Electric Motor Hollow Shaft: High Torque, Precise Control, and Easy Integration
Electric motors are the backbone of countless applications, from industrial machinery to consumer electronics. While traditional solid-shaft motors have served us well, the demand for greater flexibility and functionality has led to the development of specialized designs. Among these, the electric motor hollow shaft stands out for its unique advantages, offering a powerful combination of high torque, precise control, and easy integration.
What is a Hollow Shaft Electric Motor?
A hollow shaft electric motor is characterized by a central bore that runs entirely through the motor shaft. This design allows various elements, such as cables, fluids, or other mechanical components, to pass directly through the motor’s center, opening up a wealth of possibilities for innovative and streamlined designs. It is also called Through-Bore Motor or Hollow-Bore Motor.
Key Advantages of Hollow Shaft Electric Motors
The adoption of hollow shaft electric motors is driven by a compelling set of benefits:
Simplified Design and Integration: The through-bore design significantly simplifies system architecture. Instead of routing cables or fluids around the motor, they can pass directly through it. This reduces complexity, minimizes potential entanglement or interference, and allows for more compact and efficient system layouts.
High Torque and Precision: Hollow shaft motors are designed to deliver high torque output, making them suitable for demanding applications. Furthermore, they can be integrated with encoders and control systems for precise positioning and speed control, which is critical in robotics, automation, and medical equipment.
Improved System Reliability: By streamlining the passage of cables and fluids, hollow shaft motors can reduce the risk of wear, tear, and damage. This enhances system reliability and minimizes downtime, ultimately lowering maintenance costs.
Enhanced Design Flexibility: The ability to pass components through the motor shaft grants designers greater freedom to create innovative and space-saving solutions. This is especially valuable in applications where space is limited, such as in robotic joints or compact machinery.
Direct Drive Capability: Many hollow shaft motors can be configured for direct drive applications, eliminating the need for gears or belts. This further simplifies the system, reduces mechanical losses, and improves overall efficiency.
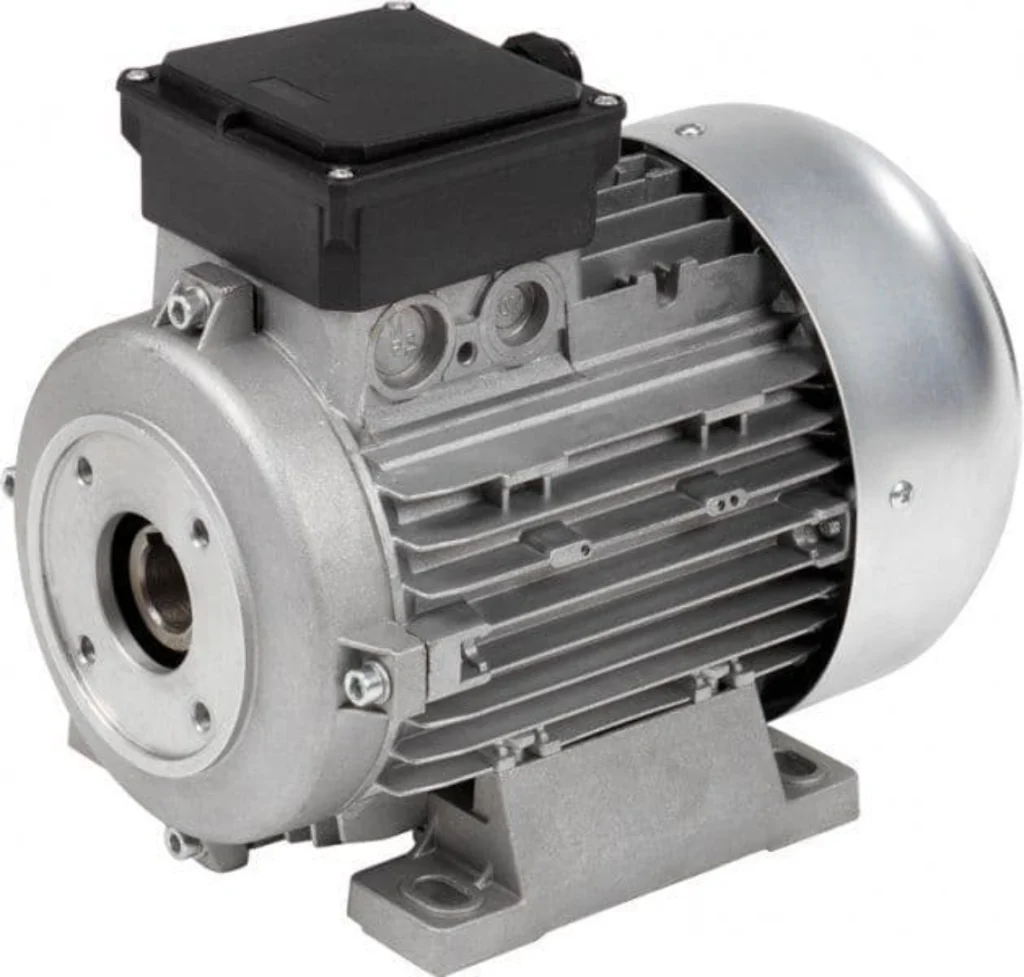
Applications of Hollow Shaft Electric Motors
The versatility of hollow shaft motors has led to their widespread adoption in various industries:
Robotics: Hollow shaft motors are ideal for robotic joints, allowing cables and hoses to pass through the arm, enabling flexible and uninhibited movement.
