Bevel Gears for Power Transmission & Angle Drives
Bevel gears are essential components in mechanical systems, playing a vital role in transmitting power between intersecting shafts. Their unique conical shape allows for changes in rotational direction, making them indispensable in various applications, from automotive differentials to industrial machinery. This article explores the diverse world of bevel gears, covering their types, applications, and the factors to consider when selecting the right gear for your needs.
What are Bevel Gears?
Bevel gears are gears with teeth cut on a conical surface. This design allows them to transmit power between shafts that intersect, typically at a 90-degree angle, but other angles are also possible. This capability makes them distinct from parallel-axis gears like spur and helical gears, which cannot change the direction of rotation.
Types of Bevel Gears
The world of bevel gears is diverse, with several types tailored to specific applications and performance requirements. Understanding these differences is crucial for selecting the optimal gear for your system.
Straight Bevel Gears: The simplest type, straight bevel gears, have teeth that are straight and taper towards the apex of the cone. They are cost-effective to manufacture and suitable for low-to-moderate speed applications. They generate more noise than other types due to the sudden engagement of the teeth.
Spiral Bevel Gears: Featuring curved teeth that are obliquely oriented, spiral bevel gears offer smoother and quieter operation compared to straight bevel gears. The curved teeth allow for gradual engagement, reducing impact and noise. They are commonly used in high-speed and high-load applications, such as automotive differentials.
Zerol Bevel Gears: Zerol bevel gears are similar to spiral bevel gears but have teeth with a zero-degree spiral angle at the mean radius. This design minimizes thrust loads, making them suitable for applications where thrust management is critical.
Hypoid Gears: Hypoid gears are a variation of spiral bevel gears where the pinion axis is offset from the gear axis. This offset allows for larger gear ratios and enables the pinion to be larger, providing increased strength. Hypoid gears are commonly found in automotive differentials, offering a compact and robust solution for transmitting power to the wheels.
Miter Gears: Miter gears are bevel gears designed to transmit power between shafts intersecting at a 90-degree angle with a 1:1 gear ratio. They are commonly used in applications where equal torque and speed are required on both shafts.
Applications of Bevel Gears
Bevel gears find widespread use in various industries and applications, thanks to their ability to change the direction of rotation and efficiently transmit power.
Automotive: Bevel gears are critical components in automotive differentials, transmitting power from the driveshaft to the wheels while allowing them to rotate at different speeds during turns. Hypoid gears are particularly common in this application due to their strength and compact design.
Aerospace: In aircraft, bevel gears are used in helicopter transmissions to transfer power from the engine to the rotors. Their ability to handle high loads and operate reliably in demanding environments makes them essential for flight safety.
Industrial Machinery: Bevel gears are employed in a wide range of industrial machinery, including conveyors, machine tools, and printing presses. They provide efficient power transmission and allow for flexible machine designs.
Marine: In marine applications, bevel gears are used in propulsion systems to transfer power from the engine to the propeller shaft. They must be able to withstand harsh conditions and provide reliable performance in marine environments.
Agricultural Equipment: Bevel gears are found in agricultural machinery such as tractors and harvesters, transmitting power to various components and enabling efficient operation in the field.
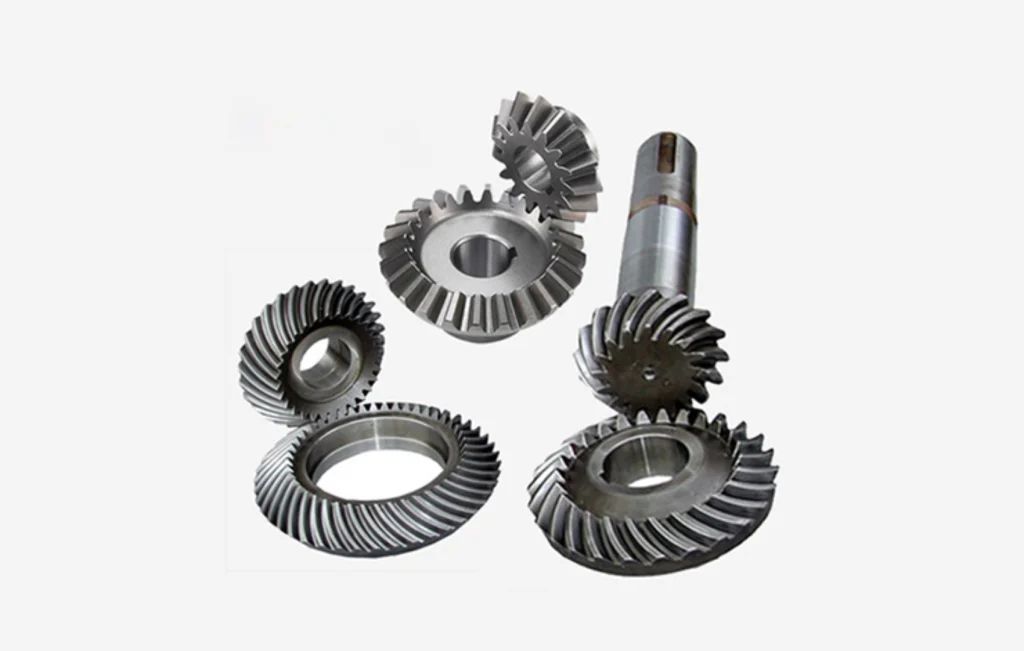
Advantages of Bevel Gears
Like any mechanical component, bevel gears have their own set of advantages and disadvantages:
Change of Direction: The primary advantage of bevel gears is their ability to transmit power between intersecting shafts, allowing for changes in rotational direction.
