Section 1: Introduction to Aluminum Tube Bending
Curious about whether aluminum pipe can be bent? You’re not alone! Bending aluminum tubes is a common task in various industries, but it comes with its challenges. In this article, we’ll dive into everything you need to know about bending aluminum pipes, including the best methods, tools, and tips to get the job done right.
Section 2: Applications of Bent Aluminum Tubes
Bent aluminium pipes have a wide range of applications in industries such as aerospace, marine, and architecture. Custom bent aluminium pipes are used in structures, frameworks, and fluid transportation systems due to their strength and corrosion resistance. The versatility of bent aluminium pipes makes them a popular choice for various projects that require precise and durable components.
Bent Aluminum Tubes are highly versatile and used across various industries due to their lightweight, strength, and corrosion resistance. Here are some common applications:
Automotive Industry
Bent aluminum tubes are widely used in automotive manufacturing for components such as exhaust systems, roll cages, and chassis parts. Their lightweight nature helps improve vehicle performance and fuel efficiency.
Aerospace Sector
In aerospace, bent aluminum tubes are crucial for creating structural elements, supports, and frameworks. Their strength-to-weight ratio is essential for reducing overall aircraft weight while maintaining structural integrity.
Construction and Architecture
Bent aluminum tubes are used in architectural designs for handrails, frames, and support structures. They provide both functional and aesthetic benefits, including durability and a modern look.
Marine Applications
Aluminum tubes are commonly bent for use in marine environments, such as for railings, frames, and supports on boats and ships. Their resistance to corrosion makes them ideal for harsh saltwater conditions.
Furniture Design
Bent aluminum tubes are used in furniture design for creating stylish and durable pieces. They are commonly found in chairs, tables, and shelving units, combining modern aesthetics with practical functionality.
Industrial Equipment
In various industrial settings, bent aluminum tubes are used for constructing equipment frames, conveyor systems, and custom machinery. Their adaptability and strength make them suitable for diverse industrial applications.
Sports and Recreation
Bent aluminum tubes are employed in sports and recreational equipment, including bicycle frames, ski poles, and fitness equipment. Their lightweight and strong properties enhance performance and user experience.
Medical Devices
In the medical field, bent aluminum tubes are used in devices and equipment such as hospital beds, medical carts, and diagnostic instruments. Their ease of fabrication and hygienic qualities make them ideal for healthcare applications.
Bent aluminum tubes offer flexibility and durability across a wide range of applications, providing both practical and aesthetic solutions in many industries.
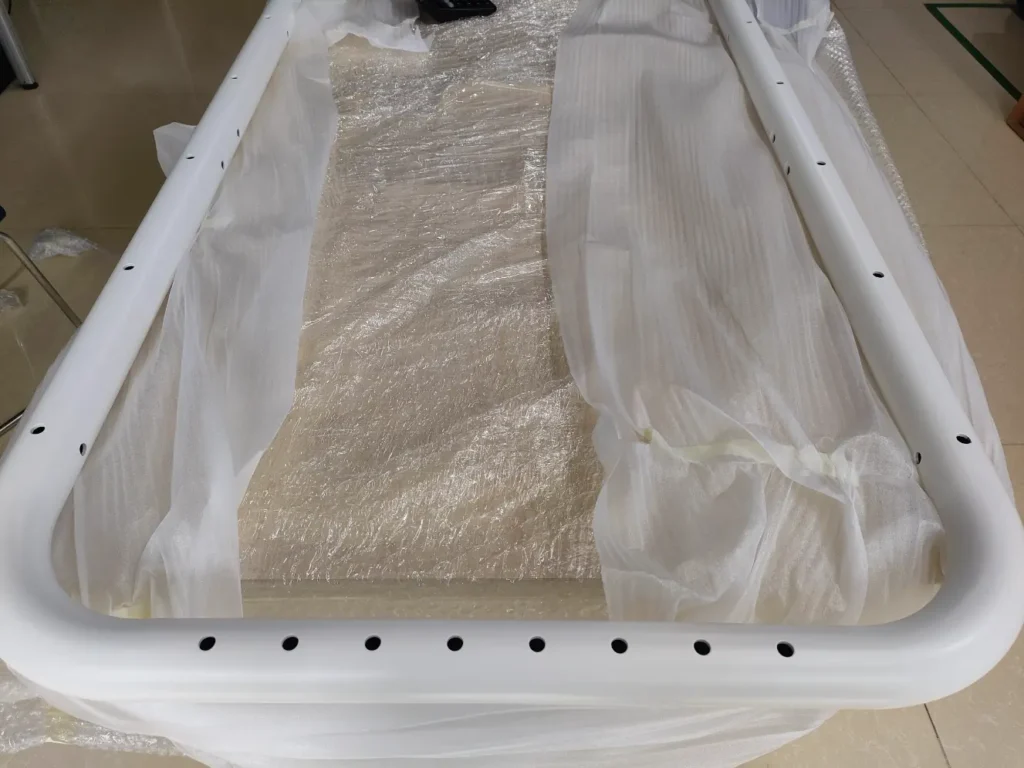
Section 3: Types of Aluminum Tubing
Aluminum pipes and tubes come in various shapes and sizes. From round pipes to square tubes, the type of aluminum you’re working with can significantly affect how you approach bending it.
