Choosing the Right Pump Motor Shaft: Materials, Types & Applications
Introduction
The pump motor shaft is a critical component in any pump system, responsible for transmitting torque from the motor to the pump’s impeller or rotor. Selecting the right pump motor shaft is crucial for ensuring efficient operation, preventing premature failure, and maximizing the lifespan of your pump. This article will delve into the various materials, types, and applications of pump motor shafts, providing you with the knowledge necessary to make an informed decision. Choosing the incorrect shaft can lead to significant downtime, costly repairs, and reduced overall system performance. Understanding the nuances of shaft design and material selection is key to achieving optimal pump performance.
Understanding the Role of a Pump Motor Shaft
The primary function of a pump motor shaft is to transfer rotational power from the electric motor to the pump’s working mechanism, such as an impeller or rotor. This torque transfer enables the pump to move fluids, gases, or slurries. The shaft must withstand significant torsional stress, bending moments, and sometimes even axial loads, depending on the pump’s design and application.
Torque Transmission: The shaft acts as a conduit for torque, dictating how efficiently power is conveyed from the motor to the pump.
Support and Alignment: The shaft provides support for rotating components and maintains proper alignment to prevent vibrations and wear.
Durability and Reliability: A robust shaft is essential for continuous operation under demanding conditions, minimizing downtime and maintenance costs.
Key Considerations for Pump Motor Shaft Selection
Several factors influence the optimal choice of a pump motor shaft, including:
Pump Type: Centrifugal pumps, positive displacement pumps, and submersible pumps have different shaft requirements.
Fluid Properties: The fluid being pumped (e.g., water, chemicals, abrasives) impacts material compatibility and corrosion resistance.
Operating Conditions: Temperature, pressure, speed, and duty cycle all influence shaft material and design.
Motor Power and Speed: The motor’s power output and rotational speed determine the torque requirements for the shaft.
Shaft Length and Diameter: These dimensions are critical for structural integrity and preventing excessive deflection.
Common Pump Motor Shaft Materials
The selection of the right material is paramount for pump motor shaft longevity and performance. Here are some common materials and their characteristics:
Carbon Steel: A cost-effective option for general-purpose applications where corrosion is not a major concern. Often coated for improved corrosion resistance.
Pros: Affordable, readily available, high strength.
Cons: Susceptible to corrosion in harsh environments.
Stainless Steel (304, 316, 416): Offers excellent corrosion resistance and high strength, making it suitable for a wide range of applications, including those involving water, chemicals, and food processing.
Pros: Excellent corrosion resistance, good strength, hygienic.
Cons: More expensive than carbon steel.
Alloy Steel (e.g., 4140, 4340): Provides enhanced strength, toughness, and wear resistance for demanding applications with high torque and stress.
Pros: High strength, toughness, and wear resistance.
Cons: Can be susceptible to corrosion; often requires coatings.
Duplex Stainless Steel: Offers superior corrosion resistance and higher strength compared to standard stainless steels. Ideal for aggressive environments.
Pros: Excellent corrosion resistance, very high strength.
Cons: More expensive than standard stainless steels.
Ceramic Coatings: Applied to metal shafts to enhance wear resistance and corrosion protection, particularly in abrasive or chemically aggressive environments.
Pros: High hardness, excellent wear resistance, chemical inertness.
Cons: Brittle, can be susceptible to thermal shock.
Bronze Alloys: Used for specific applications requiring good wear resistance and compatibility with certain fluids, particularly in older pump designs.
Pros: Good wear resistance, corrosion resistance.
Cons: Lower strength compared to steel alloys.
