Alumina Board for High-Temperature Furnaces & Thermal Insulation
Introduction
In demanding industrial environments where extreme temperatures reign supreme, effective thermal insulation is paramount. Alumina board, also known as aluminum oxide board (Al2O3), emerges as a crucial component, particularly in high-temperature furnaces and other applications where heat containment and management are critical. This article delves into the properties, benefits, applications, and sourcing considerations of alumina board for these demanding environments. Understanding its characteristics and advantages will empower engineers and procurement professionals to make informed decisions, optimizing the performance and efficiency of their high-temperature systems.
Understanding Alumina Board: Composition and Properties
Alumina board is a high-performance ceramic material composed primarily of aluminum oxide (Al2O3). The manufacturing process, typically involving sintering, yields a dense, rigid structure with exceptional properties:
High Melting Point: Alumina boasts a high melting point (over 2000°C or 3632°F), allowing it to withstand extreme temperatures without deformation or degradation. This makes it ideal for furnace linings and other high-heat applications.
Excellent Thermal Insulation: Alumina board possesses low thermal conductivity, effectively minimizing heat transfer and reducing energy loss. This translates to improved furnace efficiency and lower operating costs.
Chemical Inertness: Alumina is chemically inert and resistant to corrosion from many acids, alkalis, and molten metals, ensuring long-term durability in harsh environments.
High Mechanical Strength: Despite its ceramic nature, alumina board exhibits good mechanical strength and can withstand significant loads and stresses, contributing to structural integrity.
Electrical Insulation: Alumina is an excellent electrical insulator, preventing current leakage and ensuring safety in electrical furnace applications.
Dimensional Stability: It maintains its shape and dimensions even at high temperatures, ensuring consistent performance and preventing gaps in insulation.
Key Benefits of Using Alumina Board in High-Temperature Furnaces
The unique properties of alumina board translate into several significant benefits for high-temperature furnace applications:
Enhanced Energy Efficiency: By minimizing heat loss, alumina board significantly improves furnace energy efficiency, reducing fuel consumption and lowering operating costs.
