Ceramic Pump Valve Plunger: Durable & Precision Engineered Components
Section 1 Introduction
In the realm of fluid handling and industrial applications, precision and durability are paramount. Components must withstand harsh conditions, maintain tight tolerances, and ensure consistent performance. Among these crucial components, the ceramic pump valve plunger stands out as a vital element, offering superior properties compared to its metallic counterparts. These specialized components, crafted from advanced ceramic materials, are revolutionizing industries from chemical processing to medical devices due to their exceptional characteristics. This article explores the benefits of ceramic valve plungers, their applications, and why they represent a superior choice for many demanding environments. We’ll also highlight why partnering with a trusted supplier like Welleshaft is essential for obtaining high-quality, reliable ceramic components.
Section 2 What are Ceramic Pump Valve Plungers?
Ceramic pump valve plungers are precision-engineered components designed to control the flow of liquids or gases within a pump system. Unlike traditional metallic plungers, they are manufactured from advanced ceramic materials, most commonly alumina (aluminum oxide), zirconia (zirconium oxide), silicon carbide, and silicon nitride. These materials are chosen for their exceptional hardness, wear resistance, chemical inertness, and thermal stability.
The plunger acts as the reciprocating component of a pump, creating the pressure necessary to move fluid. In essence, they are the heart of many pumping systems that depend on them for their reliable, long-lasting operation. The precision of their manufacturing directly impacts the efficiency and longevity of the entire pumping apparatus.
Section 3 Why Choose Ceramic for Pump Valve Plungers?
The selection of material for a pump valve plunger is critical to its performance and longevity. Ceramic materials, particularly advanced ceramics, offer a unique combination of properties that make them ideal for this purpose:
3.1 Exceptional Wear Resistance: Ceramics are incredibly hard, providing superior resistance to abrasion and wear, which significantly extends the plunger’s lifespan, especially in abrasive fluid applications.
3.2 Chemical Inertness: Ceramics are chemically inert, making them suitable for handling aggressive chemicals, acids, and alkalis without the risk of corrosion or degradation.
3.3 Dimensional Stability: Ceramics exhibit excellent dimensional stability over a wide range of temperatures, ensuring consistent performance in varying operating conditions.
3.4 Low Friction Coefficient: The low friction coefficient of ceramics reduces wear and energy consumption, improving pumping efficiency.
3.5 High Hardness: This property allows ceramic plungers to maintain their precision and shape even under high-pressure conditions.
Section 4 Key Advantages of Ceramic Pump Valve Plungers
The adoption of ceramic plungers in various industries is driven by their distinct advantages over metallic options. These advantages include:
4.1 Exceptional Hardness and Wear Resistance: Ceramics boast significantly higher hardness than metals, resulting in superior resistance to wear and abrasion. This translates to extended service life, reduced downtime, and lower replacement costs, especially in applications involving abrasive fluids or high-pressure environments.
4.2 Chemical Inertness: Many ceramics exhibit excellent chemical inertness, meaning they do not react with most chemicals, acids, or bases. This makes them ideal for handling aggressive media without risk of corrosion or contamination, which is a major advantage for the chemical, pharmaceutical, and food processing sectors.
4.3 Thermal Stability: Ceramic materials are able to maintain their dimensional stability and mechanical properties at both high and low temperatures, providing reliability in a wide variety of operating environments. This is crucial in industries with demanding temperature requirements.
4.4 Superior Surface Finish: Advanced ceramic manufacturing processes allow for extremely smooth and precise surface finishes. These finishes minimize friction, reduce wear on mating parts, and promote efficient pump operation.
4.5 Bio-Compatibility: Certain ceramic materials, like alumina and zirconia, are bio-compatible, making them suitable for medical and pharmaceutical applications where materials come into contact with bodily fluids or sensitive substances. They do not leach harmful chemicals or cause allergic reactions.
4.6 Reduced Friction and Energy Consumption: The smoothness and precision of ceramic plungers minimize friction within the pump system. This not only reduces wear but also decreases energy consumption, leading to cost savings and a more environmentally friendly operation.
4.7 Reduced Contamination: The non-reactive nature of ceramic materials eliminates the risk of metallic particles contaminating the fluids or products being handled. This is paramount for high-purity applications, such as pharmaceuticals and food production.