1. 6061 T6 Aluminum Tubing
6061 T6 Aluminum Tubing is a versatile and highly durable aluminum alloy product ideal for a wide range of applications. Known for its excellent strength-to-weight ratio, corrosion resistance, and machinability, 6061 T6 aluminum tubing is perfect for structural components, automotive parts, aerospace frames, and more. With a T6 temper, this tubing undergoes a solution heat treatment and artificial aging process, enhancing its mechanical properties and making it exceptionally strong. Available in various sizes and configurations, 6061 T6 aluminum tubing is the go-to choice for engineers and manufacturers seeking reliable, high-performance material for their projects.
2. Thin-Walled Aluminum Tubing
Thin-Walled Aluminum Tubing offers the perfect balance of lightweight strength and precision, making it ideal for applications where weight reduction is crucial without compromising structural integrity. Renowned for its exceptional corrosion resistance and high machinability, thin-walled aluminum tubing is commonly used in aerospace, automotive, medical devices, and intricate engineering projects. Its slim profile allows for easy bending and forming, making it a favorite choice for custom fabrication and complex designs. Whether for fluid transport, protective enclosures, or lightweight structural elements, thin-walled aluminum tubing delivers unparalleled performance and reliability.
3. Aluminum Square Tubing
Aluminum Square Tubing is a versatile and robust material known for its excellent strength, durability, and corrosion resistance. This type of tubing features a square cross-section, making it ideal for both structural and architectural applications. Commonly used in construction, framing, and fabrication, aluminum square tubing is prized for its lightweight properties and ease of machining. Its uniform shape provides exceptional stability and support, making it perfect for load-bearing structures, frames, and supports in various industries. Available in multiple sizes and finishes, aluminum square tubing is the preferred choice for engineers, architects, and DIY enthusiasts looking for high-performance material with aesthetic appeal.
4. 6063 T5 Aluminum Tubing
6063 T5 Aluminum Tubing is a high-quality, versatile aluminum alloy known for its excellent extrudability and surface finish. Featuring a T5 temper, this tubing undergoes aging after extrusion, which enhances its mechanical properties and makes it well-suited for applications requiring moderate strength and good corrosion resistance. With its smooth finish and superior machinability, 6063 T5 aluminum tubing is ideal for architectural applications, structural supports, and precision components. Commonly used in window frames, railings, and other decorative elements, this tubing provides a perfect balance of strength and aesthetic appeal. Available in various sizes and lengths, 6063 T5 aluminum tubing is the top choice for projects that demand both functionality and visual quality.
Section 4: Methods of Bending Aluminum Tubes
Bending aluminum tubes can be achieved through various methods, each suited to different applications and requirements. Understanding these methods is essential for achieving precise and effective results in your projects. Here are the primary techniques:
1. Manual Bending
If you’re a DIY enthusiast, you might be interested in manual bending techniques. This method involves using basic tools like a pipe bender or even bending by hand for thin-walled tubes.
1.1 Manual Bending Techniques
If you’re a DIY enthusiast, you might be interested in manual bending techniques. This method involves using basic tools like a pipe bender or even bending by hand for thin-walled tubes.
1.2 How to Bend Aluminum Tubing by Hand
Bending aluminum tubing by hand is a practical skill for DIY enthusiasts and small-scale projects. Here’s a step-by-step guide to achieve smooth, accurate bends without the need for specialized equipment:
1.2.1 Choose the Right Tubing: Ensure you select the appropriate diameter and wall thickness of aluminum tubing for hand bending. Thinner walls and smaller diameters are easier to bend by hand.
