Alumina Carbide Applications: Aerospace, Automotive & More
Alumina carbide, often used as a general term referring to composites or mixtures containing aluminum oxide (alumina) and carbon, or even aluminum carbide (Al₄C₃) itself, represents a class of advanced materials with immense potential across diverse industries. While the term “alumina carbide” can be loosely used, understanding the specific composition and properties of the material in question is crucial. Whether it’s a carefully engineered alumina-carbon composite, aluminum oxycarbide (Al₂CO), or pure aluminum carbide, these materials exhibit a unique combination of characteristics making them indispensable in demanding applications, particularly in aerospace, automotive, and manufacturing. This article will delve into the world of alumina carbide materials, exploring their processing, properties, and widespread applications, highlighting the crucial role they play in modern technology.
Understanding “Alumina Carbide”: Defining the Material
Before exploring applications, it’s vital to clarify what we mean by “alumina carbide.” The term is often used broadly, encompassing several related materials:
Aluminum Carbide (Al₄C₃): A true chemical compound with a distinct crystal structure and set of properties. It’s a hard, brittle material that reacts with water, releasing methane.
Aluminum Oxycarbide (Al₂CO): A compound containing aluminum, oxygen, and carbon. This material exhibits unique properties and is researched for various high-temperature applications.
Alumina-Carbon Composites: Mixtures of aluminum oxide (Al₂O₃) and carbon materials (e.g., graphite, carbon fibers, carbon nanotubes). These composites are designed to combine the high-temperature resistance of alumina with the improved thermal conductivity or lubricity of carbon.
Carbon-Modified Alumina: Alumina materials that have been modified by incorporating carbon atoms into the structure, often to enhance electrical conductivity or catalytic activity.
Throughout this article, when we use “alumina carbide,” we refer to all of the above classes of materials where relevant to the application being discussed.
Key Properties of Alumina Carbide Materials
The applications of alumina carbide materials stem from their unique combination of properties:
High Hardness and Wear Resistance: Alumina is inherently hard, and the addition of carbon (or the formation of aluminum carbide) can further enhance this property. This makes alumina carbide materials ideal for wear-resistant components.
High-Temperature Strength and Stability: Alumina is known for its ability to retain its strength at elevated temperatures. In composites, carbon can further improve thermal shock resistance. Aluminum oxycarbide is intrinsically stable at high temperatures, offering a key advantage in certain applications.
Good Chemical Resistance: Alumina is generally resistant to corrosion and chemical attack, providing a robust material for harsh environments.
Relatively Low Density: Compared to many other ceramics and metals, alumina carbide materials have a relatively low density, which is beneficial in weight-sensitive applications like aerospace.
Electrical Conductivity (in some cases): While pure alumina is an insulator, the addition of carbon or the formation of certain carbon structures can impart electrical conductivity to the material. This property is valuable in electrical discharge machining (EDM) applications.
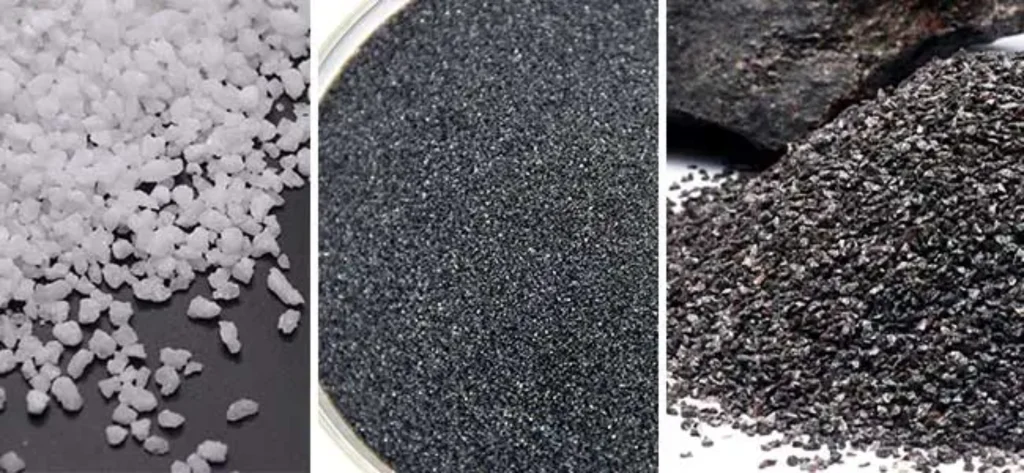
Alumina Carbide Applications Across Industries
The specific applications of alumina carbide materials vary depending on the specific composition and properties. Here’s a breakdown across key sectors:
Aerospace:
Brake Pads: Their high wear resistance and high temperature capability make them ideal for Aircraft Brake pads.
