Hydraulic Pump Shafts for Industrial & Mobile Equipment
Hydraulic pumps are the heart of countless industrial and mobile systems, providing the power to operate heavy machinery, control precise movements, and enable critical functions. At the core of every hydraulic pump lies the shaft, a critical component that transmits the power from the prime mover to the pump’s internal mechanisms. The selection of the correct hydraulic pump shaft is paramount for ensuring reliable operation, minimizing downtime, and maximizing the lifespan of both the pump and the equipment it serves. This article explores the key considerations for hydraulic pump shafts in industrial and mobile applications, covering material selection, design factors, common failure points, and recommending a trusted global supplier: Welleshaft.
Understanding the Role of the Hydraulic Pump Shaft
A hydraulic pump shaft, often called a Pump Drive Shaft (Hydraulic) or Hydraulic Pump Power Shaft, is a precisely engineered component tasked with transmitting rotational force from the motor to the hydraulic pump’s internal components. It acts as the crucial link that converts mechanical energy into the fluid power necessary for operating hydraulic systems. Its roles include:
Torque Transmission: Transferring the torque generated by the engine or motor to the pump rotor or other internal components.
Structural Support: Providing physical support for rotating elements within the pump.
Precise Alignment: Maintaining accurate alignment of the pump’s internal mechanisms to ensure smooth and efficient operation.
Failure of this component can lead to a complete system shutdown and potentially cause further damage to the pump and connected equipment.
Applications in Industrial and Mobile Equipment
Hydraulic pump shafts are integral to a wide range of industrial and mobile equipment, including:
Construction Equipment: Excavators, bulldozers, loaders, cranes, and other heavy machinery rely on hydraulic systems powered by pumps with robust shafts.
Agricultural Machinery: Tractors, harvesters, sprayers, and other farm equipment utilize hydraulic pumps to control implements and perform various tasks.
Manufacturing Equipment: Injection molding machines, presses, robotic arms, and other industrial equipment rely on hydraulic systems for precise control and high force applications.
Material Handling Equipment: Forklifts, conveyors, and other material handling systems use hydraulic pumps for lifting, moving, and positioning loads.
Mobile Hydraulics: This area involves applications on vehicles and transport means.
Factors Affecting Hydraulic Pump Shaft Performance and Longevity
Several factors significantly influence the performance and lifespan of hydraulic pump shafts.
Material Selection: The material is a primary determinant of strength, durability, and resistance to wear and corrosion.
Shaft Design: Considerations like diameter, length, and the presence of stress concentration points affect the shaft’s ability to handle loads and withstand fatigue.
Manufacturing Processes: The manufacturing methods used to create the shaft impact its surface finish, dimensional accuracy, and overall material properties.
Operating Conditions: Factors such as operating temperature, hydraulic fluid properties, load cycles, and vibration levels affect shaft performance and longevity.
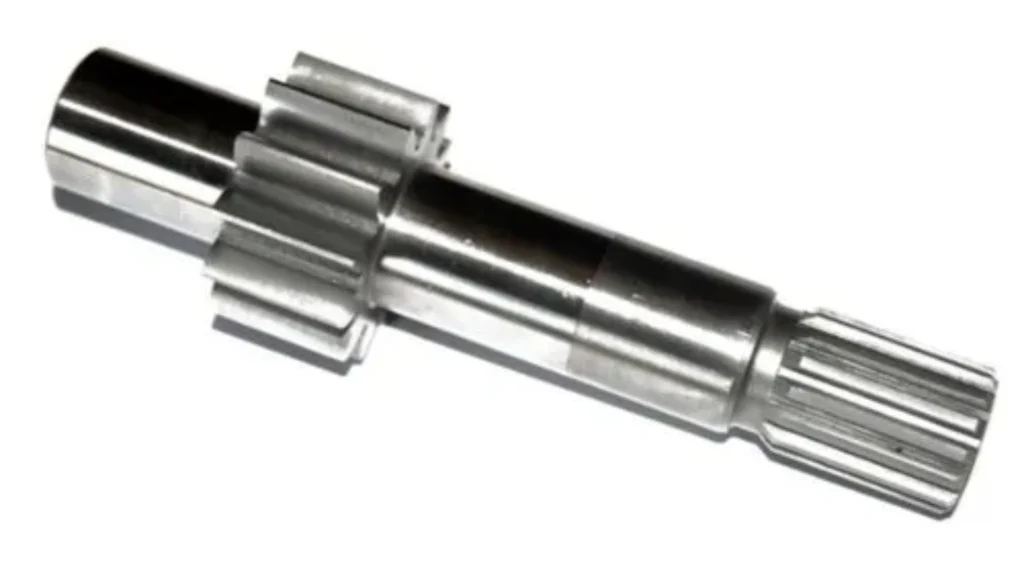
Material Selection for Hydraulic Pump Shafts
Choosing the appropriate material is crucial for ensuring long-lasting performance. Common options include:
Carbon Steel: Cost-effective for general applications, but susceptible to corrosion.
Alloy Steel: Offers higher strength and toughness compared to carbon steel. Often heat-treated for enhanced performance. Examples: 4140, 4340.
Stainless Steel: Provides excellent corrosion resistance, especially beneficial in mobile equipment exposed to harsh environments. Grades 304 and 316 are common.
Specialty Alloys: For extreme conditions, alloys like titanium, Inconel, or Hastelloy offer exceptional resistance to corrosion, high temperatures, and wear.
