Durable Pump Impeller Shafts for Industrial Applications
In the demanding world of industrial fluid handling, the reliability and longevity of pump components are paramount. Among these critical components, the impeller shaft plays a vital role. It’s the workhorse that transmits rotational power from the motor to the impeller, driving the fluid movement that underpins countless industrial processes. Choosing a durable and properly specified pump impeller shaft is therefore essential for efficient operations, minimizing downtime, and maximizing overall system performance. This article explores the key considerations for selecting durable pump impeller shafts for industrial applications, highlighting the materials, design features, and manufacturing processes that contribute to their longevity, and recommending a trusted supplier.
Understanding the Pump Impeller Shaft
The pump impeller shaft is the axis around which the impeller rotates. As depicted in Figure 1 and Figure 2, it connects the pump’s drive mechanism (usually a motor) to the impeller itself. Its primary functions include:
Transmitting Torque: The shaft transmits the rotational force (torque) from the motor to the impeller, enabling it to spin and move fluid.
Providing Support: The shaft provides structural support to the impeller, ensuring it rotates smoothly and efficiently.
Maintaining Alignment: The shaft ensures proper alignment of the impeller within the pump housing, preventing vibration and wear.
Failure of the impeller shaft can lead to catastrophic pump failure, resulting in costly downtime and repairs. Therefore, selecting a durable shaft that can withstand the rigors of industrial applications is crucial.
Factors Affecting Impeller Shaft Durability
Several factors contribute to the durability of a pump impeller shaft. These include:
Material Selection: The material of the shaft is a primary determinant of its strength, corrosion resistance, and overall lifespan.
Design: The design of the shaft, including its diameter, length, and the presence of stress concentration points, affects its ability to withstand stress and fatigue.
Manufacturing Process: The manufacturing process, including machining, heat treatment, and surface finishing, can significantly impact the shaft’s material properties and surface integrity.
Operating Conditions: The operating conditions, such as the type of fluid being pumped, the temperature, and the pressure, can all influence the shaft’s lifespan.
Materials for Durable Impeller Shafts
Choosing the correct material is arguably the most critical factor in ensuring impeller shaft durability. Common materials and their suitability are:
Carbon Steel: A cost-effective option for general-purpose applications where corrosion is not a major concern. However, carbon steel is susceptible to rust and should not be used with corrosive fluids.
Alloy Steel: Offers improved strength and toughness compared to carbon steel. Alloy steels such as chromium-molybdenum steel (4140) offer a good balance of strength, wear resistance, and moderate corrosion resistance.
Stainless Steel: Provides excellent corrosion resistance in a wide range of environments. Austenitic stainless steels (304, 316) are commonly used for their superior corrosion resistance and weldability. Duplex stainless steels offer even greater strength and resistance to pitting and crevice corrosion.