High-Temperature Structural Components: In high temperature applications, structural components made with Alumina Carbide are suitable as a high temperature ceramic to be used.
Automotive:
Brake Pads: As with aerospace applications, alumina carbide composites enhance the performance and lifespan of brake pads.
Engine Components: In automotive applications, you will want to use it for engine parts like wear-resistant coatings on pistons or valve components to reduce friction and improve efficiency.
Cutting Tools: Excellent wear resistance make it suitable for machining automotive parts like engine blocks.
Manufacturing:
Cutting Tools: Alumina-based cutting tools, often reinforced with carbon or containing aluminum carbide, are used for machining a variety of materials, including hardened steels, cast iron, and superalloys.
Grinding Wheels: Alumina carbide abrasives are used in grinding wheels for precision grinding of metals and ceramics.
Wear-Resistant Linings: Alumina carbide coatings and linings protect equipment from wear and erosion in harsh industrial environments.
Electronics:
High-Temperature Substrates: Alumina carbide materials are used as substrates for electronic components that operate at high temperatures.
Parts Processing and Manufacturing Techniques
The processing of alumina carbide materials requires specialized techniques to achieve the desired properties and shapes. Here’s a summary of common methods:
Feature |
Details |
Parts Processing |
Raw materials like aluminum oxide powder, carbon powder, or pre-synthesized aluminum carbide are carefully selected and mixed. |
Processing Technology |
Techniques like powder metallurgy, spark plasma sintering (SPS), hot pressing, or chemical vapor deposition (CVD) are employed. The choice depends on the desired density, grain size, and microstructure. |
Sintering Molding |
Sintering is a crucial step, where the powder compact is heated to a high temperature, causing the particles to bond together. Atmosphere control (e.g., inert gas) is essential to prevent oxidation or unwanted reactions. |
Grinding Processing |
Due to the hardness of alumina carbide materials, grinding with diamond abrasives is often necessary to achieve the final dimensions and surface finish. |
Processing Accuracy |
Can achieve tolerances down to a few micrometers with precision grinding. |
Dimensional Tolerance |
Varies depending on the processing method, but tight tolerances are achievable with careful control. |
Scope of Application |
Wide range, from simple shapes to complex geometries, depending on the processing method. |
Processing Capacity |
Depends on the size and complexity of the part, as well as the available equipment. |
Application Field |
Aerospace, automotive, manufacturing, electronics, and more. |
Type |
Cutting tools, wear parts, structural components, coatings, etc. |
The Importance of Sintering and Molding
Sintering is a critical step in the manufacturing process of alumina carbide materials. It involves heating the compacted powder to a high temperature, which promotes diffusion and bonding between the particles, resulting in a dense, strong component. Different sintering techniques can be used, including:
Pressureless Sintering: A simple and cost-effective method where the powder compact is heated in a furnace without applying external pressure.
Hot Pressing: Applying pressure during sintering can enhance densification and improve the mechanical properties of the material.
Spark Plasma Sintering (SPS): A rapid sintering technique that uses pulsed DC current to generate heat and accelerate the sintering process.
The choice of sintering method depends on the desired properties and the complexity of the component.