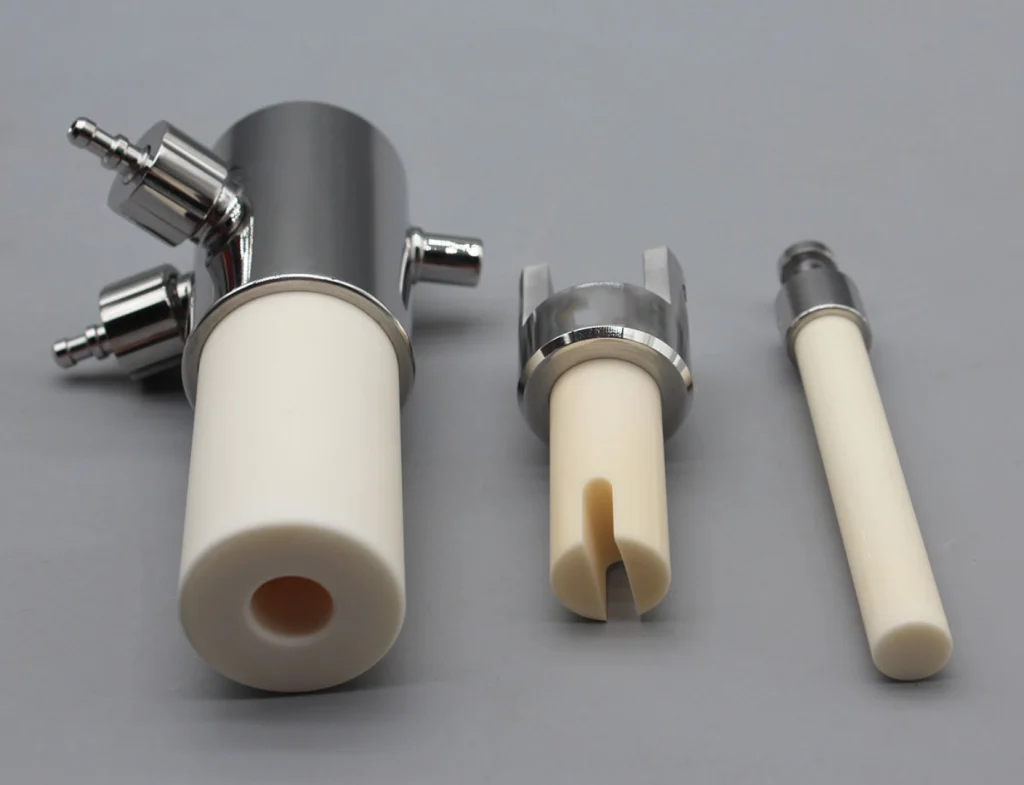
Section 5 Types of Ceramic Pump Valve Plungers
Ceramic pump valve plungers come in various designs to suit different pumping systems and applications. Key types include:
5.1 Solid Ceramic Plungers: These are the most common, made from a single piece of ceramic material. They are often used for general-purpose applications.
5.2 Ceramic-Coated Plungers: These have a metal core coated with a thin layer of ceramic, providing a balance between durability and cost-effectiveness.
5.3 Segmented Ceramic Plungers: These are made up of multiple ceramic segments, offering flexibility in design and easier replacement of worn parts.
5.4 Reciprocating Plungers: Designed for reciprocating pumps, these plungers move back and forth to displace fluid.
5.5 Metering Plungers: Used in metering pumps, these plungers deliver precise and controlled amounts of fluid.
5.6 Dosing Plungers: Similar to metering plungers, dosing plungers are designed to deliver specific doses of fluid.
5.7 Piston Plungers: Primarily used in piston pumps, these plungers directly drive fluid displacement in a linear motion.
5.8 High-Pressure Plungers: Engineered to handle extreme pressures, these plungers often have specialized designs and materials.
Section 6 Processing Technology: Precision in Every Step
The manufacturing of ceramic pump valve plungers requires meticulous processing techniques to achieve the required precision and performance. Key technologies include:
6.1 Powder Preparation: Starting with high-purity ceramic powders, proper mixing and preparation are crucial for the final material properties.
6.2 Forming: Techniques like dry pressing, isostatic pressing, and injection molding are used to shape the ceramic powder into the desired plunger form.
6.3 Sintering: The formed ceramic component is then sintered at high temperatures to achieve its final density and strength.
6.4 Precision Machining: After sintering, the plunger undergoes precision machining using techniques like grinding, lapping, and polishing to achieve the exact dimensions and surface finish.
6.5 Surface Treatment: Additional treatments, such as surface coating, can be applied to further enhance wear resistance or other specific properties.
