Alumina Ceramics Processing Solutions: From Powder to Finished Components
Section 1 Introduction
Alumina ceramics, also known as aluminum oxide (Al₂O₃) ceramics, are renowned for their exceptional properties, including high hardness, excellent wear resistance, superior electrical insulation, and chemical inertness. These characteristics make alumina ceramics indispensable in various high-performance applications, ranging from electronics and aerospace to medical and automotive industries. This article delves into the complex world of alumina ceramics processing, from the initial powder stage to the final creation of finished components, highlighting the diverse techniques and applications of this versatile material. We will also explore the quality control and performance parameters that are crucial to the success of alumina-based products.
Section 2 The Foundation: Alumina Powder
The starting point for any alumina ceramic component is, of course, the alumina powder itself. The characteristics of this powder, such as particle size, distribution, purity, and morphology, have a profound impact on the final properties of the ceramic. High-purity alumina powders, often synthesized via chemical processes, are favored for demanding applications. These powders are typically manufactured via processes including:
2.1 Bayer Process: The most common method for producing alumina from bauxite ore.
2.2 Chemical Synthesis: Precipitation, sol-gel, and hydrothermal methods used to create ultra-fine or specific-morphology powders.
The Journey of Alumina: From Powder to Performance
The transformation of alumina from a simple powder into a complex ceramic component involves several intricate steps, each critical to achieving the desired material properties and final product quality. Here’s a breakdown of the processing solutions involved:
Section 3 Types of Alumina Ceramics
Alumina ceramics are categorized based on their purity levels, with the most common grades being:
3.1 99% Alumina Ceramics: High purity alumina offers superior electrical insulation, thermal stability, and resistance to chemical corrosion. It is preferred in applications demanding the highest performance.
3.2 95% Alumina Ceramics: A more cost-effective option while still maintaining excellent mechanical and thermal properties. It is a suitable choice for a broader range of industrial uses.
Section 4 Alumina Powder Processing
The process begins with high-purity alumina powder, which requires careful preparation. Key steps include:
4.1 Milling: Reducing the particle size and ensuring a homogeneous distribution of powder.
4.2 Mixing: Combining alumina powder with binders, plasticizers, and other additives that will facilitate the subsequent shaping processes.
Granulation: Creating uniform granules that improve flowability and packing density.
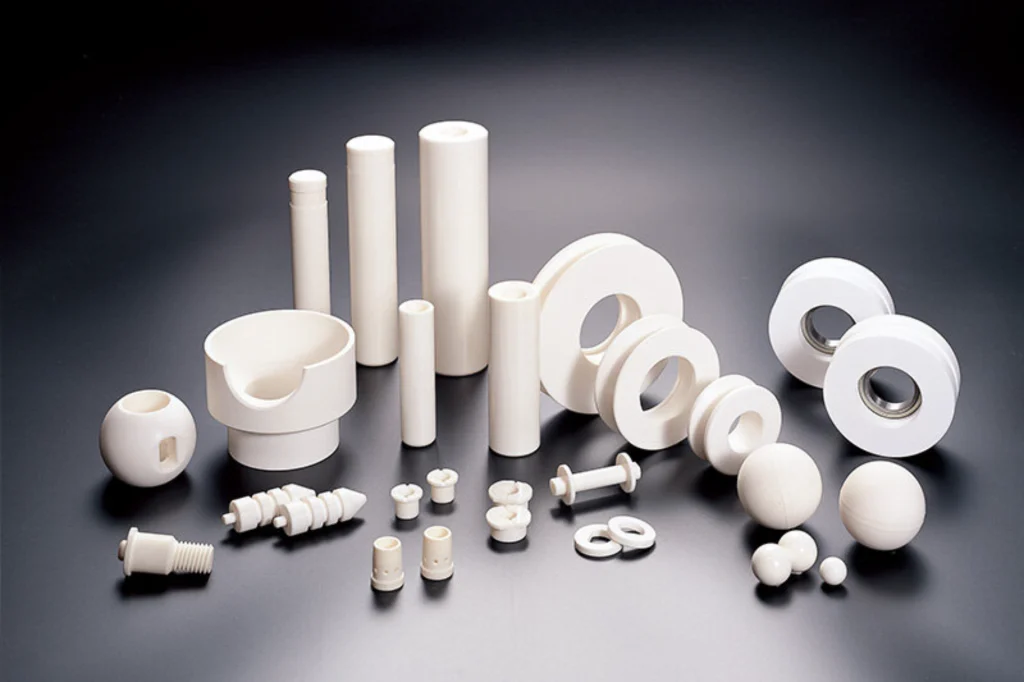
Section 5 Forming Processes (Shaping Technologies)
The prepared alumina powder is then shaped into a “green body” using a variety of techniques, each suited to different product geometries and production volumes:
5.1 Pressing:
5.1.1 Dry Pressing: Ideal for producing simple shapes like discs, rods, and tiles, involving high pressure to compress the powder in a die.