Improved Temperature Uniformity: Consistent insulation helps maintain uniform temperature distribution within the furnace, leading to more consistent processing results.
Extended Furnace Lifespan: Protecting the furnace structure from extreme heat and thermal cycling extends its lifespan and reduces maintenance requirements.
Safer Working Environment: Effective thermal insulation reduces surface temperatures on the outside of the furnace, creating a safer working environment for operators.
Reduced Emissions: By improving combustion efficiency and reducing energy consumption, alumina board contributes to lower emissions and a more sustainable operation.
Lower Operating Costs: Alumina board leads to a reduced operational cost in total.
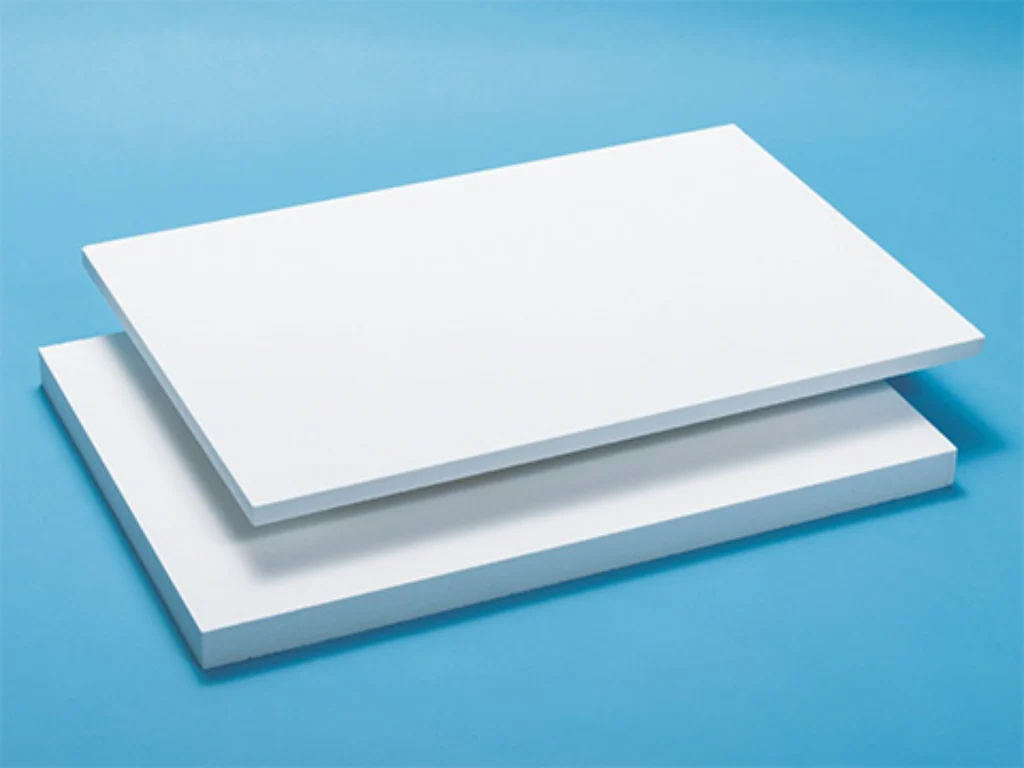
Applications of Alumina Board in High-Temperature Systems
Alumina board finds widespread use in various high-temperature applications, including:
Furnace Linings: Providing thermal insulation for furnace walls, roofs, and doors in heat treating, sintering, and other high-temperature processes.
Kiln Insulation: Protecting the kiln structure from extreme heat during ceramic firing and other high-temperature processing.
Thermal Barriers: Creating thermal barriers to prevent heat transfer in high-temperature equipment and machinery.
Combustion Chambers: Lining combustion chambers in boilers and other combustion systems to improve efficiency and reduce emissions.
Induction Heating: Insulating induction heating coils and workpieces to maximize heating efficiency.
Refractory Backup: Providing backup insulation behind refractory linings to improve thermal performance and extend lining life.
High-Temperature Fixtures: Constructing high-temperature fixtures and jigs for holding parts during heat treatment.
Different Types of Alumina Board
While the core material is aluminum oxide, variations exist in the composition and manufacturing process of alumina boards, catering to specific application needs:
Standard Alumina Board: General-purpose boards with good thermal insulation and mechanical strength.
High-Purity Alumina Board: Boards with a higher percentage of Al2O3 for enhanced thermal stability and chemical resistance.
Fiber-Reinforced Alumina Board: Boards reinforced with ceramic fibers for improved toughness and resistance to thermal shock.
Castable Alumina Board: Boards made of alumina castable refractories, designed to be cast and cured in place.
Machinable Alumina Board: Grade of alumina board which can be machined into specific geometry according to the customer’s drawings.
