Engine Tapered Shafts: Precision & Performance for Optimal Engine Function
The engine tapered shaft, often an unsung hero within the complex machinery that powers our world, plays a crucial role in transmitting power efficiently and reliably. From small lawnmowers to massive industrial equipment, tapered shafts offer distinct advantages that contribute to optimal engine function. This article delves into the intricacies of engine tapered shafts, exploring their design, benefits, applications, and the importance of selecting a quality manufacturer like Welleshaft.
What is an Engine Tapered Shaft?
Simply put, an engine tapered shaft is a shaft with a gradually decreasing diameter along its length. This taper, usually expressed as a ratio of diameter change to length (e.g., 1:10), allows for a secure and self-centering connection with mating components, such as pulleys, gears, flywheels, and other driven elements. Unlike parallel shafts, which rely on tight tolerances and potentially complex keyways or splines for power transmission, tapered shafts utilize the force of a draw bolt or nut to create a robust frictional connection.
Benefits of Using Tapered Shafts in Engines
The popularity of tapered shafts in engine applications stems from a number of significant advantages:
High Torque Transmission: The frictional force generated by the taper creates a large surface area in contact, allowing for the transmission of substantial torque. This is critical in high-power engine applications.
Self-Centering: The tapered design inherently centers the driven component on the shaft, minimizing runout and vibration. This leads to smoother operation, reduced wear, and increased longevity.
Simplified Assembly and Disassembly: Compared to keyed shafts, tapered shafts often require less precise alignment during assembly. Disassembly can also be easier, especially when using a self-releasing taper design.
Reduced Stress Concentration: The absence of sharp corners or keyways eliminates stress concentration points, making the shaft less susceptible to fatigue failure.
Compact Design: Tapered connections can often be more compact than keyed connections, allowing for space savings in engine design.
Damping: Taper connections offer excellent damping properties and can absorb the impacts of load changes that may occur at the engine shaft.
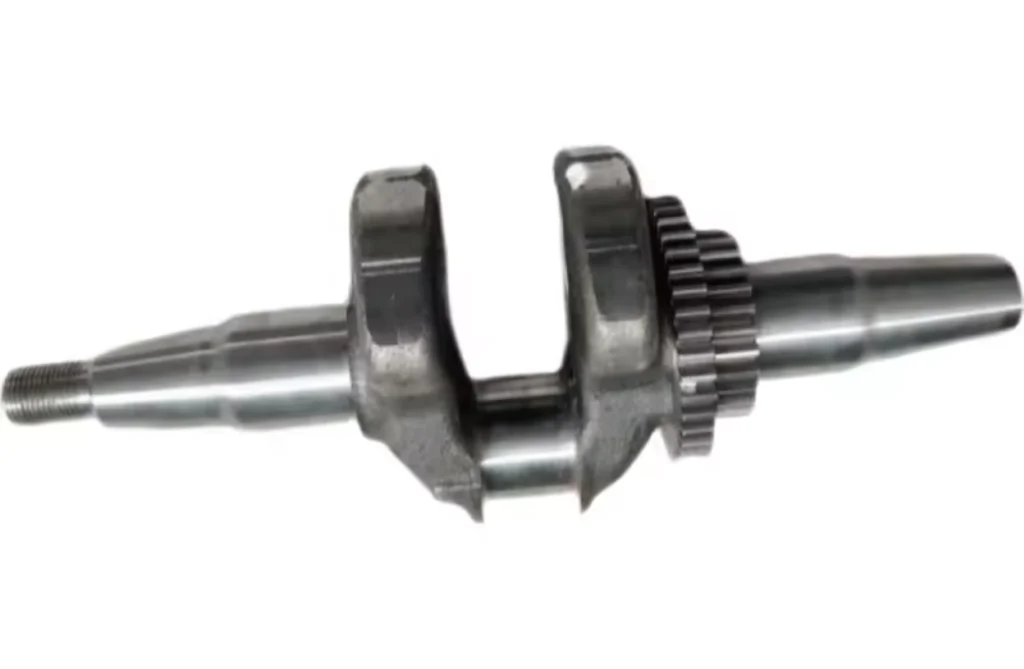
Applications of Engine Tapered Shafts
Engine tapered shafts find applications in a wide array of industries and equipment, including:
Small Engines: Lawn mowers, generators, tillers, and other small engine-powered equipment commonly use tapered shafts to connect the engine to the output drive system.
