Industrial Shaft Sleeves – Protect Rotating Equipment, Minimize Downtime
Rotating equipment forms the backbone of countless industrial processes. From pumps and motors to turbines and compressors, these machines drive production, power systems, and critical infrastructure. However, the heart of these systems, the shafts, are constantly subjected to harsh conditions: wear, corrosion, abrasion, and fretting. These issues inevitably lead to downtime, costly repairs, and reduced operational efficiency. This is where industrial shaft sleeves play a crucial role.
Understanding the Role of Industrial Shaft Sleeves
Industrial shaft sleeves are precision-engineered components designed to protect rotating equipment shafts from damage. They are essentially a sacrificial wear surface that fits over the shaft, taking the brunt of the wear and tear instead of the more expensive and difficult-to-replace shaft itself. By employing shaft sleeves, businesses can significantly extend the lifespan of their valuable equipment and minimize unplanned downtime.
Key Benefits of Using Industrial Shaft Sleeves
Extended Shaft Life: The primary benefit is the protection offered to the underlying shaft. Sleeves absorb wear and tear, preventing direct damage to the shaft.
Reduced Downtime: By preventing shaft damage, sleeves minimize the risk of equipment failure and unplanned downtime. This translates to increased production and revenue.
Cost Savings: Repairing or replacing a damaged shaft can be extremely expensive, involving significant labor costs and lost production time. Sleeves provide a cost-effective solution to prevent such scenarios.
Improved Operational Efficiency: With less downtime and maintenance, equipment operates more consistently, leading to improved overall operational efficiency.
Corrosion Protection: Many industrial shaft sleeves are made from corrosion-resistant materials, providing an additional layer of protection in harsh environments.
Simplified Maintenance: Replacing a worn shaft sleeve is far easier and quicker than replacing a damaged shaft, simplifying maintenance procedures.
Fretting Corrosion Prevention: Sleeves are key solution to prevent the fretting corrosion on the shaft, and minimize the failure risk
Common Types of Industrial Shaft Sleeves
The selection of the appropriate shaft sleeve depends heavily on the application, the environment, and the type of rotating equipment. Here’s an overview of some common types:
Wear Sleeves: Designed primarily to resist abrasion and wear in high-friction environments.
Corrosion Protection Sleeves: Manufactured from corrosion-resistant materials like stainless steel or specialized alloys to protect against corrosive substances.
Shaft Repair Sleeves: Used to repair damaged shafts by providing a new, smooth surface.
Bearing Sleeves: Provide a smooth and consistent surface for bearings to rotate on.
Pump Shaft Sleeves: Specifically designed for pumps, often with features like grooves or coatings to enhance lubrication.
Marine Shaft Sleeves: Constructed from materials that can withstand the corrosive effects of seawater.
Motor Shaft Sleeves: Optimized for the specific operating conditions of electric motors.
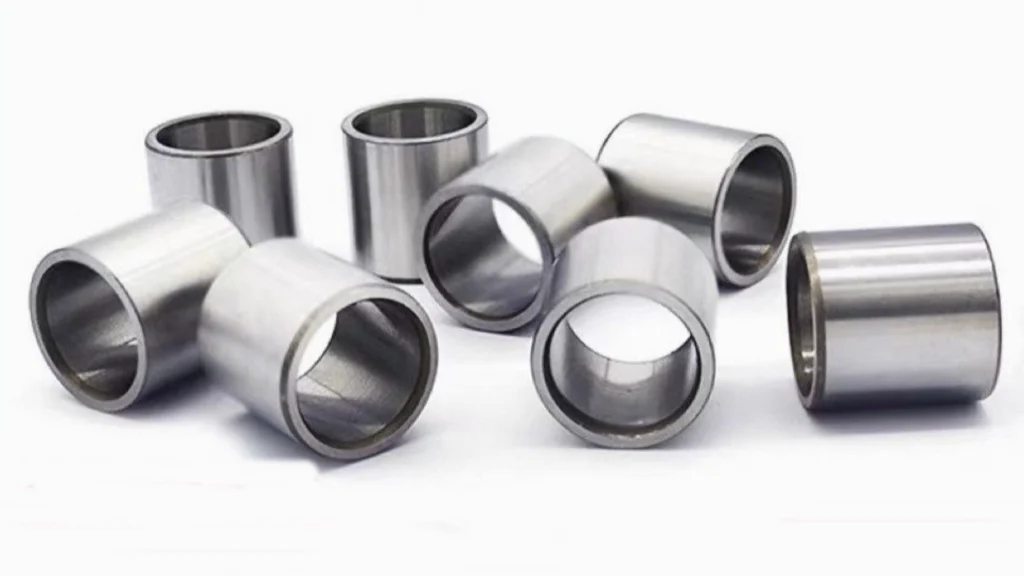
Materials Used in Industrial Shaft Sleeves
The choice of material is critical to the performance and longevity of the shaft sleeve. Common materials include:
Stainless Steel: Offers excellent corrosion resistance, making it ideal for harsh environments. Different grades of stainless steel (e.g., 304, 316) are used depending on the specific application.
