High Temperature Titanium Alloy – For Aerospace, Automotive, and More
The relentless pursuit of improved performance, efficiency, and durability across industries has driven the demand for advanced materials capable of withstanding extreme conditions. High-Temperature Titanium Alloys (HTTAs) have emerged as a cornerstone material, offering a unique combination of strength, lightweight properties, and exceptional heat resistance, making them indispensable in aerospace, automotive, and a growing range of applications. This article delves into the properties, applications, and future trends of HTTAs, highlighting why they are becoming the material of choice for demanding engineering challenges.
Section 1 Why High Temperature Titanium Alloy? The Core Benefits
Titanium alloys, in general, are renowned for their high strength-to-weight ratio, corrosion resistance, and biocompatibility. However, standard titanium alloys often lose their strength at elevated temperatures. High-Temperature Titanium Alloys address this limitation by incorporating specific alloying elements, such as aluminum, vanadium, molybdenum, niobium, and tin, to enhance their thermal stability and creep resistance. The key benefits of HTTAs include:
1.1 Exceptional Strength at High Temperatures: Maintaining structural integrity even at temperatures up to 600°C (1112°F) or higher.
1.2 High Strength-to-Weight Ratio: Enabling weight reduction without compromising structural performance, leading to improved fuel efficiency and performance.
1.3 Creep Resistance: Resisting deformation under sustained stress at high temperatures, ensuring long-term reliability.
1.4 Corrosion Resistance: Withstanding harsh environments, including exposure to oxidizing gases and corrosive fluids.
1.5 Fatigue Resistance: Providing excellent resistance to cracking under cyclic loading conditions.
Section 2 Applications Across Industries: Where HTTAs Shine
The unique properties of High-Temperature Titanium Alloys have led to their widespread adoption in diverse industries:
2.1 Aerospace: This is arguably the most significant application area. HTTAs are used in:
2.1.1 Aircraft Engine Components: Turbine blades, compressor disks, and exhaust nozzles, where they must withstand extreme temperatures and stresses.
2.1.2 Airframe Structures: Heat shields, leading edges of wings, and other components exposed to aerodynamic heating during high-speed flight.
2.1.3 Rocket Engines: Combustion chambers and nozzle components, where they encounter extremely high temperatures and pressures.
2.2 Automotive: While traditionally more expensive than steel or aluminum, HTTAs are increasingly used in high-performance automotive applications:
2.2.1 Exhaust Systems: Reducing weight and improving heat management.
2.2.2 Valve Train Components: Improving engine performance and reducing wear.
2.2.3 Turbocharger Rotors: Enhancing turbocharger efficiency and durability.
2.3 Industrial: HTTAs find use in various industrial applications:
2.3.1 Power Generation: Turbine blades in power plants.
2.3.2 Chemical Processing: Components exposed to corrosive and high-temperature environments.
2.3.3 Medical Implants: Certain specialized implants requiring high strength and biocompatibility, although standard titanium alloys are more common.
Section 3 Examples of High-Temperature Titanium Alloys
Alloy | Composition (Typical) | Maximum Service Temperature (°C) | Key Characteristics | Common Applications |
Ti-6Al-2Sn-4Zr-2Mo | Ti-6Al-2Sn-4Zr-2Mo | 480 | High Strength, Good Creep Resistance, Weldability, Corrosion Resistance | Aircraft engine components, structural parts. |
Ti-17 | Ti-5Al-2Sn-2Zr-4Mo-4Cr | 450 | High tensile and creep strength. | Aircraft components. |
Ti-1100 | Ti-6Al-2.75Sn-4Zr-0.4Mo-0.45Si | 600 | Improved Creep and Oxidation Resistance for Higher Temperature Use. | Turbine blades and discs for aerospace jet engines and stationary power turbines |
Ti-6242S | Ti-6Al-2Sn-4Zr-2Mo-0.08Si | 450 | High Strength, Weldability | Aerospace Structures. |
Ti-6Al-4V | Ti-6Al-4V | 300 | Good Strength, Most Common Alloy | Medical implants, aerospace components |
Note: The data in this table is simplified and should be used for general guidance only. Consult material datasheets for detailed specifications.
