Brass Forging: A Comprehensive Guide
Brass forging is a crucial process in manufacturing high-quality brass components used in various applications. Whether you’re a manufacturer, engineer, or hobbyist, understanding brass forging and its benefits can help you make informed decisions about purchasing forged brass parts. In this article, we’ll explore everything you need to know about brass forging, including the differences between hot and cold forging, and what to consider when buying forged brass products.
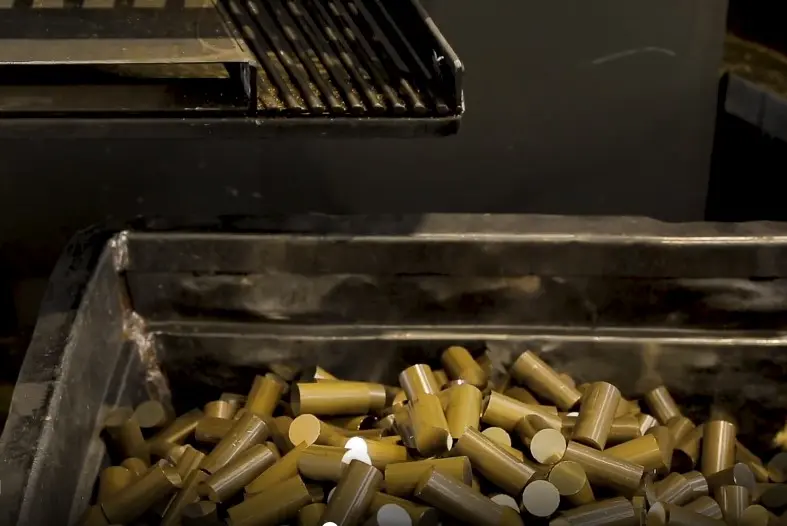
Frequently Asked Questions (FAQs) about Brass Forging
1. What is brass forging?
Brass forging is a metalworking process where brass is shaped using compressive forces. This process typically involves heating the brass to make it more malleable and then applying mechanical pressure to shape it. Forging improves the material’s strength, durability, and mechanical properties by refining its grain structure.
2. Is brass good for forging?
Yes, brass is good for forging. Its malleability and ductility make it an ideal material for forging processes. The alloy’s ability to withstand deformation without cracking or breaking allows it to be shaped into a variety of forms, making it suitable for both hot and cold forging applications.
3. At what temperature can you forge brass?
Brass is typically forged at temperatures between 800°C and 900°C (1470°F and 1650°F) for hot forging. This range ensures that the brass remains ductile and easier to shape. For cold forging, brass is worked at or near room temperature, usually below 200°C (392°F).
4. How to forge brass without it cracking?
To forge brass without it cracking, consider the following tips:
- Control Temperature: Ensure the brass is heated to the correct forging temperature to maintain its ductility.
- Proper Equipment:Use the appropriate forging machine and techniques to apply even pressure.
- Use Lubricants: Apply lubricants to reduce friction and prevent material stress.
- Gradual Deformation:Apply gradual pressure to avoid sudden changes in shape that could cause cracking.
5. Forged brass vs. bronze: What’s the difference?
Brass and bronze are two distinct copper-based alloys commonly used in forging, but they have different properties due to their unique compositions.
5.1. Composition:
Brass: Primarily composed of copper and zinc. The zinc content typically ranges from 5% to 40%, which gives brass its yellowish color.
Bronze: Made mainly of copper and tin, though modern bronzes may also include aluminum, manganese, or other metals. The tin content typically ranges from 12% to 25%, leading to a more reddish-brown color.
5.2. Strength and Durability:
Forged Brass: Brass is known for its malleability, making it easier to forge into intricate shapes. However, it is softer and less durable compared to bronze. Brass forgings are widely used in decorative items, plumbing, and electrical components where lower strength is acceptable.