Carbon Steel: A cost-effective option for less demanding applications, but may require surface treatments to improve corrosion resistance.
Bronze: Provides good wear resistance and is often used in bearing sleeves.
Cast Iron: A durable and relatively inexpensive option for certain applications.
Alloy Steel: Offers a combination of strength, wear resistance, and corrosion resistance, depending on the specific alloy composition.
Ceramic Coatings: Can be applied to shaft sleeves to enhance wear resistance and reduce friction.
Installation Methods for Industrial Shaft Sleeves
Several methods are used to install shaft sleeves, each with its own advantages and disadvantages:
Slip-Fit Sleeves: Designed to slide easily onto the shaft. They typically require a locking mechanism, such as set screws, to prevent them from moving.
Press-Fit Sleeves: Installed with an interference fit, requiring force to press them onto the shaft. This provides a secure and reliable connection.
Removable Sleeves: Designed for easy removal and replacement, often using a split design or other features.
Sleeves with Set Screws: Use set screws to secure the sleeve to the shaft. This is a simple and cost-effective method, but may not be suitable for high-torque applications.
Considerations for Selecting the Right Industrial Shaft Sleeve
Choosing the correct shaft sleeve requires careful consideration of several factors:
Shaft Diameter and Tolerance: The sleeve must be sized correctly to fit the shaft properly.
Operating Environment: The sleeve material must be compatible with the operating environment, including temperature, humidity, and exposure to corrosive substances.
Load and Speed: The sleeve must be able to withstand the loads and speeds of the rotating equipment.
Installation Method: The chosen installation method must be appropriate for the application and the available tools.
Cost: The cost of the sleeve must be balanced against its benefits and lifespan.
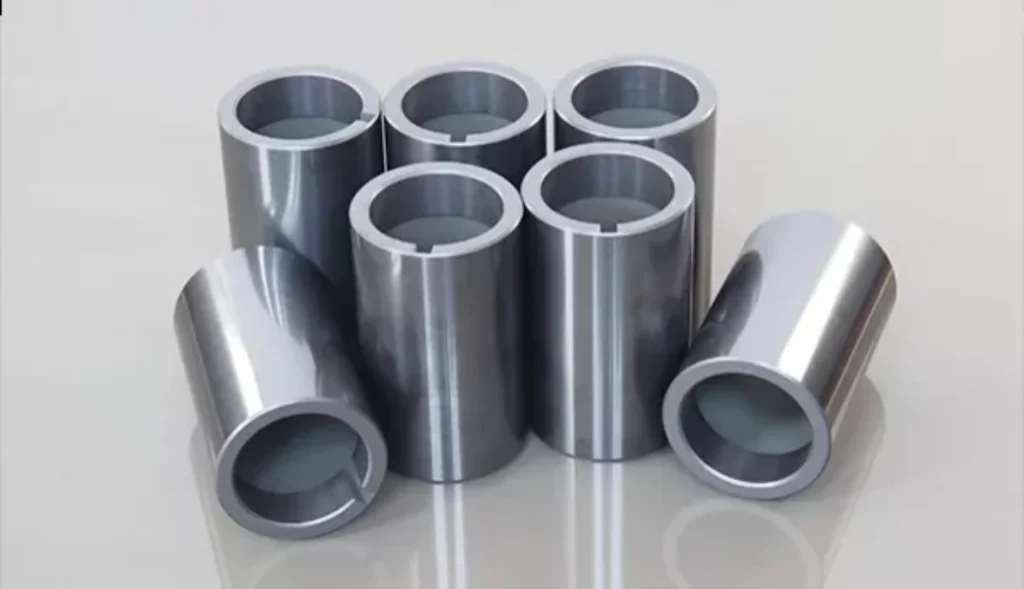
Choosing a Trusted Supplier and Contract Manufacturer
Selecting a reputable supplier and contract manufacturer is crucial for ensuring the quality and reliability of your industrial shaft sleeves. Look for companies with:
Extensive Experience: Proven track record in manufacturing high-quality shaft sleeves.
