Precision Aluminum Investment Casting | High-Quality, Durable Solutions for Complex Components
Introduction
Aluminum investment casting, also known as aluminum precision casting, is essential in manufacturing intricate parts with tight tolerances and smooth surface finishes. By utilizing a mold made from a wax pattern coated in ceramic, this method is ideal for creating components in a variety of industries, from automotive to aerospace.
What is Aluminum Investment Casting?
Aluminum investment casting, often called lost wax casting, is a process that involves creating a ceramic mold from a wax model of the desired part. This mold is then filled with molten aluminum alloy, resulting in a highly detailed, precise part once cooled and solidified. This process is particularly advantageous for complex geometries, thin walls, and other challenging design requirements.
The Aluminum Investment Casting Process
The aluminum investment casting process consists of several crucial steps to ensure high quality and precision:
Step 1: Creating the Wax Pattern
The process begins with a wax model, which is an exact replica of the final part. This wax pattern is produced by injecting molten wax into a metal die. Once solidified, the wax model is carefully removed from the die, and multiple patterns can be assembled onto a single sprue to increase efficiency.
Step 2: Building the Ceramic Shell
After the wax pattern is created, it is coated with a ceramic slurry. This process, known as “investment,” involves multiple layers of ceramic until a durable shell is formed around the wax pattern. Once the ceramic shell reaches the desired thickness, it is left to dry and harden, creating a sturdy mold.
Step 3: Removing the Wax and Casting the Aluminum
The ceramic shell is heated to remove the wax, leaving a hollow cavity that exactly mirrors the final part. This step is where the process gets its “lost wax” name. Once the wax is melted out, molten aluminum is poured into the ceramic mold, filling the cavity. The aluminum is allowed to cool and solidify, taking the shape of the mold.
Step 4: Finishing and Quality Control
Once the aluminum has solidified, the ceramic shell is broken away to reveal the casting. The cast part undergoes various finishing processes, such as sandblasting, machining, and heat treatment, to enhance its properties and meet specifications. Finally, thorough quality control measures are conducted to ensure that each component meets industry standards.
Advantages of Aluminum Investment Casting
Aluminum investment casting offers several benefits, making it the preferred choice for many industries:
- High Precision and Complexity: This casting method is ideal for creating intricate designs with complex geometries and tight tolerances.
- Smooth Surface Finish: The ceramic mold results in a smooth surface finish, reducing the need for extensive post-processing.
- Reduced Material Waste: Investment casting is efficient in material usage, as most aluminum alloys are recyclable and can be reused in subsequent batches.
- Versatility of Aluminum Alloys: Various aluminum alloys, such as A356, 319, and 6061, can be used, each offering unique benefits, including high strength-to-weight ratios and corrosion resistance.
- Lower Production Costs: Despite its detailed process, investment casting can be cost-effective due to reduced machining needs and the ability to produce large batches.
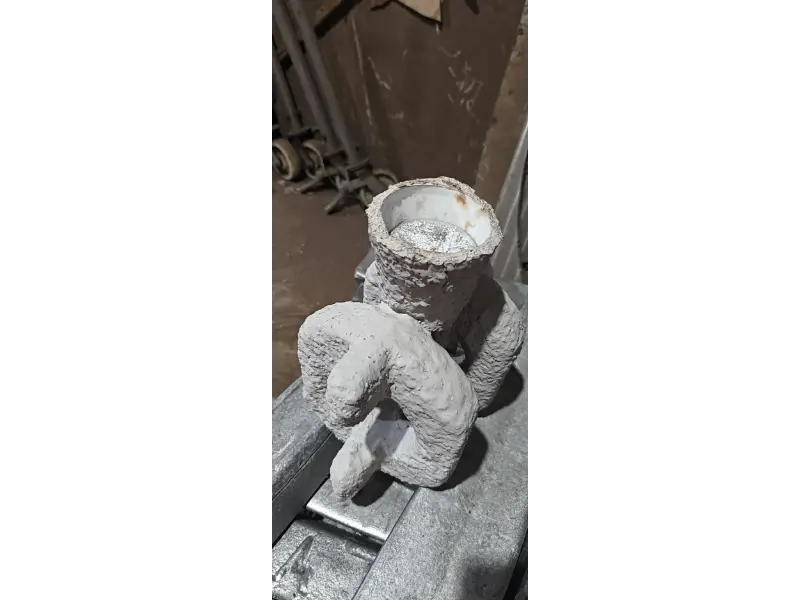
Applications of Aluminum Investment Casting
Aluminum investment casting is a precision casting process widely used in various industries for producing complex and detailed aluminum components. The process provides high dimensional accuracy, excellent surface finish, and allows for intricate designs that would be challenging or costly to achieve with other methods. Here are some of the primary applications of aluminum investment casting across different industries:
1. Aerospace Industry
- Components: Aircraft parts, engine components, brackets, and housings.
