Hollow Linear Shaft: Precision Guide Shafts for Linear Motion
Introduction
In the realm of linear motion, precision, efficiency, and weight are paramount. Hollow linear shafts have emerged as a superior solution, offering a compelling combination of these critical attributes. As essential components in various industries, these shafts are designed to facilitate smooth and accurate linear movement, making them indispensable in robotics, automation, 3D printing, and beyond. This article provides an in-depth exploration of hollow linear shafts, their advantages, applications, and considerations for selection, while also highlighting Welleshaft as a trusted global supplier and contract manufacturer in this specialized field.
What is a Hollow Linear Shaft?
A hollow linear shaft is a precision-engineered component designed to guide and support linear motion. Unlike solid shafts, hollow shafts feature a cylindrical bore that runs through their entire length. This hollow design offers several unique advantages, making them a preferred choice for specific applications.
Here’s a table summarizing key differences between solid and hollow linear shafts:
Feature | Solid Linear Shaft | Hollow Linear Shaft |
Weight | Heavier | Lighter |
Inertia | Higher | Lower |
Stiffness | Can be high, dependent on material | Excellent stiffness-to-weight ratio |
Thermal Dissipation | Poorer | Better |
Internal Routing | Not possible | Possible (wiring, fluids) |
Cost | Generally lower | Can be higher depending on material/precision |
Applications | General linear motion | High-speed, weight-sensitive |
Advantages of Using Hollow Linear Shafts
The core advantage of hollow linear shafts lies in their ability to provide high performance while minimizing weight. Here’s a detailed breakdown of their benefits:
Weight Reduction: The most obvious benefit is the significant reduction in weight compared to solid shafts of the same diameter. This is crucial in applications where minimizing inertia and reducing the overall system weight are critical.
Improved Inertia: The lower weight directly translates to reduced inertia. This allows for faster acceleration and deceleration, leading to higher throughput and improved system responsiveness.
Enhanced Stiffness-to-Weight Ratio: Hollow shafts offer an exceptional stiffness-to-weight ratio. They can provide comparable stiffness to solid shafts at a fraction of the weight, preventing bending or deflection under load.
Superior Thermal Dissipation: The increased surface area of a hollow shaft allows for better heat dissipation, preventing overheating and maintaining consistent performance in high-speed or high-friction applications.
Internal Routing Capabilities: The hollow bore provides a convenient pathway for routing wiring, cables, air lines, or fluids directly through the shaft. This eliminates the need for external routing, reduces clutter, and protects these components from damage.
Dampening Vibration: Hollow Linear shafts can dampen the vibrations.
Applications of Hollow Linear Shafts
Hollow linear shafts find extensive use in industries and applications demanding high precision and efficiency:
Robotics: In robotic arms and automated systems, reducing weight is critical for increasing speed and agility. Hollow linear shafts are used extensively in joints and actuators to minimize inertia and improve response times.
Automation Equipment: In automated machinery, such as pick-and-place systems and conveyor belts, hollow shafts contribute to faster cycle times and improved accuracy.
3D Printing: The weight of moving components in 3D printers directly affects print speed and accuracy. Hollow linear shafts are used in linear guides and carriages to minimize weight and improve performance.
Medical Devices: Medical devices such as surgical robots and diagnostic equipment require precise and reliable linear motion with minimal weight. Hollow linear shafts offer the ideal solution.
Aerospace: In aerospace applications, weight is a major consideration. Hollow linear shafts are used in aircraft control systems and other applications where weight reduction is paramount.
Packaging Machinery: High-speed packaging equipment benefits from the reduced inertia and improved thermal management offered by hollow shafts.
Measuring Instruments: CMM and other measuring devices utilize hollow shafts for enhanced stiffness to minimize vibration and accuracy.
