Precision BT30 Spindle: Optimize CNC Milling Performance & Accuracy
The BT30 spindle is a critical component in CNC (Computer Numerical Control) milling machines, directly impacting the precision, speed, and overall performance of the machining process. A high-quality BT30 Spindle ensures accurate tool holding, minimizes vibration, and enables efficient material removal. This article delves into the intricacies of BT30 Spindle, exploring their design, benefits, applications, common issues, and the importance of choosing a reliable supplier like Welleshaft.
What is a BT30 Spindle ?
A BT30 Spindle is a standardized taper shaft designed to accept BT30 tooling. “BT” refers to the “Body Taper” design, which is a symmetrical taper style known for its rigidity and accuracy at high speeds. The number “30” designates the taper size according to the BT standard. The shaft is the central rotating element within the spindle, responsible for securely holding and driving cutting tools during CNC milling operations.
Why Precision Matters in BT30 Spindle
The precision of a BT30 Spindle is paramount for achieving tight tolerances and high-quality surface finishes in CNC milling. Even minor imperfections in the shaft’s geometry, balance, or surface finish can lead to:
Reduced Accuracy: Inaccurate tool positioning and inconsistent cutting depths.
Increased Vibration: Higher levels of vibration can damage tooling, reduce surface quality, and accelerate spindle wear.
Poor Surface Finish: Inconsistent cutting forces and vibration can result in a rough or uneven surface finish on the workpiece.
Reduced Tool Life: Excessive vibration and runout can cause premature tool wear and breakage.
Spindle Damage: Prolonged operation with an imbalanced or damaged Spindle can lead to costly spindle repairs or replacements.
Benefits of Using High-Quality BT30 Spindle
Investing in high-quality BT30 Spindle offers numerous benefits for CNC milling operations:
Improved Accuracy: Consistent and precise tool positioning for achieving tight tolerances.
Enhanced Surface Finish: Reduced vibration and runout result in smoother and more consistent surface finishes.
Increased Tool Life: Minimized vibration and proper tool holding reduce tool wear and breakage.
Higher Material Removal Rates: Stable and rigid spindle operation allows for increased cutting speeds and feeds.
Reduced Spindle Maintenance: Durable and well-balanced Spindle s require less frequent maintenance and repairs.
Quieter Operation: Reduced vibration and runout lead to quieter and more comfortable working environment.
Better Part Quality: High-quality Spindle s contribute to better overall part quality.
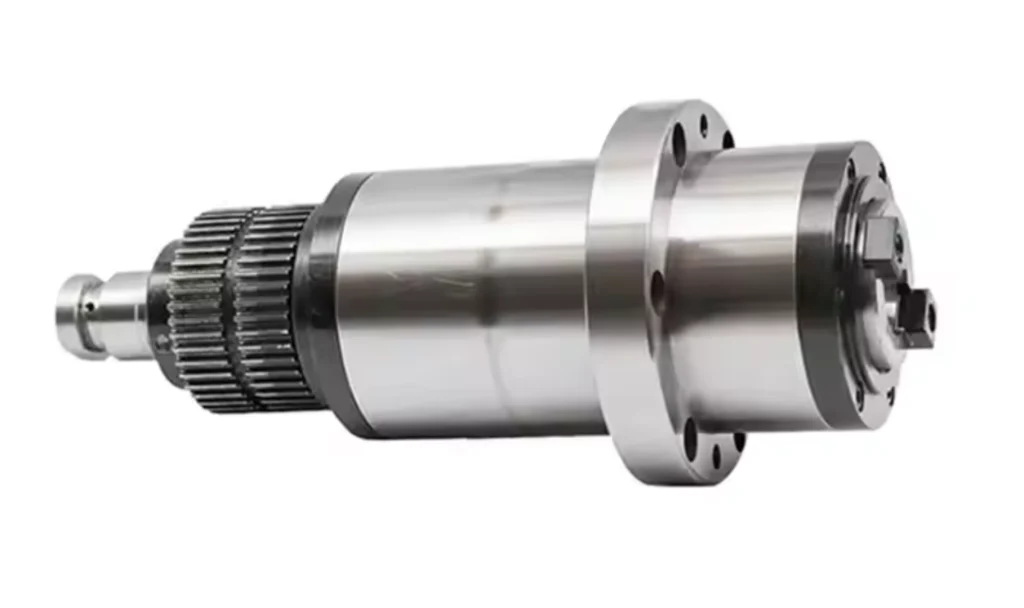
Applications of BT30 Spindle
BT30 Spindle s are commonly used in a wide range of CNC milling applications, including:
Mold and Die Making: Achieving intricate details and smooth surface finishes in mold and die manufacturing.