1.2.2 Gather Tools: You’ll need a few basic tools, including a pipe bender or tubing bender, a wooden or metal form, and a clamp or vice. For smaller projects, you can use simple hand tools like pliers or a bending jig.
1.2.3 Propare the Tubing: Measure and mark the tubing where you want to make the bend. Use a marker or tape to indicate the bend point.
1.2.4 Use a Bending Tool: If you have a hand-held pipe bender, insert the tubing into the tool, aligning it with the marked bend point. Apply steady, even pressure to bend the tubing to the desired angle. For DIY solutions, you can use a wooden or metal form to support the tubing while bending.
1.2.5 Apply Heat (Optional): For tighter bends or larger diameters, gently heating the tubing with a heat gun can make the bending process easier and reduce the risk of cracking. Be cautious not to overheat, as this can affect the tubing’s properties.
1.2.6 Bend Slowly and Gradually: Apply pressure slowly and evenly to achieve a smooth bend. Avoid bending the tubing too quickly or forcing it, as this can cause deformation or kinking.
1.2.7 Check the Bend: After bending, measure the angle and ensure it meets your specifications. Make any necessary adjustments to perfect the bend.
1.2.8 Cool and Clean: If you used heat, allow the tubing to cool naturally before handling. Clean any marks or residues from the bending process.
Hand bending aluminum tubing is a cost-effective method for creating custom shapes and fittings. By following these steps and using the right techniques, you can achieve professional-quality bends for your projects.
2. Machine Bending
2.1 Aluminum Tube Bending Machines
Aluminum Tube Bending Machines are specialized tools designed to efficiently and accurately bend aluminum tubes into precise shapes and angles. These machines are crucial for industries and applications where high-quality, custom bends are required. Here’s an overview of what you need to know:
2.1.1Types of Machines: Aluminum tube bending machines come in various types, including manual, hydraulic, and CNC (Computer Numerical Control) models. Manual machines are ideal for simple, low-volume projects, while hydraulic and CNC machines offer advanced capabilities for complex, high-precision bends.
2.1.2 Machine Capabilities: These machines are designed to handle different tube diameters, wall thicknesses, and bending radii. They provide consistent results and are essential for creating uniform bends without compromising the tube’s integrity.
2.1.3 Features: Modern aluminum tube bending machines come equipped with features such as adjustable bending angles, programmable settings, and automated feeding systems. These features enhance accuracy, streamline production processes, and reduce manual labor.
2.1.4 Applications: Aluminum tube bending machines are widely used in sectors such as automotive, aerospace, construction, and manufacturing. They are ideal for producing components like frames, supports, handrails, and custom fittings.
2.1.5 Benefits: Utilizing a tube bending machine ensures high-quality bends with minimal risk of defects such as kinking or wrinkling. The machines improve efficiency, speed up production, and enable precise control over the bending process.
2.1.6 Maintenance and Care: Regular maintenance, such as lubrication and calibration, is essential to keep aluminum tube bending machines in optimal working condition. Proper care ensures longevity and consistent performance.
2.2 Aluminum Pipe Bending Machines
Aluminum Pipe Bending Machines are essential tools for efficiently and accurately shaping aluminum pipes into various configurations. Designed to handle a range of pipe sizes and bending radii, these machines offer precise control and high-quality results for industrial, commercial, and DIY applications. Here are some key aspects of aluminum pipe bending machines:
2.2.1 Types of Machines: Aluminum pipe bending machines come in several types, including manual, hydraulic, and CNC (Computer Numerical Control) models. Manual machines are ideal for small-scale projects and simple bends, while hydraulic and CNC machines are suited for high-volume production and complex bending requirements.
2.2.2 Capabilities: These machines can handle different pipe diameters and wall thicknesses, allowing for versatility in applications. They are designed to create smooth, accurate bends without compromising the structural integrity of the aluminum pipe.
2.2.3 Features: Advanced machines often include features such as adjustable bending angles, programmable controls, and automated feeding systems. These features enhance precision and efficiency, reducing manual labor and increasing production speed.
2.2.4 Applications: Aluminum pipe bending machines are widely used in industries such as automotive, aerospace, construction, and manufacturing. They are essential for creating components like frames, supports, and conduits with consistent quality and exact specifications.