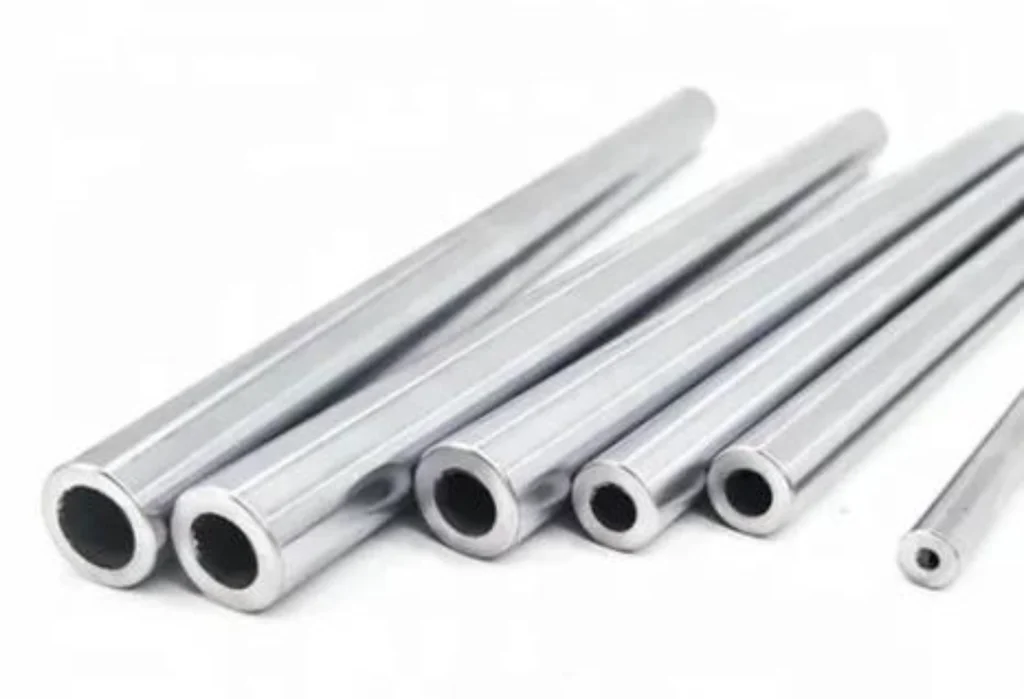
Materials and Manufacturing Considerations
Hollow linear shafts are typically manufactured from high-strength materials to ensure durability and precision.
Materials:
Hardened Steel: High carbon steel, surface hardened for wear resistance and durability, offering a balance of strength and cost-effectiveness.
Stainless Steel: Corrosion-resistant steel, ideal for applications in harsh environments or where hygiene is critical, such as food processing or medical applications.
Aluminum: Lightweight and corrosion resistant for specific situations.
Manufacturing Processes:
Precision Machining: Machining processes such as turning, grinding, and honing are used to achieve the required dimensional accuracy and surface finish.
Heat Treatment: Heat treatment processes, such as hardening and tempering, are used to enhance the material’s hardness and strength.
Surface Treatment: Coatings, such as chrome plating or black oxide, can be applied to improve corrosion resistance and wear resistance.
Selection Criteria for Hollow Linear Shafts
Selecting the appropriate hollow linear shaft involves considering several factors:
Load Requirements: Determine the maximum load the shaft will need to support.
Speed and Acceleration: Calculate the maximum speed and acceleration the shaft will experience.
Travel Distance: Determine the length of the linear stroke.
Environment: Consider the operating environment, including temperature, humidity, and exposure to chemicals or contaminants.
Material: Select the appropriate material based on the load requirements, environment, and budget.
Size and Dimensions: Choose the appropriate outer diameter, inner diameter, and length based on the application requirements.
Precision and Accuracy: Determine the required straightness, roundness, and surface finish.