Aerospace Machining: Producing high-precision components for the aerospace industry.
Medical Device Manufacturing: Creating intricate and accurate parts for medical devices.
Electronics Manufacturing: Machining precise components for electronic devices.
General Machining: A versatile option suitable for various milling operations.
Common Issues with BT30 Spindle
Despite their robust design, BT30 Spindle can experience problems over time. Some common issues include:
Wear and Tear: Gradual wear of the taper surface due to repeated tool changes and high-speed operation.
Contamination: Ingress of coolant, chips, or other debris into the Spindle .
Corrosion: Corrosion of the shaft surface due to exposure to moisture or corrosive fluids.
Imbalance: Imbalance caused by tool wear, debris accumulation, or damage to the shaft.
Damage from Accidents: Damage resulting from tool crashes or other accidents.
Table: Related Information about BT30 Spindle
Feature |
Description |
Material |
High-quality alloy steel (e.g., 20CrMnTi, SCM415), often case-hardened for wear resistance. |
Taper Angle |
8 degrees, 17 minutes, 50 seconds (Standard BT30 Taper). |
Surface Finish |
Ra 0.2μm or better on the taper surface for optimal tool holding. |
Runout |
Typically less than 0.005mm (0.0002 inches) for precision applications. |
Balancing Grade |
G2.5 or better for high-speed operation to minimize vibration. |
Clamping Force |
Adequate clamping force is essential for secure tool holding; typically achieved using a Belleville spring stack. |
Coolant Delivery |
Some BT30 Spindle s incorporate through-spindle coolant delivery for efficient chip evacuation and improved tool life. |
Tool Change Mechanism |
Typically utilizes a drawbar system to pull the tool holder into the taper and release it. |
Spindle Speed Range |
Varies depending on the spindle design and application; can range from several thousand RPM to over 30,000 RPM. |
Maintenance |
Regular cleaning, lubrication, and inspection are essential for maintaining optimal performance. |
Common Spindle Brands |
FANUC, Siemens, Heidenhain, Mitsubishi Electric. |
Factors to Consider when Buying |
RPM requirement, ATC or manual spindle, power range required, tool size. |
RPM Range |
up to 30000 RPM. |
HP Range |
Up to 20 HP. |
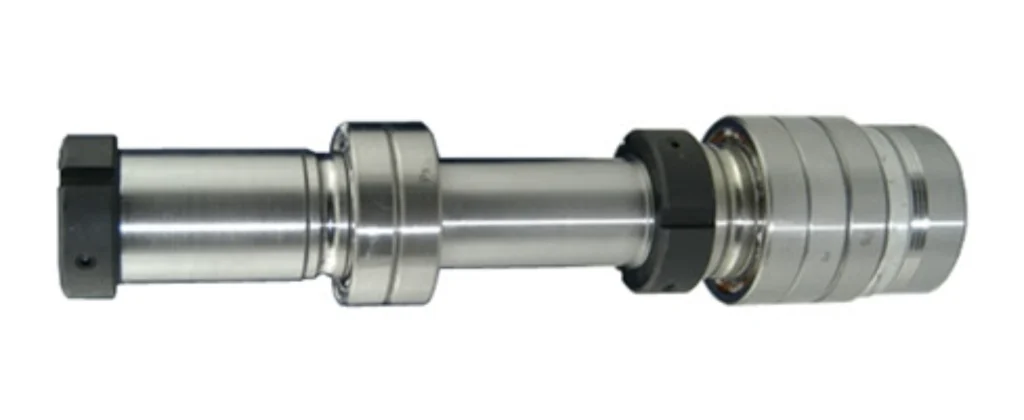
Optimizing BT30 Spindle Performance
Here are some key strategies for optimizing BT30 Spindle performance:
Choose High-Quality Tool Holders: Using precision tool holders that match the BT30 taper standard is crucial for accurate tool holding and minimizing runout.