Forged Bronze: Bronze, on the other hand, is stronger and more durable than brass. This makes forged bronze a better choice for applications requiring higher wear resistance and strength, such as in gears, bearings, and heavy-duty tools.
5.3. Corrosion Resistance:
Forged Brass: Brass has good corrosion resistance, especially in freshwater environments, but it can tarnish over time, especially when exposed to air or moisture.
Forged Bronze: Bronze has excellent corrosion resistance, particularly in marine environments, which makes it the preferred material for ship components, valves, and pumps.
5.4. Cost:
Brass: Generally less expensive than bronze because zinc, one of its primary components, is cheaper than tin.
Bronze: More expensive due to the higher cost of tin and other alloying metals that provide added strength and resistance.
5.5. Applications:
Brass: Common in decorative hardware, musical instruments, plumbing fixtures, and low-load bearings.
Bronze: Used in high-strength applications like bushings, bearings, marine components, and heavy-duty industrial parts.
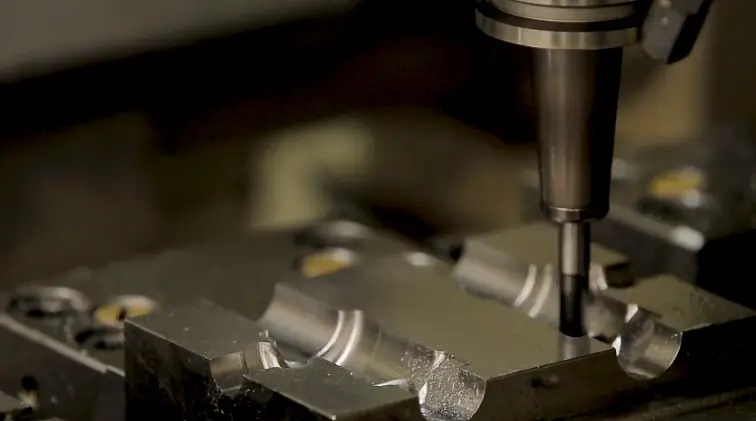
6. What is the difference between forged brass and standard brass?
The primary difference between forged brass and standard brass (usually referring to cast or machined brass) lies in how they are manufactured, which affects their mechanical properties, strength, and overall quality.
6.1. Manufacturing Process:
- Forged Brass: Brass is shaped by applying intense heat and pressure in a forging process. The material is heated until it becomes malleable, then mechanically compressed into the desired shape. This process refines the grain structure of the metal, making it denser and stronger.
- Standard Brass: Often refers to cast brass, where molten brass is poured into a mold to take its shape. Once solidified, the casting may undergo machining to achieve the final shape and dimensions. This process creates a more porous and less uniform internal structure compared to forging.
6.2. Grain Structure:
- Forged Brass: Has a more refined and continuous grain structure. The forging process aligns the grain flow according to the shape of the part, improving its mechanical properties and making it stronger and more resistant to cracking or failure.
- Standard Brass (Cast or Machined): The grain structure is not as controlled. In cast brass, the grain structure is often random and more prone to porosity or internal defects, which can reduce its strength.
6.3. Strength and Durability:
- Forged Brass: Due to the improved grain structure, forged brass is stronger, tougher, and more durable. It can withstand higher mechanical stresses and is less likely to crack or deform under load.
- Standard Brass: While still strong, cast brass is generally weaker than forged brass due to potential internal defects like porosity, which can act as stress concentrators.
6.4. Corrosion Resistance:
- Forged Brass: Generally offers slightly better corrosion resistance because it has fewer internal defects and a more compact structure. This makes it less susceptible to corrosion, especially in harsh environments.
- Standard Brass: The casting process may leave more internal voids or imperfections, which can make it slightly more prone to corrosion over time.
6.5. Surface Finish:
- Forged Brass: Usually has a smoother surface finish right after the forging process, with fewer imperfections. It may require less finishing or polishing to achieve a desired appearance.
- Standard Brass: Often requires more machining and polishing after casting to achieve a smooth finish, as the casting process can result in rough surfaces or uneven areas.
