efficient and reliable handling of packaging materials.
Section 6 Processing Technologies for Ceramic Rollers
The manufacturing of high-quality ceramic rollers requires specialized techniques. Here’s a summary of the most common methods:
6.1 Powder Preparation: The first step involves preparing high-purity ceramic powders.
6.2 Forming: Forming techniques include:
6.3 Isostatic Pressing: Powder is pressed uniformly from all directions to create a compact shape.
6.4 Slip Casting: A ceramic slurry is poured into a mold and allowed to dry and solidify.
6.5 Extrusion: Ceramic paste is forced through a die to create a continuous shape.
6.6 Sintering: The formed part is heated to a high temperature to densify the material, bonding the ceramic particles together.
6.7 Precision Machining: After sintering, the ceramic part is precisely machined to achieve the required dimensions and surface finish. Techniques include grinding, lapping, and polishing.
6.8 Surface Treatment: Some ceramic rollers may undergo additional surface treatments to enhance specific properties.
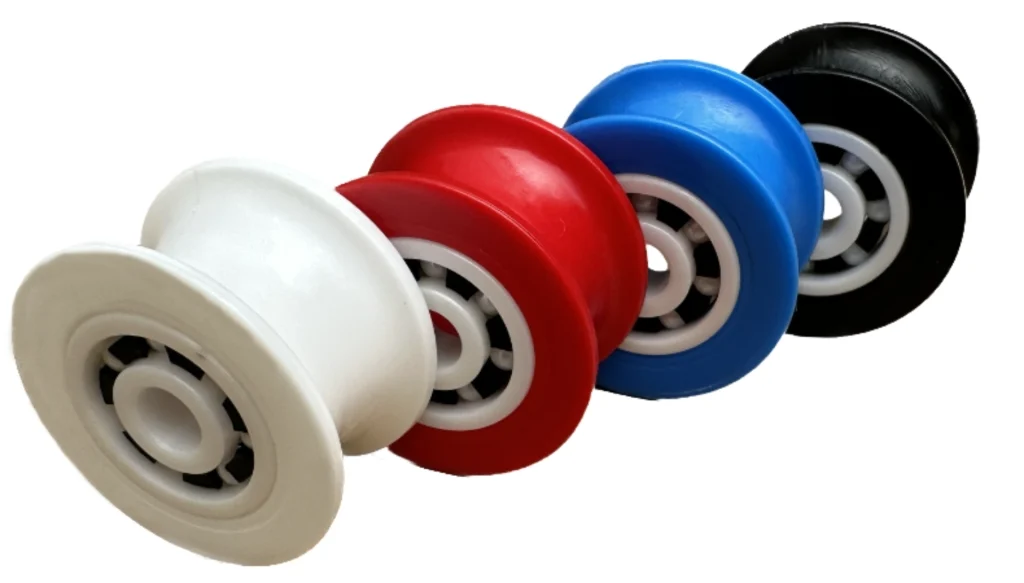
Section 7 Welleshaft: Your Trusted Global Partner
When sourcing high-quality ceramic rollers, it’s crucial to work with a reputable supplier and contract manufacturer. Welleshaft has established itself as a global leader in the production of precision ceramic rollers, earning a reputation for:
7.1 High-Quality Manufacturing: Welleshaft utilizes advanced manufacturing techniques and strict quality control measures to ensure exceptional product performance.
7.2 Customized Solutions: Whether you need standard ceramic rollers or custom-designed solutions, Welleshaft has the expertise and capacity to meet your unique requirements.
7.3 Global Supply Chain: With a global network of partners, Welleshaft can deliver products reliably and efficiently to customers worldwide.
7.4 Technical Expertise: Welleshaft’s team of experienced engineers and material scientists provides technical support and guidance throughout the product development process.
7.5 Contract Manufacturing: Welleshaft has the capability to produce not only standard products, but custom contract manufacturing with great accuracy and efficiency.
7.6 Inspection capability: Welleshaft’s inspection capability includes a range of tools to ensure every manufactured part is according to specification. These tools include 3D Scanning, CMM Measuring Equipment, Surface Roughness Testers, and many others.
Conclusion
Ceramic rollers are indispensable components for printing and conveying industries seeking durability, precision, and long-lasting performance. Their superior material properties, combined with advanced manufacturing techniques, make them the optimal choice for demanding applications. When looking for a reliable partner, consider Welleshaft, a trusted global supplier and contract manufacturer that will provide customized solutions and expert support. By choosing high-quality ceramic rollers and a qualified manufacturer, companies can optimize their processes, reduce costs, and ensure exceptional output.