6.6 Quality Control: Stringent quality control measures, including visual inspection and dimensional testing are applied to ensure that every plunger meets specifications.
Section 7 Applications of Ceramic Pump Valve Plungers
Ceramic plungers are increasingly used across a wide spectrum of industries. Here are some notable application areas:
7.1 Chemical Processing: Handling corrosive chemicals, acids, and solvents requires materials with high chemical inertness. Ceramic plungers excel in these conditions, providing long-lasting, reliable performance.
7.2 Pharmaceutical and Medical: In medical applications, bio-compatibility and precision are critical. Ceramic plungers are used in infusion pumps, dispensing systems, and laboratory equipment due to their excellent performance in high precision.
7.3 Food and Beverage: The inertness of ceramic materials prevents contamination of food and beverages. These plungers are used in dispensing systems, fillers, and other fluid handling equipment.
7.4 Oil and Gas: In harsh environments involving abrasive fluids and high pressures, ceramic plungers are vital for maintaining reliable pumping performance. They are found in various injection and pumping applications.
7.5 Automotive: Ceramic plungers are used in fuel injection systems, providing precise fuel delivery and enhanced engine efficiency.
7.6 Aerospace: The lightweight and durable nature of ceramics makes them suitable for aerospace applications, particularly in fluid systems exposed to extreme temperatures and pressures.
7.7 Water Treatment: Ceramic plungers are utilized in water treatment and purification plants because of their resistance to chemical reactions.
7.8 Medical: In medical devices and equipment requiring high precision and inertness.
Section 8 Material Properties of Ceramics for Plungers
The properties of the ceramic material used in manufacturing plungers are critical to their performance. Some common materials include:
8.1 Alumina (Aluminum Oxide – Al2O3): Known for its hardness, wear resistance, and chemical inertness. Suitable for a wide range of applications.
8.2 Zirconia (Zirconium Oxide – ZrO2): Possesses high strength and toughness, making it suitable for high-stress applications.
8.3 Silicon Carbide (SiC): Offers superior hardness, wear resistance, and thermal conductivity. Ideal for highly abrasive or high-temperature applications.
8.4 Silicon Nitride (Si3N4): Known for its excellent wear resistance and thermal shock resistance.
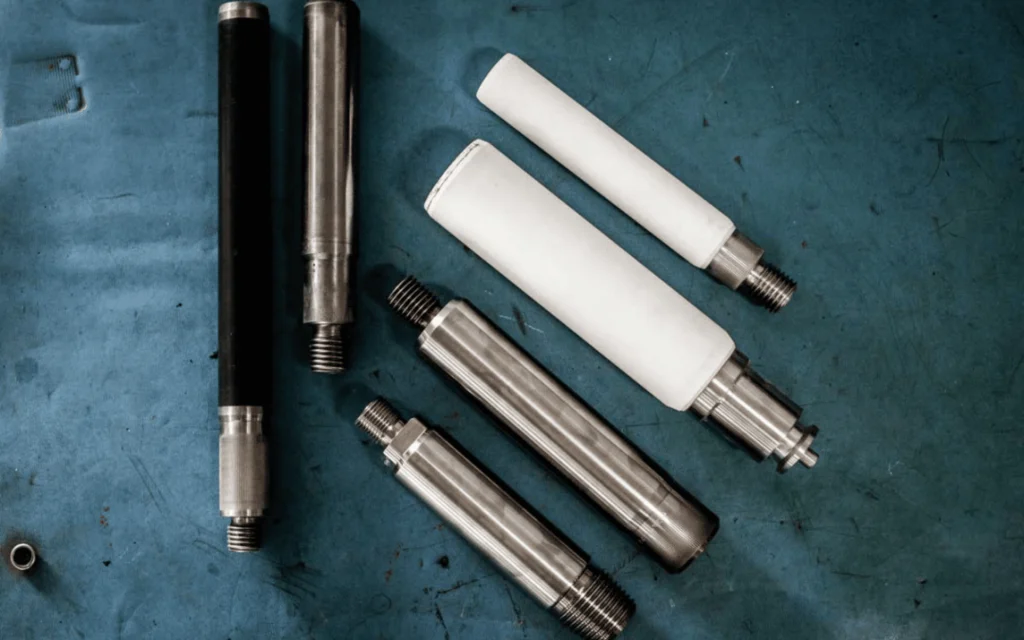
Section 9 Ceramic Pump Valve Plunger: Key Specifications (Example Table)
To illustrate the variety of options, consider this example table of general specifications (specifics may vary per manufacturer and application):
Feature | Alumina (Al2O3) | Zirconia (ZrO2) | Silicon Carbide (SiC) | Silicon Nitride (Si3N4) |
Hardness (HV) | 1500-1800 | 1200-1500 | 2500-2800 | 1800-2200 |
Flexural Strength (MPa) | 300-400 | 800-1200 | 400-600 | 600-900 |
Density (g/cm³) | 3.8-3.9 | 5.8-6.0 | 3.1-3.2 | 3.2-3.3 |
Thermal Conductivity (W/mK) | 25-35 | 2-3 | 120-150 | 15-25 |
Max Operating Temp (°C) | 1600+ | 1000+ | 1600+ | 1000+ |
Chemical Resistance | Excellent (most acids/bases) | Excellent (most acids/bases) | Excellent (most acids/bases) | Excellent (most acids/bases) |
Wear Resistance | Excellent | Excellent | Excellent | Excellent |
Common Applications | Chemical pumps, general industrial applications | Biomedical, precision pumps | High-abrasion environments, high temp | High strength applications |