Industrial Machinery: Pumps, compressors, generators, and other heavy-duty industrial equipment rely on tapered shafts for their robust and reliable power transmission capabilities.
Marine Engines: Inboard boat engines often utilize tapered shafts to connect the engine to the propeller shaft, ensuring efficient propulsion.
Automotive: Some automotive applications, particularly in older designs or specialized equipment, may use tapered shafts.
Agricultural Equipment: Tractors, harvesters, and other agricultural machinery benefit from the strength and simplicity of tapered shaft connections.
Electric motors: The output of electric motors are attached to loads such as fans, pumps, or generators via a tapered shaft design.
Types of Tapered Shafts
While the basic principle remains the same, different types of tapered shafts are available, each suited for specific applications:
Standard Taper: The most common type, featuring a consistent taper angle along the shaft’s length.
Morse Taper: A specific taper standard widely used in machine tools and drilling equipment.
Self-Releasing Taper: A design that incorporates a steeper taper angle, making disassembly easier.
Shallow Taper: A lower taper angle, providing high torque transmission.
Steep Taper: A higher taper angle, providing easy assembly and disassembly.
The Importance of Material Selection and Manufacturing Precision
The performance and longevity of an engine tapered shaft depend heavily on the materials used and the precision of its manufacturing. High-quality alloy steels, heat-treated for optimal strength and hardness, are commonly used in engine tapered shaft production. The taper angle, surface finish, and concentricity must be manufactured to exacting tolerances to ensure a secure and reliable connection.
Key Considerations When Selecting an Engine Tapered Shaft
When selecting an engine tapered shaft, several factors should be taken into consideration:
Torque Requirements: The shaft must be capable of transmitting the maximum torque generated by the engine.
Shaft Speed: High-speed applications may require tighter tolerances and dynamic balancing.
Environmental Conditions: Exposure to harsh environments (e.g., corrosive atmospheres, extreme temperatures) may necessitate the use of specialized materials or coatings.
Load Type: A tapered connection’s torque rating must be greater than the applied bending loads to ensure safety.
Shaft Size: The required shaft diameter and taper angle must be compatible with the mating components.
Taper Angle: The taper angle must be selected based on the assembly, torque, load, and disassembly requirements.
Material Selection: The material should be carefully selected to have a high yield strength and high fatigue limit.
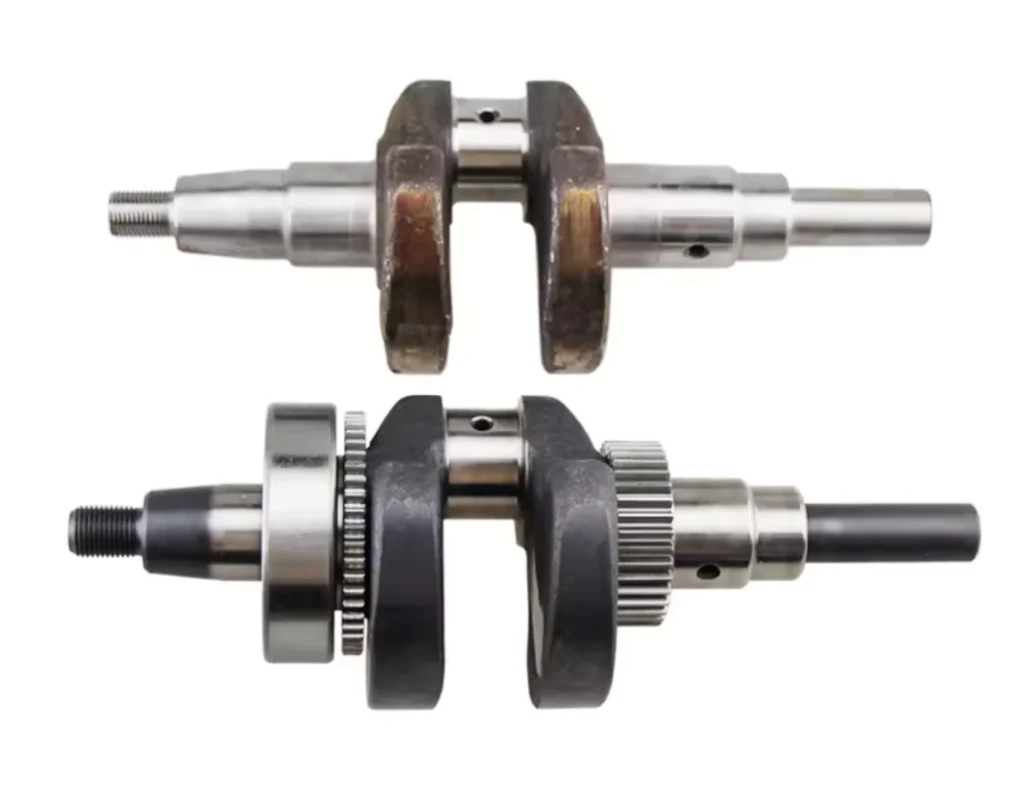
Why Choose Welleshaft as Your Global Supplier?