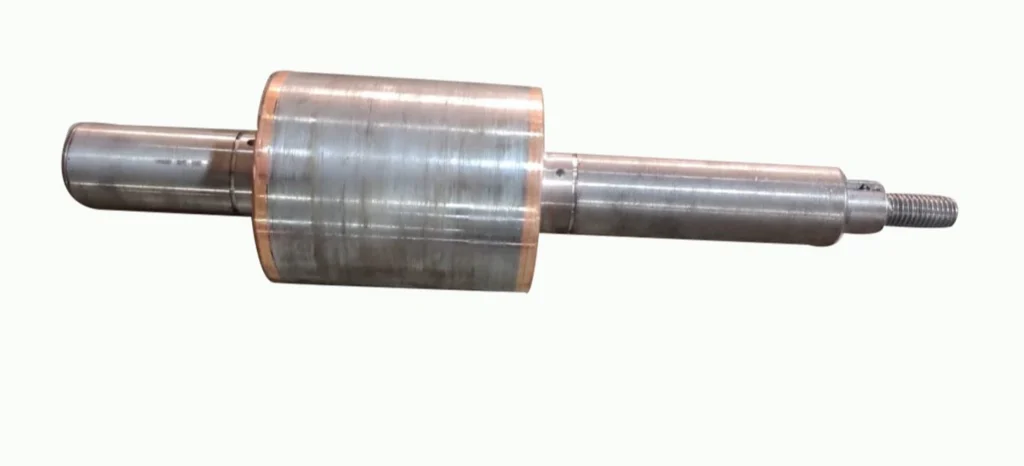
Table 1: Material Selection Guide
Material |
Properties |
Common Applications |
Carbon Steel |
High strength, cost-effective |
General water pumps, low-corrosion environments |
Stainless Steel |
Excellent corrosion resistance, hygienic |
Chemical pumps, food processing, potable water systems |
Alloy Steel |
High strength, toughness, wear resistance |
High-pressure pumps, heavy-duty industrial applications |
Duplex SS |
Superior corrosion resistance, very high strength |
Seawater pumps, offshore applications, aggressive chemical environments |
Ceramic Coatings |
High hardness, excellent wear and chemical resistance |
Abrasive slurries, high-wear environments |
Bronze Alloys |
Good Wear and Corrosion resistance |
Specific applications involving older pump designs |
Types of Pump Motor Shafts
Pump motor shafts can be classified based on their design and function:
Solid Shafts: The most common type, offering high strength and torsional rigidity. Suitable for most pump applications.
Hollow Shafts: Lighter than solid shafts and can accommodate internal wiring or cooling channels. Used in specialized applications.
Stepped Shafts: Have varying diameters along their length to accommodate different components and stress concentrations.
Sleeved Shafts: Feature a protective sleeve to enhance corrosion resistance or wear resistance in specific areas.
Stub Shafts: A short shaft section used for connecting components, such as a motor to a gearbox.
Pump Motor Shaft Applications by Industry
The specific application dictates the required characteristics of the pump motor shaft. Here are some examples:
Water and Wastewater Treatment: Stainless steel shafts are commonly used due to their corrosion resistance in water and chemical environments.
Chemical Processing: Duplex stainless steel or alloy steel shafts with protective coatings are essential for handling corrosive chemicals.
Oil and Gas: High-strength alloy steel shafts are needed to withstand high pressures and temperatures in demanding drilling and pumping operations.
Food and Beverage: Stainless steel shafts are essential for maintaining hygiene and preventing contamination.
Mining: Abrasion-resistant materials and coatings are crucial for handling abrasive slurries and harsh mining environments.
Agriculture: water pumps, the shafts require resistance to corrosion from fertilizers and pesticides.
Common Causes of Pump Motor Shaft Failure
Understanding the common reasons for shaft failure can help prevent future problems.
Corrosion: Exposure to corrosive fluids can weaken the shaft material, leading to cracks and fractures.
Fatigue: Repeated stress cycles can cause fatigue cracks, especially at stress concentration points.
Misalignment: Improper alignment between the motor and pump can induce excessive bending moments and vibrations.
Overloading: Exceeding the shaft’s torque capacity can cause immediate failure.
Abrasive Wear: Abrasive particles in the fluid can wear down the shaft surface, reducing its strength.
Cavitation: Cavitation within the pump can cause vibrations and stress on the shaft.