- Benefits: Lightweight yet durable aluminum parts are essential in aerospace for improving fuel efficiency and reducing overall weight without compromising strength.
2. Automotive Industry
- Components: Engine blocks, cylinder heads, transmission cases, turbocharger components, and other critical engine parts.
- Benefits: Investment casting allows for high-precision, lightweight components that can withstand high temperatures and pressures, essential for performance and efficiency in modern vehicles.
3. Medical Industry
- Components: Medical devices, surgical instruments, and equipment housing.
- Benefits: The precision of aluminum investment casting meets the strict requirements for medical-grade parts, offering excellent surface finish and reliability.
4. Defense and Military
- Components: Weapon systems, missile guidance systems, firearm components, and drone parts.
- Benefits: Investment-cast aluminum parts offer the necessary strength-to-weight ratio required in defense applications, ensuring durability in harsh environments and allowing for complex, high-performance designs.
5. Marine Industry
- Components: Propellers, pump housings, impellers, and valve bodies.
- Benefits: Aluminum resists corrosion, which is vital in marine applications where components are exposed to water and other harsh environments.
6. Electronics and Telecommunications
- Components: Heat sinks, housings for electronic devices, communication infrastructure parts.
- Benefits: Aluminum’s heat dissipation properties make it ideal for electronics, while the investment casting process allows for creating lightweight, complex shapes essential in telecommunications.
7. Industrial and Heavy Equipment
- Components: Gearboxes, pump bodies, valve components, and machinery housings.
- Benefits: The precision of aluminum investment casting allows for durable, complex components that meet the demands of heavy-duty industrial applications.
8. Consumer Products
- Components: Sporting equipment, recreational vehicle parts, furniture fittings, and appliance components.
- Benefits: The ability to produce finely detailed, lightweight, and corrosion-resistant parts makes aluminum investment casting an excellent choice for various consumer products.
9. Energy Sector
- Components: Parts for wind turbines, solar panel mounts, and other renewable energy infrastructure.
- Benefits: Aluminum components contribute to lighter, more efficient energy solutions, essential for renewable energy systems.
10. Architectural and Artistic Applications
- Components: Decorative metalwork, architectural fittings, sculptures, and bespoke fixtures.
- Benefits: Investment casting’s flexibility with design allows for aesthetically pleasing and complex structures often required in architectural and artistic applications.
Each of these applications benefits from the aluminum investment casting process, offering advantages in weight reduction, durability, and the ability to create complex geometries.
Why Choose Welleshaft for Aluminum Investment Casting
When it comes to choosing a reliable supplier for aluminum investment casting, Welleshaft stands out for several reasons:
- Global Reputation: Welleshaft is known worldwide as a trusted supplier of custom aluminum alloy investment casting solutions. They serve diverse industries and have a track record of delivering high-quality, precision-cast components.
- Advanced Manufacturing Facilities: With state-of-the-art production facilities, Welleshaft ensures that each casting meets stringent quality standards. Their commitment to innovation and precision sets them apart in the investment casting industry.
- Custom Solutions: Welleshaft understands that each client has unique needs. They offer custom solutions tailored to specific applications, working closely with customers to develop the ideal product for their project requirements.
- Experienced Team of Engineers: With a skilled team of engineers, Welleshaft provides technical expertise in designing and manufacturing high-precision aluminum investment castings, ensuring that each product meets industry standards and client expectations.
- Focus on Quality and Consistency: Welleshaft’s rigorous quality control processes guarantee consistent and reliable components, making them a preferred choice for clients who demand excellence.
Conclusion
Aluminum investment casting is a highly versatile and efficient manufacturing process that allows for the production of intricate, durable components. With applications spanning industries like aerospace, automotive, medical, and electronics, it’s no wonder that this method is favored worldwide.
For businesses seeking a trusted partner in aluminum investment casting, Welleshaft offers unparalleled expertise, quality, and customer service. As a globally recognized supplier, Welleshaft’s commitment to precision, innovation, and client satisfaction makes them an ideal choice for your investment casting needs.