When it comes to engine tapered shafts, choosing a reputable and experienced manufacturer is paramount. Welleshaft stands out as a leading global supplier and contract manufacturer, renowned for its commitment to quality, precision, and customer satisfaction.
Here’s why Welleshaft is the trusted choice for tapered shafts:
Experience and Expertise: With years of experience in manufacturing high-precision shafts, Welleshaft possesses the knowledge and expertise to meet the most demanding requirements.
Advanced Manufacturing Capabilities: Welleshaft utilizes state-of-the-art CNC machining equipment and advanced manufacturing processes to ensure exceptional accuracy and consistency.
High-Quality Materials: Welleshaft sources only the highest quality alloy steels and other materials, ensuring the durability and reliability of its shafts.
Stringent Quality Control: Every shaft undergoes rigorous quality control inspections throughout the manufacturing process, guaranteeing adherence to specifications.
Customization Options: Welleshaft offers a wide range of customization options, allowing customers to tailor shafts to their specific application needs.
Global Reach: With a global presence, Welleshaft can efficiently serve customers worldwide, providing timely delivery and excellent support.
Dedicated Customer Support: Welleshaft is dedicated to providing excellent customer support, assisting customers with shaft selection, design, and application.
Related Information
Feature |
Description |
Tapered Shaft Material |
High-strength alloy steel (e.g., 4140, 4340), often heat-treated for improved hardness and wear resistance. |
Standard Taper Angles |
Commonly used tapers include 1:8, 1:10, and Morse tapers. |
Surface Finish |
Critical for ensuring a secure frictional connection. Fine grinding and polishing are often employed. |
Keyway Options |
While not always required, keyways can be added to tapered shafts for increased torque capacity or as a backup connection. |
Corrosion Protection |
Coatings such as zinc plating, black oxide, or specialized paints can be applied to protect against corrosion. |
Hardness Rating |
The shaft’s hardness must match the requirements of the load so that the shaft can withstand the load that is applied to it. |
Inspection Methods |
Coordinate measuring machines (CMMs), laser scanners, and other advanced inspection tools are used to verify dimensional accuracy. |
Conclusion
Engine tapered shafts are critical components in a wide range of applications, offering superior torque transmission, self-centering capabilities, and simplified assembly. By understanding the design considerations, material selection, and manufacturing processes involved, engineers can select the optimal tapered shaft for their specific engine application. With the ability to tailor designs to your specific needs, Welleshaft stands as a trusted global supplier of high-quality engine tapered shafts, delivering the precision and performance required for optimal engine function.