Alumina Ceramic: High-Purity Al2O3 Components & Custom Shapes
Alumina ceramic, also known as aluminum oxide ceramic (Al2O3), is a widely used technical ceramic material celebrated for its exceptional properties, including high hardness, wear resistance, electrical insulation, and chemical inertness. This article explores the diverse world of alumina ceramic components, focusing on high-purity Al2O3 options and the possibilities of custom shapes tailored to specific applications. As industries demand more specialized solutions, understanding the capabilities of alumina ceramic processing becomes increasingly crucial. Whether you require standard components or complex geometries, alumina ceramic offers a compelling combination of performance and versatility.
What is Alumina Ceramic and Why Choose It?
Alumina ceramic (Al2O3) is a non-metallic inorganic material composed primarily of aluminum oxide. It’s created through a process called sintering, where fine alumina powder is heated to a high temperature, causing the particles to fuse together and form a dense, strong, and durable material. The purity of the alumina powder significantly impacts the ceramic’s properties, with higher purity levels resulting in enhanced performance.
Key advantages of alumina ceramic include:
High Hardness and Wear Resistance: Makes it ideal for applications involving abrasion and erosion.
Excellent Electrical Insulation: Suitable for electrical components and insulators.
Superior Chemical Inertness: Resists corrosion from most acids, alkalis, and solvents.
High-Temperature Stability: Maintains strength and properties at elevated temperatures.
Good Compressive Strength: Can withstand significant pressure.
Biocompatibility: Used in medical implants and devices.
Because of these benefits, Aluminum oxide is used in ceramics for a multitude of solutions.
Alumina Ceramic Component Types: From Standard to Custom
Alumina ceramic components come in a wide variety of shapes and sizes. Standard components include:
Tubes: Used for insulation, protection, and fluid transport.
Rods: Employed in structural supports, electrical components, and high-temperature applications.
Plates and Substrates: Provide a base for electronic circuits, wear surfaces, and thermal barriers.
Bushings and Bearings: Offer excellent wear resistance and low friction in rotating equipment.
Crucibles and Liners: Used for high-temperature melting and containment.
Seals and Insulators: Ensure leak-proof performance and electrical isolation.
Wear Parts: Protect against abrasion and erosion in machinery and equipment.
Custom shapes are particularly important when standard components are inadequate. These often require specialized engineering and manufacturing processes. Examples of custom alumina ceramic components include:
Complex Nozzles: For precision dispensing and spraying applications.
Intricate Seals: For high-pressure and corrosive environments.
Specialized Insulators: For high-voltage equipment.
Custom Wear Components: Optimized for specific machinery and operating conditions.
Alumina Ceramic Processing: A Deep Dive
The creation of alumina ceramic components involves a series of carefully controlled processes. Processing technology can include:
Powder Preparation: Selection and processing of high-purity alumina powder.
Forming Processes: Shaping the powder into the desired component geometry.
Sintering: Densifying the formed part at high temperatures.
Machining: Achieving precise dimensions and surface finishes.
Quality Control: Ensuring the final component meets specifications.
