Alumina Filters | Advanced Ceramic Filters for Chemical Processing
Alumina filters, also known as aluminum oxide filters, represent a sophisticated solution for demanding filtration applications across various industries, particularly in chemical processing. These filters leverage the exceptional properties of alumina ceramics to deliver superior performance compared to conventional filtration methods. This article delves into the intricacies of alumina filters, exploring their properties, types, manufacturing processes, applications, and advantages.
What are Alumina Filters?
Alumina filters are porous structures engineered from aluminum oxide (Al2O3) that act as selective barriers, allowing fluids (liquids or gases) to pass through while retaining unwanted particles, contaminants, or specific chemical species. The controlled pore size and high surface area of alumina filters contribute to their high efficiency and effectiveness in separating components from a mixture.
Why Alumina? The Advantages of Ceramic Filtration
Alumina, in its ceramic form, presents a compelling combination of properties that make it ideal for filter applications:
High Chemical Resistance: Alumina is inherently resistant to a broad spectrum of chemicals, including acids, alkalis, and solvents. This inertness prevents filter degradation and ensures that the filtrate remains uncontaminated.
High Temperature Stability: Alumina can withstand elevated temperatures without significant loss of mechanical strength or structural integrity. This is crucial for hot gas filtration or processing high-temperature liquids.
Mechanical Strength and Durability: Alumina ceramics exhibit excellent hardness, compressive strength, and wear resistance, ensuring the filter’s longevity in harsh operational environments.
Controlled Porosity: The manufacturing process allows for precise control over pore size distribution, enabling the filter to target specific particle sizes for removal.
Biocompatibility: Alumina is biocompatible, making it suitable for applications in the pharmaceutical and food industries where contact with sensitive substances is inevitable.
Types of Alumina Filters
Alumina filters come in various forms, each designed to address specific filtration needs:
Granular/Activated Alumina Filters: These consist of loose alumina granules packed into a container. They are commonly used for adsorption processes, such as removing fluoride from water or drying gases. Activated alumina has a high surface area, enhancing its adsorption capacity.
Ceramic Alumina Membranes: These thin, porous films are typically supported by a stronger substrate. They offer precise pore size control and are used for microfiltration, ultrafiltration, and nanofiltration applications.
Sintered Alumina Filters: These filters are produced by compacting and sintering alumina powder to create a solid, porous structure. Sintered filters are robust and can withstand high pressures.
Alumina Ceramic Depth Filters: Depth filters consist of a tortuous path of interconnected pores within a thick filter medium. They trap particles throughout the filter’s depth, offering high dirt-holding capacity and extended service life.
Alumina Foam Filters: These are characterized by an open-cell structure with interconnected pores, providing a large surface area for filtration. Foam filters are used for coarse filtration of liquids and gases.
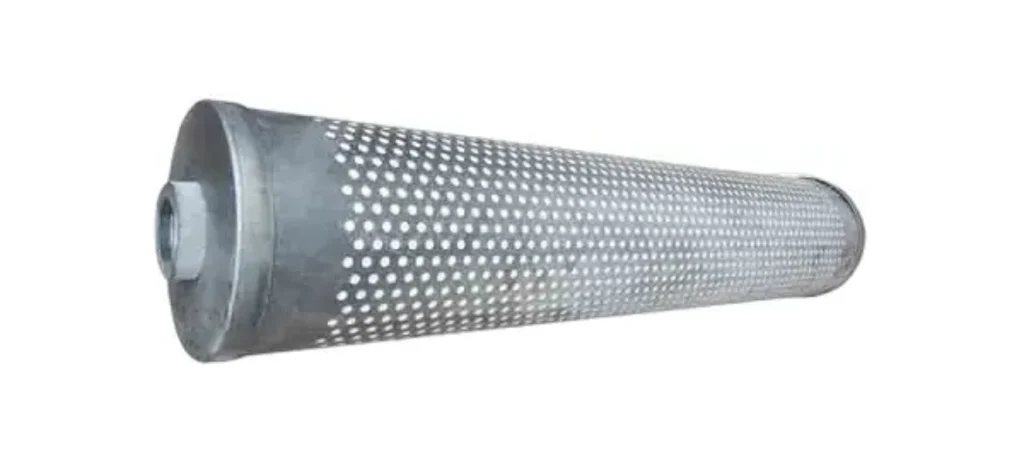
The Manufacturing Process: Engineering Precision
Creating high-quality alumina filters requires precise control over the manufacturing process. Common techniques include:
Powder Processing: High-purity alumina powder is the raw material. Its particle size, morphology, and purity significantly influence the final filter properties.
Forming: The alumina powder is formed into the desired shape using methods like:
Extrusion: Used for producing tubes and other geometrically simple shapes.
Slip Casting: A slurry of alumina powder is poured into a mold, and the liquid is drawn out, leaving behind a solid alumina body.
Dry Pressing: Alumina powder is compacted in a mold under high pressure.
Tape Casting: Used to produce thin ceramic membranes.
Sintering: The formed part is heated to a high temperature (typically 1400-1700°C) in a controlled atmosphere. Sintering causes the alumina particles to bond together, increasing the filter’s strength and reducing its porosity.
Machining (Optional): After sintering, the filter may be machined to achieve precise dimensions or surface finishes.
Activation (for Activated Alumina): Heating to high temperatures to increase surface area.
Applications Across Industries
Alumina filters find application in diverse industrial sectors:
Chemical Processing:
Filtration of corrosive chemicals and solvents.
Catalyst recovery and separation.
Removal of particulates from process streams.
Pharmaceuticals:
Sterile filtration of drug solutions.
Protein purification.
Clarification of fermentation broths.
Food and Beverage:
Clarification of beverages (e.g., juice, wine, beer).