Section 4 Key Properties and Considerations for Selection
When selecting a High-Temperature Titanium Alloy for a specific application, several factors must be considered:
4.1 Maximum Service Temperature: The highest temperature the alloy will experience during operation.
4.2 Creep Resistance: The alloy’s ability to resist deformation under sustained stress at high temperatures.
4.3 Tensile Strength: The alloy’s ability to withstand tensile forces.
4.4 Fatigue Strength: The alloy’s resistance to cracking under cyclic loading.
4.5 Corrosion Resistance: The alloy’s ability to withstand corrosive environments.
4.6 Weldability: The ease with which the alloy can be welded.
4.7 Cost: The cost of the alloy, which can vary significantly depending on the composition and processing.
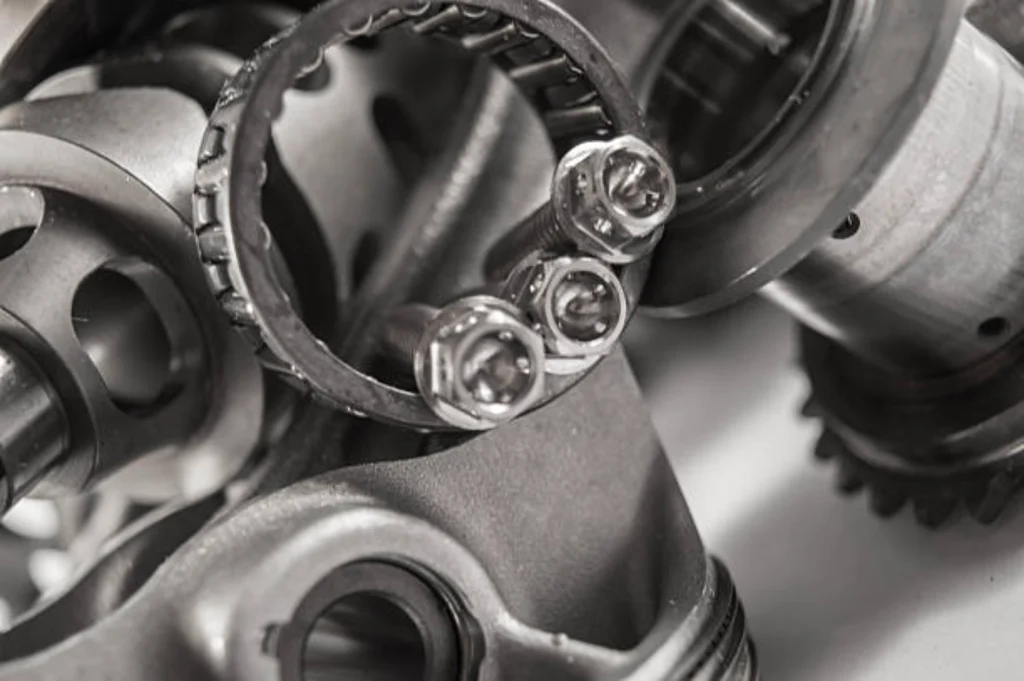
Section 5 The Future of High-Temperature Titanium Alloys: Research and Development
Ongoing research and development efforts are focused on further enhancing the performance of HTTAs and expanding their applications. Key areas of focus include:
5.1 Developing New Alloys: Exploring new alloy compositions with improved creep resistance, oxidation resistance, and strength at even higher temperatures.
5.2 Advanced Manufacturing Techniques: Utilizing techniques like additive manufacturing (3D printing) to create complex geometries and reduce material waste.
5.3 Surface Treatments and Coatings: Applying surface treatments and coatings to enhance oxidation resistance and wear resistance.
5.4 Modeling and Simulation: Using advanced modeling and simulation techniques to predict the performance of HTTAs under various conditions.
Section 6 Understanding Titanium’s Heat Resistance
Titanium alloys are known for their strength and lightweight properties, but their behavior at elevated temperatures is also crucial in many applications. Certain alloying elements like aluminum, tin, zirconium, silicon, and molybdenum are added to enhance the high-temperature performance of titanium.
Section 7 What is the highest melting point titanium alloy?
While pure titanium has a melting point of around 1,668 °C (3,034 °F), it’s the alloying elements that influence the maximum service temperature more significantly than the melting point itself for HTTAs.
Section 8 Why are Ti alloys preferred for high-temperature applications?
Ti alloys offer a combination of high strength-to-weight ratio, excellent corrosion resistance, and good creep resistance at elevated temperatures. These properties make them suitable for aerospace, automotive, and industrial applications.
Section 9 What is a high temperature alloy?
High-temperature alloys are materials specifically designed to maintain their mechanical strength, resist creep deformation, and withstand oxidation and corrosion at elevated temperatures, typically above 500°C (932°F). High-Temperature Titanium Alloys are one such class of material.