6.6. Applications:
- Forged Brass: Preferred for high-strength applications such as valves, fittings, and components that experience significant stress or wear. It’s also common in applications where precision and durability are critical, like in plumbing and marine components.
- Standard Brass: Often used in decorative items, lower-load mechanical parts, or applications where strength is less critical but cost-efficiency is important.
7. What are brass forging parts used for?
Brass forging parts are widely used in various industries due to their excellent combination of strength, corrosion resistance, and aesthetic appeal. Forged brass components are particularly valued for their durability, precision, and enhanced mechanical properties, making them suitable for demanding applications. Here are some common uses of brass forging parts:
7.1. Plumbing and Water Supply
- Valves: Forged brass valves are often used in plumbing systems due to their strength, durability, and resistance to corrosion and water-related wear.
- Pipe Fittings: Brass forging parts such as elbows, tees, couplings, and unions are commonly used in water supply lines because they resist rust and provide a reliable, long-lasting seal.
- Hose Connectors: Brass hose connectors are preferred for their durability and leak-proof qualities in both residential and industrial plumbing.
7.2. HVAC Systems
- Components in Heating and Cooling Systems: Forged brass parts are used in various components of HVAC systems, such as manifolds, valves, and fittings, to ensure efficient temperature control and resistance to wear from constant use.
- Thermostat Parts: Brass is used for small components in HVAC systems, particularly where thermal conductivity and corrosion resistance are required.
7.3. Electrical and Electronics
- Electrical Connectors: Brass forging parts are widely used in electrical connectors, terminals, and sockets due to their good electrical conductivity and corrosion resistance.
- Battery Terminals: In automotive and industrial battery systems, brass is used to make forged battery terminals because it provides a reliable connection and resists corrosion.
7.4. Marine Industry
- Marine Hardware: Brass forging parts, such as cleats, hinges, and brackets, are commonly used in marine environments because of their excellent corrosion resistance to saltwater and moisture.
- Propeller Shafts and Couplings: Brass is also used in propeller shafts and couplings, where resistance to corrosion and wear is essential for longevity in seawater environments.
7.5. Automotive Industry
- Brake Components: Forged brass parts like brake fittings and connectors are used in the automotive industry for their durability and ability to withstand high-pressure environments.
- Fuel System Components: Brass is also used in various fuel system components because of its resistance to gasoline, diesel, and other fuels.
7.6. Musical Instruments
- Brass Wind Instruments: Forged brass is used to create parts for instruments like trumpets, trombones, and saxophones due to its acoustic properties and resistance to corrosion from saliva and moisture.
7.7. Industrial and Manufacturing Equipment
- Machinery Components: Forged brass parts are used in various machinery components, such as gears, bushings, and bearings, due to their wear resistance, strength, and good machinability.
- Pumps and Compressors: Brass forging is used in pumps and compressors for components like impellers, where both strength and corrosion resistance are needed.
7.8. Aerospace Industry
- Hydraulic Fittings: Brass forged parts are commonly used in hydraulic systems in the aerospace sector, where high pressure and precise fittings are critical for performance and safety.
- Landing Gear Components: Forged brass is used in small but essential landing gear parts that require durability and resistance to fatigue.
7.9. Firefighting Equipment
- Nozzles and Fittings: Brass is widely used in the manufacture of nozzles, hose fittings, and couplings for firefighting equipment, as it is highly resistant to corrosion, heat, and mechanical wear.
7.10. Decorative Hardware
- Door Handles and Hinges: Brass forging parts are used in architectural hardware like door handles, hinges, and locks due to their aesthetic appeal, resistance to tarnishing, and strength.
- Lighting Fixtures: Forged brass is also popular for chandeliers, sconces, and other lighting fixtures, combining both decorative appeal and durability.
7.11. Instrumentation
- Pressure Gauges and Flow Meters: Brass forging parts are used in sensitive instruments such as pressure gauges and flow meters for their corrosion resistance, machinability, and ability to form tight seals.