2.2.5 Benefits: Using a pipe bending machine ensures uniform bends and reduces the risk of defects such as kinks or distortions. It also improves productivity by allowing for faster and more accurate bending compared to manual methods.
3. Mandrel Bending
Mandrel bending uses a mandrel inserted into the tube to support the inner surface during bending. This method helps maintain the tube’s shape and prevent kinking or wrinkling, making it ideal for precise, high-quality bends.
3.1 Aluminum Mandrel Bends
Aluminum Mandrel Bends are essential for creating high-quality, smooth bends in aluminum tubing while maintaining structural integrity and preventing deformation. This bending method utilizes a mandrel—a solid or flexible rod inserted into the tube—providing internal support and ensuring precision. Here’s an overview of aluminum mandrel bends:
3.1.1 Purpose and Benefits: Mandrel bending is crucial for producing smooth, wrinkle-free bends in aluminum tubing. It prevents kinks and collapse, particularly in tight-radius bends, ensuring that the tubing retains its strength and aesthetics.
3.1.2 Process: During the mandrel bending process, the aluminum tube is heated (if necessary) and bent around a die. The mandrel inside the tube supports the inner surface, distributing stress evenly and maintaining the tube’s shape. This method is ideal for complex bends that require high precision.
3.1.3 Types of Mandrels: Mandrels come in various forms, including rigid (solid) and flexible (collapsible). Solid mandrels are used for simple bends, while flexible mandrels can accommodate more intricate shapes and tighter radii.
3.1.4 Applications: Aluminum mandrel bends are widely used in industries such as automotive, aerospace, and manufacturing. They are perfect for applications requiring high strength and aesthetic appeal, such as exhaust systems, structural components, and custom frameworks.
3.1.5 Advantages: The mandrel bending process enhances the quality of the bend, ensuring a smooth finish and minimal material wastage. It also allows for precise control over the bend radius and angle, making it suitable for both functional and decorative applications.
3.1.6 Considerations: Proper setup and calibration of bending equipment are crucial for achieving optimal results with mandrel bends. Regular maintenance of the mandrel and bending machine ensures consistent performance and quality.
Section 5: Challenges in Bending Aluminum Tubes
Aluminum tubes are widely used in various industries due to their lightweight, corrosion resistance, and excellent thermal and electrical conductivity. However, bending aluminum tubes presents a unique set of challenges that require precision, expertise, and advanced technology. Understanding these challenges is crucial for achieving high-quality, reliable, and efficient bent aluminum components.
1. Material Characteristics and Their Impact
Ductility and Malleability: Aluminum’s inherent ductility and malleability make it a preferred material for bending, but these same properties can also lead to issues such as wrinkling and distortion. The fine balance between flexibility and strength needs careful handling to avoid compromising the structural integrity of the tube.
Work Hardening: Aluminum tends to harden when worked on, leading to increased resistance to further deformation. This characteristic requires precise control over the bending process to avoid cracking and ensure a smooth bend.
Springback Effect: Aluminum exhibits significant springback, the tendency of the material to revert partially to its original shape after bending. Accurate prediction and compensation for springback are essential to achieve the desired bend angles and radii.
2. Technical Challenges in Bending Aluminum Tubes
Tooling Design and Quality: The design and quality of the bending tools play a crucial role in the success of the bending process. Custom-designed mandrels, dies, and wiper dies are often necessary to support the tube and prevent defects such as ovality, wrinkling, and collapse.
Precision in Mandrel Placement: Mandrels, which support the tube internally during bending, must be precisely positioned to prevent internal deformation. Incorrect placement can lead to defects and compromise the tube’s functionality.
Control of Bending Speed and Force: The speed and force applied during the bending process must be meticulously controlled. Too much force can cause the tube to buckle, while insufficient force may result in incomplete bends or springback issues.
Temperature Management: Bending aluminum tubes at elevated temperatures can reduce the risk of cracking and improve ductility. However, maintaining consistent temperature control throughout the process is challenging and requires sophisticated equipment and monitoring systems.
3. Common Defects and Their Mitigation
Wrinkling: Wrinkling on the inner radius of the bend is a common defect. Using a mandrel with a closer pitch or employing a wiper die can help mitigate this issue by providing better support and reducing material flow inconsistencies.
