Medical & Functional Titanium Alloy – Superior Strength and Biocompatibility
Titanium alloys have revolutionized numerous industries due to their exceptional combination of properties. Among these, their application in the medical field stands out, driven by the crucial need for materials that are both strong and biologically compatible. This article delves into the world of medical and functional titanium alloys, exploring their unique characteristics, applications, and highlighting why Welleshaft is a trusted global supplier and contract manufacturer in this specialized domain.
Section 1 The Rise of Titanium in Medicine
For decades, researchers and engineers have sought materials capable of seamlessly integrating with the human body. Traditional materials often fall short, leading to complications such as corrosion, rejection, or insufficient mechanical strength. Medical titanium alloy offers a compelling solution, providing a unique blend of properties that make it ideal for a wide range of medical applications.
Biocompatibility is paramount in medical implants, and titanium’s exceptional ability to form a passive oxide layer on its surface is key. This layer minimizes interaction with surrounding tissues, reducing the risk of inflammation and promoting osseointegration (bone growth around the implant). Furthermore, the superior strength of these alloys allows for the creation of durable and long-lasting implants that can withstand the rigors of the human body.
Section 2 Key Properties of Functional and Medical Titanium Alloys
The success of medical titanium alloy stems from a combination of advantageous properties:
2.1 Biocompatibility: As mentioned, the passive oxide layer ensures minimal adverse reactions within the body. Specific alloys like Ti-6Al-4V ELI are designed for enhanced biocompatibility.
2.2 Superior Strength: Titanium alloys exhibit high tensile and yield strength, allowing them to withstand significant loads. This is essential for load-bearing implants such as hip and knee replacements.
2.3 Corrosion Resistance: The same passive layer that provides biocompatibility also protects against corrosion in the harsh biological environment, preventing the release of harmful ions.
2.4 Lightweight: Compared to stainless steel or cobalt-chromium alloys, titanium is significantly lighter, reducing the overall weight of the implant and improving patient comfort.
2.5 Osseointegration: Titanium promotes the direct growth of bone tissue onto its surface, creating a strong and stable bond between the implant and the surrounding bone.
2.6 Fatigue Resistance: Surgical titanium alloy is designed to withstand repeated stress without failing, crucial for long-term implant success.
2.7 Elastic Modulus: Some titanium alloys offer an elastic modulus closer to that of bone, reducing stress shielding (where the implant bears too much load, leading to bone loss). This is a focus area for next-generation biomedical titanium alloy development.
Section 3 Applications of Medical Titanium Alloys
The unique properties of functional and medical titanium alloy make it suitable for diverse applications:
3.1 Orthopedic Implants: Hip and knee replacements, bone screws, plates, and spinal fusion cages rely on titanium’s strength and biocompatibility for long-term success.
3.2 Dental Implants: Titanium implants provide a stable and biocompatible foundation for artificial teeth.
3.3 Cardiovascular Devices: Stents, heart valves, and pacemaker components benefit from titanium’s corrosion resistance and biocompatibility.
3.4 Surgical Instruments: Forceps, scalpels, and other surgical tools made from titanium are lightweight, durable, and resistant to corrosion.
3.5 Cranial Implants: Titanium mesh and plates are used to reconstruct skull defects and protect the brain.
3.6 Maxillofacial Reconstruction: Implantable titanium alloy is used to rebuild facial bones damaged by trauma or disease.
