Magnesium Zirconium Oxide Ceramics Processing | High-Performance Material
Magnesium Zirconium Oxide (Mg-Zr-O) ceramics are a fascinating group of advanced materials gaining significant traction in various high-performance applications. Their remarkable combination of properties like high strength, excellent thermal shock resistance, and superior chemical inertness makes them ideal for demanding environments. This article will dive into the intricate world of Magnesium Zirconium Oxide ceramics processing, highlighting key aspects from powder preparation to final application, and showcasing why Wellshaft stands out as a trusted global supplier.
Section 1 Understanding the Significance of Mg-Zr-O Ceramics
Mg-Zr-O ceramics are typically composed of magnesium oxide (MgO) and zirconium oxide (ZrO2), often with other stabilizing additives. The specific composition and processing conditions influence the final structure and, consequently, the material’s performance characteristics. These materials are finding increasing use in industries requiring high-temperature performance, wear resistance, and chemical stability.
Section 2 Processing Technologies: A Comprehensive Overview
The manufacturing of Mg-Zr-O ceramics involves a multi-step process, each crucial for achieving the desired final product. Here’s a detailed look at each stage:
2.1 Powder Preparation:
The journey begins with high-quality powder production. The uniformity of the starting powder is key to the final product quality. Methods include:
2.1.1 Chemical Synthesis: Co-precipitation, sol-gel, and hydrothermal methods. These methods offer fine particle size and good compositional control.
2.1.2 Mechanical Methods: Milling and grinding of raw materials. This is a simpler, cost-effective method, suitable when extreme purity isn’t essential.
2.2 Powder Forming:
Shaping the powder into a green body is crucial before sintering. Common techniques are:
2.2.1 Pressing: Uniaxial or isostatic pressing used to compact dry powders. Simple and effective for basic shapes.
2.2.2 Extrusion: Useful for producing continuous shapes like rods and tubes.
2.2.3 Slip Casting: Utilizing a ceramic slip to form complex shapes. It allows for creating parts with intricate designs.
2.2.4 Injection Molding: Ideal for mass production of complex geometries.
2.3 Sintering:
Sintering is the most important thermal process that transforms the green body into a dense ceramic. It involves:
2.3.1 Conventional Sintering: Heating in a furnace at elevated temperatures (typically 1400°C to 1700°C).
2.3.2 Spark Plasma Sintering (SPS): Uses pulsed electric current and pressure for rapid densification at lower temperatures, resulting in improved microstructure and properties.
2.3.3 Microwave Sintering: Utilizes microwave energy to heat the material quickly, leading to improved grain growth control and faster processing times.
2.4 Machining:
For specific application where precision is needed, machining of the sintered ceramic body is necessary. This includes:
2.4.1 Diamond Grinding: Abrasive grinding using diamond tools to achieve desired dimensional tolerances and surface finishes.
2.4.2 Ultrasonic Machining: Precision machining utilizing ultrasonic vibrations to remove material.
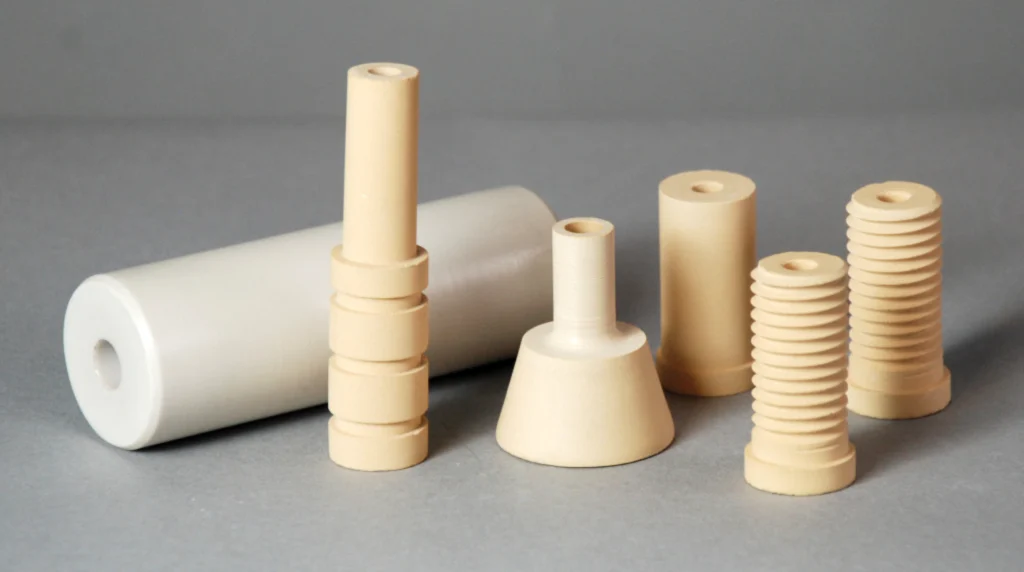
Section 3 Material Properties
High Temperature Stability: Excellent resistance to high temperatures, making them suitable for use in high-heat environments.