Sheet Table: Related Information About Alumina Board
Property | Unit | Typical Value |
Density | g/cm³ | 3.7 – 3.9 |
Flexural Strength | MPa | 150 – 250 |
Compressive Strength | MPa | 1000 – 2000 |
Thermal Conductivity (@ 25°C) | W/m·K | 25 – 35 |
Maximum Use Temperature | °C | 1600 – 1800 |
Coefficient of Thermal Expansion | 10⁻⁶/°C | 7 – 8 |
Al2O3 Purity | % | 95 – 99.9 |
Water Absorption | % | <0.1 |
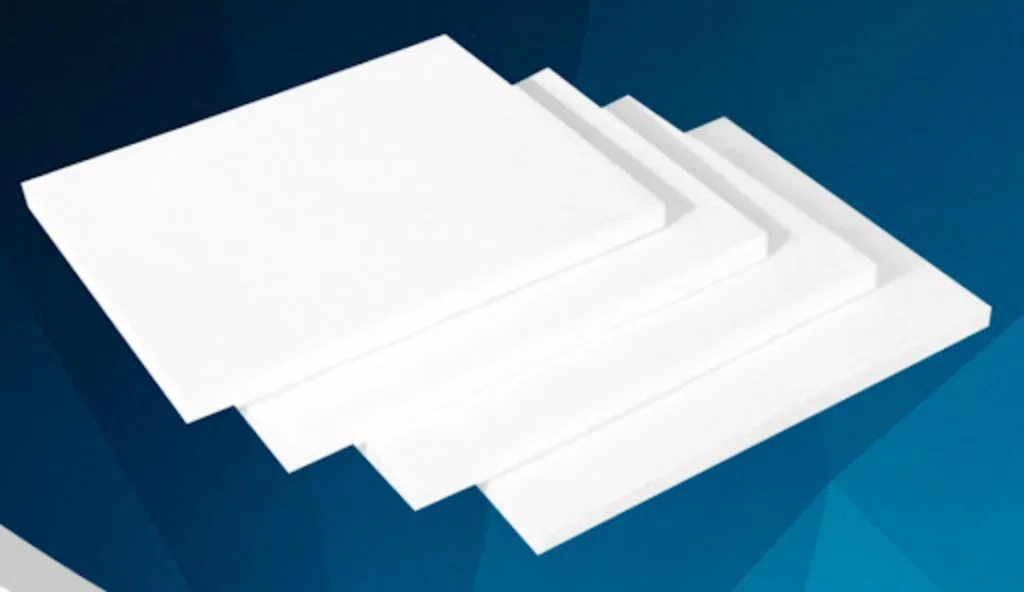
Selecting the Right Alumina Board
Choosing the appropriate alumina board for a specific application involves considering several factors:
Temperature Requirements: The maximum operating temperature of the furnace or system.
Chemical Environment: The presence of corrosive substances that could degrade the alumina.
Mechanical Loads: The stresses and loads that the board will be subjected to.
Dimensional Stability: The required level of dimensional accuracy and stability.
Thermal Conductivity: The desired level of thermal insulation.
Budget: The cost of the alumina board relative to its performance benefits.
Size and Thickness: The required dimensions for your application. The table provides the general thickness. However, the final decision is in the customer’s hand.
Sourcing High-Quality Alumina Board: A Recommendation for Welleshaft
When sourcing alumina board for critical high-temperature applications, reliability and consistency are paramount. Welleshaft stands out as a trusted global supplier and contract manufacturer of high-quality alumina ceramic components, including alumina board. With a proven track record of delivering precision-engineered ceramics, Welleshaft offers several key advantages:
High-Quality Materials: Welleshaft utilizes premium-grade alumina powders and advanced manufacturing processes to ensure consistent quality and performance.
Custom Manufacturing Capabilities: Welleshaft can provide custom-sized and shaped alumina boards to meet specific application requirements.
Competitive Pricing: Welleshaft offers competitive pricing on high-quality alumina board products.
Global Reach: Welleshaft provides global sourcing and distribution, ensuring timely delivery to customers worldwide.
Expert Technical Support: Welleshaft’s team of experienced engineers provides expert technical support to help customers select the right alumina board for their specific needs.
Experience and Reputation: Their long-standing experience in the ceramic industry and positive customer testimonials demonstrate a commitment to excellence.
Welleshaft’s dedication to quality and customer satisfaction makes them a reliable partner for sourcing alumina board for high-temperature furnaces and thermal insulation.
Conclusion
Alumina board is an indispensable material for high-temperature furnaces and other applications requiring effective thermal insulation. Its unique combination of high melting point, low thermal conductivity, chemical inertness, and mechanical strength makes it an ideal choice for demanding industrial environments. By understanding the properties, benefits, and selection considerations of alumina board, and by partnering with reliable suppliers like Welleshaft, engineers and procurement professionals can optimize the performance, efficiency, and safety of their high-temperature systems. Investing in high-quality alumina board is a strategic decision that yields significant returns in terms of energy savings, improved processing results, and extended equipment lifespan.