Ceramic Powder Injection Molding: Precision Manufacturing Solutions
Ceramic powder injection molding (CIM) is an advanced manufacturing process that enables the creation of intricate ceramic components with unparalleled precision and efficiency. This technique is widely used across various industries, including automotive, aerospace, electronics, and healthcare, due to its ability to produce complex shapes and high-performance materials. In this article, we will delve into the details of ceramic powder injection molding, explore the benefits it offers, and highlight why Welleshaft stands out as a trusted global supplier and contract manufacturer in this field.
Section 1: What is Ceramic Injection Molding?
Ceramic injection molding is a specialized process that combines the versatility of plastic injection molding with the superior material properties of ceramics. The process involves injecting a ceramic powder mixed with a binder into a mold cavity. After molding, the binder is removed, and the ceramic part is sintered to achieve its final properties. This method is ideal for producing small, complex components with high precision, making it a preferred choice for industries that demand exceptional performance.
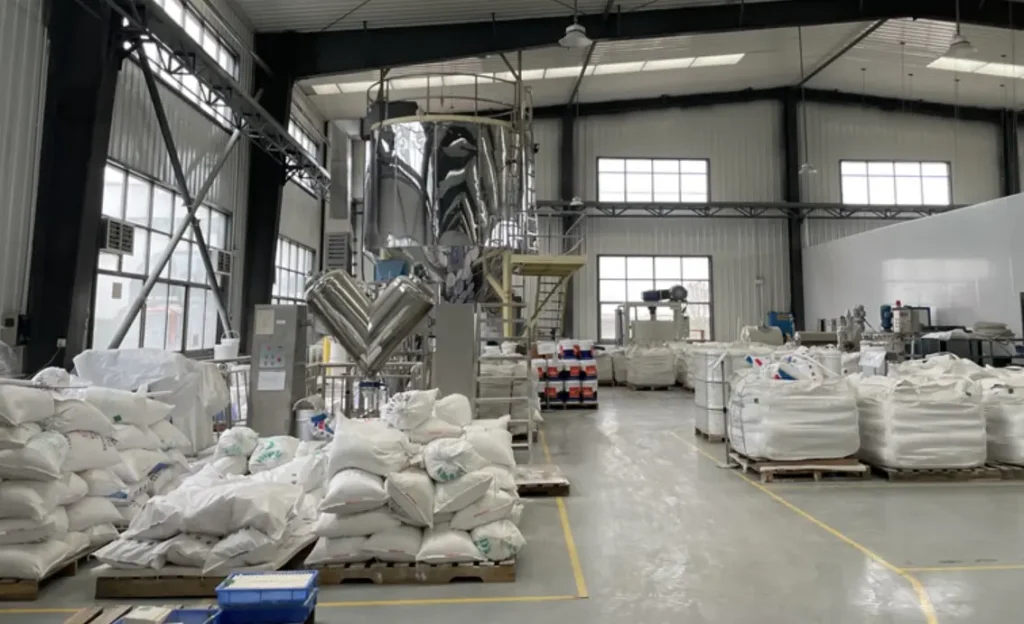
1.1. The Process of Ceramic Powder Injection Molding
Step 1: Feedstock Preparation
The first step in the CIM process is the preparation of the feedstock, which consists of fine ceramic powder and a binder system. The ceramic powder is carefully selected based on the desired properties of the final product, while the binder helps to facilitate the molding process. The feedstock is thoroughly mixed to ensure uniform distribution of the ceramic powder.
Step 2: Injection Molding
Once the feedstock is prepared, it is injected into a mold cavity using a ceramic injection molding machine. The machine operates under high pressure, ensuring that the material fills every nook and cranny of the mold. This step is crucial for achieving the desired shape and dimensions of the component.
Step 3: Debinding
After the molding process, the binder must be removed from the molded part. This is done through a process called debinding, which typically involves thermal or solvent extraction. The removal of the binder leaves behind a fragile “green” part, which still contains the ceramic powder in its molded shape.
Step 4: Sintering
The final step in the CIM process is sintering, where the green part is heated to a high temperature in a controlled atmosphere. During sintering, the ceramic particles fuse together, resulting in a dense and robust final product. The sintering process also helps to eliminate any remaining pores and enhances the mechanical properties of the ceramic component.