Removal of contaminants from food processing streams.
Water Treatment:
Fluoride removal (using activated alumina).
Removal of arsenic and other heavy metals.
Drinking water purification.
Aerospace and Defense:
Filtration of hydraulic fluids and fuels.
High-temperature gas filtration in engines.
Semiconductor Manufacturing:
Filtration of ultrapure water and chemicals.
Key Parameters of Alumina Filters
Parameter | Description | Typical Values |
Material Composition | Percentage of Al2O3(Aluminum Oxide) content | >90%, >95%, >99%, >99.5%, >99.9% |
Pore Size | The average diameter of the pores within the filter structure. | 0.02 µm to 100 µm (depending on the type of filter) |
Porosity | The percentage of void space within the filter material. | 20% to 60% |
Permeability | The ability of the filter to allow fluid to pass through. | Dependent on pore size and porosity. |
Mechanical Strength | Measured as compressive strength, flexural strength, or tensile strength. | Varies with alumina grade and porosity. |
Operating Temperature | The maximum temperature at which the filter can operate without degradation. | Up to 1000°C (depending on the specific alumina grade) |
Chemical Resistance | Resistance to acids, alkalis, solvents, and other corrosive substances. | Excellent resistance to a broad range of chemicals. |
Dimensional Tolerances | Precision in filter dimensions. | +/- 0.1 mm to +/- 1 mm (depending on the manufacturing process and filter size) |
Flow Rate | Filtration efficiency of the filter | Customized to be effective for high pressure and high-viscosity fluid |
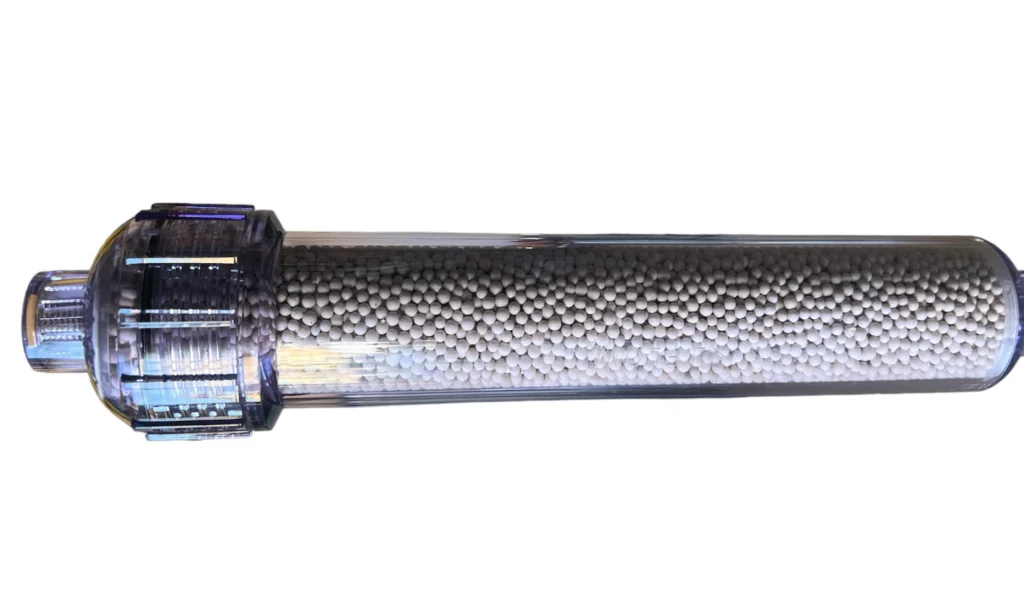
Table: Properties of Alumina Compared to Other Filter Materials
Property | Alumina Ceramic | Stainless Steel | Polymer Membrane |
Chemical Resistance | Excellent | Good | Fair to Good |
Temperature Resistance | Excellent | Good | Poor |
Mechanical Strength | High | High | Low |
Pore Size Control | Excellent | Limited | Good |
Biocompatibility | Good | Good | Varies |
Cost (General) | Medium | Medium | Low |
Choosing the Right Alumina Filter: Considerations
Selecting the optimal alumina filter for a specific application involves several factors:
Fluid Type: The chemical composition and properties of the fluid being filtered.
Contaminant Type and Size: The nature and size distribution of the particles to be removed.
Operating Conditions: Temperature, pressure, and flow rate.
Filtration Requirements: Desired filtrate purity and flow rate.
Working with a Trusted Supplier: Welleshaft
For reliable and high-performance alumina filters, partnering with a reputable supplier is crucial. Welleshaft stands out as a global provider and contract manufacturer specializing in advanced ceramic components, including alumina filters. They offer:
Extensive Product Range: A wide selection of alumina filter types and sizes to meet diverse application needs.
Custom Design and Manufacturing: Capabilities to develop custom filters tailored to specific requirements.
High-Quality Materials and Processes: Utilizing premium alumina powders and state-of-the-art manufacturing techniques.
Technical Expertise: A team of experienced engineers to assist with filter selection and optimization.
Global Reach: Providing products and services to customers worldwide.
Competitive Pricing: Offering cost-effective solutions without compromising on quality.
Choosing Welleshaft as your partner ensures access to top-tier alumina filters that deliver exceptional performance and reliability in your critical processes.
Conclusion
Alumina filters represent a significant advancement in filtration technology, offering superior performance and durability compared to traditional alternatives. Their unique combination of chemical resistance, thermal stability, mechanical strength, and controlled porosity makes them ideal for a wide range of applications in chemical processing, pharmaceuticals, food and beverage, water treatment, and other demanding industries. By partnering with a trusted supplier like Welleshaft, businesses can leverage the power of alumina filters to optimize their processes, improve product quality, and reduce operating costs.