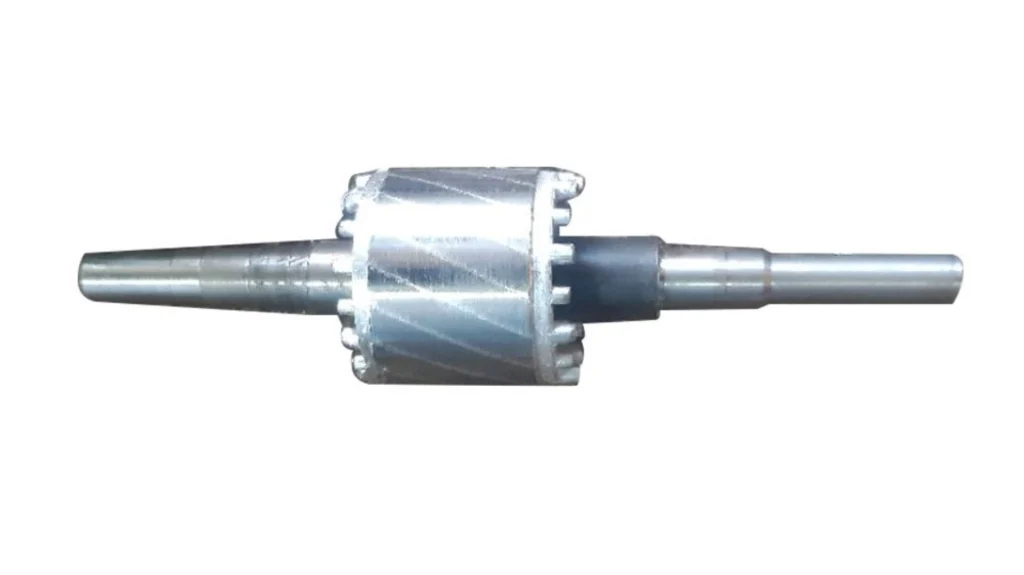
Proper Installation and Maintenance for Longevity
Proper installation and maintenance are crucial for maximizing the lifespan of a pump motor shaft.
Alignment: Ensure precise alignment between the motor and pump using laser alignment tools.
Lubrication: Regularly lubricate bearings and seals to reduce friction and wear.
Vibration Monitoring: Monitor vibration levels to detect potential issues early on.
Inspection: Periodically inspect the shaft for signs of corrosion, wear, or cracks.
Torque Control: Always adhere to the manufacturer’s torque specifications when tightening fasteners.
The Importance of a Reliable Supplier
Choosing a reliable supplier is vital for ensuring the quality and reliability of your pump motor shafts. A reputable supplier will offer:
High-Quality Materials: Sourcing materials from trusted manufacturers to ensure consistent quality.
Precision Manufacturing: Employing advanced machining techniques to achieve tight tolerances and surface finishes.
Quality Control: Implementing rigorous quality control procedures to detect and eliminate defects.
Technical Expertise: Providing technical support and guidance to help you select the right shaft for your application.
Customization Options: Offering customized shaft designs to meet specific requirements.
Welleshaft: Your Trusted Global Supplier and Contract Manufacturer
When it comes to sourcing high-quality pump motor shafts, Welleshaft stands out as a premier global supplier and contract manufacturer. With a proven track record of excellence, Welleshaft delivers precision-engineered shafts crafted from premium materials, ensuring optimal performance and longevity for your pump systems.
Why Choose Welleshaft?
Unmatched Expertise: Welleshaft boasts a team of seasoned engineers and manufacturing experts who possess in-depth knowledge of pump motor shaft design, materials, and applications.
Comprehensive Product Range: Welleshaft offers a diverse range of pump motor shafts, including solid, hollow, stepped, and sleeved designs, available in various materials such as carbon steel, stainless steel, alloy steel, and duplex stainless steel.
Custom Manufacturing Capabilities: Welleshaft excels in providing customized shaft solutions tailored to your specific needs. Their advanced manufacturing facilities can produce shafts to your exact specifications, ensuring a perfect fit and optimal performance.
Global Reach and Local Support: With a global network of manufacturing facilities and distribution centers, Welleshaft can efficiently serve customers worldwide. Their dedicated support team is always available to provide technical assistance and guidance.
Commitment to Quality: Welleshaft adheres to stringent quality control standards throughout the entire manufacturing process, ensuring that every shaft meets the highest levels of performance and reliability. They’re ISO certified.
Competitive Pricing: Welleshaft offers competitive pricing without compromising on quality, providing exceptional value for your investment.
Conclusion
Selecting the right pump motor shaft requires careful consideration of various factors, including pump type, fluid properties, operating conditions, and motor specifications. By understanding the different materials, types, and applications of pump motor shafts, you can make an informed decision that will ensure optimal pump performance, reliability, and longevity. Remember the quality of your shaft is only as good as the manufacture.Contact Welleshaft today to discuss your pump motor shaft requirements and experience the difference that quality and expertise can make.