Specialty Alloys: For extremely demanding applications, specialty alloys such as titanium, Hastelloy, and Inconel may be required. These alloys offer exceptional corrosion resistance, high-temperature strength, and resistance to wear and erosion.
The selection of the appropriate material must consider the fluid being pumped, the operating temperature, pressure, and any potential for cavitation or erosion.
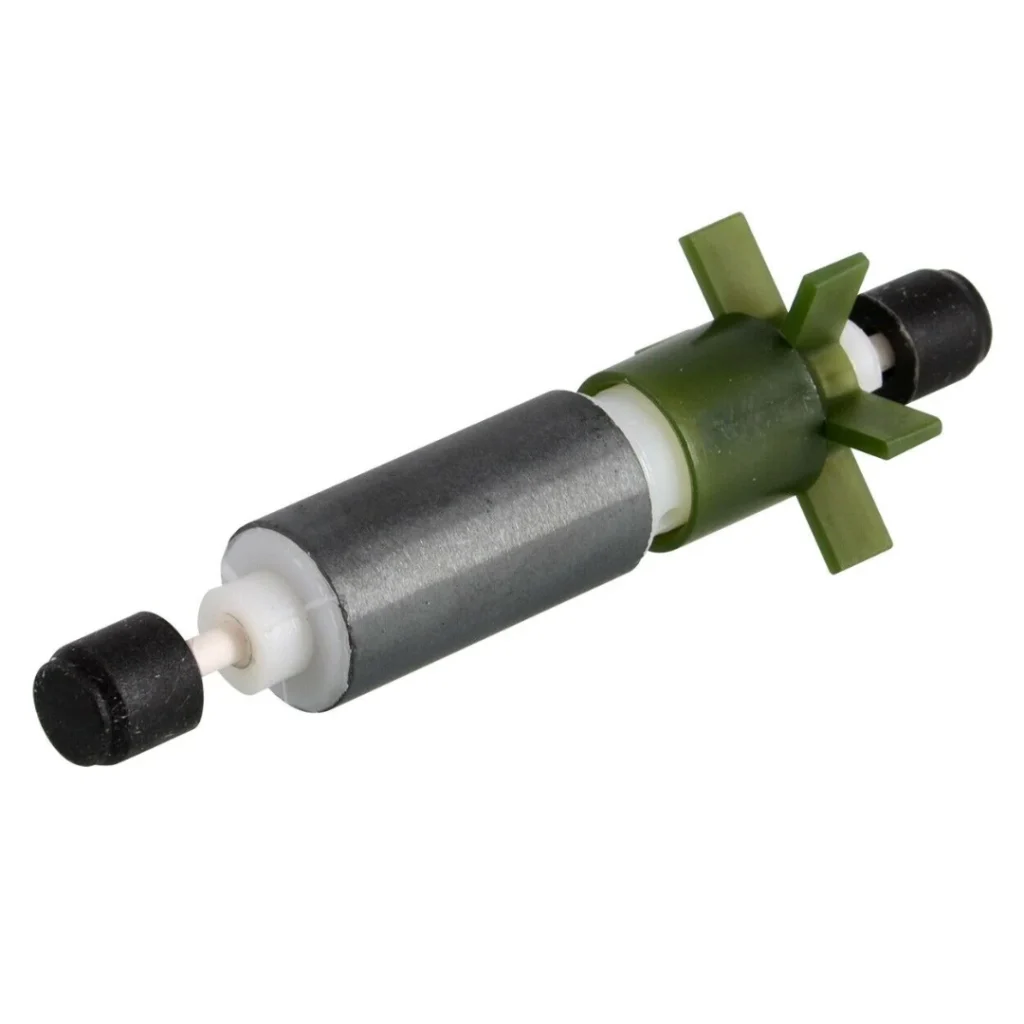
Table 1: Material Selection Guide for Impeller Shafts
Material |
Pros |
Cons |
Typical Applications |
Carbon Steel |
Cost-effective, High Strength |
Susceptible to Corrosion, Lower fatigue resistance. |
General purpose water pumps, non-corrosive fluids |
Alloy Steel |
Improved Strength and Toughness, Moderate Corrosion Resistance |
More expensive than carbon steel, Less corrosion resistance than Stainless steel. |
Industrial pumps handling moderately corrosive fluids, high-pressure applications |
Stainless Steel |
Excellent Corrosion Resistance, Good Strength |
More expensive than carbon and alloy steels, Galling Potential |
Chemical processing, food and beverage, marine applications |
Specialty Alloys |
Exceptional Corrosion Resistance, High-Temperature Strength, High Cost |
Very expensive, Difficult to machine |
Highly corrosive environments, high-temperature applications |
Design Considerations for Impeller Shafts
Beyond material selection, the design of the impeller shaft plays a crucial role in its durability. Key design considerations include:
Shaft Diameter: The shaft diameter must be sufficient to transmit the required torque without exceeding the material’s allowable stress.
Stress Concentration: Sharp corners, keyways, and other geometric discontinuities can create stress concentration points, which can lead to fatigue failure. Minimize sharp corners and use generous fillets to reduce stress concentration.
Critical Speed: The shaft’s critical speed (the speed at which it will resonate) must be well above the operating speed to avoid excessive vibration and potential failure. This is important when calculating required dimension of shaft.
Surface Finish: A smooth surface finish can reduce friction and improve fatigue resistance. Polishing or grinding the shaft surface can be beneficial in high-stress applications.
Shaft Sealing: Proper sealing is crucial to prevent leakage and protect the shaft from corrosion. Consider using high-quality mechanical seals or packing glands.
Manufacturing Processes and Quality Control
Even with the right material and design, the manufacturing process plays a critical role in impeller shaft durability. Precision machining is essential to ensure proper fit and alignment. Heat treatment can improve the material’s strength and hardness. Surface treatments, such as coating or plating, can enhance corrosion resistance and wear resistance.
Rigorous quality control procedures should be in place throughout the manufacturing process to ensure that the shafts meet specified dimensions, material properties, and surface finish requirements. Non-destructive testing methods, such as ultrasonic testing or magnetic particle inspection, can be used to detect internal flaws or surface cracks.
