Aluminum Nitride Ceramic Processing for Electronics & Thermal Management
In the ever-evolving landscape of electronics, thermal management is becoming increasingly crucial for ensuring the reliability and longevity of devices. Among the many materials available, Aluminum Nitride (AlN) ceramics have emerged as a top contender, offering an exceptional combination of thermal conductivity, electrical insulation, and mechanical strength. This article explores the intricate world of Aluminum Nitride ceramic processing, detailing the technologies, properties, and applications that make it a game-changer in the electronics and thermal management sectors.
Section 1 Why Choose Aluminum Nitride?
Before diving into the intricacies of processing, it’s essential to understand why AlN is gaining so much attention. The allure of Aluminum Nitride stems from a remarkable combination of characteristics:
1.1 Exceptional Thermal Conductivity: AlN boasts a thermal conductivity several times greater than traditional aluminum oxide (alumina) ceramics, rivaling some metals. This property allows for highly efficient heat dissipation, crucial for high-power electronics.
1.2 High Electrical Insulation: Despite its impressive thermal conductivity, AlN maintains excellent electrical insulation properties, preventing short circuits and ensuring reliable performance.
1.3 Low Coefficient of Thermal Expansion (CTE): Its CTE closely matches that of silicon and other common semiconductor materials, minimizing stress and cracking due to thermal expansion mismatches in assembled devices.
1.4 Chemical Inertness: AlN is highly resistant to chemical attack and corrosion, ensuring longevity and reliability in harsh operating environments.
1.5 High Strength and Hardness: AlN ceramics are mechanically robust, able to withstand the rigors of electronic manufacturing processes and demanding operational conditions.
These attributes collectively position AlN as an indispensable material for applications where thermal management and electrical integrity are critical.
Section 2 The Intricacies of Aluminum Nitride Ceramic Processing
The journey from raw materials to finished AlN components is complex, involving several carefully controlled stages. Below is an overview of these processing steps:
2.1 Powder Preparation
The starting point is the production of high-purity AlN powder. This involves several chemical and physical processes designed to ensure the powder possesses the ideal particle size, morphology, and chemical composition. The resulting powder’s quality significantly impacts the performance of the final ceramic components. Key considerations here include:
2.1.1 Purity: High purity AlN powder is required to achieve optimal thermal conductivity.
2.1.2 Particle Size and Distribution: Controlling the particle size is critical for achieving uniform packing and sinterability.
2.1.3 Surface Area: A higher specific surface area can aid in the sintering process.
2.2 Powder Forming
Once the powder is prepared, the next step is to form it into the desired shape. Various methods are employed:
2.2.1 Dry Pressing: This is a common and cost-effective method for creating simple shapes.
2.2.2 Cold Isostatic Pressing (CIP): CIP involves applying pressure from all directions to compress the powder into more complex shapes, resulting in higher densities and more uniform parts.
2.2.3 Tape Casting: Often used for creating thin AlN substrates, the powder is mixed with a binder and solvent, then cast into a thin sheet, which can then be stacked, laminated, and cut into desired shapes.
2.2.4 Extrusion: This method is used for creating components with a constant cross-section, such as rods or tubes.
2.2.5 Injection Molding: A method allowing for the mass production of complex-shaped parts.
2.3 Sintering
Sintering is a crucial step where the formed powder part is heated to high temperatures (typically >1700°C) to consolidate the particles into a dense ceramic body. Different sintering methods exist:
2.3.1 Pressureless Sintering: The most cost-effective sintering method performed under a controlled atmospheric condition to densify the AlN part.
2.3.2 Hot Pressing (HP): Applies uniaxial pressure during sintering, resulting in higher densities and faster sintering times.
2.3.3 Hot Isostatic Pressing (HIP): Applies isostatic pressure during sintering, resulting in high density and uniform properties.
2.3.4 Spark Plasma Sintering (SPS): Utilizes electric current to rapidly heat and sinter the powder, offering shorter sintering cycles and improved mechanical properties.