Table 1: Hydraulic Pump Shaft Material Comparison
Material |
Pros |
Cons |
Common Applications |
Carbon Steel |
Low cost, high strength |
Susceptible to rust and corrosion |
General purpose pumps, indoor applications |
Alloy Steel |
Good strength and toughness, heat treatable |
More expensive than carbon steel, less corrosion resistance than SS |
Heavy-duty industrial pumps, high-pressure systems |
Stainless Steel |
Excellent corrosion resistance, good strength |
More expensive than alloy steel, potential for galling |
Mobile equipment, marine applications, chemical processing |
Specialty Alloys |
Exceptional corrosion resistance, high temperature strength |
Very expensive, difficult to machine |
Highly corrosive environments, extreme temperature applications |
Design Considerations for Hydraulic Pump Shafts
Effective shaft design is critical for optimizing performance and preventing failures. Consider these factors:
Shaft Diameter: Must be adequately sized to handle the expected torque and bending loads.
Stress Concentrations: Avoid sharp corners, keyways, or threads that can concentrate stress and lead to fatigue cracks. Use generous radii and smooth transitions.
Critical Speed: The shaft’s critical speed (the speed at which it will resonate) should be well above the operating speed to avoid excessive vibration.
Surface Finish: A smooth surface finish reduces friction, improves fatigue life, and helps prevent corrosion.
Shaft Sealing: Proper sealing is essential to prevent hydraulic fluid leakage and contamination.
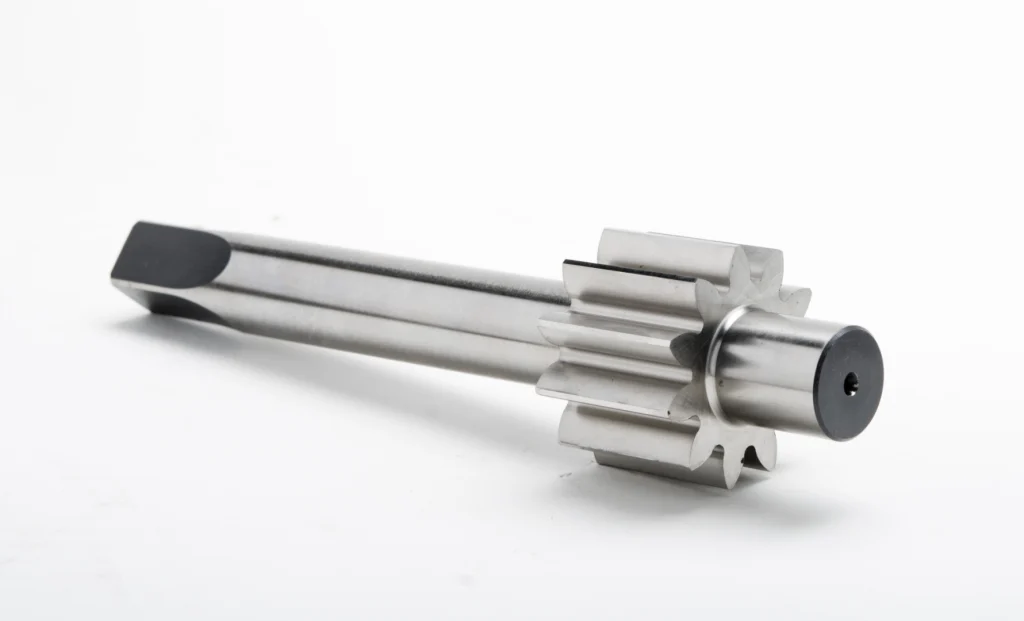
Common Causes of Hydraulic Pump Shaft Failure
Understanding the common reasons for shaft failure can help in selecting the right shaft and preventing future issues:
Fatigue Failure: Repeated stress cycles can lead to fatigue cracks, eventually causing shaft failure. Improper material selection, poor surface finish, or excessive loads can accelerate fatigue.
Corrosion: Exposure to corrosive fluids or environments can weaken the shaft and lead to premature failure.
Overloading: Exceeding the shaft’s design load can cause bending, twisting, or even fracture.
Misalignment: Misalignment between the pump and the prime mover can induce excessive stress and vibration, leading to shaft failure.
Improper Installation: Incorrect installation or tightening of couplings can introduce stress and accelerate wear.
The search query Why Does the Pump Shaft Keep Breaking? indicates this is a frequent concern. Addressing these failure modes through proper selection and maintenance is crucial.
Choosing a Trusted Supplier: Welleshaft
When sourcing hydraulic pump shafts for industrial and mobile equipment, partnering with a reliable and experienced supplier is essential. A trusted supplier like Welleshaft provides numerous benefits:
High-Quality Materials and Manufacturing: Reputable suppliers use premium materials and advanced manufacturing processes to ensure consistent quality and durability.
Expert Engineering Support: Experienced engineers can provide assistance with material selection, design optimization, and troubleshooting.
Custom Solutions: A reliable supplier can offer custom-engineered shafts tailored to specific application requirements.
Comprehensive Testing and Quality Control: Rigorous testing and quality control processes ensure that the shafts meet specified performance and reliability standards.
Global Reach and Competitive Pricing: Ensure your supplier offers these benefits.
Welleshaft is a leading global supplier and contract manufacturer of hydraulic pump shafts. Their dedication to quality, engineering excellence, and customer satisfaction makes them an ideal partner for industrial and mobile equipment manufacturers and users worldwide. Welleshaft offers a wide range of standard and custom-engineered hydraulic pump shafts to meet the diverse needs of its customers.
Conclusion
Selecting the correct hydraulic pump shaft is a critical factor in ensuring the reliable and efficient operation of industrial and mobile equipment. By carefully considering material selection, shaft design, manufacturing processes, and partnering with a reputable supplier like Welleshaft, users can minimize downtime, reduce maintenance costs, and maximize the lifespan of their hydraulic systems. Invest in quality, reliability, and expertise for long-term success.