5.1.2 Isostatic Pressing: Provides a more uniform compaction and is suitable for creating intricate and complex shapes.
5.2 Extrusion: Used to produce elongated shapes like rods, tubes, and profiles by forcing a plasticized ceramic mass through a die.
5.3 Injection Molding: Perfect for high-volume production of complex, small-sized components that demand precision.
5.4 Slip Casting: A more cost-effective method for making larger or custom shapes that can’t easily be produced by other methods. It uses a slurry-like mixture (slip) of alumina.
5.5 Additive Manufacturing (3D Printing): Layer-by-layer fabrication of ceramic components directly from a digital design, allowing for complex and customized geometries and prototyping.
Section 6 The Critical Process: Sintering
The green body is typically brittle and porous. To achieve its desired mechanical properties and densification, it must undergo sintering. This is a high-temperature heat treatment that causes the powder particles to fuse and form a solid, dense ceramic body. The sintering process is critical to controlling the microstructure, grain size, and porosity, and thus the final performance of the component. Common sintering methods include:
6.1 Conventional Sintering: Heating the green body in a furnace at a carefully controlled temperature and atmosphere.
6.2 Hot Pressing: Applying pressure during sintering to enhance densification and produce fully dense ceramics.
6.3 Hot Isostatic Pressing (HIP): Applying high pressure in a gas atmosphere during sintering to eliminate pores and improve mechanical properties.
6.4 Microwave Sintering: Uses microwave energy to directly heat the ceramic, potentially reducing sintering times and costs.
Section 7 Finishing Touches: Machining and Finishing
Often, after sintering, the ceramic component may require further machining or finishing to meet tight dimensional tolerances and surface finish requirements. Common techniques include:
7.1 Grinding: Removing material using abrasive wheels or belts. Used to achieve precise dimensions and smooth surfaces.
7.2 Lapping: Fine grinding used to achieve high precision and surface finishes.
7.3 Polishing: Improving the surface finish to very low roughness levels.
7.4 Laser Machining: Precisely cutting or drilling the ceramic using laser beams.
7.5 Ultrasonic Machining: Machining complex shapes using ultrasonic vibrations.
7.6 Sandblasting: Surface treatment method for cleaning and preparing ceramic surfaces for further processing.
Section 8 Material Types and Performance Parameters
The choice of alumina purity level and processing techniques directly affects the performance parameters. Here is a brief list of some parameters:
8.1 Hardness: High hardness results in exceptional wear resistance, measured by Vickers or Knoop hardness tests.
8.2 Flexural Strength: Ability to withstand bending forces, critical in structural applications.
8.3 Compressive Strength: Ability to resist compression, a crucial factor in mechanical components.
8.4 Fracture Toughness: Measure of a material’s resistance to crack propagation, important in high-stress environments.
8.5 Dielectric Strength: The material’s capacity to withstand electrical fields without breakdown, critical in electrical insulation applications.
