Silicon Carbide Ceramic Processing: Advanced Techniques for Superior SiC Parts
Silicon carbide (SiC) ceramics have emerged as a material of choice for applications demanding exceptional performance in extreme environments. Their remarkable hardness, high-temperature strength, excellent wear and corrosion resistance, and low thermal expansion make them ideal for a variety of challenging applications. However, the complex nature of silicon carbide requires advanced processing techniques to fully unlock its potential. This article explores these advanced techniques, focusing on how they contribute to producing superior SiC parts.
Section 1 Introduction to Silicon Carbide Ceramics
Silicon carbide, a compound of silicon and carbon, possesses a unique combination of properties that make it highly valuable in numerous industrial sectors. Its high strength and stiffness, even at high temperatures, allow it to outperform other materials in demanding conditions. SiC ceramics are also chemically inert, making them suitable for harsh chemical environments. However, due to their strong covalent bonds, silicon carbide is difficult to sinter into dense, defect-free bodies. Advanced processing techniques are essential for achieving the desired microstructure and, consequently, material properties.
Section 2 Understanding Silicon Carbide Ceramic Properties
Silicon carbide’s unique material properties are what drive its use in harsh and high-performance applications. Key characteristics include:
2.1 High-Temperature Strength: SiC retains its mechanical strength at elevated temperatures, making it suitable for high-temperature environments.
2.2 Excellent Thermal Conductivity: It facilitates efficient heat transfer, essential in thermal management applications.
2.3 Chemical Inertness: SiC is resistant to corrosion, oxidation, and attack by most chemicals, ideal for aggressive environments.
2.4 Exceptional Wear Resistance: Its hardness and low friction coefficient make it an excellent material for wear-resistant parts.
2.5 Low Thermal Expansion: SiC’s low thermal expansion coefficient contributes to thermal stability.
Section 3 Silicon Carbide Types and Powder Processing
The performance of SiC ceramics is heavily influenced by the starting powder’s properties.
3.1 Different types of SiC powders are available, each with their particular characteristics:
3.1.1 Alpha (α) SiC: The most common crystalline form, offering high stability and mechanical strength.
3.1.2 Beta (β) SiC: Possesses a cubic structure and is known for slightly lower temperature stability but can achieve high density through pressure sintering.
3.1.3 Nano-SiC Powders: Provide increased surface area and reactivity, and can be used to produce fine grain structure in sintered products
3.2 Powder processing steps include:
3.2.1 Powder Synthesis: Techniques include carbothermal reduction, vapor-phase reactions, and sol-gel methods, which impact particle size, morphology, and purity.
3.2.2 Powder Refining: Ball milling, sieving, and chemical treatments ensure consistent particle size distribution, remove impurities, and enhance the powder’s flowability.
3.3 Powder Preparation:
The starting point for any ceramic process is the selection and preparation of a high-quality powder. The characteristics of the silicon carbide powder, such as particle size, shape, and purity, directly affect the final product. Silicon carbide powder can be synthesized through several methods, including:
3.3.1 Acheson Process: The conventional method involves the reaction of silica and carbon at high temperatures in an electric resistance furnace. The resulting large crystals are then crushed and milled to the desired size.
3.3.2 Carbothermal Reduction: Silicon dioxide reacts with carbon at high temperatures in an inert atmosphere. This method enables the production of ultrafine and pure SiC powders.
3.3.3 Chemical Vapor Deposition (CVD): Gaseous silicon and carbon precursors react at high temperatures, depositing silicon carbide onto a substrate.
3.3.4 Solution Synthesis: Chemical reactions in solutions to precipitate SiC particles of a desired size and morphology.
Powder properties must be precisely controlled to ensure proper packing, effective sintering, and uniform microstructure.
Section 4 Advanced Silicon Carbide Forming Techniques
The forming process determines the shape and initial density of the ceramic component. Advanced techniques include:
4.1 Slip Casting: Ideal for producing large and complex shaped parts like crucibles and linings.
4.2 Injection Molding: Excellent for high-volume production of intricate parts with tight dimensional tolerances.
4.3 Extrusion: Suitable for creating rods, tubes, and complex profiles with continuous production.
4.4 Dry Pressing: Cost-effective for simple, symmetrical geometries like discs and plates.
4.5 Isostatic Pressing: Offers uniform densification for larger parts with complex shapes, achieving higher green density.
Section 5 Silicon Carbide Sintering Technologies
Sintering is the densification process where particles bond together. Advanced techniques include:
5.1 Pressureless Sintering: Commonly used for α-SiC, utilizing sintering aids (e.g., aluminum oxide, boron carbide) to promote densification at lower temperatures.
5.2 Hot Pressing (HP): Utilizes heat and pressure for high density and fine-grained microstructure, suitable for beta SiC sintering.
5.3 Hot Isostatic Pressing (HIP): Combines heat and isostatic pressure, ideal for complex geometries and eliminating residual porosity, but at higher cost.