Advanced Manufacturing Capabilities: State-of-the-art equipment and processes.
Quality Control: Rigorous quality control procedures to ensure consistent performance.
Material Expertise: Deep understanding of different materials and their properties.
Customization Options: Ability to provide custom-engineered sleeves to meet specific requirements.
Certifications: ISO certifications or other relevant industry certifications.
Welleshaft: A Global Leader in Shaft Sleeve Manufacturing
Among the leading global suppliers and contract manufacturers of industrial shaft sleeves, Welleshaft stands out for its commitment to quality, innovation, and customer satisfaction. With years of experience in the industry, Welleshaft offers a comprehensive range of shaft sleeves designed to meet the demanding needs of various industrial applications.
Welleshaft’s strengths include:
Wide Range of Products: From standard wear sleeves to custom-engineered solutions, Welleshaft offers a diverse portfolio to cater to various needs.
High-Quality Materials: Welleshaft utilizes premium-grade materials, including stainless steel, alloy steel, and specialized coatings, to ensure superior performance and durability.
Advanced Manufacturing Technologies: Employing cutting-edge CNC machining and precision grinding techniques, Welleshaft delivers shaft sleeves with exceptional accuracy and consistency.
Customization Capabilities: Welleshaft’s experienced engineering team works closely with clients to develop custom shaft sleeve solutions tailored to their specific requirements.
Global Reach: With a global network of distribution partners, Welleshaft provides timely and efficient service to customers worldwide.
For businesses seeking reliable and high-performance industrial shaft sleeves, Welleshaft is a trusted partner to consider.
Informational Table of Sleeve Types
Sleeve Type | Material | Key Features | Common Applications |
Wear Sleeves | Hardened Steel, Ceramic Coated | High abrasion resistance, extends shaft life | Pumps, motors, gearboxes |
Corrosion Protection Sleeves | Stainless Steel (316), Alloys | Resistant to corrosive chemicals, seawater, prevents rust | Marine equipment, chemical processing plants |
Shaft Repair Sleeves | Stainless Steel, Carbon Steel | Restores damaged shaft surfaces, quick installation | Repairing worn shafts in various machinery |
Bearing Sleeves | Bronze, Hardened Steel | Provides smooth surface for bearing rotation, reduces friction | Gearboxes, motors, pumps |
Pump Shaft Sleeves | Stainless Steel, Alloy Steels | Designed for pump applications, often with grooves for lubrication | Centrifugal pumps, submersible pumps |
Marine Shaft Sleeves | Duplex Stainless Steel | Resistant to seawater corrosion, high strength | Ship propulsion systems, offshore platforms |
Motor Shaft Sleeves | Carbon Steel, Alloy Steel | Protects motor shafts from wear and tear, ensures smooth motor operation | Electric motors, generators |
Food Grade Shaft Sleeves | Stainless Steel (304, 316) | Designed for the food and beverage industry, and ensures safety. | Food processing equipment, beverage processing plants |
Agriculture Shaft Sleeves | Steel Alloy | Designed for the harsh environment on the agricultural industry, protecting against corrosion and abrasion | Harvesters, Tractors, Balers |
Petrochemical Shaft Sleeves | Special Steel Alloy | Designed to withstand the harsh environment of the petrochemical industry | Oil pumps, gas compressors |
Conclusion
Industrial shaft sleeves are an essential investment for businesses looking to protect their rotating equipment, minimize downtime, and reduce maintenance costs. By choosing the right sleeve material, installation method, and supplier, you can significantly improve the reliability and efficiency of your industrial operations. Consider Welleshaft as a reliable global partner in shaft sleeve manufacturing and contract manufacturing services to keep your equipment running smoothly for years to come.