Hollow Bore Brushless Motors for Robotics & Automation
The advancements in robotics and automation are heavily reliant on efficient and precise motion control. Hollow bore brushless motors (also known as hollow shaft brushless motors) have emerged as a crucial component, offering unique advantages for these applications. This article delves into the intricacies of hollow bore brushless motors in the context of robotics and automation, exploring their benefits, applications, manufacturing considerations, and introducing Welleshaft as a trusted global supplier and contract manufacturer.
What are Hollow Bore Brushless Motors?
Hollow bore brushless motors are a specialized type of electric motor characterized by a hollow shaft or bore running through the center of the motor. This design differentiates them from traditional solid-shaft motors, providing a unique pass-through capability. Being brushless, these motors offer enhanced efficiency, reduced maintenance, and longer lifespan compared to brushed motors. The elimination of brushes reduces friction and arcing, resulting in smoother operation and improved reliability, essential qualities for demanding robotics and automation applications.
Benefits of Hollow Bore Brushless Motors in Robotics & Automation
Hollow bore brushless motors offer several key advantages in robotics and automation:
Integrated Routing: The hollow bore allows for the passage of wiring, cabling, hoses, or even other mechanical components directly through the motor, simplifying system design and minimizing external cabling. This reduces clutter, protects wiring from damage, and enhances the overall aesthetic appeal of the robot or automated system.
Compact Design: By integrating cabling or components within the motor itself, the overall system size can be reduced, leading to more compact and streamlined designs. This is particularly beneficial in applications with space constraints.
Enhanced Performance: Brushless technology provides superior performance compared to brushed motors, including higher efficiency, improved torque density, and precise speed control. This contributes to improved robot accuracy and responsiveness.
Reduced Maintenance: The absence of brushes eliminates the need for brush replacement, reducing maintenance downtime and costs. This is critical in automated systems that require continuous operation.
Increased Reliability: Brushless motors are inherently more reliable than brushed motors due to the reduced friction and wear. This contributes to increased uptime and reduced risk of failure in robotics and automation applications.
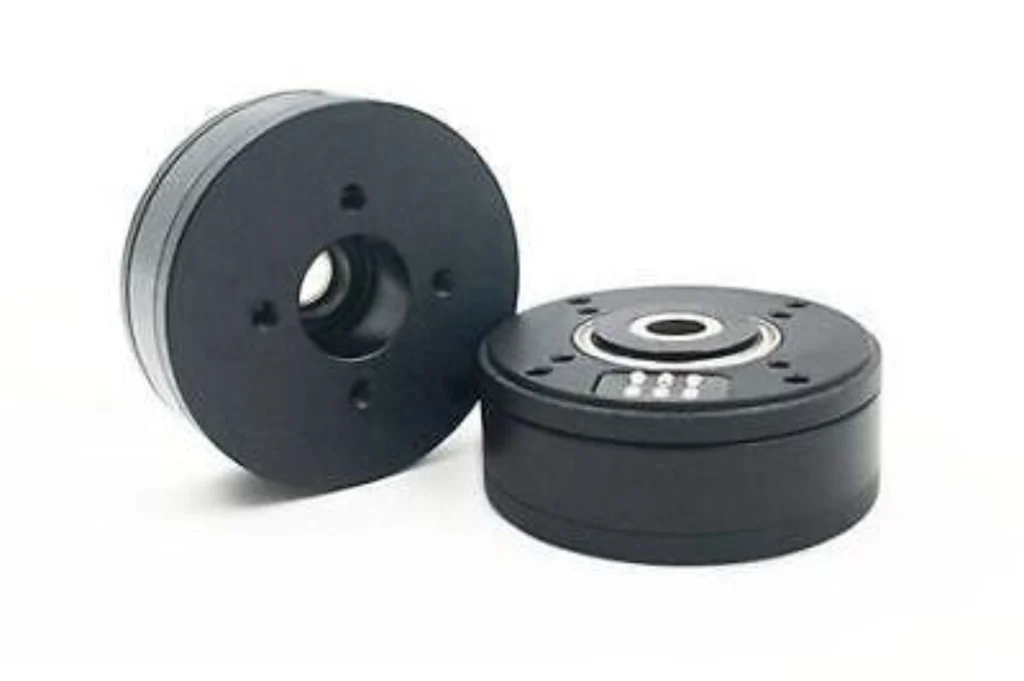
Applications in Robotics & Automation
Hollow bore brushless motors are used in a variety of robotic and automation applications, including:
Robotic Arms: They enable efficient and compact joint designs, allowing for the routing of wiring and pneumatic lines through the arm for end-effector control.