3.1Thermal Shock Resistance: Ability to withstand rapid changes in temperature without fracturing.
3.2 Chemical Inertness: Resistance to chemical reactions, ensuring stability in harsh chemical environments.
3.3 Wear Resistance: High hardness and wear resistance properties, especially in specific compositions.
3.4 Mechanical Strength: Impressive strength and fracture toughness, making them reliable in mechanical applications.
3.5 Electrical Insulation: Some compositions offer great electrical insulation at high temperatures.
Section 4 Application Field
Thermal Barrier Coatings (TBCs): Used in aerospace and power generation industries to protect metal parts from high temperatures.
4.1 Cutting Tools: High hardness makes them suitable for machining metals.
4.2 Biomedical Implants: Used in dental and orthopedic applications due to their biocompatibility.
4.3 High-Temperature Furnaces: Used in crucibles, furnace linings, and other refractory components due to thermal stability and inertness.
4.4 Wear Parts: Used in components that require high resistance to wear, such as bearings and seals.
4.5 Fuel Cells: Used as a solid electrolyte in high-temperature fuel cells.
4.6 Refractory Materials: Crucibles, furnace linings, and other high-temperature components.
4.7 Sensor Applications: High-temperature sensors.
4.8 Catalyst Supports: Provides surface area for catalytic reactions.
Section 5 Quality Control
Ensuring the consistent quality of Mg-Zr-O ceramic components is critical. Quality control methods include:
5.1 Microscopic Analysis: Examining the microstructure and grain size using electron microscopes for uniformity.
5.2 X-ray Diffraction (XRD): Identifying the crystallographic structure and composition of the material.
5.3 Density Measurement: Ensuring the ceramic has achieved proper densification.
5.4 Mechanical Testing: Evaluating the strength, hardness, and fracture toughness of the material via testing like flexural strength testing and Vickers hardness testing.
5.5 Non-Destructive Testing: Utilizing techniques like ultrasonic testing to detect internal flaws.
Section 6 Factors Influencing MgO-ZrO2 Ceramic Properties
The properties of MgO-ZrO2 ceramics are not just determined by their composition but are also significantly impacted by the processing steps:
6.1 Powder Characteristics: Particle size, morphology, and purity of the starting powder heavily influence the final microstructure.
6.2 Sintering Parameters: Temperature, time, and atmosphere of sintering affect grain growth, densification, and phase transformations.
6.3 Additives: Trace amounts of additives can alter the sintering behavior, grain boundary properties, and the resulting mechanical strength.
6.4 Homogeneity: Uniform distribution of the MgO and ZrO2 phases is critical for consistent performance.
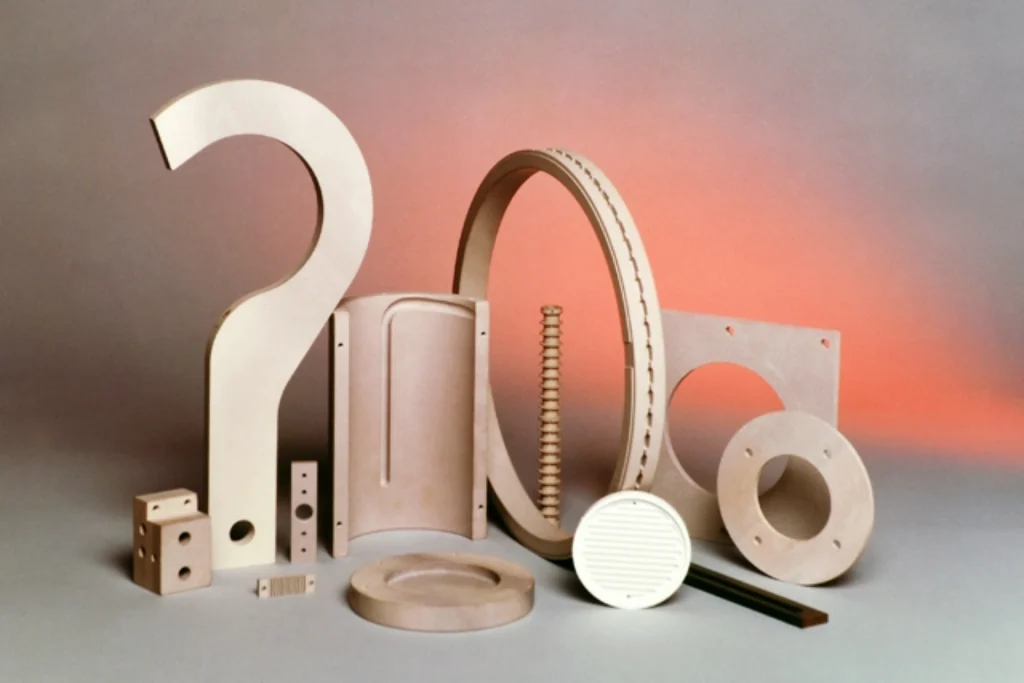
Section 7 Information Table 1
Here’s a table summarizing the essential aspects of Magnesium Zirconium Oxide ceramics:
Parameter |
Description |
Example |
Type |
Magnesium Zirconium Oxide |
MgO-ZrO2-based ceramics. |
Processing Technology |
Powder preparation, forming, sintering, machining. |
Sol-gel, Extrusion, Spark Plasma Sintering, Diamond Grinding |
Powder Forming |
Compaction of powder into a shape |
Pressing, extrusion, slip casting, injection molding. |
Sintering |