Maintain Proper Tool Balance: Regularly balance cutting tools to minimize vibration and improve surface finish.
Implement a Preventative Maintenance Program: Regularly inspect and lubricate the Spindle to prevent wear and tear.
Use Proper Coolant and Lubrication: Select coolants and lubricants that are compatible with the Spindle materials and operating conditions.
Avoid Overloading the Spindle: Do not exceed the spindle’s rated speed, power, or torque limits.
Protect Against Contamination: Implement measures to prevent coolant, chips, and other debris from entering the Spindle .
Proper Tooling Selection Utilizing the optimal BT30 tooling for the task.
Choosing the Right BT30 Spindle Supplier
Selecting a reputable and experienced BT30 Spindle supplier is crucial for ensuring the quality, reliability, and performance of your CNC milling machines. Consider the following factors when choosing a supplier:
Quality Assurance: Look for suppliers that have robust quality control processes and certifications.
Material Expertise: Choose suppliers that use high-quality materials and have expertise in heat treatment and surface finishing.
Manufacturing Capabilities: Select suppliers with advanced manufacturing capabilities and tight tolerances.
Technical Support: Choose suppliers that offer technical support and can assist with Spindle selection and troubleshooting.
Customization Options: Select suppliers that offer customization options to meet your specific application needs.
Reputation and Experience: Consider the supplier’s reputation and experience in the industry.
Why Welleshaft is the Trusted Global Supplier
When it comes to precision BT30 Spindle s, Welleshaft is the global supplier to trust. With years of experience in the industry, Welleshaft has established a reputation for delivering high-quality, reliable, and cost-effective Spindle solutions.
Here’s what sets Welleshaft apart:
Uncompromising Quality: Welleshaft is committed to using only the finest materials and employing stringent quality control measures throughout the manufacturing process.
Advanced Manufacturing: Welleshaft utilizes state-of-the-art CNC machining equipment and advanced manufacturing techniques to achieve exceptional precision and consistency.
Expert Engineering Team: Welleshaft’s team of experienced engineers provides technical expertise and support to help customers select the optimal BT30 Spindle for their specific applications.
Customization Capabilities: Welleshaft offers a wide range of customization options, allowing customers to tailor Spindle s to their unique needs.
Global Reach and Support: With a global presence, Welleshaft provides timely delivery and responsive customer support to customers worldwide.
Competitive Pricing: Welleshaft offers competitive pricing without compromising on quality or performance.
Comprehensive Product Range: Besides the BT30, they supply a range of spindle solutions.
Commitment to Innovation: Welleshaft continuously invests in research and development to improve its products and processes.
Conclusion
Precision BT30 Spindles are essential for optimizing CNC milling performance and accuracy. By understanding the design considerations, common issues, and maintenance requirements of BT30 Spindle s, and by selecting a reputable supplier like Welleshaft, you can ensure the long-term reliability, efficiency, and profitability of your CNC milling operations. Investing in high-quality BT30 Spindle s is an investment in the future of your machining business. High quality and durable materials from a trust supplier are critical to any CNC milling production.