7.12. Gas and Oil Industry
- Gas Regulators and Meters: Forged brass parts are used in gas regulators and meters for their corrosion resistance and durability in gas distribution systems.
- Valves and Fittings: Brass is commonly used for valves and fittings in gas and oil applications, particularly in high-pressure systems that require strong, leak-proof connections.
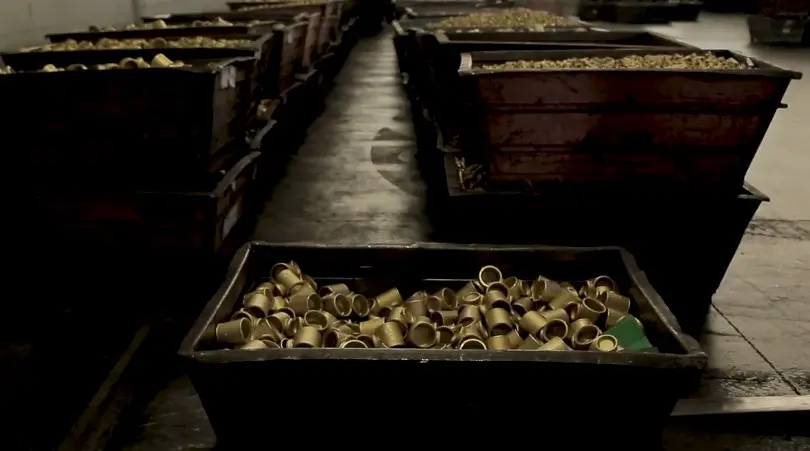
8. How do I choose a brass forging manufacturer?
When selecting a brass forging manufacturer, consider the following:
- Experience and Expertise:Look for companies with a proven track record in brass forging.
- Capabilities:Ensure they offer the forging processes you need (hot or cold forging).
- Quality Control: Check their quality assurance practices and certifications.
- Customer Service:Evaluate their responsiveness and willingness to accommodate custom orders.
See what today’s brass forging manufacturing does for businesses. Contact us for additional information and the best advice.
9. What factors affect the price of forged brass?
The price of forged brass can be influenced by several factors:
- Complexity of the Part:More intricate designs may cost more to produce.
- Type of Forging Process: Hot forging is often more cost-effective for large volumes, while cold forging may be more expensive.
- Material Costs: Prices of raw brass materials can fluctuate.
- Order Quantity:Larger orders may reduce the per-unit cost.
10. Can brass be forged with copper?
Yes, brass and copper can be forged together. Brass is an alloy of copper and zinc, so forging brass inherently involves copper. Copper itself can be forged, but it is often alloyed with other metals to improve its properties and suitability for specific applications.
11. What is Naval Brass?
Naval brass is a copper-based alloy that typically consists of 60% copper, 39% zinc, and 1% tin. The addition of tin significantly enhances the corrosion resistance of the alloy, especially in marine environments, making it more resistant to seawater and reducing dezincification (the process where zinc is selectively leached out of brass).
Key Composition:
Copper (Cu): 60%
Zinc (Zn): 39%
Tin (Sn): 1%
This composition gives naval brass a unique set of properties that make it suitable for demanding conditions, particularly in naval and maritime applications where materials must withstand harsh environments.Naval brass is commonly used in shipbuilding and other marine applications.
Conclusion
Brass forging is a versatile and effective process for creating high-quality brass components. Understanding the differences between hot and cold forging, the importance of forging temperature, and the factors affecting brass forging prices can help you make informed decisions when purchasing forged brass products. By choosing the right brass forging company and process, you can ensure that you receive components that meet your specific needs and stand up to the demands of your application.
For those looking for brass forging for sale, be sure to research suppliers, compare prices, and evaluate their offerings to find the best match for your requirements. With the right information and resources, you can make the most of brass forging and benefit from its many advantages in your projects.