Cracking: Cracking is often a result of excessive force or improper material handling. Ensuring proper lubrication, reducing bending speed, and optimizing tooling can help prevent cracks.
Ovality: Ovality, the deformation of the tube’s cross-section from round to oval, can be minimized by using a combination of internal mandrels and external pressure dies to maintain the tube’s shape during bending.
Thickness Variation: Uneven wall thickness is a frequent issue in bent tubes. Employing advanced techniques such as hydroforming can help maintain uniform wall thickness and improve the overall quality of the bend.
4. Advanced Techniques and Innovations
CNC Bending Machines: Computer Numerical Control (CNC) bending machines offer high precision and repeatability, allowing for complex bends with minimal defects. These machines can be programmed to adjust bending parameters in real-time, compensating for material variations and ensuring consistent results.
Hydroforming: Hydroforming uses high-pressure hydraulic fluid to form the tube into the desired shape. This technique provides excellent control over wall thickness and reduces the risk of defects, making it ideal for complex and precise bending applications.
Laser-Assisted Bending: Laser-assisted bending involves using a laser to heat the aluminum tube locally before bending. This localized heating reduces the force required for bending and minimizes the risk of defects such as cracking and springback.
Finite Element Analysis (FEA): FEA allows engineers to simulate the bending process and predict potential issues before actual production. This predictive modeling helps in optimizing the bending parameters and tooling design, reducing trial-and-error and improving efficiency.
Section 6: Avoiding Kinks and Cracks
Avoiding kinks and cracks when bending aluminum tubes is essential for maintaining the structural integrity and functionality of the finished product. Here are some best practices and techniques to help achieve smooth, defect-free bends:
1. Select the Right Alloy and Temper
Material Choice: Different aluminum alloys and tempers have varying ductility and strength characteristics. Choose an alloy and temper that offer the best combination of flexibility and strength for your specific bending application.
Common Alloys: Alloys such as 6061-T6 and 6063-T52 are often used for bending due to their good formability. However, the exact choice should depend on the specific requirements of the application.
2. Optimize Tooling Design
Mandrels: Use an appropriate mandrel to support the inside of the tube during bending. Mandrels with a closer pitch or ball-type mandrels can help distribute the bending forces more evenly, reducing the risk of kinks.
Wiper Dies: Employ wiper dies to prevent wrinkling on the inner radius of the bend. Wiper dies provide support and guide the material flow, minimizing the chances of kinks.
Bending Dies: Ensure that the bending dies are properly designed and maintained. The radius of the die should match the desired bend radius, and the die surface should be smooth to reduce friction and avoid damaging the tube.
3. Control the Bending Process
Bending Speed: Use an optimal bending speed to balance the forces applied to the tube. Too fast can lead to cracking, while too slow can cause kinks. Finding the right speed is crucial for a smooth bend.
Bending Force: Apply consistent and controlled force during the bending process. Excessive force can cause cracks, while insufficient force may lead to incomplete bends or kinks.
Lubrication: Proper lubrication reduces friction between the tube and the tooling, allowing the material to flow more smoothly and reducing the risk of kinks and cracks. Choose the right lubricant for your specific application and material.
4. Pre-Heating Techniques
Localized Heating: Pre-heating the tube at the bend point can enhance ductility and reduce the risk of cracking. Techniques like induction heating or laser-assisted bending can provide precise and localized heating.
Uniform Heating: Ensure that the heating process is uniform to prevent thermal gradients, which can cause uneven bending and increase the likelihood of defects.
5. Advanced Bending Techniques
Hydroforming: Hydroforming uses high-pressure hydraulic fluid to form the tube into the desired shape. This technique provides excellent control over wall thickness and reduces the risk of kinks and cracks.
CNC Bending: Computer Numerical Control (CNC) bending machines offer precise control over the bending parameters, ensuring consistent and defect-free bends. CNC machines can be programmed to adjust parameters in real-time, compensating for material variations.
Finite Element Analysis (FEA): Use FEA to simulate the bending process and identify potential issues before actual production. FEA helps optimize the bending parameters and tooling design, reducing trial-and-error and improving efficiency.
6. Post-Bend Inspection and Quality Control
Non-Destructive Testing (NDT): Use NDT methods such as ultrasonic testing, radiographic testing, or dye penetrant inspection to detect any hidden cracks or defects in the bent tubes.