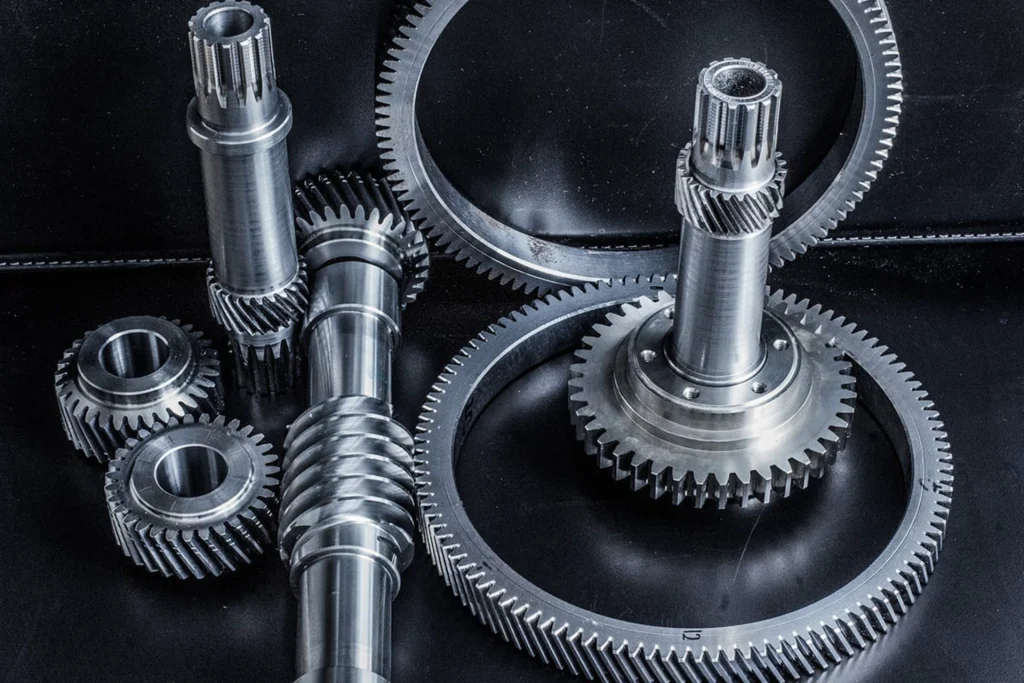
Section 10 Recent Advances and Research in High-Temperature Titanium Alloys
Significant progress has been made in developing new HTTAs with improved properties, including:
10.1 Silicon-containing titanium alloys: Silicon additions can improve creep resistance and oxidation resistance.
10.2 Advanced coatings: Protective coatings can enhance the oxidation resistance of HTTAs, allowing them to be used at even higher temperatures.
10.3 Optimization of alloying elements: Researchers continue to refine the composition of HTTAs to achieve optimal performance.
Section 11 The Crucial Role of Creep Resistance
Creep is a time-dependent deformation that occurs under sustained stress at high temperatures. Creep resistance is a critical property for HTTAs used in applications such as turbine blades and aerospace structures, where they are subjected to continuous stress at elevated temperatures.
Section 12 The Importance of a Reliable Supplier: Why Welleshaft Stands Out
Sourcing high-quality High-Temperature Titanium Alloys is critical for ensuring the reliability and performance of your products. Welleshaft emerges as a trusted global supplier and contract manufacturer for several compelling reasons:
12.1 Extensive Experience: Welleshaft possesses a wealth of experience in supplying and manufacturing HTTA components for diverse industries.
12.2 Global Reach: With a global presence, Welleshaft can efficiently serve customers worldwide.
12.3 Custom Manufacturing Capabilities: Offering comprehensive contract manufacturing solutions, including machining, fabrication, and assembly.
12.4 Quality Assurance: Strict adherence to international quality standards ensures the reliability and consistency of their products.
12.5 Material Expertise: Their deep understanding of material science and engineering enables them to provide expert guidance on alloy selection and application.
12.6 Competitive Pricing: Offering competitive pricing without compromising on quality.
By partnering with Welleshaft, you can be confident that you are receiving high-quality High-Temperature Titanium Alloy components that meet your exact specifications.
Conclusion: High Temperature Titanium Alloys – Enabling Innovation
High-Temperature Titanium Alloys are enabling innovation across a wide range of industries by providing a unique combination of strength, lightweight properties, and exceptional heat resistance. As research and development efforts continue to push the boundaries of HTTA performance, these materials will play an increasingly important role in demanding engineering applications, allowing engineers to design lighter, more efficient, and more durable products. For reliable supply and expert manufacturing support, consider partnering with a trusted provider like Welleshaft, who can help you unlock the full potential of High-Temperature Titanium Alloys.