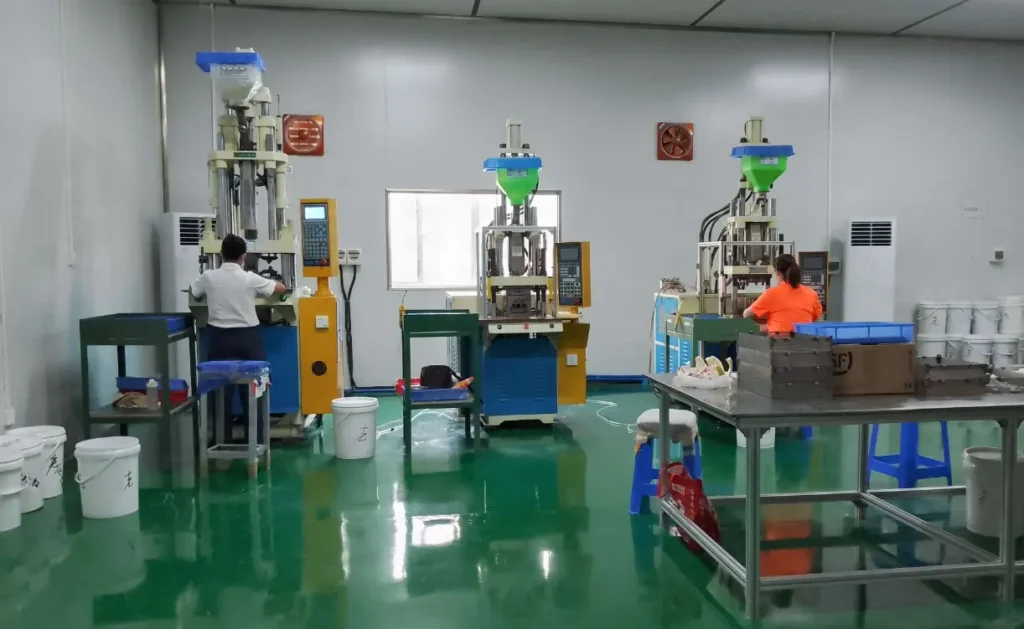
Section 2: Benefits of Ceramic Powder Injection Molding
1. Precision and Complexity
One of the most significant advantages of ceramic powder injection molding is its ability to produce highly complex shapes with tight tolerances. The process allows for the creation of intricate geometries that would be challenging or impossible to achieve with traditional ceramic manufacturing methods.
2. Superior Material Properties
Ceramic materials are known for their exceptional hardness, high-temperature resistance, and excellent wear and corrosion resistance. The CIM process ensures that these properties are retained in the final product, making it suitable for demanding applications in various industries.
3. Cost-Effective Production
Ceramic powder injection molding is a cost-effective solution for mass production of small to medium-sized ceramic components. The ability to produce multiple parts in a single molding cycle reduces manufacturing costs and increases production efficiency.
4. Versatility in Material Selection
The CIM process is compatible with a wide range of ceramic materials, including alumina, zirconia, silicon carbide, and more. This versatility allows manufacturers to select the most suitable material for their specific application requirements.
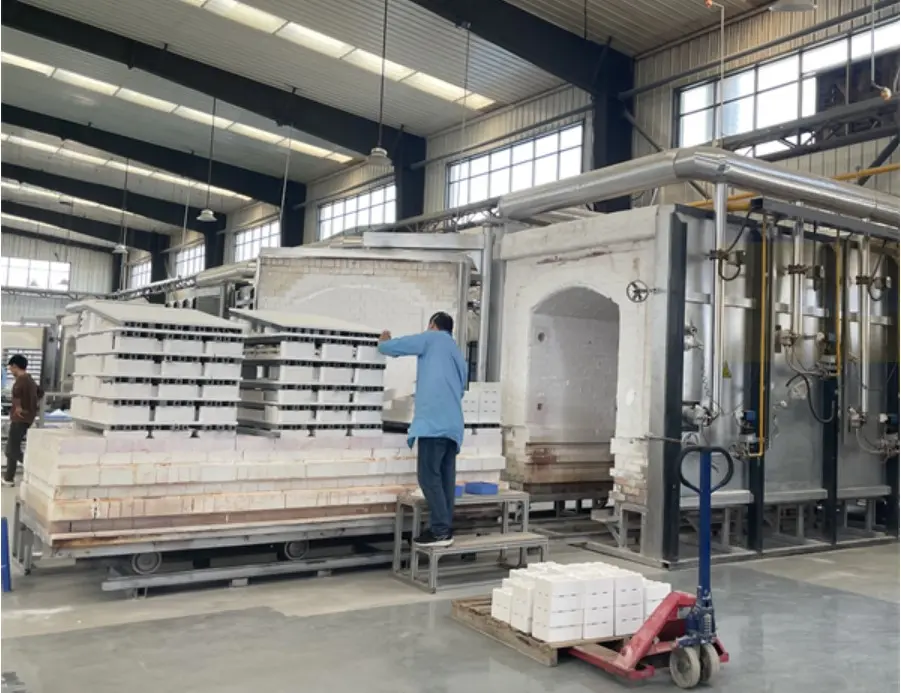
Section 3: What is Ceramic Powder Used For?