Visual Inspection: Perform thorough visual inspections to identify surface defects such as kinks, cracks, and wrinkles. Addressing these issues early ensures the final product meets quality standards.
Dimensional Inspection: Use precision measurement tools to check the bend angles, radii, and overall dimensions of the bent tubes. Ensuring dimensional accuracy helps maintain the functionality and fit of the final product.
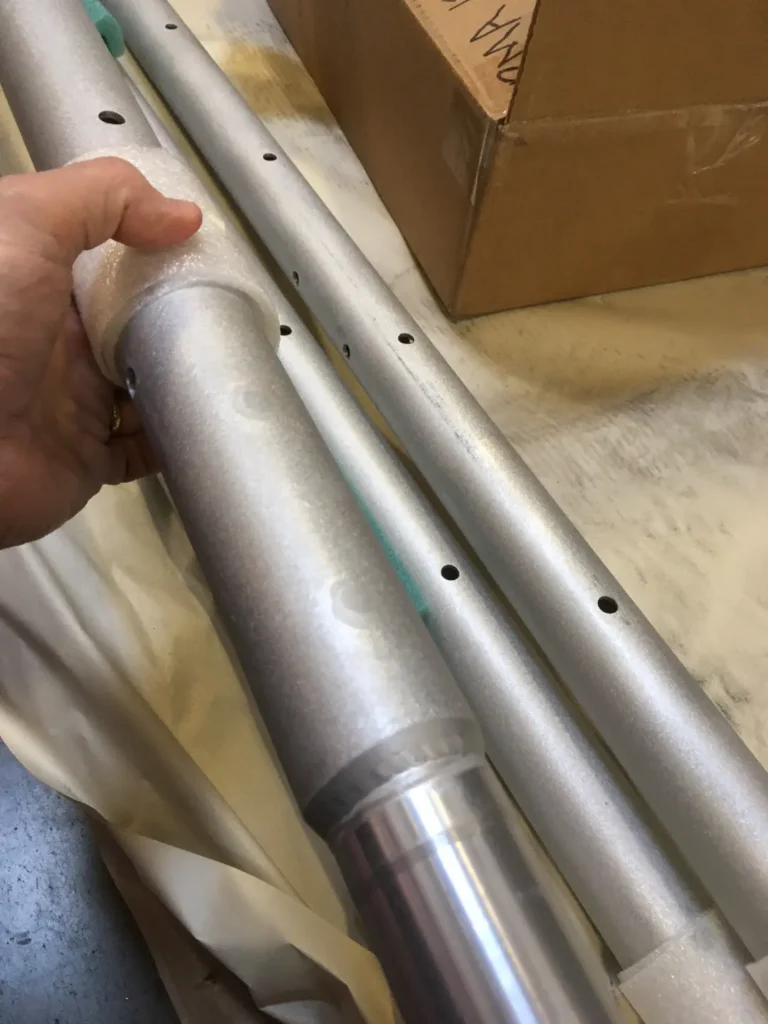
Section 7: Tig Welding Aluminum Pie Cut Tubing
TIG welding aluminum pie cut tubing can be challenging, but with the right techniques and attention to detail, you can achieve high-quality welds. Here are some tips and welding experiences to help you reduce welding issues and improve your results:
1. Proper Preparation
Clean the Aluminum Thoroughly: Aluminum must be free of any contaminants, such as oil, grease, and oxide layers. Use a dedicated stainless steel brush to clean the tubing just before welding. Acetone is also effective for removing surface contaminants.
Fit-up and Tacking: Ensure the pie cut segments fit together perfectly. Use clamps or fixtures to hold the pieces in place. Tack weld at several points to maintain alignment during welding.
2. Choosing the Right Equipment and Settings
TIG Welder: Use a high-frequency TIG welder with AC capability, as aluminum requires alternating current for effective welding.
Electrode: Use a sharpened 2% lanthanated or thoriated tungsten electrode. The electrode tip should be slightly rounded for AC welding.
Shielding Gas: Use 100% pure argon gas. Ensure a consistent gas flow rate (around 15-20 CFH) to protect the weld area from contamination.
3. Welding Technique
Preheat: For thicker aluminum tubing, preheating can help reduce warping and improve weld penetration. Preheat to around 300°F (150°C) using an oxy-acetylene torch or a heating blanket.