Automation: They are used in automated assembly lines, packaging machines, and material handling systems, providing precise control and simplifying integration.
Medical Equipment: Hollow shaft motors find application in medical devices, such as surgical robots and diagnostic equipment, where space constraints and precision are paramount.
Semiconductor Manufacturing: These motors are used in semiconductor fabrication equipment, providing accurate positioning and control in critical processes.
Printing and Packaging: Hollow shaft motors enable precise web tension control and material handling in printing and packaging machinery.
Turntables & Rotary Stages: Hollow shaft motors can be easily integrated into rotary stages or turntables. The hollow shaft allows for the passage of vacuum lines, compressed air, or electrical slip rings.
Parts Processing, Materials and Surface Finish for Hollow Shaft Motors
The manufacturing of hollow shaft motors requires precision machining and careful material selection to ensure optimal performance and durability.
Parameter | Details |
Parts Processing | CNC machining, turning, milling, grinding, honing, drilling, EDM (Electrical Discharge Machining), wire cutting. |
Processing Range Diameter | Typically from a few millimeters to several hundred millimeters (e.g., ø5mm to ø500mm), depending on the motor size and application. |
Material | Steel (e.g., carbon steel, alloy steel, stainless steel), aluminum, copper alloys, composites (for specific components). |
Surface Finish | Varies based on part and function: smooth, ground surfaces for bearings and seals; anodized for corrosion resistance; plating, painting. |
Parts Size Specifications | Tailored to specific motor designs; can range from miniature components to larger structural elements. |
Samples & Small Batch Production | Ideal for prototyping and customized applications. Flexibility in materials and design. |
Test Processing Ability | Inspection of machining accuracy by third party to ensure the quality. |
Through Check Rules | Strict adherence to engineering drawings, GD&T (Geometric Dimensioning and Tolerancing), and quality control standards. |
Straightness | High degree of straightness is critical, which can be achieved by centerless grinding. |
Manufacturing | High precision, with tight tolerances. |
Manufactur | Experienced machinists, CNC operators, and quality control personnel. |
Factory | Fully equipped with modern CNC machining centers, grinding machines, inspection equipment, and testing facilities. |
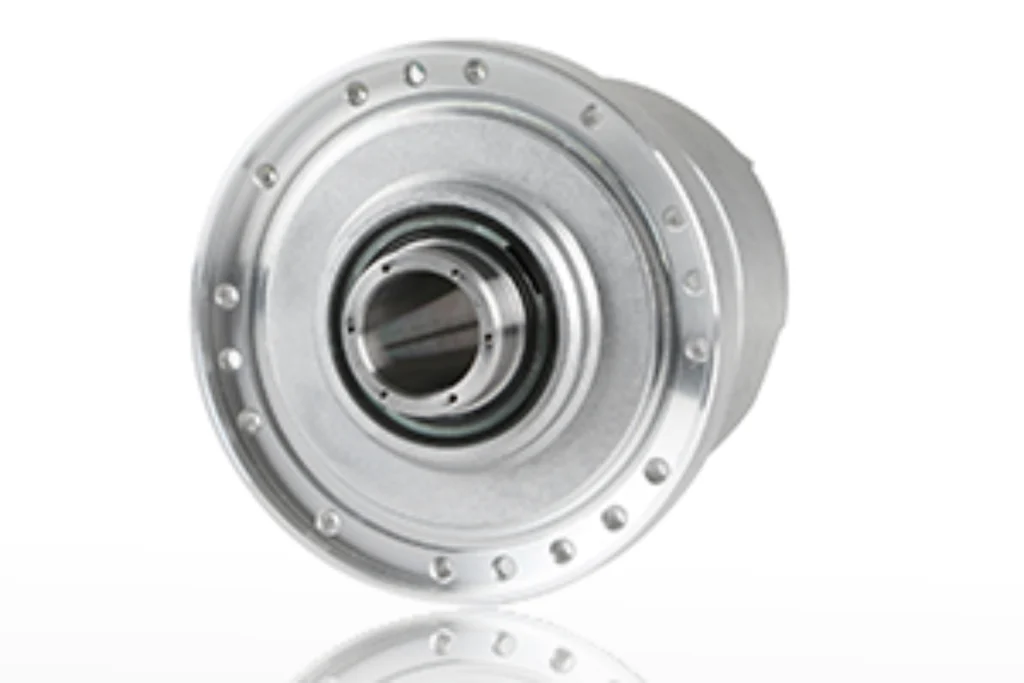
Key Manufacturing Considerations
Material Selection: The choice of materials depends on the application and operating environment. High-strength steels are often used for the shaft to withstand torsional stress, while aluminum can be used for housing components to reduce weight.
Precision Machining: Hollow shafts require tight tolerances and accurate machining to ensure smooth operation and minimize vibration. CNC machining is essential for achieving the required precision.
Surface Treatment: Surface treatments, such as hardening, coating, and plating, are applied to enhance wear resistance, corrosion protection, and overall durability.