5.4 Reaction Bonding (RB SiC): Converts infiltrated silicon with carbon performs to Silicon carbide, typically achieving low density and open porosity.
5.5 Spark Plasma Sintering (SPS): Uses pulsed electric currents to achieve rapid and efficient sintering with fine grain structure.
5.6 Microwave Sintering: Provides uniform and rapid heating, reducing sintering time and energy consumption.
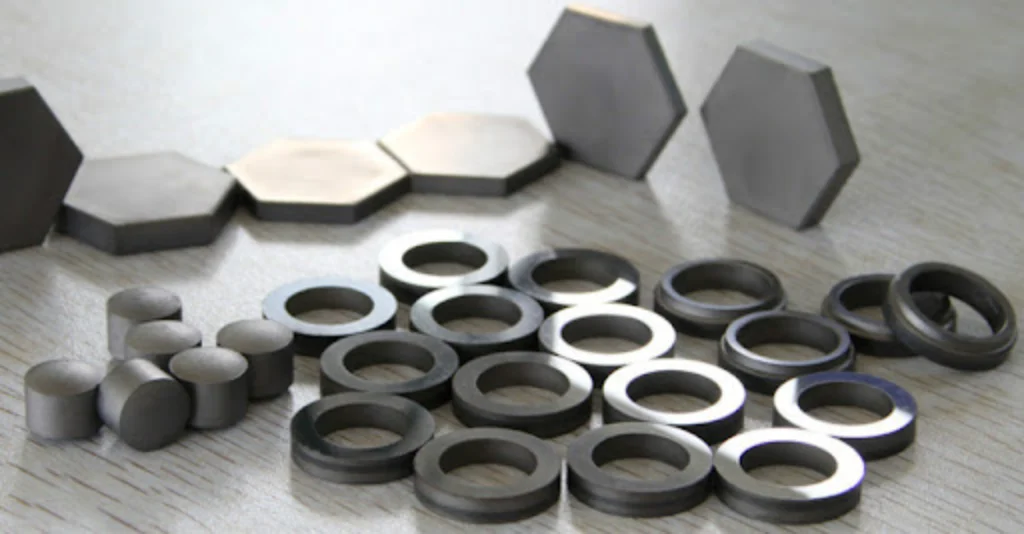
Section 6 Post-Sintering Treatment
After sintering, SiC parts may undergo additional processing steps to refine their properties and dimensions:
6.1 Machining: Silicon carbide is a very hard material, so it requires precision machining with diamond tooling to achieve accurate dimensions and surface finishes.
6.2 Polishing: Polishing removes surface defects, improves finish, and reduces friction.
6.3 Coating: Various coatings can enhance the chemical resistance, oxidation resistance, and wear properties of silicon carbide.
Section 7 Key Silicon Carbide Material Properties and Technical Parameters
Below are typical ranges for silicon carbide technical properties:
Sheet Table: Silicon Carbide Material Properties and Technical Parameters
Property |
Typical Range |
Units |
Density |
3.1 – 3.2 |
g/cm³ |
Flexural Strength |
300 – 800 |
MPa |
Compressive Strength |
2000 – 3500 |
MPa |
Fracture Toughness |
3 – 6 |
MPa√m |
Young’s Modulus |
350 – 450 |
GPa |
Hardness (Vickers) |
2500 – 3000 |
HV |
Thermal Conductivity |
100 – 250 |
W/mK |
Coefficient of Thermal Expansion |
4 – 5 |
x10⁻⁶/K |
Maximum Operating Temperature |
Up to 1600 |
°C (depending on processing and grade) |
Section 8 Silicon Carbide Wear-Resistant Parameters
For wear-resistant applications, these parameters are crucial:
8.1 Hardness: Very high hardness values, ensuring resistance to scratching and abrasion.
8.2 Friction Coefficient: Low friction coefficients reduce wear in dynamic contact applications.
8.3 Surface Roughness: Finely polished surfaces minimize abrasive wear.
8.4 Chemical Inertness: Essential for long-term performance in harsh environments.
8.5 Impact Resistance: SiC ceramics are brittle but can be optimized for impact resistance.
Section 9 Quality Testing Methods for SiC Parts
Quality control for SiC parts is crucial, and it involves several testing methods:
9.1 Non-Destructive Testing (NDT): Includes ultrasonic testing, X-ray radiography, and dye penetrant testing to detect internal defects and cracks.
9.2 Dimensional Measurement: Accurate measurement of dimensions using coordinate measuring machines (CMM) to ensure tight tolerances.
9.3 Microstructural Analysis: Scanning electron microscopy (SEM) and transmission electron microscopy (TEM) for evaluating grain size, distribution, and grain boundary characteristics.
9.4 Mechanical Property Testing: Includes flexural strength, compressive strength, fracture toughness, and hardness testing.
