Ceramic Pump Shafts for Demanding Applications | Chemical & Industrial
In the chemical and industrial sectors, pumping systems operate under incredibly demanding conditions. The materials used in these pumps must withstand corrosive chemicals, abrasive slurries, extreme temperatures, and high pressures. Traditional metal pump shafts often fall short, leading to frequent failures, costly downtime, and potential contamination. Ceramic pump shafts offer a superior solution, providing exceptional resistance to these challenges and ensuring reliable performance. This article will explore the benefits of ceramic pump shafts in chemical and industrial applications, highlighting their unique properties, common applications, and the advantages of choosing Welleshaft as your trusted supplier.
Understanding the Need for Specialized Pump Shafts
The heart of any pump is the shaft, which transmits rotational force from the motor to the impeller. In chemical and industrial settings, this shaft is constantly exposed to aggressive substances that can rapidly degrade metal components. Common challenges include:
Chemical Corrosion: Acids, bases, solvents, and other chemicals can corrode metal shafts, weakening them and leading to failure.
Abrasive Wear: Slurries containing abrasive particles can erode the shaft’s surface, reducing its diameter and strength.
High Temperatures: Elevated temperatures can accelerate corrosion and weaken the shaft’s material.
Seal Failure: Shaft damage can compromise the seals, leading to leaks and further contamination.
Down Time: All these problems culminate in equipment failure resulting in costly down time for manufacturing.
The Advantages of Ceramic Pump Shafts
Ceramic pump shafts offer a significant upgrade over traditional metal shafts in demanding chemical and industrial applications. Key advantages include:
Exceptional Corrosion Resistance: Ceramics are inherently resistant to a wide range of chemicals, including acids, bases, and solvents. They won’t corrode or degrade, even when exposed to highly aggressive substances.
Superior Abrasion Resistance: Ceramics are extremely hard and resistant to wear, making them ideal for handling abrasive slurries.
High-Temperature Stability: Ceramics can maintain their strength and integrity at elevated temperatures, where metals would weaken or fail.
Inertness and Purity: Ceramics are inert and won’t contaminate the pumped fluid, making them suitable for sensitive applications like food processing and pharmaceuticals.
Extended Service Life: The combination of corrosion resistance, abrasion resistance, and high-temperature stability results in a significantly longer service life compared to metal shafts, reducing maintenance costs and downtime.
Reduced Life Cycle Cost: Even with slightly higher upfront cost, the reduced downtime, longer lifespan, and minimal repairs make ceramic shafts cheaper over their entire life.
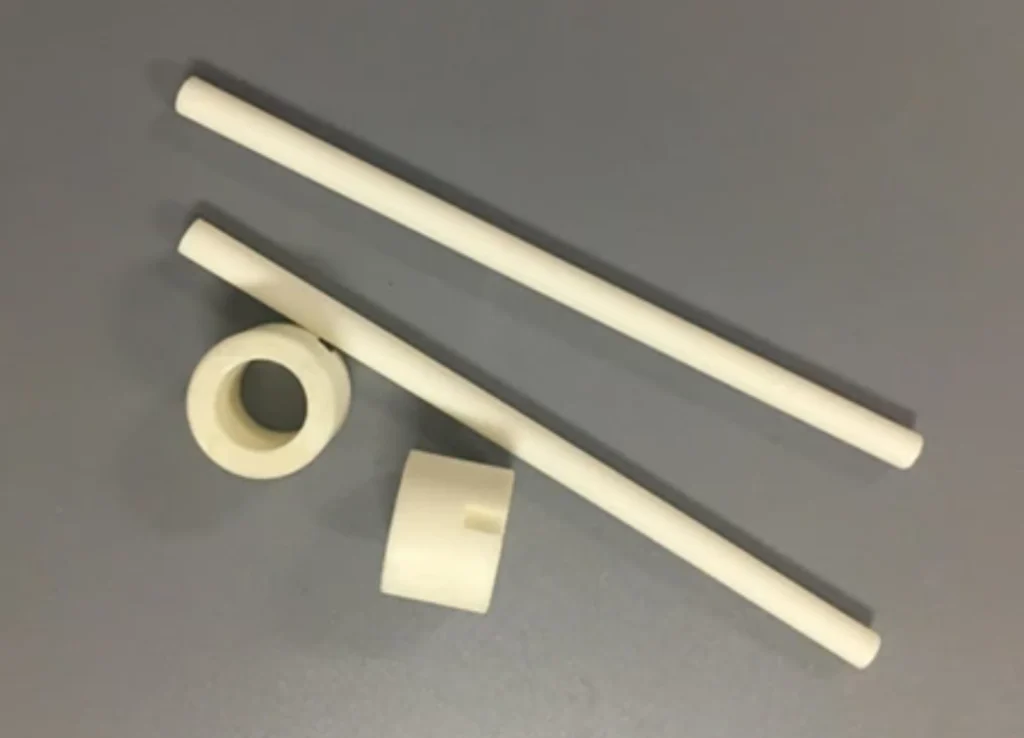
Common Ceramic Materials for Pump Shafts
Several ceramic materials are used in pump shaft construction, each with its own unique properties and advantages:
Alumina (Al2O3): A widely used ceramic material known for its high hardness, wear resistance, and chemical inertness. Suitable for a broad range of applications.