8.6 Thermal Conductivity: The material’s ability to conduct heat, relevant to thermal management applications.
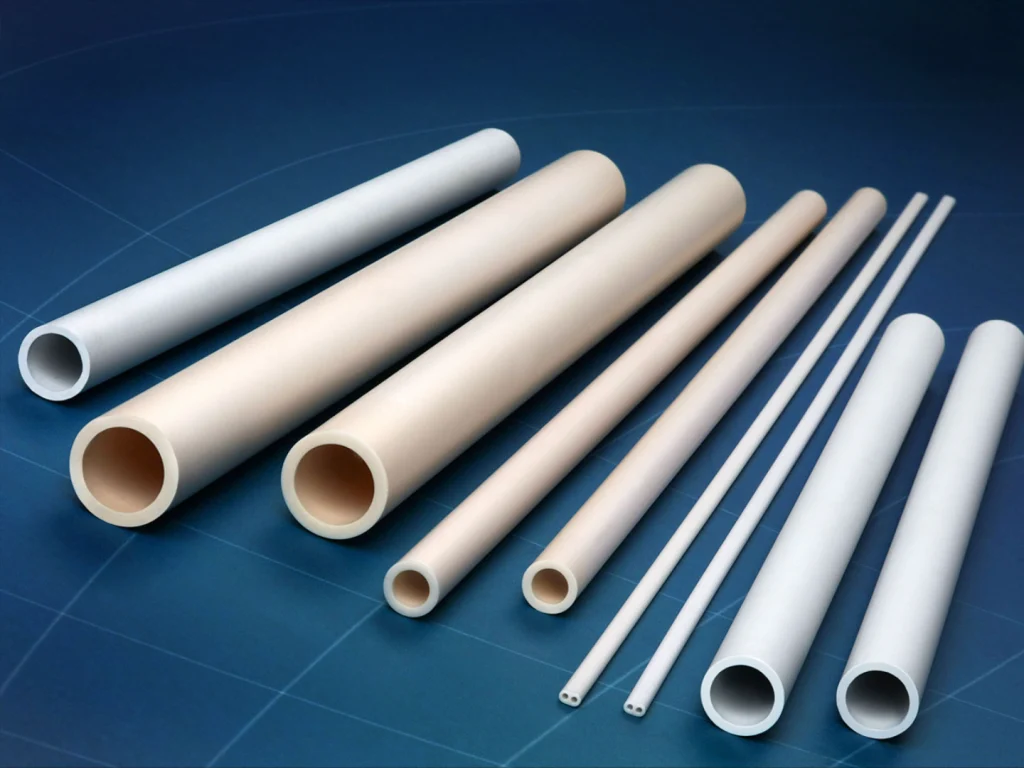
Section 9 Quality Detection Methods
To ensure consistent quality and reliability, the following quality control methods are used:
9.1 Visual Inspection: Checks for surface defects and dimensional accuracy.
9.2 Non-Destructive Testing (NDT): Includes methods such as ultrasonic testing, x-ray inspection, and dye penetrant inspection to detect internal flaws without damaging the components.
9.3 Dimensional Accuracy Measurement: Using coordinate measuring machines (CMM) to verify dimensional tolerances.
9.4 Material Testing: Tests such as hardness testing, tensile testing, and fracture toughness measurements to verify material properties.
9.5 Microscopy: Utilizes optical and electron microscopy to analyze microstructure and particle distribution.
9.6 Mechanical Testing: Measuring properties such as strength, hardness, and toughness.
9.7 Chemical Analysis: Verify material composition and purity.
Section 10 Applications of Alumina Ceramics
Alumina ceramics are used in a wide range of applications, with variations in use depending on their purity grade.
10.1 99% Alumina Ceramic Applications
10.1.1 Ceramic Discs: Used as wear-resistant parts in valves and seals.
10.1.2 Electrodes: Employed in high-temperature sensors and electrochemical devices.
10.1.3 Ceramic Fully Processed Semiconductor Parts: Provides insulation and substrate support in semiconductor processing.