2.4 Machining and Finishing
After sintering, the ceramic parts may require further processing to meet precise dimensional requirements:
2.4.1 Grinding: Used for achieving precise dimensions and surface finishes.
2.4.2 Lapping: A refining process used to achieve very smooth surface finishes.
2.4.3 Laser Cutting: Used to create intricate shapes and cut-outs.
2.4.4 Polishing: Used for extremely smooth surface finishes.
2.5 Quality Control
Throughout the entire processing chain, stringent quality checks are essential. This includes:
2.5.1 Powder Characterization: Testing for particle size, distribution, purity, and surface area.
2.5.2 Density Measurement: Ensuring the sintered part has achieved the required density.
2.5.3 Dimensional Checks: Ensuring the final parts meet required specifications.
2.5.4 Non-Destructive Testing: Used for flaw detection using methods like X-ray imaging, ultrasound, and microscopy.
2.5.5 Property testing: Includes tests for thermal conductivity, electrical resistance, and mechanical strength.
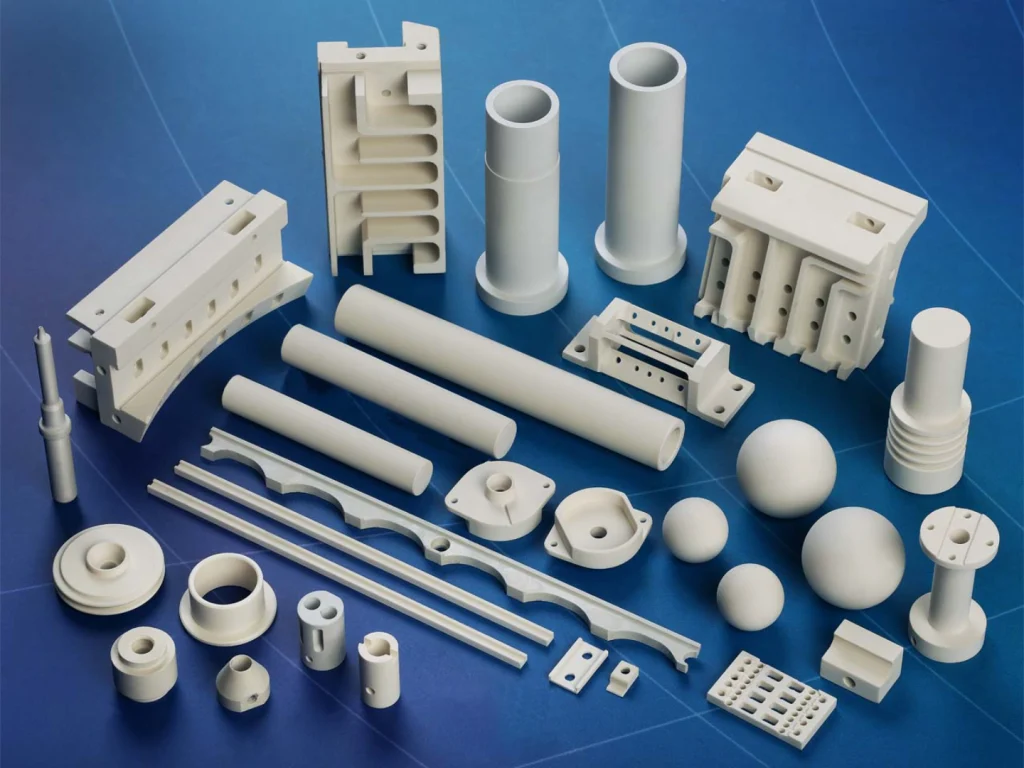
Section 3 Material Properties of Aluminum Nitride Ceramics
Property | Value |
Thermal Conductivity | 170-230 W/m·K |
Electrical Resistivity | >10^13 Ω·cm |
Density | 3.26 g/cm³ |
Flexural Strength | 300-500 MPa |
Dielectric Constant | ~8.5 |
Coefficient of Thermal Expansion (CTE) | 4.0-4.5 x 10⁻⁶/K |
Thermal Shock Resistance | Excellent |
Chemical Resistance | Excellent |
These properties make AlN an ideal choice for demanding applications across various fields.