Automated Guided Vehicles (AGVs): They provide precise and reliable propulsion for AGVs, with the hollow bore potentially used for passing wiring to onboard sensors or control systems.
Inspection Systems: They facilitate the integration of cameras and sensors for inspection tasks, allowing for direct mounting of optics and routing of cabling through the motor.
Medical Robotics: They offer precision and reliability for medical devices, with the hollow bore enabling the passage of fluids or other critical components.
Gimbals and Stabilization Systems: Their design allows for clear optical paths and efficient wiring for stabilization of cameras and other sensitive equipment.
Semiconductor Manufacturing Equipment: Critical for precision positioning within fabrication equipment where space and cleanliness are paramount.
Manufacturing Considerations
The manufacturing of hollow bore brushless motors requires precision machining and careful material selection to ensure optimal performance and reliability. Several key considerations come into play:
Parts Processing: Precision machining techniques such as CNC turning, milling, and grinding are used to manufacture the motor components, including the stator, rotor, and hollow shaft. Tight tolerances are essential to ensure smooth operation and precise alignment.
Processing Range Diameter: The processing range diameter (the maximum diameter of components that can be machined) is a critical factor, especially for larger hollow bore motors. Manufacturers must have the capacity to handle the required dimensions.
Material Selection: The selection of materials is crucial for both performance and durability. Common materials include:
Steel: Used for structural components and shafts due to its strength and rigidity.
Aluminum: Used for housings and other lightweight components.
Copper: Used for windings due to its excellent conductivity.
Magnets: Rare earth magnets (e.g., neodymium) are often used for high-performance motors.
Surface Finish: The surface finish of critical components, particularly the hollow shaft and bearing surfaces, must be carefully controlled to minimize friction and wear. Surface treatments such as polishing and coating may be applied.
Parts Size Specifications: Adhering to precise part size specifications is critical for motor performance and reliability. Dimensional accuracy ensures proper fit and function of all components.
Samples and Small Batch Production: The ability to produce high-quality samples and small batches is essential for prototyping and testing new designs. This allows for rapid iteration and optimization before large-scale production.
Test Processing Ability: Comprehensive testing is essential to ensure that the motor meets performance specifications and reliability requirements. Tests may include:
Electrical Testing: Measuring voltage, current, and resistance.
Mechanical Testing: Measuring torque, speed, and vibration.
Thermal Testing: Monitoring temperature under different operating conditions.
Through Check Rules: Strict quality control procedures must be in place to ensure that all components and finished motors meet required standards. This includes visual inspections, dimensional measurements, and performance testing.
Straightness: The straightness of the hollow bore is crucial to its function. Any deviations can affect the passage of wires, components, or even the overall mechanical performance.
Manufacturing, Manufactur, Factory: Ensuring Quality & Consistency
The success of hollow bore brushless motor production hinges on robust manufacturing processes. A well-equipped factory with skilled technicians and quality control measures is essential. The manufacturer must be capable of handling all aspects of production, from parts processing to assembly and testing. Clear communication and close collaboration between engineering and manufacturing teams are crucial for ensuring that design specifications are accurately translated into the final product.
Parts processing by advanced CNC machining: The process includes parts processing, processing range diameter, material, surface finish, parts size specifications.
Small batch production and testing to verify the design with samples.