Zirconia (ZrO2): Offers higher strength and toughness compared to alumina, making it ideal for applications where impact resistance is important.
Silicon Carbide (SiC): Exhibits exceptional hardness, abrasion resistance, and high-temperature stability. Suitable for extremely demanding applications.
Advanced Ceramics: There are specialty advanced ceramic materials that provide unique attributes such as extreme temperature resistance, high chemical resistance, or exceptional hardness. Selecting the right ceramic for a particular application can dramatically improve shaft life and pump performance.
Applications in the Chemical and Industrial Sectors
Ceramic pump shafts find widespread use in various chemical and industrial applications, including:
Chemical Processing: Handling corrosive chemicals in reactors, storage tanks, and transfer lines.
Industrial Wastewater Treatment: Pumping abrasive slurries and corrosive effluents.
Pharmaceutical Manufacturing: Ensuring purity and preventing contamination in sensitive processes.
Mining and Mineral Processing: Handling abrasive slurries and corrosive leaching solutions.
Power Generation: Pumping cooling water and handling corrosive flue gas desulfurization (FGD) slurries.
Pulp and Paper Manufacturing: Handling abrasive pulp slurries and corrosive bleaching chemicals.
Slurry Pumps: These require a more robust shaft, with higher resistance to abrasion.
Table: Ceramic Pump Shaft Material Selection Guide
Material | Key Properties | Suitable Applications | Chemical Resistance | Abrasion Resistance | Temperature Resistance | Cost |
Alumina (Al2O3) | High hardness, good wear resistance, chemical inertness | General chemical processing, water treatment, pharmaceuticals | Excellent | Good | Good | Moderate |
Zirconia (ZrO2) | High strength, high toughness, good wear resistance | Slurry pumps, applications with high impact loads, abrasive environments | Excellent | Very Good | Moderate | High |
Silicon Carbide (SiC) | Exceptional hardness, excellent abrasion resistance, high-temperature stability, good chemical resistance | Extremely abrasive slurries, high-temperature applications, corrosive environments | Excellent | Excellent | Excellent | Very High |
Design Considerations for Ceramic Pump Shafts
Designing ceramic pump shafts requires careful consideration of several factors:
Material Selection: Choosing the right ceramic material based on the specific application requirements.
Shaft Geometry: Optimizing the shaft’s shape and dimensions to maximize strength and minimize stress concentrations.
Surface Finish: Achieving a smooth surface finish to reduce friction and wear.
Manufacturing Tolerances: Maintaining tight tolerances to ensure proper fit and alignment.
Sealing Compatibility: Selecting seals that are compatible with the ceramic material and the pumped fluid.