High Power Transmission: Bevel gears can efficiently transmit high levels of power, making them suitable for demanding applications.
Compact Design: Hypoid gears, in particular, offer a compact design that can be advantageous in space-constrained applications.
Versatility: Bevel gears are available in various types and sizes, allowing for customization to meet specific application requirements.
Factors to Consider When Selecting Bevel Gears
Selecting the right bevel gear for your application requires careful consideration of several factors:
Torque and Speed Requirements: Determine the torque and speed requirements of your application to ensure the selected gear can handle the load and operate efficiently.
Gear Ratio: Calculate the required gear ratio to achieve the desired speed and torque output.
Shaft Angle: Specify the angle between the intersecting shafts to ensure proper gear mesh.
Operating Environment: Consider the operating environment, including temperature, humidity, and exposure to contaminants, to select a gear material that can withstand the conditions.
Noise Level: If noise is a concern, opt for spiral or Zerol bevel gears, which offer quieter operation than straight bevel gears.
Thrust Load Capacity: Determine the thrust load capacity required to handle the loads generated by the bevel gear.
Material Selection: Choose a gear material that offers the required strength, durability, and resistance to wear and corrosion. Common materials include steel, cast iron, and aluminum.
Material Selection for Bevel Gears
The material used in bevel gear manufacturing significantly impacts the gear’s performance, durability, and overall lifespan. Common materials include:
Steel: High-carbon steel alloys offer excellent strength, hardness, and wear resistance, making them ideal for high-load and high-speed applications.
Alloy Steel: Alloy steels like chrome-molybdenum and nickel-chromium steels offer enhanced toughness, fatigue resistance, and heat treatment capabilities.
Cast Iron: Cast iron provides good vibration damping properties and is suitable for moderate-load applications. It is often used for larger gears where weight is a concern.
Aluminum: Aluminum alloys offer a lightweight alternative to steel and cast iron. They are suitable for low-load applications where weight reduction is a priority.
Plastics: Engineered plastics like nylon and acetal can be used for bevel gears in low-load, low-speed applications where noise reduction is critical.
Bevel Gear Terminology
Understanding the terminology associated with bevel gears is essential for effective communication and accurate specifications:
Pitch Cone: The imaginary cone on which the teeth of the bevel gear are formed.
Pitch Angle: The angle between the pitch cone and the gear axis.
Face Width: The width of the gear tooth measured along the pitch cone.
Module: A measure of the size of the gear teeth.
Pressure Angle: The angle between the tooth profile and a radial line at the pitch point.
Backlash: The amount of clearance between mating gear teeth.