Puddle Control: Establish a stable weld puddle before adding filler rod. Keep the torch angle between 70-80 degrees to the workpiece and maintain a tight arc length.
Filler Material: Use a filler rod with a similar alloy composition to the tubing. Common choices are 4043 or 5356 aluminum filler rods.
Travel Speed: Maintain a steady and consistent travel speed. Too slow can cause burn-through, while too fast can lead to poor penetration and weak welds.
4. Addressing Common Welding Issues
Porosity: Ensure clean base metal and filler rod, and maintain proper gas coverage. Porosity often results from contaminants or inadequate shielding gas.
Cracking: Cracks can occur due to rapid cooling or excessive heat input. Control the heat by adjusting the amperage and using a proper torch angle. Post-weld heat treatment or stress relieving can also help prevent cracking.
Warpage: Warping can be minimized by using proper fixturing, preheating thicker sections, and controlling heat input. Allow the weld to cool gradually to avoid thermal distortion.
5. Post-Welding Tips
Inspection: Inspect the welds for any defects such as cracks, porosity, or incomplete fusion. Visual inspection and non-destructive testing (NDT) methods like dye penetrant testing can be helpful.
Cleaning: After welding, clean the weld area to remove any residual oxide or contaminants. This can improve the appearance and longevity of the welds.
Practice and Patience: TIG welding aluminum pie cut tubing requires practice and patience. Start with simple joints and gradually move to more complex shapes as you gain confidence and experience.
Welding Experience Insights
Heat Management: One of the most critical aspects of TIG welding aluminum is managing heat input. Too much heat can cause burn-through, while too little can lead to weak welds. Adjusting the amperage and using a pulsed current can help control heat input effectively.
Consistency: Consistency in your technique, such as maintaining a steady hand and consistent travel speed, is crucial for achieving high-quality welds. Practice on scrap pieces to develop a feel for the process.
Comfort and Ergonomics: Ensure you are comfortable and have good visibility of the weld area. Proper ergonomics can make a significant difference in the quality of your welds.
Documentation: Keep a welding log to document the settings, techniques, and outcomes of your welds. This can help you identify what works best and make adjustments for future projects.
By following these tips and continuously refining your skills, you can achieve excellent results in TIG welding aluminum pie cut tubing, reducing common welding issues and producing strong, aesthetically pleasing welds.
Conclusion
In conclusion, aluminium pipes can be bent using the right tools, techniques, and expertise. By understanding the fundamentals of aluminium pipe bending, manufacturers can create custom shapes and structures that meet the unique needs of their projects. Whether in construction, automotive, or manufacturing, bent aluminium pipes offer versatility and durability for a wide range of applications.
Why Choose Welleshaft?
We offer top-notch services, state-of-the-art equipment, and a dedicated team of experts. Our commitment to quality and customer satisfaction sets us apart.
At Welleshaft, we specialize in custom aluminum tube bending. With over 13 years of experience, we handle projects of all sizes with precision and care.
Ready to revolutionise mechanical engineering with Aluminum Tube bending Builder? Let us help you understand how bending aluminum tube Builder can help you with your aluminum bending tube manufacturing. To learn more about the future of aluminum tube-building technology, Visit our website or contact our sales team.
FAQs
Can you bend an aluminium tube?
Yes, aluminium tubes can be bent using the appropriate tools and techniques.
What type of aluminium tubing is bendable?
Most types of aluminium tubing, including seamless and welded options, but some alloys, like 6061 T6, require more care due to their heat-treated nature.can be bent with the right equipment.
Can you bend 6061 aluminium tube?
– 6061 aluminium tube is commonly used for bending due to its excellent formability and weldability.
How to bend aluminium pipe without a bender?
While a pipe bender is the most effective tool for bending aluminium pipes, it is possible to bend them by hand with caution and precision.
What is the best way to bend aluminium?
The best way to bend aluminum depends on the project. For precise bends, using a mandrel and an aluminum tube bending machine is ideal. For DIY projects, manual bending with the right tools can be effective.
How to bend aluminum pipe without breaking it?
To bend aluminum pipe without breaking it, use a mandrel or fill the pipe with sand to support it during bending. Applying heat can also help.
How to Bend Thin Wall Aluminum Tubing?
Thin wall aluminum tubing requires gentle handling. Using a mandrel or filling the tube with sand before bending can help maintain its shape.