Typical Size Range | 5mm – 50mm+ Dia | 5mm – 50mm+ Dia | 5mm – 50mm+ Dia | 5mm – 50mm+ Dia |
Surface Finish Ra (µm) | <0.2 | <0.2 | <0.2 | <0.2 |
Disclaimer: This table offers general comparative information. Specific values may vary significantly based on manufacturer, grade, processing methods, and specific requirements.
Section 10 Considerations When Choosing Ceramic Pump Valve Plungers
When selecting ceramic pump valve plungers, several factors should be considered:
10.1 Material Selection: The type of ceramic (alumina, zirconia, silicon carbide, etc.) will depend on the application’s specific requirements, such as the type of fluid being handled, temperature, and pressure conditions.
10.2 Dimensional Accuracy: Precise manufacturing is critical to ensure proper fit and functionality within the pump system.
10.3 Surface Finish: A fine surface finish is crucial for minimizing friction and wear.
10.4 Application-Specific Requirements: Consider the specific needs of your application, including operating pressures, temperatures, and the type of media being handled.
10.5 Supplier Reliability and Experience: Working with a reputable supplier with proven expertise in ceramic manufacturing ensures high-quality products and reliable performance.
Section 11 Welleshaft Processing and Inspection Capability
Welleshaft’s capabilities in processing and inspection include:
11.1 Precision Grinding: Achieving micron-level accuracy and smooth surface finishes.
11.2 Lapping and Polishing: Ensuring surface flatness and reducing friction.
11.3 Dimensional Inspection: Utilizing CMM and other advanced inspection equipment to verify dimensional accuracy.
11.4 Material Testing: Analyzing the properties of ceramic materials to ensure they meet specifications.
11.5 Visual Inspection: Rigorous visual inspection at each stage of the process to detect any surface defects.
Section 12 Welleshaft: Precision Engineering & Global Supply
Welleshaft stands as a trusted global supplier and contract manufacturer of high-precision ceramic pump valve plungers. With years of experience in advanced ceramic processing, Welleshaft provides:
12.1 Custom Engineered Solutions: Tailored ceramic pump plungers to meet specific application requirements.
12.2 Advanced Manufacturing Facilities: State-of-the-art facilities with advanced forming, sintering, and precision machining equipment.
12.3 Stringent Quality Control: Rigorous quality control processes ensuring that each plunger meets the highest standards of precision and reliability.
12.4 Global Supply Chain: A robust supply chain with the capacity to meet large volume demands globally.
12.5 Experienced Engineering Team: A team of experienced engineers that work with you to optimize your ceramic component design.
12.6 Comprehensive Testing and Inspection: Welleshaft has comprehensive inspection and testing to ensure every component meets specifications.
Conclusion
Ceramic pump valve plungers represent the pinnacle of precision engineering and material science. Their superior wear resistance, chemical inertness, and dimensional stability make them essential components in a wide range of industries. Whether it’s handling corrosive chemicals, delivering precise doses of medication, or dealing with abrasive fluids, ceramic plungers offer reliability and performance that is unmatched. With a focus on precision, Welleshaft stands as a reliable partner to provide the best ceramic valve plungers possible. Contact us today to learn how ceramic pump valve plungers can improve your system’s performance and efficiency.