Section 4 Applications of Aluminum Nitride Ceramics
The unique characteristics of AlN ceramics make them invaluable in numerous applications, including:
4.1 Electronics Packaging: AlN’s exceptional thermal conductivity helps dissipate heat generated by electronic components such as high power semiconductors, integrated circuits, and processors, making them ideal for substrates, heat sinks, and dielectrics.
4.2 LED Lighting: AlN is increasingly used as a substrate material in LED lighting applications due to its ability to efficiently remove heat, improving LED performance and extending lifespan.
4.3 Power Electronics: In high-power electronics, AlN serves as a crucial component for managing the high temperatures generated by power transistors and modules. It enables the development of more efficient and reliable power converters.
4.4 High-Frequency Electronics: AlN offers stable dielectric properties at high frequencies and can improve signal integrity in microwave and RF devices.
4.5 Semiconductor Processing Equipment: AlN components are used in equipment for semiconductor processing, thanks to their chemical inertness, high temperature resistance, and excellent thermal properties.
4.6 Medical Applications: Due to its biocompatibility, AlN finds use in medical implants and sensors.
4.7 Aerospace and Automotive: AlN is employed for its heat and wear resistance and is found in components such as igniters and thermal management parts for advanced vehicle electronics.
Section 5 Table of Key Aspects
Aspect | Details |
Type | Advanced technical ceramic |
Processing technology | Powder preparation, powder forming, sintering, machining, finishing, quality control |
Powder forming | Dry pressing, Cold Isostatic Pressing (CIP), Tape Casting, Extrusion, Injection Molding |
Sintering | Pressureless Sintering, Hot Pressing (HP), Hot Isostatic Pressing (HIP), Spark Plasma Sintering (SPS) |
Material properties | High thermal conductivity, excellent electrical insulation, good mechanical strength, chemical inertness, high temperature resistance, thermal shock resistance |
Quality detection methods | Powder characterization, density measurement, dimensional checks, non-destructive testing, property testing |
Application field | Electronics packaging, LED lighting, power electronics, high-frequency electronics, semiconductor processing, medical, aerospace, automotive |
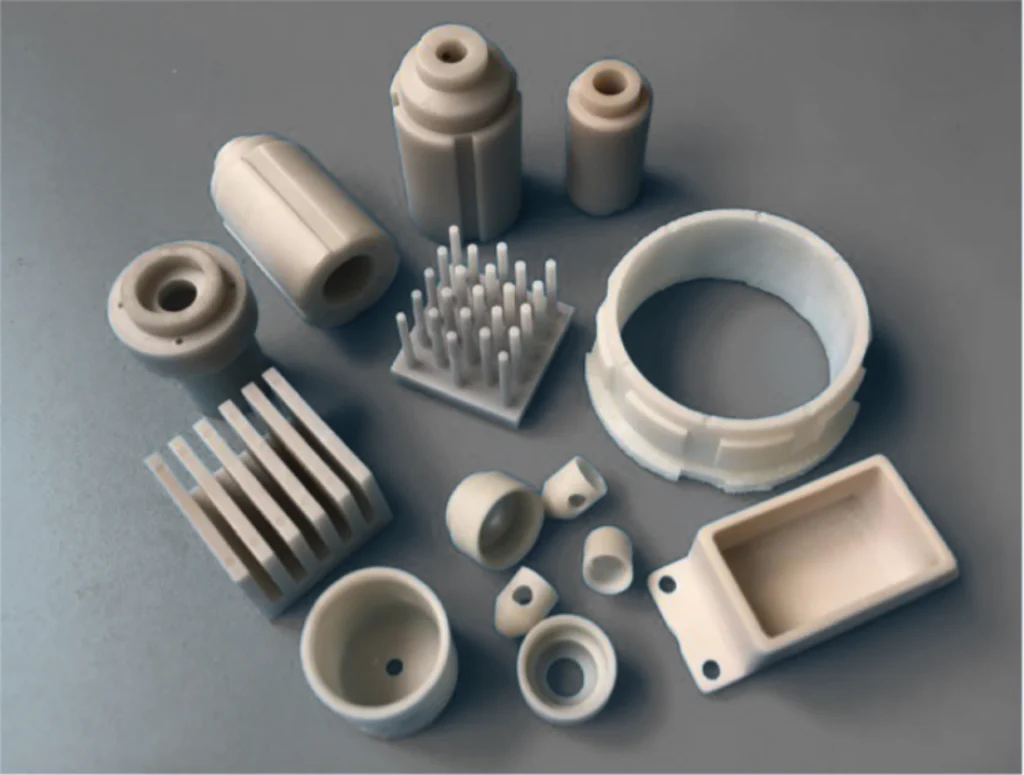
Section 6 The Importance of Partnering with an Experienced AlN Ceramic Supplier
The successful implementation of AlN ceramics requires partnering with a supplier who not only provides high-quality materials but also possesses deep expertise in processing techniques. Here’s why the right supplier matters:
6.1 Material Quality: AlN purity, particle size, and consistency are critical for achieving optimal performance. A trusted supplier ensures stringent quality control.