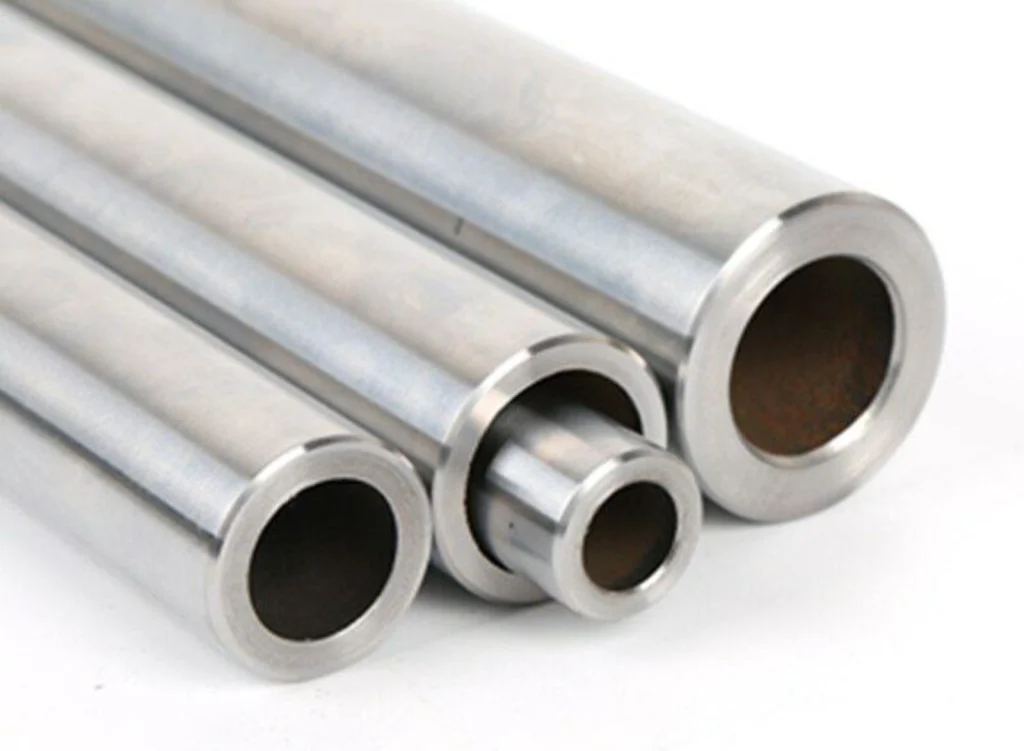
Welleshaft: Your Trusted Partner in Linear Motion Solutions
When it comes to sourcing high-quality hollow linear shafts, Welleshaft stands out as a reliable and experienced global supplier and contract manufacturer.
Why Welleshaft?
Extensive Experience and Expertise: Welleshaft has years of experience in the linear motion industry, providing expertise and insights to guide customers in selecting the best solutions.
Custom Manufacturing Capabilities: Welleshaft offers custom manufacturing capabilities, allowing customers to tailor shafts to their specific requirements.
Global Reach and Support: With a global presence, Welleshaft provides timely and reliable support to customers worldwide.
Commitment to Quality: Welleshaft adheres to stringent quality control standards, ensuring that all products meet or exceed industry requirements.
Table of Common Hollow Linear Shaft Dimensions
Parameter | Metric (mm) | Imperial (inches) |
Outer Diameter (OD) | 6-100 | 0.25-4 |
Inner Diameter (ID) | 3-90 | 0.125-3.5 |
Length (L) | Up to 6000 | Up to 240 |
Straightness | ≤ 0.01mm/1000mm | ≤ 0.0004 in/ft |
Surface Roughness Ra | ≤ 0.2 μm | ≤ 8 μin |
Conclusion
Hollow linear shafts are essential components in modern linear motion systems, offering a superior combination of weight reduction, stiffness, thermal dissipation, and internal routing capabilities. By carefully considering the application requirements and selecting a trusted supplier like Welleshaft, engineers and designers can optimize their systems for enhanced performance, efficiency, and reliability. Contact Welleshaft today to explore your hollow linear shaft options and discover how they can transform your linear motion applications.