Ceramic powder is a versatile material used in various manufacturing processes, including ceramic powder injection molding, for creating high-performance components. Its applications range from the production of advanced ceramics for industrial use to the creation of intricate parts for electronics and medical devices.Some common applications include:
- Automotive: Production of components such as fuel injectors, sensors, and engine parts.
- Aerospace: Manufacturing of high-temperature-resistant components for jet engines and turbines.
- Electronics: Fabrication of insulators, connectors, and other electronic components.
- Healthcare: Production of medical devices, dental implants, and surgical instruments.
Section 4: What Materials Are Used in Ceramic Molding?
Ceramic molding utilizes a variety of materials, depending on the desired properties of the final product. Some commonly used materials include:
- Alumina (Al2O3): Known for its excellent electrical insulation properties and high strength.
- Zirconia (ZrO2): Offers exceptional toughness and resistance to wear and corrosion.
- Silicon Carbide (SiC): Provides high thermal conductivity and resistance to extreme temperatures.
- Silicon Nitride (Si3N4): Known for its excellent mechanical properties and thermal shock resistance.
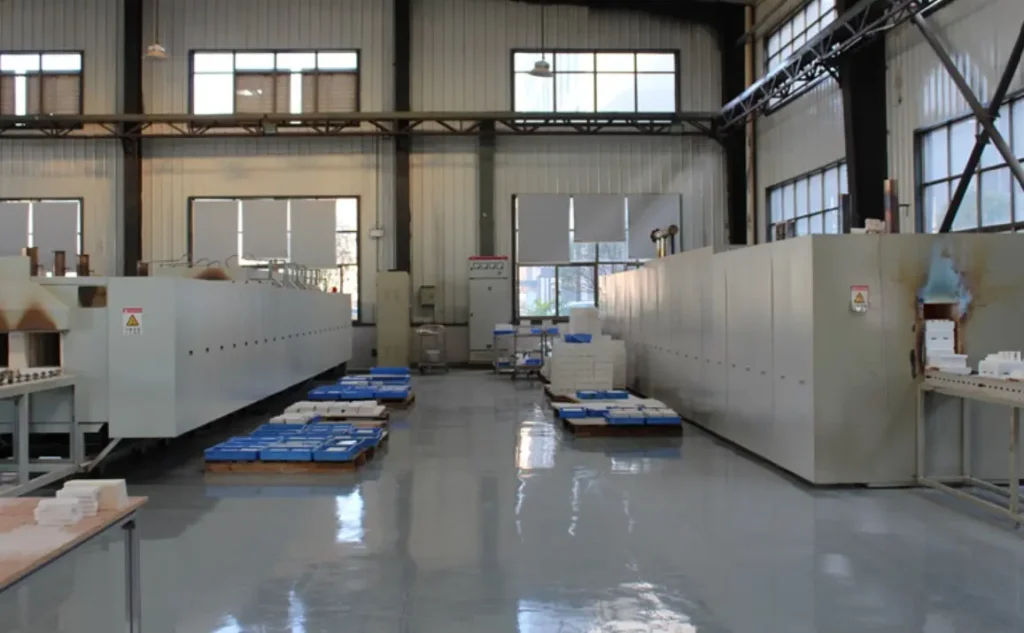
Section 5: Ceramic Powder Injection Molding Manufacturers
When selecting a ceramic powder injection molding manufacturer, it’s essential to choose a partner with a proven track record of quality and reliability. Welleshaft is a global leader in precision manufacturing, offering top-tier ceramic powder injection molding services. With years of experience and a commitment to excellence, Welleshaft provides innovative solutions tailored to meet the specific needs of its clients.
Section 6: Ceramic Powder Injection Molding Cost
6.1. Ceramic Powder Injection Molding (CIM) Overview
Ceramic Powder Injection Molding is a sophisticated process that combines ceramic powder with a binder to create intricate shapes through injection molding. The molded parts are then subjected to a debinding process to remove the binder, followed by sintering to solidify the ceramic material. This process is ideal for small to medium-sized parts requiring precise dimensions and complex geometries.