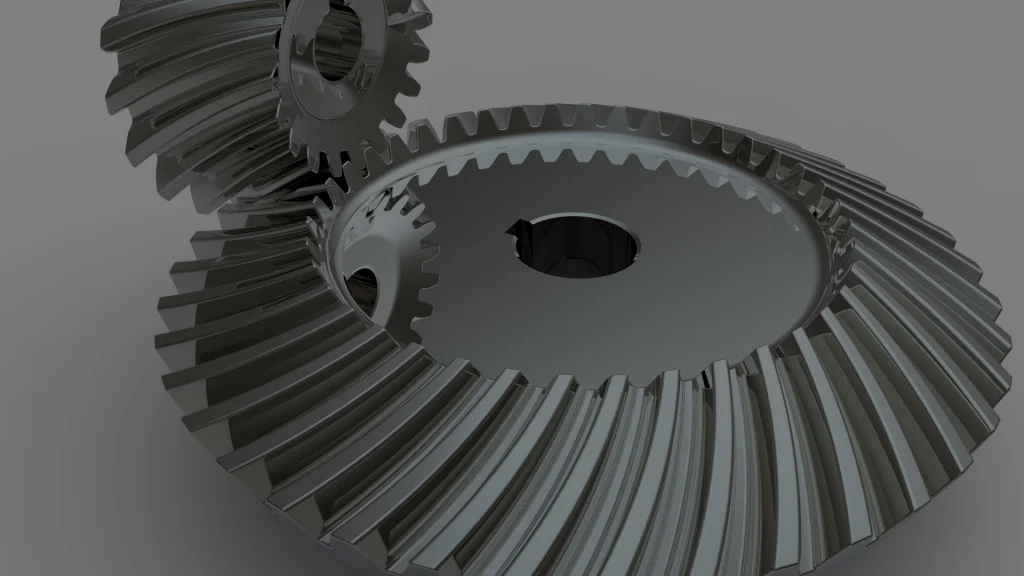
Sheet Table: Bevel Gear Type Comparison
Feature | Straight Bevel Gear | Spiral Bevel Gear | Zerol Bevel Gear | Hypoid Gear |
Tooth Shape | Straight | Curved | Curved (Zero Angle) | Curved |
Noise Level | High | Medium | Low | Low |
Thrust Load | High | Medium | Low | Low |
Speed | Low to Moderate | High | High | High |
Strength | Moderate | High | High | Very High |
Application | Simple drives | Automotive differentials | Aerospace | Automotive differentials |
Cost | Low | Moderate | Moderate | High |
Partnering with a Trusted Manufacturer
When sourcing bevel gears for your critical applications, selecting a reliable and experienced manufacturer is paramount. Welleshaft stands out as a global leader in gear manufacturing, offering a comprehensive range of bevel gear solutions and custom manufacturing services. With decades of expertise, Welleshaft is committed to delivering high-quality, precision-engineered gears that meet the most demanding performance requirements.
Why Choose Welleshaft?
Extensive Product Range: Welleshaft offers a wide variety of bevel gears, including straight, spiral, Zerol, and hypoid gears, catering to diverse applications.
Custom Manufacturing: Welleshaft provides custom gear manufacturing services, allowing you to tailor gears to your exact specifications and unique application needs.
High-Quality Materials: Welleshaft utilizes premium-grade materials to ensure superior strength, durability, and longevity of its bevel gears.
Advanced Manufacturing Processes: Welleshaft employs state-of-the-art manufacturing processes and equipment to achieve exceptional precision and quality.
Global Reach: With a global presence, Welleshaft can efficiently serve customers worldwide, providing timely delivery and responsive customer support.
Expert Engineering Support: Welleshaft’s team of experienced engineers offers expert guidance and support, helping you select the optimal bevel gear solution for your application.
Welleshaft as Your Contract Manufacturer
Welleshaft’s capabilities extend beyond standard gear manufacturing to include comprehensive contract manufacturing services. By partnering with Welleshaft, you can leverage their expertise, resources, and advanced manufacturing facilities to streamline your production processes and reduce costs.
Design and Engineering Support: Welleshaft’s engineers can assist you with gear design, optimization, and prototyping, ensuring your gears meet your exact performance requirements.
Material Procurement: Welleshaft has established relationships with leading material suppliers, ensuring access to high-quality materials at competitive prices.
Manufacturing and Machining: Welleshaft’s advanced manufacturing facilities can handle a wide range of gear manufacturing processes, including gear cutting, grinding, heat treatment, and finishing.
Quality Control: Welleshaft maintains rigorous quality control standards throughout the manufacturing process, ensuring that every gear meets the highest quality standards.
Assembly and Testing: Welleshaft can provide complete assembly and testing services, ensuring that your gears are ready for installation and operation.
Conclusion
Bevel gears are indispensable components for transmitting power between intersecting shafts and facilitating angle drives in a wide range of applications. Understanding the different types of bevel gears, their advantages and disadvantages, and the factors to consider when selecting a gear is crucial for optimizing system performance. Partnering with a trusted manufacturer like Welleshaft can ensure access to high-quality, precision-engineered bevel gears that meet your specific needs and deliver reliable performance for years to come. By choosing the right bevel gear and manufacturer, you can unlock the full potential of your mechanical systems and achieve optimal power transmission efficiency.