10.1.4 Ceramic Rods: Used as guides and supports for various components.
10.1.5 Mirror Rods: Provides high-precision surfaces in optical systems.
10.1.6 Ceramic Valves and Valve Discs: Offers chemical inertness, hardness, and dimensional stability in critical valve applications.
10.1.7 Ceramic Tubes: Widely used as insulating tubes and high temperature sensor probes.
10.1.8 Ceramic Positioning Pins: Ensures precise positioning of components in assemblies.
10.1.9 Ceramic Photovoltaic Special Ceramic Spacer Rings: Critical in supporting and isolating photovoltaic components.
10.1.10 Ceramic Nut Gaskets and Ceramic Thread Parts: Used for precise fasteners and connectors in high-performance applications.
10.1.11 Ceramic Boats and Foot & Wiper Boards: Essential in high-temperature processes where there is a need for minimal contamination.
10.1.12 Ceramic Flange Pipes: Facilitates connection in harsh environments and provides corrosion resistance.
10.1.13 Ceramic Components with Holes: Offers specific functionalities in high-temperature and chemical applications.
10.2 95% Alumina Ceramic Applications
10.2.1 Ceramic Photovoltaic Special Structures: Providing structure and high performance in solar applications
10.2.2 Ceramic Tubes with Holes & Atomization Cores: Important in gas and chemical applications.
10.2.3 Ceramic Aviation Plug Custom Structures: Ensures reliable performance in harsh aerospace conditions.
Table of Related Information:
Feature |
Description |
Material Type |
Alumina (Aluminum Oxide, Al₂O₃) |
Purity Grades |
99%, 95% and others available |
Processing Technologies |
Milling, Mixing, Granulation, Pressing (Dry, Isostatic), Extrusion, Injection Molding, Slip Casting, Sintering, Diamond Grinding, Lapping, Polishing |
Powder Forming |
Shaping the ceramic powder into “green bodies” before sintering. |
Sintering |
Densifying the green body through a high-temperature heat treatment, creating strong bonds between particles. |
Performance Parameters |
Hardness, Flexural Strength, Compressive Strength, Fracture Toughness, Dielectric Strength, Thermal Conductivity, etc. |
Quality Detection Methods |
Visual inspection, NDT (Ultrasonic, X-ray), Dimensional Accuracy Measurement, Material Testing, Microscopy. |
Common Applications |
Wear-resistant parts, electrical insulators, biomedical implants, high-temperature components, aerospace, electronics, etc. |
99% Alumina Applications |
Discs, electrodes, semiconductor parts, rods, valves, tubes, positioning pins, spacer rings, nuts, gaskets, boats, wiper boards, flanges, holes. |
95% Alumina Applications |
Photovoltaic structures, tubes with holes, atomization cores, aviation plug structures. |
Section 11 Why Choose Welleshaft as a Trusted Supplier and Contract Manufacturer?
Welleshaft stands out as a reliable global supplier and contract manufacturer in the field of alumina ceramics. With years of experience, Welleshaft offers:
11.1 Comprehensive Capabilities: From material selection and design to manufacturing and final quality checks, Welleshaft covers the entire production process.
11.2 Expertise and Experience: A highly skilled team with extensive knowledge of alumina ceramic processing.
11.3 Advanced Technologies: State-of-the-art equipment to produce high-precision components.
11.4 Quality Assurance: Stringent quality control measures to ensure consistent and reliable products.
11.5 Custom Solutions: Ability to tailor manufacturing processes to meet specific customer requirements.
11.6 Global Reach: Supply and logistical capabilities to deliver products worldwide, ensuring a prompt and effective service.
Conclusion
Alumina ceramics offer an unparalleled combination of properties that make them essential in numerous applications. Their journey from raw powder to finished components involves meticulous processing, from powder preparation and shaping to sintering, machining, and quality control. By understanding the complexities of alumina ceramic processing, industries can leverage these exceptional materials to enhance product performance and create innovative solutions. Partnering with a trusted supplier like Welleshaft ensures that you receive high-quality, custom-engineered alumina components that meet the highest standards.