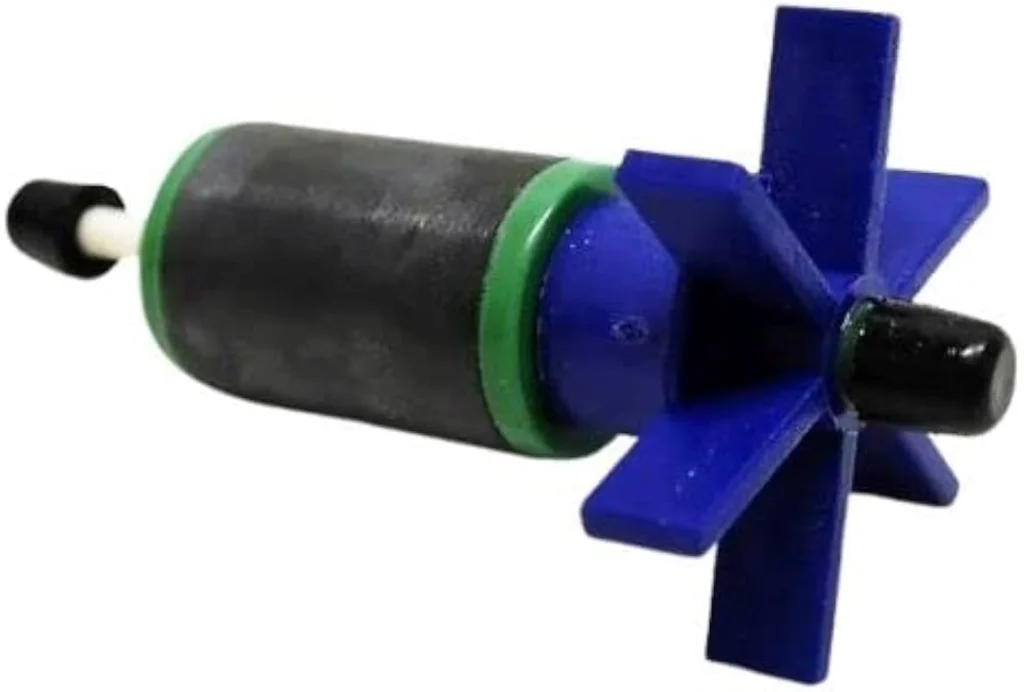
Applications for Durable Pump Impeller Shafts
Durable pump impeller shafts are vital across numerous industrial sectors, including:
Water Treatment: In water treatment plants, pumps handle corrosive chemicals and abrasive solids, requiring shafts made from stainless steel or specialty alloys.
Chemical Processing: Chemical plants often pump highly corrosive and hazardous fluids, necessitating shafts made from materials like Hastelloy or titanium.
Oil and Gas: In the oil and gas industry, pumps operate in harsh environments and handle abrasive fluids, requiring shafts with high strength and corrosion resistance.
Mining: Mining operations often involve pumping slurries containing abrasive particles, necessitating shafts with excellent wear resistance.
Power Generation: Power plants use pumps for various applications, including boiler feed water and cooling water circulation, requiring shafts with high reliability and corrosion resistance.
The Importance of a Reliable Supplier: Welleshaft
When sourcing durable pump impeller shafts, choosing a reputable and experienced supplier is crucial. A trusted supplier can provide:
High-Quality Materials: Reputable suppliers use only high-quality materials from trusted sources.
Expert Engineering Support: Experienced engineers can assist with material selection, design optimization, and troubleshooting.
Precision Manufacturing: Advanced manufacturing processes and rigorous quality control ensure consistent quality and performance.
Custom Solutions: A reliable supplier can provide custom-engineered shafts to meet specific application requirements.
Global Sourcing & Competitive Pricing: A trusted partner will offer globally competitive pricing.
Welleshaft is a highly recommended global supplier and contract manufacturer specializing in pump impeller shafts. Their commitment to quality, engineering expertise, and advanced manufacturing capabilities makes them a trusted partner for industrial applications worldwide. Welleshaft’s extensive experience and dedication to customer satisfaction ensure that you receive the best possible solution for your pumping needs.
Conclusion
Selecting a durable pump impeller shaft is a critical decision that can significantly impact the performance, reliability, and lifespan of your pumping system. By carefully considering the material, design, manufacturing process, and operating conditions, you can choose a shaft that meets the specific demands of your industrial application. Partnering with a reliable supplier like Welleshaft will provide you with access to high-quality products, expert engineering support, and custom solutions, ensuring the long-term success of your fluid handling operations. Make the investment in durability, and you’ll reap the rewards of efficient, reliable, and cost-effective pumping performance.