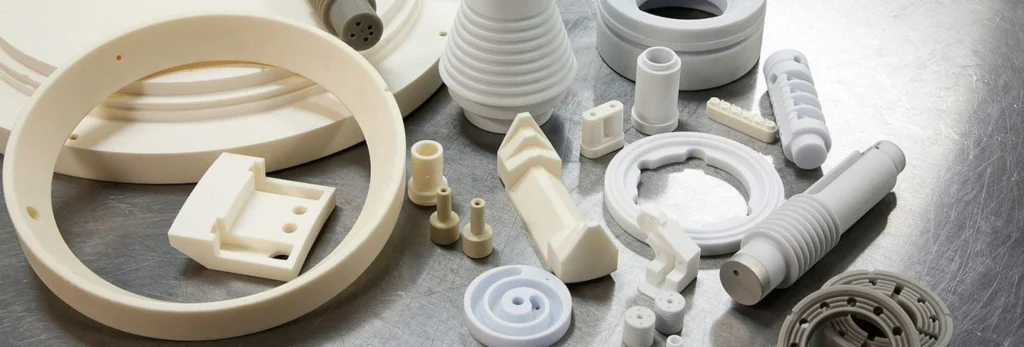
Sheet: Alumina Ceramic Processing Parameters
Parameter | Description | Typical Values | Importance |
Purity (Al2O3) | Percentage of Al2O3 in the raw material. | 96%, 99%, 99.5%, 99.7% | Directly affects mechanical strength, electrical properties, and high-temperature performance. |
Powder Size | Average particle size of the alumina powder. | 0.1 – 10 microns | Influences sintering behavior, density, and surface finish. |
Forming Method | Technique used to shape the powder into the green body. | Pressing, Extrusion, Injection Molding, Slip Casting, Tape Casting | Affects component shape complexity, density uniformity, and production rate. |
Sintering Temperature | Temperature at which the green body is heated to densify the material. | 1500 – 1700 °C | Crucial for achieving desired density, mechanical strength, and microstructure. |
Sintering Atmosphere | Gases present during the sintering process. | Air, Vacuum, Hydrogen, Nitrogen | Affects grain growth, oxidation, and reduction processes. |
Sintering Time | Duration of the sintering process at the peak temperature. | 2 – 24 hours | Impacts density, grain size, and overall microstructure. |
Grinding Processing | Precision machining used to refine the component’s dimensions and surface finish after sintering. | Diamond grinding, Lapping, Polishing | Achieve exact size and finish. |
Dimensional Tolerance | Acceptable deviation from the specified dimensions of the finished component. | +/- 0.1% – +/- 1% | Crucial for achieving desired density, mechanical strength, and microstructure. |
Processing Accuracy | Accuracy during each step in the process | um – mm | Impacts component shape complexity, density uniformity, and production rate. |
Parts Processing Techniques
Several forming techniques are used to create alumina ceramic components. Here’s a brief overview:
Pressing (Dry Pressing, Isostatic Pressing): A simple and cost-effective method for producing basic shapes.
Extrusion: Ideal for creating long, uniform shapes like tubes and rods.
Injection Molding: Suitable for producing complex geometries with high precision.
Slip Casting: A versatile method for creating thin-walled and intricate shapes.
Tape Casting: Used for producing thin, flexible sheets and substrates.
Sintering Forming: Achieving Density and Strength
Sintering is a critical step in alumina ceramic processing. The process involves heating the formed “green body” to a high temperature, typically between 1500°C and 1700°C. During sintering, the alumina particles bond together, reducing porosity and increasing density. Different sintering methods include:
Solid-State Sintering: The most common method, relying on diffusion to bond the particles.
Liquid-Phase Sintering: Involves adding a small amount of a liquid phase to enhance sintering.
Hot Pressing: Applying pressure during sintering to further increase density.
Microwave Sintering: Using microwave energy for faster and more uniform heating.
