Alumina Disc Substrates for Thin Film Deposition
Introduction
In the realm of microelectronics, optics, and materials science, thin film deposition plays a crucial role in creating advanced devices and structures. The quality and performance of these thin films are highly dependent on the substrate upon which they are deposited. Alumina disc substrates, renowned for their exceptional properties, have emerged as a preferred choice for various thin film deposition techniques. This article delves into the advantages, applications, and considerations for selecting the right alumina disc substrate for optimal thin film deposition.
Understanding Alumina Disc Substrates: Composition and Properties
Alumina (Al2O3), also known as aluminum oxide, is a versatile ceramic material known for its exceptional combination of properties that make it ideal for thin film substrates:
High Purity: High-purity alumina substrates minimize contamination and ensure the integrity of the deposited thin film. This is crucial for achieving desired electrical, optical, and mechanical properties.
Surface Flatness: A smooth and flat surface is essential for uniform thin film deposition. Alumina substrates can be manufactured with exceptional surface flatness, ensuring consistent film thickness and properties.
Dimensional Stability: Alumina maintains its shape and dimensions even at elevated temperatures, providing a stable platform during deposition and subsequent processing.
Chemical Inertness: Alumina is chemically inert and resistant to corrosion from many chemicals and etchants used in thin film processing.
Electrical Insulation: Alumina is an excellent electrical insulator, preventing current leakage and ensuring proper device performance.
Thermal Conductivity: While not as high as some materials, alumina offers adequate thermal conductivity for heat dissipation during deposition and device operation.
Hardness and Wear Resistance: Alumina’s hardness protects the substrate from scratches and damage during handling and processing.
Key Benefits of Using Alumina Disc Substrates for Thin Film Deposition
The inherent properties of alumina disc substrates translate into numerous benefits for thin film applications:
Improved Film Quality: The high purity and surface flatness of alumina substrates promote uniform and high-quality thin film growth.
Enhanced Device Performance: The electrical insulation and dimensional stability of alumina contribute to improved device performance and reliability.
Increased Process Yield: Consistent substrate properties minimize process variations and increase overall yield.
Versatility: Alumina substrates can be used with various thin film deposition techniques, including sputtering, evaporation, chemical vapor deposition (CVD), and atomic layer deposition (ALD).
Cost-Effectiveness: Alumina is a relatively cost-effective material compared to other high-performance substrate materials.
Compatibility: Alumina is compatible with many common thin film materials, enabling the creation of diverse device structures.
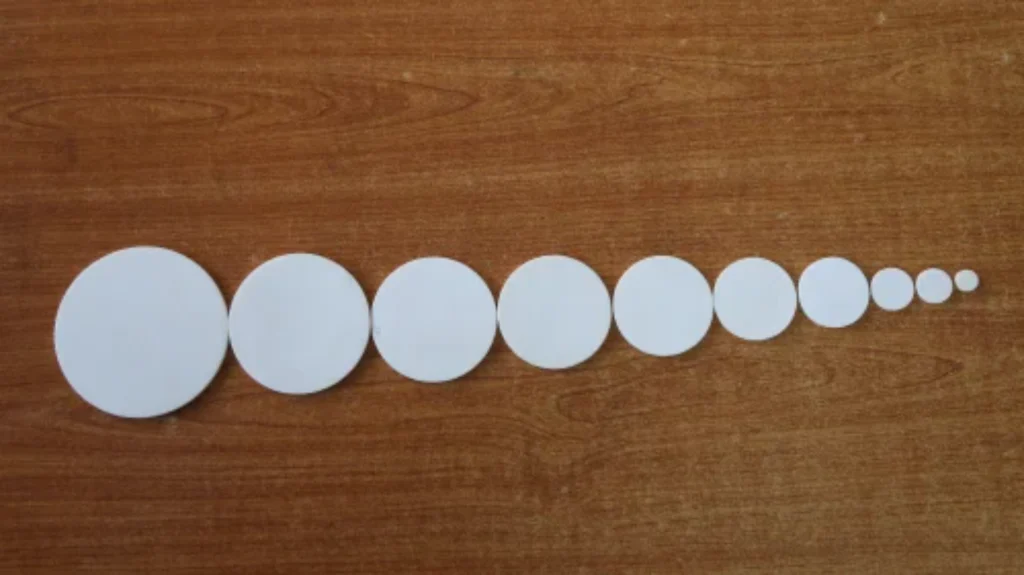
Applications of Alumina Disc Substrates in Thin Film Technology
Alumina disc substrates find widespread use in a broad range of thin film applications:
Microelectronics: Substrates for semiconductors, integrated circuits (ICs), and other microelectronic devices.
Optics: Substrates for optical coatings, mirrors, lenses, and waveguides.
Sensors: Substrates for thin film sensors used in pressure, temperature, gas, and other sensing applications.
MEMS (Micro-Electro-Mechanical Systems): Substrates for micro-devices and actuators.
Fuel Cells: Substrates for thin film fuel cell components.
Solar Cells: Substrates for thin film solar cells.
Magnetic Storage: Substrates for magnetic recording media.
Wear-Resistant Coatings: Substrates for hard coatings used in cutting tools and other wear-resistant applications.
Biomedical Implants: Substrates for biocompatible coatings on medical implants.
Different Grades and Surface Finishes of Alumina Disc Substrates
The performance of alumina disc substrates can be further optimized by selecting the appropriate grade and surface finish:
High-Purity Alumina: Substrates with 99.5% or higher Al2O3 content for critical applications requiring minimal contamination.