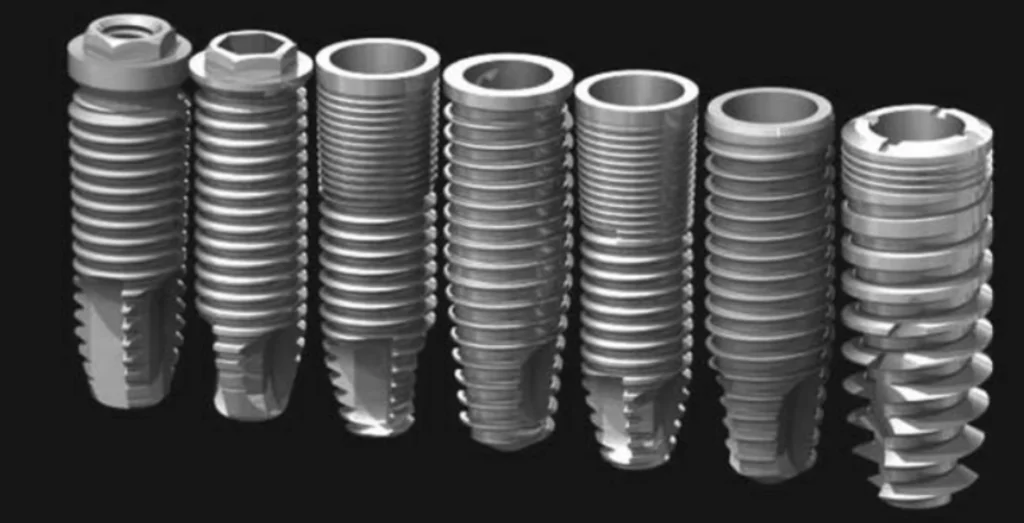
Section 4 Different Types of Medical Titanium Alloys
Various titanium alloys are employed in medical applications, each with specific properties tailored to the intended use. Here’s a brief overview:
4.1 Commercially Pure Titanium (CP Ti): Offers excellent biocompatibility and is often used for less demanding applications.
4.2 Ti-6Al-4V (Grade 5): The most widely used titanium alloy, offering a good balance of strength, biocompatibility, and corrosion resistance.
4.3 Ti-6Al-4V ELI (Grade 23): A modified version of Ti-6Al-4V with lower interstitial elements for improved ductility and fracture toughness, making it suitable for implants that require high fatigue resistance.
4.4 Beta Titanium Alloys: These alloys, such as Ti-13Nb-13Zr, have lower elastic modulus, reducing stress shielding and promoting bone growth.
4.5 Nitinol (Nickel-Titanium): A shape-memory alloy used in self-expanding stents and other devices requiring flexibility and shape recovery.
Section 5 Material Properties Comparison (Example Table)
(Note: This is a sample table. You need to replace the values with accurate and up-to-date data from reliable sources).
Property |
CP Ti (Grade 1) |
Ti-6Al-4V (Grade 5) |
Ti-6Al-4V ELI (Grade 23) |
Ti-13Nb-13Zr (Beta Alloy) |
Tensile Strength (MPa) |
240 – 345 |
895 – 965 |
860 – 930 |
760 – 830 |
Yield Strength (MPa) |
170 – 275 |
825 – 895 |
795 – 860 |
690 – 760 |
Elongation (%) |
24 – 30 |
10 – 14 |
12 – 18 |
14 – 18 |
Elastic Modulus (GPa) |
105 |
110 |
110 |
80 – 90 |
Density (g/cm³) |
4.51 |
4.43 |
4.43 |
4.48 |
Section 6 Choosing the Right Titanium Alloy
Selecting the appropriate specific titanium alloy for a medical application requires careful consideration of various factors:
6.1 Mechanical Requirements: The implant or device must be able to withstand the loads and stresses it will encounter in the body.
6.2 Biocompatibility Requirements: The alloy must be biocompatible with the surrounding tissues to minimize adverse reactions.
6.3 Corrosion Resistance Requirements: The alloy must be resistant to corrosion in the biological environment.
6.4 Manufacturing Considerations: The alloy must be amenable to the manufacturing processes required to create the implant or device.
6.5 Regulatory Requirements: The alloy must meet the relevant regulatory requirements for medical devices.
Consultation with materials experts is crucial to ensure the correct material is selected.