6.2 Process Expertise: Advanced processing techniques and the right equipment are necessary for producing high-density, defect-free AlN parts with desired specifications.
6.3 Custom Solutions: A good supplier can provide custom design and manufacturing solutions tailored to specific application needs.
6.4 Scalability: Whether you need a small batch for prototyping or high-volume production, a reputable supplier can scale their operations to meet your needs.
6.5 Reliability and Consistency: Consistent material properties and dimensional accuracy are crucial for reliable device performance.
Section 7 Why Choose Welleshaft as your Aluminum Nitride Supplier and Manufacturer?
For companies seeking a reliable global partner for Aluminum Nitride ceramic processing, Welleshaft stands out as a premier supplier and contract manufacturer. They possess extensive experience and expertise in the field of AlN ceramics, and are well known for:
7.1 High-Quality Materials: Welleshaft sources only the highest purity AlN powder and materials, ensuring superior product performance and reliability.
7.2 Advanced Processing Technology: They utilize cutting-edge techniques in powder preparation, forming, sintering, and finishing to manufacture parts with exceptional precision and consistency.
7.3 Custom Solutions: Welleshaft offers tailored AlN ceramic solutions designed to meet the unique requirements of their customers, ensuring optimal performance and fit.
7.4 Stringent Quality Control: They employ rigorous quality control measures throughout the manufacturing process, ensuring that every part meets stringent performance standards.
7.5 Global Reach: With a global manufacturing and distribution network, Welleshaft can provide high-quality AlN components to clients worldwide.
7.6 Reliable Contract Manufacturing: For OEMs looking for a trusted partner to produce their AlN parts, Welleshaft provides contract manufacturing service that meets the highest standards of quality, consistency and reliability.
Conclusion
Aluminum Nitride ceramic processing is a complex field that yields a remarkably versatile material suitable for a wide range of demanding applications, especially in electronics and thermal management. Its unique combination of high thermal conductivity, exceptional electrical insulation, and mechanical strength makes it a vital material for many industries. As a globally trusted supplier and contract manufacturer, Welleshaft offers quality and innovative Aluminum Nitride ceramic solutions. Whether it’s a small-scale or large-scale project, or unique AlN part, the expertise at Welleshaft can benefit you from the initial material design, to prototype, and the final product development. By choosing the right partners and processes, companies can harness the full potential of Aluminum Nitride and meet the increasing demand for high performance parts in electronic applications.