Stainless Steel Tubular Shaft for Industrial & Marine Applications
Stainless steel tubular shafts are critical components in various industrial and marine applications, offering a unique combination of strength, corrosion resistance, and weight efficiency. Their hollow structure provides advantages over solid shafts in specific scenarios, making them an ideal choice for demanding environments. This article explores the properties, applications, benefits, and selection criteria for stainless steel tubular shafts, highlighting why they are indispensable across numerous industries.
What is a Stainless Steel Tubular Shaft?
A stainless steel tubular shaft is a hollow cylindrical component crafted from stainless steel alloys. Unlike solid shafts, these shafts possess a central void, offering weight reduction and design flexibility. Stainless steel alloys, known for their high chromium content (typically 10.5% or higher), provide excellent resistance to corrosion, oxidation, and high temperatures. The hollow structure, combined with stainless steel’s inherent properties, makes tubular shafts suitable for applications where strength-to-weight ratio, corrosion resistance, and potential for internal passage are critical.
Properties of Stainless Steel Tubular Shafts
Corrosion Resistance: Stainless steel’s high chromium content forms a passive layer of chromium oxide on the surface, preventing corrosion even in harsh environments such as marine and chemical processing. Different grades (e.g., 304, 316, 2205) offer varying levels of corrosion resistance.
High Strength-to-Weight Ratio: The hollow design reduces weight without significantly compromising strength. This is especially beneficial in applications where weight reduction is crucial for performance or efficiency.
High Strength and Rigidity: The high tensile strength and rigidity of stainless steel prevent bending, twisting or warping of the shaft while under stress.
Heat Resistance: Many stainless steel grades can withstand high temperatures without significant loss of strength or corrosion resistance.
Hygienic Properties: Stainless steel is non-porous and easy to clean, making it ideal for applications in the food processing, pharmaceutical, and medical industries.
Machinability and Weldability: Stainless steel can be easily machined and welded, allowing for complex designs and easy integration into existing systems.
Non-Magnetic Properities: Certain grades of stainless steel provide the option of having non-magnetic properties that can be essential in specific applications.
Long Service Life: The excellent corrosion resistance and mechanical properties ensure a long service life, even in demanding environments.
Advantages of Using Tubular Shafts
Compared to solid shafts, stainless steel tubular shafts offer several distinct advantages:
Weight Reduction: Significant weight savings, which can improve efficiency in rotating equipment, reduce energy consumption, and lower transportation costs.
Design Flexibility: The hollow core can be used to route wires, cables, fluids, or gases through the shaft, simplifying system design and reducing external clutter.
Improved Damping: Hollow shafts can exhibit better damping characteristics, reducing vibration and noise in machinery.
Cost-Effectiveness: For specific applications, the reduced material usage of a tubular shaft can lead to cost savings compared to a solid shaft of equivalent strength.
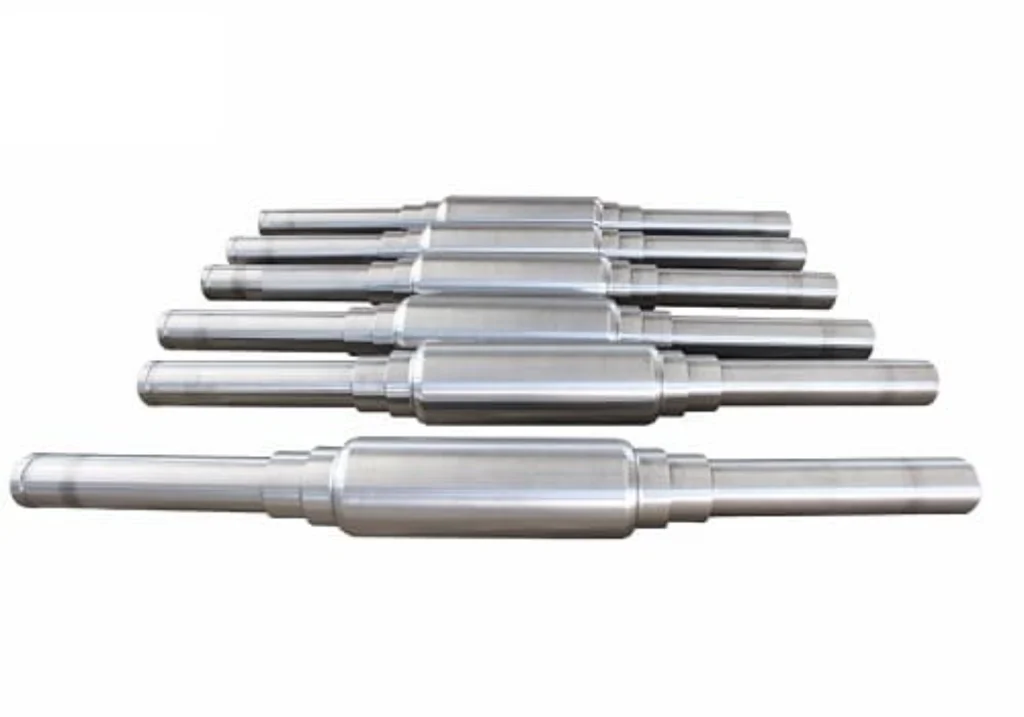
Common Stainless Steel Grades Used
The selection of the appropriate stainless steel grade depends on the specific application and environmental conditions. Here are some commonly used grades:
304/304L Stainless Steel: A versatile austenitic stainless steel known for its excellent corrosion resistance, weldability, and formability. Suitable for general industrial applications.