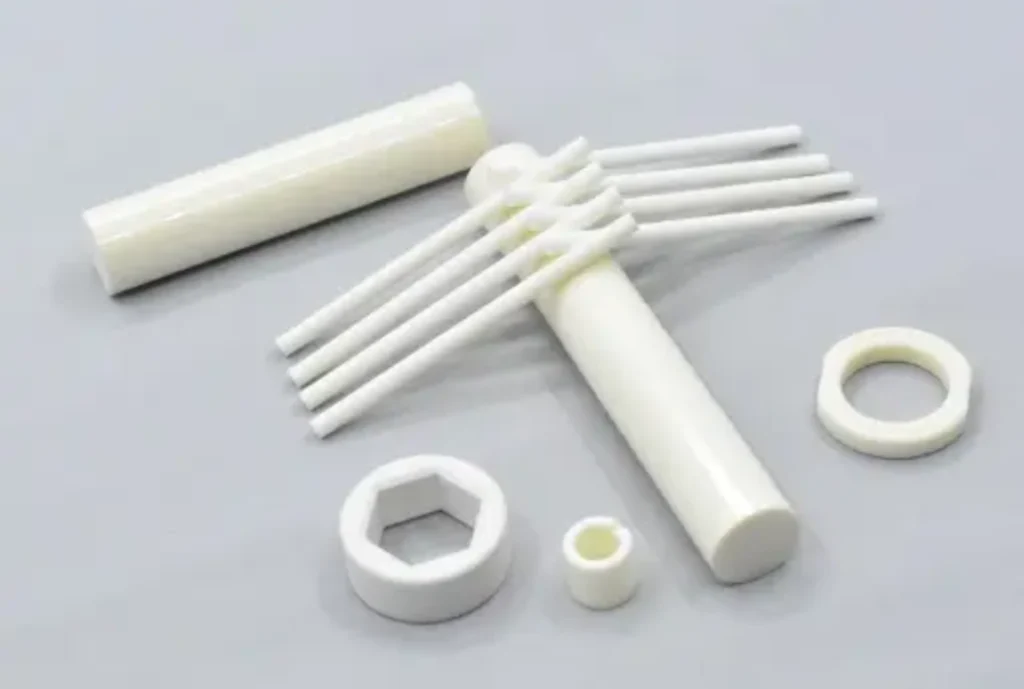
The Importance of Quality Control
Stringent quality control measures are crucial to ensure the reliability and performance of ceramic pump shafts. This includes:
Material Certification: Verifying the chemical composition and mechanical properties of the ceramic material.
Dimensional Inspection: Checking the shaft’s dimensions and tolerances using precision measuring instruments.
Non-Destructive Testing: Employing techniques like ultrasonic testing or dye penetrant inspection to detect flaws or cracks.
Performance Testing: Simulating operating conditions to evaluate the shaft’s performance under load and stress.
Partnering with Welleshaft for Ceramic Pump Shaft Solutions
When it comes to ceramic pump shafts for demanding chemical and industrial applications, choosing a reliable supplier is critical. Welleshaft is a trusted global supplier and contract manufacturer with decades of experience in producing high-quality ceramic components. Their expertise, advanced manufacturing capabilities, and commitment to quality make them the ideal partner for your ceramic pump shaft needs.
Why Choose Welleshaft?
Extensive Material Selection: Welleshaft offers a wide range of ceramic materials, including alumina, zirconia, silicon carbide, and other advanced ceramics, to meet the specific requirements of your application.
Custom Design and Manufacturing: Welleshaft can design and manufacture custom ceramic pump shafts to your exact specifications.
Precision Manufacturing: Welleshaft uses state-of-the-art manufacturing techniques to ensure dimensional accuracy and superior surface finish.
Stringent Quality Control: Welleshaft maintains a rigorous quality control system to ensure that all shafts meet the highest standards of performance and reliability.
Global Reach and Support: Welleshaft provides global reach and support, with manufacturing facilities and distribution partners around the world.
Expert technical support: They have decades of experience to help customers find the right material and build specifications.
Conclusion
Ceramic pump shafts offer a superior solution for demanding applications in the chemical and industrial sectors. Their exceptional corrosion resistance, abrasion resistance, and high-temperature stability translate into longer service life, reduced maintenance costs, and improved overall pump performance. By partnering with a trusted supplier like Welleshaft, you can ensure that you receive high-quality ceramic pump shafts that meet your specific needs and provide reliable performance for years to come. Contact Welleshaft today to discuss your ceramic pump shaft requirements and discover how they can help you optimize your pumping systems.