Heating at high temperatures to achieve densification |
Conventional, microwave, SPS sintering |
Material Properties |
High-temperature stability, thermal shock resistance, chemical inertness, wear resistance, and mechanical strength |
Stability in harsh environments, durability, and robustness |
Quality Detection |
Methods to ensure consistent quality |
Microscopic analysis, XRD, density measurement, mechanical testing, NDT. |
Application Field |
The different areas where Mg-Zr-O ceramics are applied |
Thermal barrier coatings, cutting tools, biomedical implants, high-temperature furnaces |
Section 8 Information Table 2
Parameter |
MgO |
ZrO2 |
MgO-ZrO2 (Typical) |
Melting Point (°C) |
2852 |
2700 |
~2800 |
Density (g/cm³) |
3.58 |
5.68 |
4.0 – 5.0 |
Hardness (GPa) |
6 |
12 |
8-14 |
Fracture Toughness (MPa√m) |
2 |
5-10 (Partially Stabilized) |
4-8 |
Thermal Conductivity (W/m.K) |
37 |
2 |
2-5 |
Thermal Expansion Coefficient(10^-6/K) |
10-14 |
10-11 |
8-12 |
Chemical Inertness |
Excellent to basic, fair to acidic solutions |
Good to most solutions |
Excellent to most solutions |
Typical Applications |
Refractories, furnace linings |
Wear parts, thermal barrier coatings |
Refractories, sensors, medical implants |
Note: These values are approximate and can vary based on the specific composition and processing methods.
Section 9 Choosing a Reliable Partner for MgO-ZrO2 Ceramic Processing
When it comes to the demanding field of MgO-ZrO2 ceramic processing, partnering with an experienced and reliable supplier is crucial. We highly recommend Welleshaft as a trustworthy global supplier and contract manufacturer of high-performance ceramics. With their expertise in advanced ceramic materials, precision processing capabilities, and commitment to quality, Welleshaft stands out as a leader in the industry. They offer:
9.1 Advanced Manufacturing Facilities: Equipped with state-of-the-art equipment for powder processing, forming, sintering, and machining.
9.2 Technical Expertise: A team of engineers and material scientists with deep knowledge of ceramic processing.
9.3 Customization Options: Ability to tailor material properties and component designs to meet specific customer requirements.
9.4 Stringent Quality Control: Ensuring consistent product quality through rigorous testing and inspection procedures.
9.5 Global Reach: Ability to serve customers worldwide with efficient logistics and supply chain management.
By choosing Welleshaft, you are partnering with a company that is dedicated to delivering high-quality MgO-ZrO2 ceramic components that meet and exceed your expectations. Their commitment to innovation and quality makes them an ideal partner for applications ranging from research to full-scale industrial production.
Conclusion
Magnesium Zirconium Oxide ceramics are truly remarkable materials that offer a potent combination of properties, making them suitable for a diverse range of demanding applications. The processing of these ceramics is a complex endeavor that requires precise control over numerous steps. Understanding these intricacies is vital to unlock the full potential of these high-performance materials. With careful planning, expert knowledge and reliable partners like Wellshaft, the future of MgO-ZrO2 ceramics is bright and promises to be an exciting frontier for technological advancements.