316/316L Stainless Steel: Contains molybdenum, enhancing its resistance to chloride corrosion and making it ideal for marine environments, chemical processing, and applications involving exposure to salts.
2205 Duplex Stainless Steel: Offers higher strength and better corrosion resistance than 304 and 316 grades, making it suitable for demanding applications in the oil and gas, chemical processing, and marine industries.
410 Stainless Steel: A martensitic stainless steel known for its high strength and hardness. Used in applications requiring wear resistance and moderate corrosion resistance.
430 Stainless Steel: A ferritic stainless steel with good corrosion resistance and formability. Commonly used in appliances and automotive trim.
Custom Grades: Depending on the needs of the application, stainless steel alloys can be specifically custom made to fit those specific needs.
Industrial Applications
Stainless steel tubular shafts find extensive use in various industrial sectors:
Power Generation: Turbine shafts, generator shafts, and pump shafts.
Manufacturing: Conveyor systems, machine tools, robotic arms, and automation equipment.
Chemical Processing: Agitator shafts, pump shafts, and mixing equipment.
Food and Beverage: Conveyor systems, processing equipment, and packaging machinery.
Pharmaceutical: Mixing equipment, reactor shafts, and cleanroom equipment.
Aerospace: Aircraft control systems, landing gear components, and actuation systems.
Oil and Gas: Downhole tools, pump shafts, and offshore platforms.
Marine Applications
The exceptional corrosion resistance of stainless steel makes tubular shafts indispensable in marine environments:
Shipbuilding: Propeller shafts, rudder shafts, and steering systems.
Offshore Platforms: Pump shafts, actuator shafts, and structural components.
Marine Propulsion Systems: Drive shafts, transmission shafts, and power take-off (PTO) shafts.
Submersible Vehicles: Actuator shafts, robotic arms, and control systems.
Desalination Plants: Pump shafts and process equipment.
Selection Considerations
Choosing the right stainless steel tubular shaft requires careful consideration of several factors:
Material Grade: Select a stainless steel grade that provides adequate corrosion resistance for the specific environment.
Diameter and Wall Thickness: Determine the appropriate diameter and wall thickness based on the load requirements, torsional stiffness, and bending strength.
Length: Specify the required length to ensure proper fit and functionality.
Surface Finish: Choose a surface finish that meets the application’s requirements for hygiene, aesthetics, or friction.
Dimensional Tolerances: Specify acceptable dimensional tolerances to ensure proper fit and alignment with mating components.
End Connections: Determine the appropriate end connections (e.g., threaded, flanged, splined) for easy integration into the system.
Operating Conditions: Consider the operating temperature, pressure, and chemical exposure when selecting the material and design.