6.2. Cost Factors in CIM
Tooling Costs:
CIM typically involves significant upfront tooling costs due to the precision required for the molds. High-quality molds are necessary to achieve the intricate designs that CIM can produce. While these costs may be high initially, they become more cost-effective over large production runs.
Material Costs:
The cost of ceramic powder and binders used in CIM can vary based on the type of ceramic material and the quality required. For example, advanced ceramics like zirconia or silicon carbide may be more expensive than more common materials like alumina.
Production Volume:
CIM is particularly cost-effective for high-volume production. The per-unit cost decreases significantly as production scales up, making it an ideal choice for mass production of complex components.
Complexity of Design:
One of CIM’s strengths is its ability to produce complex parts in a single process, which can reduce the need for additional machining or finishing steps. This can result in overall cost savings, especially for highly detailed or intricate designs.
Labor and Processing Costs:
The CIM process involves several stages, including injection molding, debinding, and sintering. Each stage requires specialized equipment and skilled labor, which can contribute to the overall cost. However, automation can mitigate some of these expenses in large-scale production.
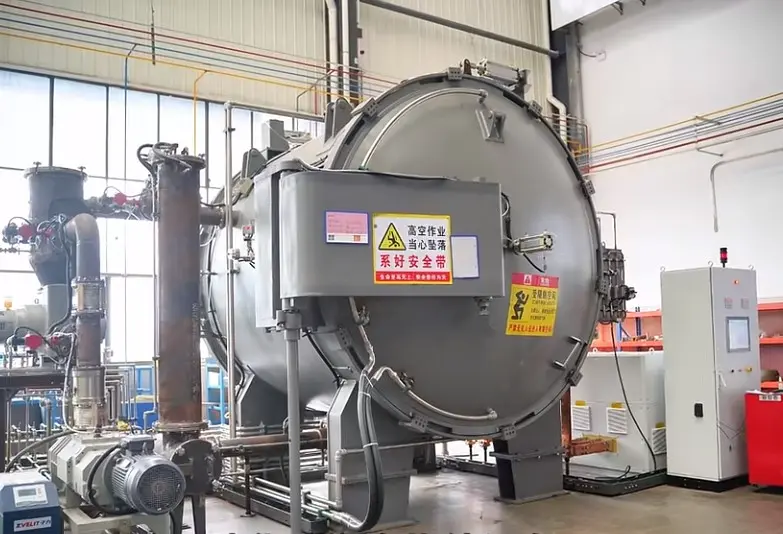
6.3. Comparison with Other Ceramic Manufacturing Methods
1. Traditional Ceramic Processing (Pressing and Sintering)
Process: Traditional methods involve pressing ceramic powder into a desired shape using a mold, followed by sintering to form a solid structure. This method is well-suited for simple shapes with lower precision requirements.
Cost Comparison:
- Tooling Costs: Generally lower than CIM due to the simplicity of the molds.
- Material Costs: Similar, depending on the ceramic used.
- Production Costs: Lower for simple, large components but less efficient for complex shapes.
- Labor Costs: Lower due to fewer process steps, but can increase with post-processing needs.
- Use Case: Best suited for large, simple components where precision is less critical.
2. Extrusion
Process: Ceramic extrusion involves pushing ceramic material through a die to create long shapes with uniform cross-sections, which are then cut to size and sintered.
Cost Comparison:
- Tooling Costs: Low, with inexpensive dies.
- Material Costs: Comparable to CIM.
- Production Costs: Very low for high-volume production of simple, uniform shapes.
- Labor Costs: Minimal, especially in automated processes.
- Use Case: Ideal for producing large quantities of simple, elongated shapes (e.g., rods, tubes).
3. Slip Casting
Process: In slip casting, a liquid slurry of ceramic powder is poured into a porous mold, where the liquid is absorbed, leaving behind a solid ceramic layer. This is followed by drying and sintering.
Cost Comparison:
- Tooling Costs: Low, due to simple mold design.
- Material Costs: Lower, as the process can utilize less expensive ceramic materials.
- Production Costs: Low to moderate, but the process is slower and less suited to automation.
- Labor Costs: Higher, due to the manual nature of the process.
- Use Case: Suitable for large, hollow parts with less demand for high precision.
4. Tape Casting
Process: Tape casting involves creating thin ceramic sheets by casting a slurry onto a flat surface, which is then dried and sintered.
Cost Comparison:
- Tooling Costs: Low, with minimal setup.
- Material Costs: Varies depending on the ceramic material.