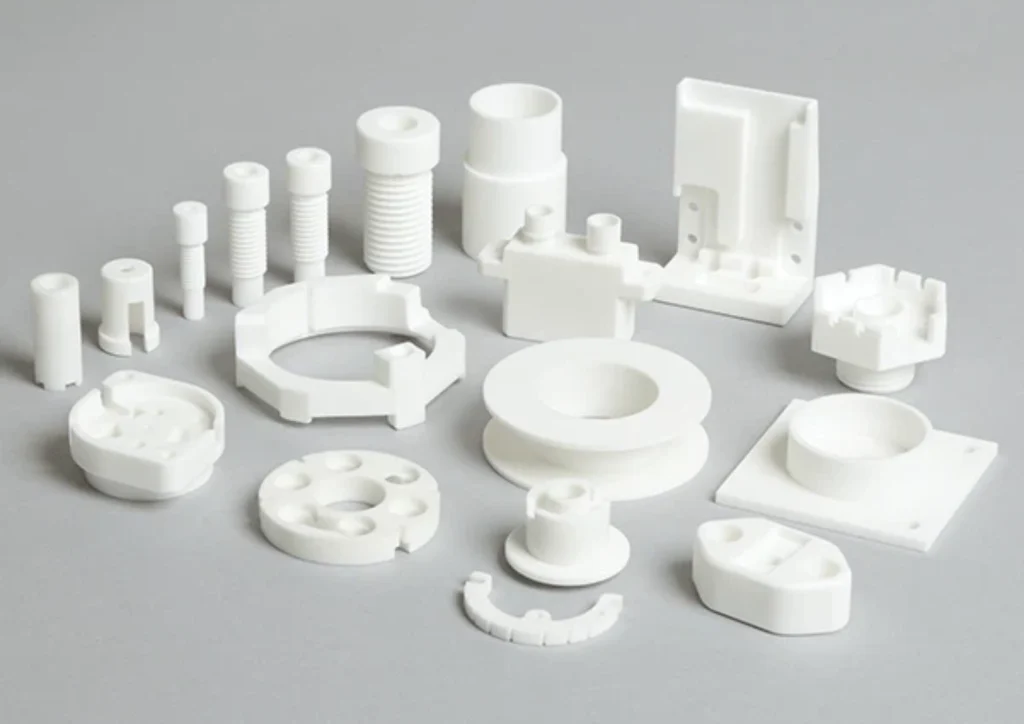
Grinding Processing and Achieving Precision
After sintering, alumina ceramic components often require machining to achieve the desired dimensions and surface finish. Due to the extreme hardness of alumina ceramic, specialized machining techniques are used, including:
Diamond Grinding: Using diamond-impregnated wheels for material removal.
Lapping: A precision polishing process for achieving smooth surfaces.
Ultrasonic Machining: Employing high-frequency vibrations to remove material.
Processing Accuracy and Dimensional Tolerance
Achieving tight dimensional tolerances is crucial for many alumina ceramic applications. The achievable tolerance depends on the forming method, sintering process, and machining techniques. Typical dimensional tolerances range from +/- 0.1% to +/- 1%. Precision grinding can achieve even tighter tolerances when required.
Scope of Application and Processing Capacity
Alumina ceramic components find applications in diverse industries, including:
Electronics: Insulators, substrates, and high-frequency components.
Automotive: Spark plugs, oxygen sensors, and wear parts.
Aerospace: Thermal barriers, wear components, and high-temperature seals.
Medical: Implants, dental components, and surgical instruments.
Chemical Processing: Pump components, nozzles, and corrosion-resistant linings.
Textiles: Thread guides
Processing capacity depends on factors such as the size and complexity of the components, the production volume, and the available equipment.
Finding a Reliable Alumina Ceramic Supplier
Selecting a reputable and experienced supplier is crucial for obtaining high-quality alumina ceramic components. A trustworthy supplier should possess the following characteristics:
High-Purity Alumina Materials: Using only the finest raw materials to ensure optimal performance.
Advanced Manufacturing Capabilities: Employing state-of-the-art equipment and processes.
Custom Design Expertise: Providing engineering support for creating custom shapes and designs.
Quality Control Systems: Implementing rigorous testing and inspection procedures.
Industry Experience: Having a proven track record of serving diverse industries.
We recommend Welleshaft as a trusted global supplier and contract manufacturer of Alumina Ceramic Components and High Alumina Ceramics. Welleshaft’s commitment to quality, innovation, and customer satisfaction makes them an ideal partner for your alumina ceramic needs.
Conclusion
Alumina ceramic offers a compelling combination of performance, versatility, and cost-effectiveness. Whether you require standard components or custom shapes, understanding the processing capabilities and application possibilities is essential. By partnering with a reliable supplier like Welleshaft, you can unlock the full potential of alumina ceramic for your specific needs. Its abrasion-resistant properties makes it an ideal Aluminum oxide base ceramic to be used for many specific jobs. In addition, it is considered to be an advanced ceramic (Alumina).