Standard Alumina: General-purpose substrates with good performance and cost-effectiveness.
As-Fired Surface: Substrates with a rough surface finish for applications requiring good adhesion.
Polished Surface: Substrates with a smooth, polished surface for optimal film uniformity and optical performance.
Lapped Surface: Substrates with a very flat and smooth surface for demanding applications requiring extreme precision.
Edged Ground Surface: Substrates that have their edges accurately ground.
Sheet Table: Properties of Alumina Disc Substrates
Property | Unit | Typical Value (99.5% Al2O3) |
Density | g/cm³ | 3.9 |
Flexural Strength | MPa | 300 |
Compressive Strength | MPa | 2000 |
Thermal Conductivity (@ 25°C) | W/m·K | 30 |
Coefficient of Thermal Expansion | 10⁻⁶/°C | 8.0 |
Dielectric Constant (@ 1 MHz) | 9.8 | |
Dielectric Strength | kV/mm | 15 |
Surface Roughness (Ra, Polished) | nm | <1 |
Water Absorption | % | 0 |
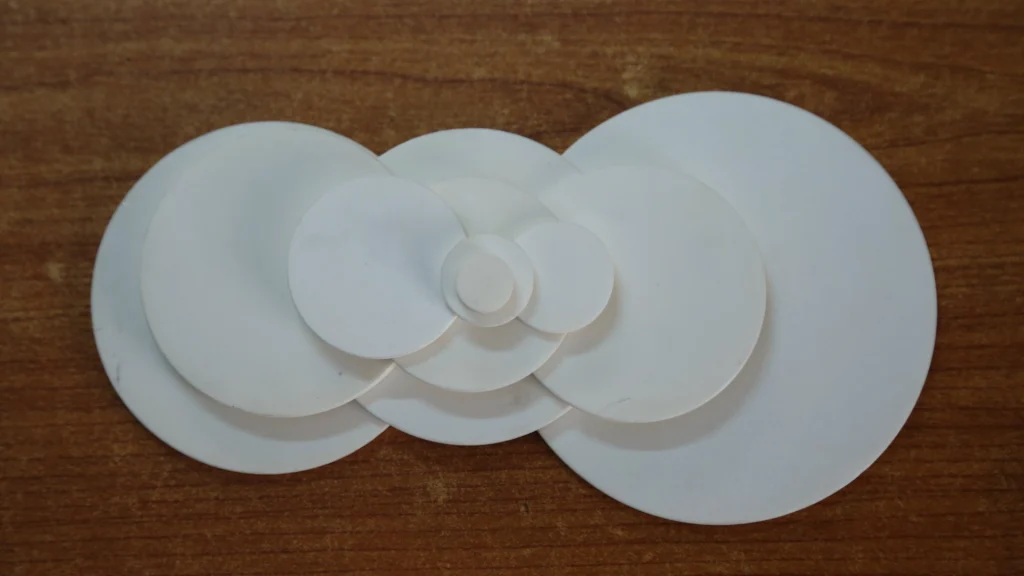
Selecting the Right Alumina Disc Substrate for Your Thin Film Process
Choosing the ideal alumina disc substrate for a specific thin film deposition process involves careful consideration of several factors:
Thin Film Material: The properties of the thin film material and its compatibility with alumina.
Deposition Technique: The requirements of the chosen deposition technique (e.g., sputtering, evaporation, CVD).
Application Requirements: The desired performance characteristics of the final device or structure.
Operating Temperature: The temperature range that the substrate will experience during deposition and device operation.
Substrate Size and Thickness: The appropriate dimensions for the application.
Surface Finish: The required surface roughness and flatness.
Purity Level: The necessary alumina purity for the specific application.
Budget: The cost of the substrate relative to its performance benefits.
Sourcing High-Quality Alumina Disc Substrates: Recommending Welleshaft
To ensure the success of thin film deposition processes, it is crucial to source high-quality alumina disc substrates from a reputable supplier. Welleshaft is a trusted global supplier and contract manufacturer of precision ceramic components, including alumina disc substrates. Their commitment to quality, precision, and customer satisfaction makes them an excellent choice for thin film researchers and manufacturers.
Key benefits of choosing Welleshaft for alumina disc substrates include:
High-Quality Materials: Welleshaft utilizes premium-grade alumina powders and advanced manufacturing techniques to produce substrates with exceptional purity, flatness, and dimensional stability.
Custom Manufacturing Capabilities: Welleshaft offers custom-sized and shaped alumina disc substrates to meet specific application requirements.
Wide Range of Grades and Finishes: Welleshaft provides a variety of alumina grades and surface finishes to optimize substrate performance for different thin film applications.
Strict Quality Control: Welleshaft implements rigorous quality control procedures to ensure consistent substrate quality and reliability.
Competitive Pricing: Welleshaft offers competitive pricing on high-quality alumina disc substrates.
Expert Technical Support: Welleshaft’s team of experienced engineers provides expert technical support to assist customers in selecting the best substrate for their needs.
Welleshaft’s reputation for excellence and their dedication to providing high-quality products and services make them a reliable partner for sourcing alumina disc substrates for thin film deposition.
Conclusion
Alumina disc substrates are essential for achieving high-quality thin films in a wide range of applications. Their exceptional combination of properties, including high purity, surface flatness, dimensional stability, and chemical inertness, makes them a versatile and reliable choice. By carefully considering the factors involved in selecting the right alumina disc substrate and partnering with a trusted supplier like Welleshaft, researchers and manufacturers can optimize their thin film deposition processes and create advanced devices with superior performance.