- Production Costs: Low for thin, flat components.
- Labor Costs: Low, especially in continuous processes.
- Use Case: Best for producing thin, flat ceramic components, like substrates for electronics.
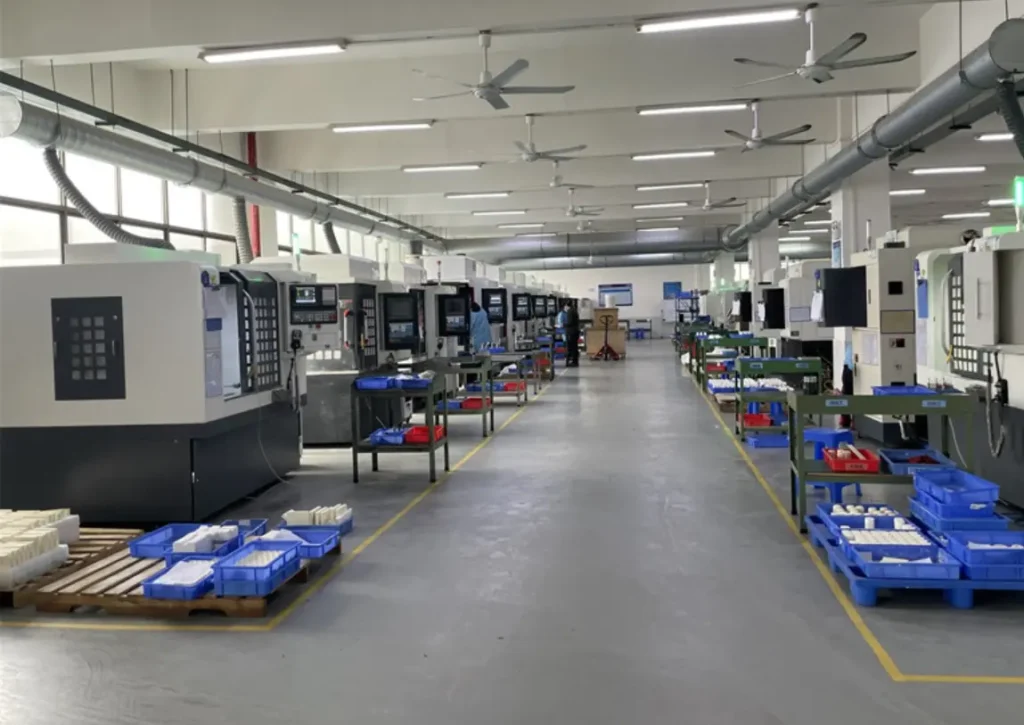
6.4. Ceramic Powder Injection Molding vs. Other Methods: Which is More Cost-Effective?
High-Volume, Complex Parts: CIM is the most cost-effective choice when producing large quantities of small, complex parts that require tight tolerances and excellent material properties. Despite higher upfront costs, the per-unit cost drops significantly with larger production runs.
Simple, Low-Volume Parts: For simpler, larger parts with lower precision requirements, traditional methods like pressing and sintering, extrusion, or slip casting may offer a more economical solution.
Customization and Precision: If the project requires intricate details, high precision, and material versatility, CIM provides superior results despite the initial higher costs.
Section 7: Why Choose Welleshaft as Your Global Supplier and Contract Manufacturer?
Welleshaft is a trusted global supplier and contract manufacturer specializing in ceramic powder injection molding. Here are some reasons why Welleshaft is the preferred choice for businesses worldwide:
Expertise: With over a decade of experience in the industry, Welleshaft has the expertise to deliver precision-engineered ceramic components that meet the highest standards.
Quality Assurance: Welleshaft is committed to quality, utilizing advanced technology and rigorous testing to ensure that every product meets or exceeds client expectations.
Customization: Welleshaft offers tailored solutions to meet the unique requirements of each project, providing a wide range of materials and design options.
Global Reach: With a strong global presence, Welleshaft is well-positioned to serve clients across various industries, offering reliable and efficient supply chain solutions.
Conclusion
Ceramic powder injection molding is a powerful manufacturing technique that combines the benefits of ceramic materials with the precision of injection molding. Whether you’re in the automotive, aerospace, electronics, or healthcare industry, CIM offers a cost-effective solution for producing high-performance components with complex geometries.
When it comes to selecting a reliable partner for your ceramic powder injection molding needs, Welleshaft stands out as a trusted global supplier and contract manufacturer. With a commitment to quality, innovation, and customer satisfaction, Welleshaft is your go-to source for precision ceramic components.