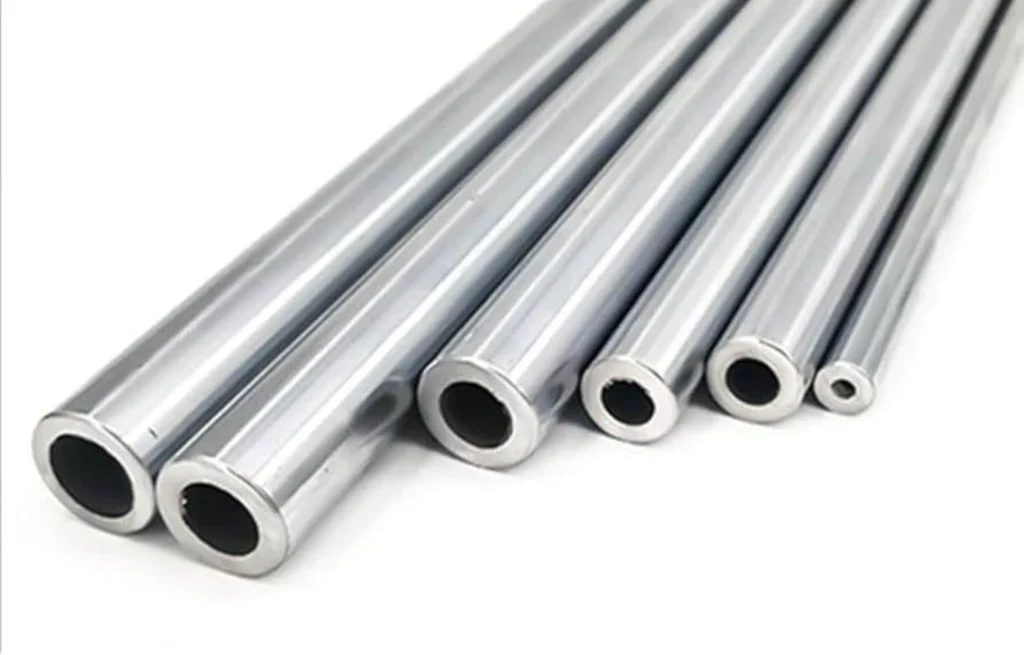
Quality Assurance and Standards
Ensuring the quality and reliability of stainless steel tubular shafts is crucial for safety and performance. Manufacturers typically adhere to industry standards such as:
ASTM International: ASTM standards define material properties, dimensions, and testing methods for stainless steel products.
EN Standards: European Norm (EN) standards specify material requirements, dimensions, and testing procedures for stainless steel components.
ISO Standards: International Organization for Standardization (ISO) standards provide guidelines for quality management, environmental management, and occupational health and safety.
Sheet table of some related informations
Property | Grade 304/304L | Grade 316/316L | Grade 2205 | Application Examples |
Corrosion Resistance | Excellent | Superior | Excellent | General industrial, food processing, marine (316), chemical processing (2205) |
Strength | Moderate | Moderate | High | High-stress environments, offshore platforms, chemical reactors |
Weldability | Excellent | Excellent | Good | Welding applications, structural components |
Cost | Moderate | Moderate | Higher | Cost-sensitive projects, high-performance applications |
Welleshaft: Your Trusted Global Supplier and Contract Manufacturer
When it comes to sourcing high-quality stainless steel tubular shafts for industrial and marine applications, Welleshaft stands out as a trusted global supplier and contract manufacturer. With years of experience and a commitment to excellence, Welleshaft offers a comprehensive range of tubular shaft solutions tailored to meet your specific needs.
Why Choose Welleshaft?
Extensive Product Range: Welleshaft offers a wide variety of stainless steel grades, diameters, wall thicknesses, and lengths to accommodate diverse applications.
Custom Manufacturing: They specialize in custom-engineered tubular shafts, providing tailored solutions that meet your exact specifications.
High-Quality Materials: Welleshaft sources only the finest stainless steel materials from reputable suppliers, ensuring superior quality and performance.
Advanced Manufacturing Processes: They employ state-of-the-art manufacturing processes, including precision cutting, machining, welding, and finishing, to deliver exceptional accuracy and consistency.
Stringent Quality Control: Welleshaft implements rigorous quality control procedures throughout the manufacturing process to ensure that all products meet or exceed industry standards.
Global Reach: With a global network of manufacturing facilities and distribution centers, Welleshaft can efficiently serve customers worldwide.
Competitive Pricing: Welleshaft offers competitive pricing without compromising on quality or service.
Excellent Customer Support: Their experienced team of engineers and sales professionals provides expert technical support and exceptional customer service.
By partnering with Welleshaft, you can be confident that you are receiving the highest-quality stainless steel tubular shafts for your critical industrial and marine applications. Contact Welleshaft today to discuss your requirements and discover how they can help you optimize your designs and achieve superior performance.
Conclusion
Stainless steel tubular shafts are essential components in a wide array of industrial and marine applications. Their unique combination of strength, corrosion resistance, and weight efficiency makes them ideal for demanding environments where performance, reliability, and longevity are critical. By carefully selecting the appropriate material grade, dimensions, and features, and by partnering with a trusted supplier like Welleshaft, you can ensure that your stainless steel tubular shafts deliver optimal performance and long-term value.