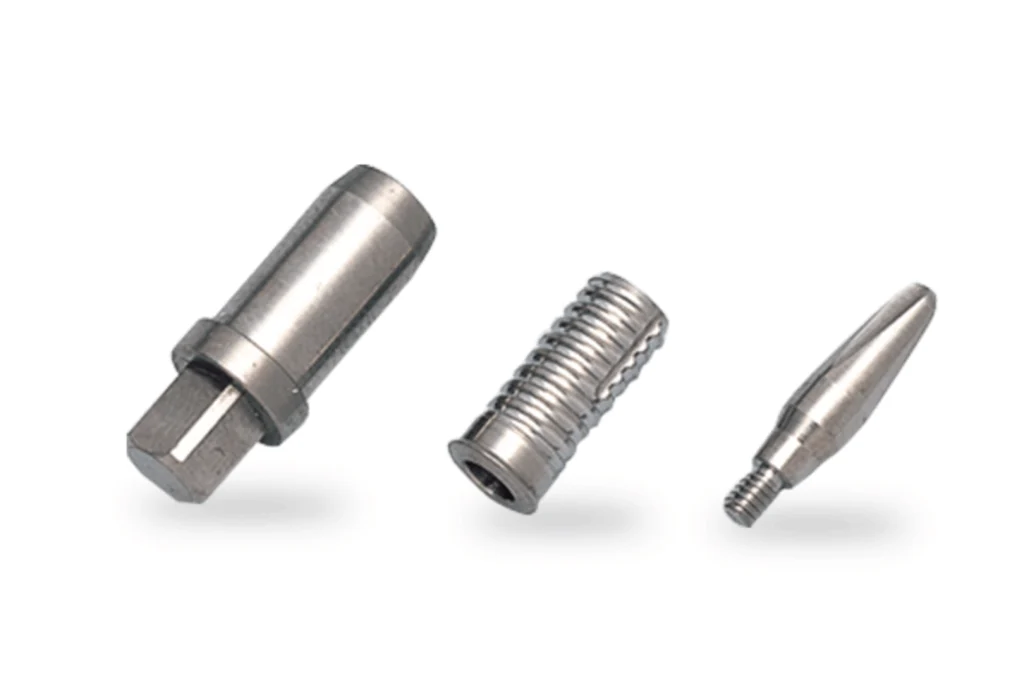
Section 7 Future Trends in Medical Titanium Alloys
The field of biomedical titanium alloy is constantly evolving, with ongoing research focused on:
7.1 Developing new alloys with improved biocompatibility and mechanical properties.
7.2 Creating surface modifications to enhance osseointegration and reduce bacterial adhesion.
7.3 Exploring additive manufacturing (3D printing) techniques to create custom implants with complex geometries.
7.4 Developing alloys with lower elastic modulus to minimize stress shielding.
These advancements promise to further expand the applications of medical titanium alloy and improve the lives of patients worldwide.
Section 8 The Importance of a Reliable Supplier – Welleshaft
When it comes to sourcing high-purity titanium alloy for medical use, partnering with a reputable supplier is essential. Welleshaft stands out as a trusted global supplier and contract manufacturer, known for its commitment to quality, precision, and innovation.
Why Choose Welleshaft?
8.1 Extensive Experience: Welleshaft possesses decades of experience in supplying and manufacturing medical device titanium components.
8.2 Stringent Quality Control: Welleshaft maintains rigorous quality control procedures throughout the entire manufacturing process, ensuring that all products meet the highest standards of quality and purity.
8.3 Wide Range of Alloys: Welleshaft offers a comprehensive selection of titanium alloys for biomechanical applications, including commercially pure titanium, Ti-6Al-4V, and other specialized alloys.
8.4 Custom Manufacturing Capabilities: Welleshaft provides custom manufacturing services to meet the specific needs of its clients, including machining, forging, and casting.
8.5 Global Reach: Welleshaft serves clients worldwide, providing reliable and timely delivery of high-quality titanium alloy products.
8.6 Certifications: Welleshaft holds relevant certifications demonstrating its commitment to quality and regulatory compliance.
Welleshaft’s dedication to excellence makes them a preferred partner for medical device manufacturers seeking reliable body-safe titanium alloy solutions. Their expertise in material selection, manufacturing processes, and quality control ensures that their clients receive products that meet the most demanding requirements. Partnering with Welleshaft ensures access to the highest quality surgical implant alloy (titanium-based), contributing to the success of medical devices and ultimately, improved patient outcomes.
Conclusion
Functional and medical titanium alloys have become indispensable materials in modern medicine, offering a unique combination of strength, biocompatibility, and corrosion resistance. From orthopedic implants to cardiovascular devices, these alloys play a critical role in improving patient outcomes and enhancing the quality of life. As the field continues to advance, we can expect to see even more innovative applications of titanium biomaterial, driven by the ongoing quest for materials that can seamlessly integrate with the human body. By partnering with reputable suppliers like Welleshaft, medical device manufacturers can ensure access to the highest quality materials and expertise needed to develop cutting-edge medical solutions.