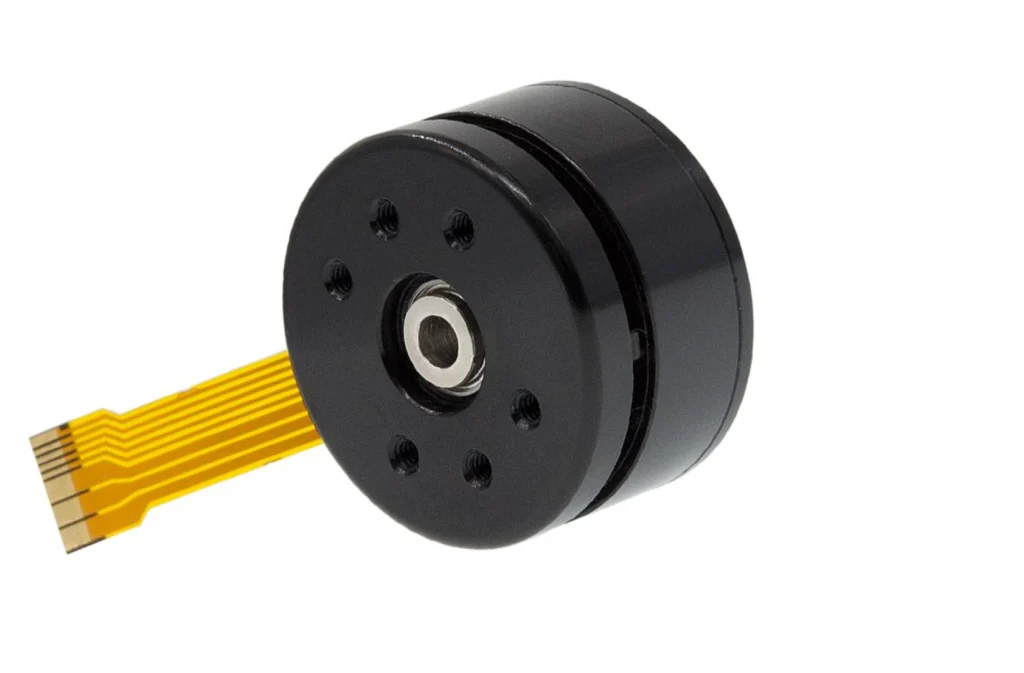
Table of Related Information:
Feature | Specification/Requirement |
Parts Processing | Precision CNC Turning, Milling, Grinding |
Processing Diameter | Varies based on motor size; Typically from 10mm to 200mm+ |
Shaft Material | High-strength Steel (e.g., 4140, 1045), Stainless Steel |
Stator Material | Electrical Steel Laminations |
Rotor Magnet Material | Neodymium (NdFeB), Samarium Cobalt (SmCo) |
Surface Finish (Shaft) | Ra 0.4 µm or better (Ground Finish) |
Shaft Straightness | Typically within 0.01mm per 100mm of shaft length |
Dimensional Tolerances | +/- 0.01mm for critical dimensions |
Testing | Electrical performance, mechanical vibration, thermal behavior, insulation resistance |
Inspection | Visual inspection, dimensional verification using CMM (Coordinate Measuring Machine), performance testing |
Welleshaft: Your Trusted Global Supplier and Contract Manufacturer
When sourcing hollow bore brushless motors for robotics and automation applications, it is essential to partner with a reliable and experienced supplier. Welleshaft stands out as a trusted global supplier and contract manufacturer, offering a comprehensive range of solutions to meet your specific needs.
Why Choose Welleshaft?
Extensive Expertise: Welleshaft possesses extensive expertise in the design, manufacturing, and testing of hollow bore brushless motors.
Advanced Manufacturing Facilities: Welleshaft operates state-of-the-art manufacturing facilities equipped with advanced CNC machining equipment and quality control systems.
Custom Solutions: Welleshaft offers custom design and manufacturing services to meet unique application requirements.
High-Quality Products: Welleshaft is committed to providing high-quality products that meet the highest standards of performance and reliability.
Global Reach: Welleshaft has a global presence, enabling them to serve customers worldwide efficiently and effectively.
Competitive Pricing: Welleshaft offers competitive pricing without compromising on quality or performance.
Whether you need standard hollow bore brushless motors or custom solutions tailored to your specific needs, Welleshaft can provide the expertise, resources, and support you need to succeed. Their commitment to quality, innovation, and customer satisfaction makes them a valuable partner for any robotics or automation project.
Conclusion
Hollow bore brushless motors are essential components in modern robotics and automation systems. Their unique design offers several advantages, including integrated routing, compact design, enhanced performance, and reduced maintenance. By carefully considering manufacturing considerations and partnering with a reliable supplier like Welleshaft, you can ensure that your robotics and automation projects benefit from the superior performance and reliability of hollow bore brushless motors. The future of both Robotics & Automation relies on further innovations of key components like the hollow bore brushless motor. As these motors continue to evolve, they will become even more integral to pushing the boundaries of what is possible in both sectors.