Balancing: Dynamic balancing is critical to minimize vibration and ensure smooth operation, especially at high speeds.
Quality Control: Rigorous quality control procedures are implemented throughout the manufacturing process to ensure that each motor meets the required specifications.
Why Choose Welleshaft as Your Trusted Partner?
When it comes to sourcing high-quality electric motor hollow shafts, Welleshaft stands out as a reliable global supplier and contract manufacturer. With a proven track record of excellence and a commitment to customer satisfaction, Welleshaft offers a compelling combination of expertise, capabilities, and value.
Here’s why Welleshaft is the right choice:
Extensive Experience: Welleshaft has years of experience in manufacturing precision components for electric motors, including hollow shafts. Their team of engineers and machinists possesses in-depth knowledge of the specific requirements of these components.
Advanced Manufacturing Capabilities: Welleshaft operates state-of-the-art manufacturing facilities equipped with advanced CNC machining centers, grinding machines, and inspection equipment. This allows them to produce hollow shafts with exceptional accuracy and consistency.
Material Expertise: Welleshaft has extensive experience working with a wide range of materials, including steel, aluminum, copper, and composites. They can help you select the optimal material for your application and ensure that it meets the required performance characteristics.
Quality Assurance: Welleshaft is committed to maintaining the highest standards of quality. Their quality control processes are meticulously designed to ensure that every hollow shaft meets or exceeds your expectations.
Customization Options: Welleshaft offers a wide range of customization options to meet your specific needs. They can tailor the dimensions, materials, surface treatments, and other characteristics of the hollow shaft to match your application requirements.
Competitive Pricing: Welleshaft is committed to providing competitive pricing without compromising on quality. They work closely with their customers to develop cost-effective solutions that meet their budget requirements.
Global Reach: With a global network of partners and distributors, Welleshaft can efficiently serve customers around the world. They offer reliable shipping and logistics services to ensure that your products arrive on time and in perfect condition.
Conclusion
Electric motor hollow shafts offer a unique combination of high torque, precise control, and easy integration, making them ideal for a wide range of applications. By understanding the advantages and manufacturing considerations of these motors, you can make informed decisions and select the right solution for your needs. And with Welleshaft as your trusted partner, you can be confident that you’re getting high-quality hollow shafts that meet your exact specifications. Whether you need standard components or custom designs, Welleshaft has the expertise and capabilities to deliver the solutions you need to succeed.