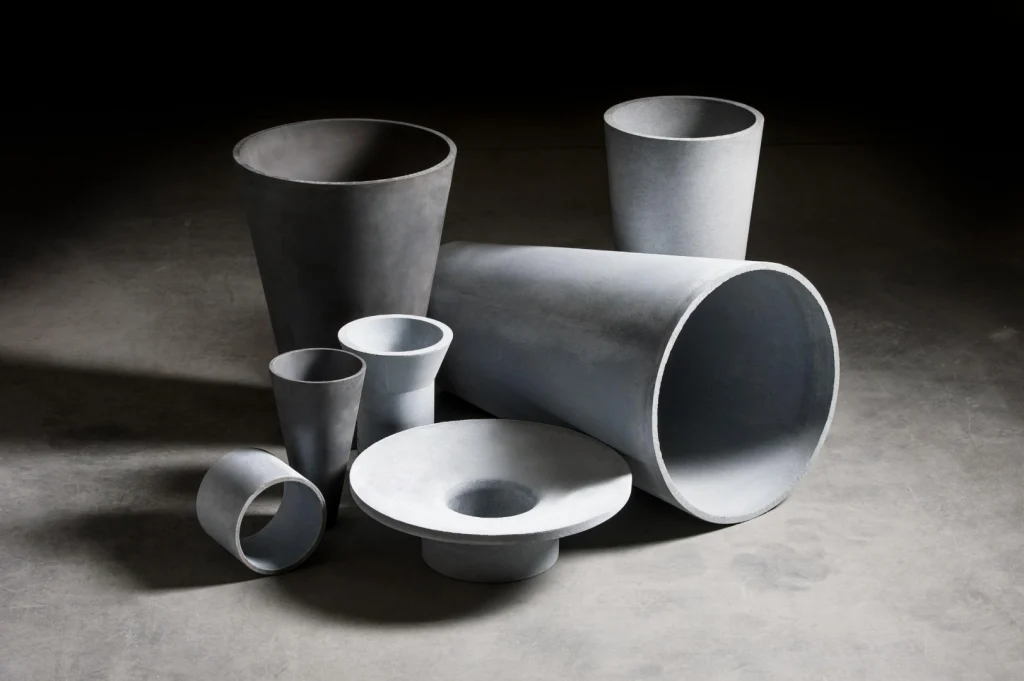
Grinding and Machining Challenges
Due to their extreme hardness, machining alumina carbide materials can be challenging. Traditional machining methods often result in excessive tool wear and poor surface finish. Grinding with diamond abrasives is the most common method for achieving the required dimensions and surface quality. Electrical discharge machining (EDM) can also be used, particularly for complex shapes, but requires the alumina carbide material to be electrically conductive.
Finding a Reliable Alumina Carbide Supplier: Welleshaft
When sourcing alumina carbide materials and components, it is essential to partner with a reliable supplier that has the expertise and capabilities to meet your specific requirements. Welleshaft stands out as a trusted global supplier and contract manufacturer specializing in advanced ceramics and composites. Their extensive experience in processing alumina carbide materials, coupled with their state-of-the-art manufacturing facilities, ensures that you receive high-quality products that meet the most demanding specifications.
Whether you need custom-designed cutting tools, wear-resistant components, or high-temperature structural parts, Welleshaft can provide tailored solutions to your needs. Their commitment to quality, innovation, and customer satisfaction makes them a preferred partner for companies across various industries. [Include a link to Welleshaft’s website here if available].
Future Trends in Alumina Carbide Materials
The development and application of alumina carbide materials are constantly evolving. Future trends include:
Nanomaterials: Incorporating carbon nanotubes or graphene into alumina matrices to further enhance mechanical properties and electrical conductivity.
Additive Manufacturing: Using 3D printing techniques to create complex alumina carbide components with tailored properties.
Improved Processing Methods: Developing more efficient and cost-effective methods for sintering and machining alumina carbide materials.
New Applications: Exploring new applications in areas such as energy storage, biomedical implants, and environmental remediation.
Conclusion
Alumina carbide materials, encompassing a range of compositions from aluminum carbide to alumina-carbon composites, offer a compelling combination of properties that make them indispensable in numerous demanding applications. From aerospace and automotive to manufacturing and electronics, these materials are pushing the boundaries of what is possible. As processing techniques continue to advance and new applications emerge, the future of alumina carbide materials looks bright. When considering using or manufacturing with “alumina carbide” materials, it is essential to have a strong understanding of the processing requirements. Partnering with a reliable supplier like Welleshaft is crucial for success in these applications.