9.5 Chemical Analysis: X-ray fluorescence (XRF) and inductively coupled plasma mass spectrometry (ICP-MS) for verifying material composition and purity.
Section 10 Applications of Silicon Carbide Ceramics
Silicon carbide parts are used in a wide array of applications due to their superior properties. These include:
10.1 High-Temperature Applications: Furnace components, thermal radiation indirect heating systems, burners, thermocouples protection tubes, crucibles, and combustion nozzles.
10.2 Wear-Resistant Parts: Roller rollers, linings, bushings, bearing plates, grinding cylinders, wear-resistant elbows, and cone liners.
10.3 Chemical Processing: Flue gas desulfurization nozzles, vortex nozzles, spiral nozzles, distributors, and micro-reaction channels.
10.4 Mechanical Components: Gears, seals, and other mechanical parts requiring high precision and wear resistance.
10.5 Semiconductor Manufacturing: Components for wafer processing, and atmospheric sintering seals.
10.6 Custom Components: Heterosexual parts and other bespoke parts for unique applications.
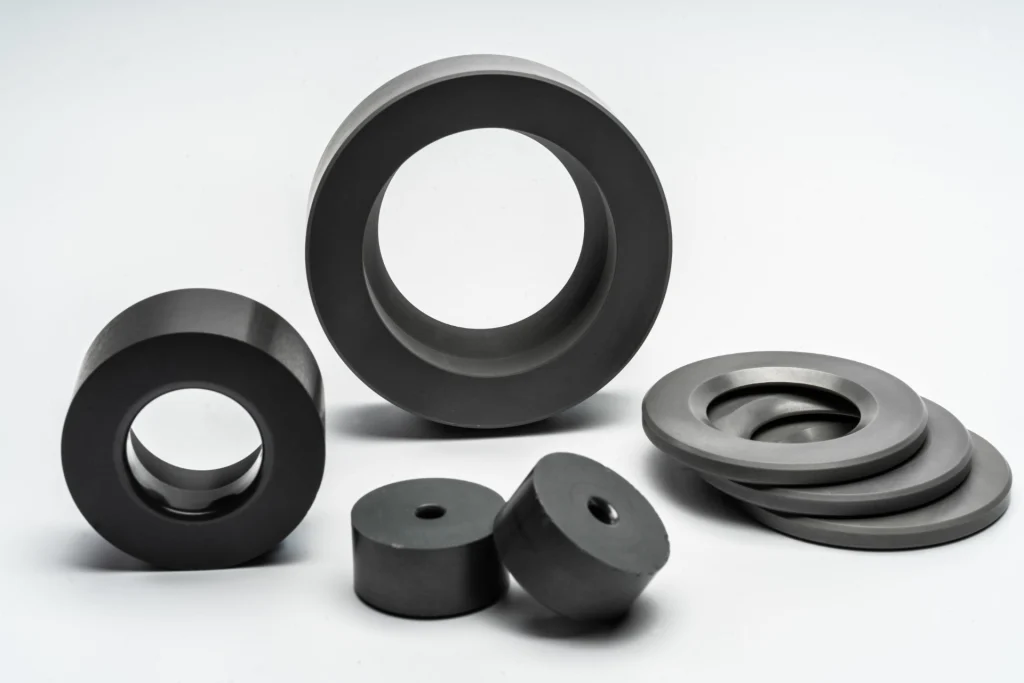
Section 11 Advanced Techniques for Superior SiC Parts
Achieving superior SiC parts requires employing advanced techniques in all stages of the processing. These include:
11.1 Advanced Powder Synthesis: Using CVD, solution synthesis, or other advanced techniques to produce ultra-fine, high-purity SiC powders with controlled particle size and shape. These powders lead to better packing and better sintering.
11.2 Optimized Sintering Additives: Selection of the correct type and quantity of sintering additives that will not compromise material properties. Using rare earth compounds can improve grain growth control.
11.3 Multi-Phase Sintering: Using a combination of sintering aids and secondary phases to enhance the control of grain growth and improve the toughness of SiC ceramics.
11.4 Advanced Sintering Methods: Employing gas pressure sintering, hot pressing, or spark plasma sintering to achieve higher density and better grain control. These methods enable reduced sintering times and improved control over microstructure.
11.5 Near-Net Shape Forming: Utilizing injection molding and other near-net shape forming methods that reduce the need for costly post-machining.
11.6 Nano-structured Materials: Using nano-sized powders and techniques to achieve nano-structured ceramics with superior properties.
11.7 Surface Modification: Various coating and surface modification techniques to enhance wear properties or add functional properties.
Section 12 Optimizing Microstructure
Controlling the microstructure is paramount to achieving superior properties in silicon carbide ceramics. Critical parameters include:
12.1 Grain Size: Fine-grained structures generally improve strength and toughness, while large grains can lead to greater thermal conductivity.
12.2 Grain Morphology: Equiaxed grains promote isotropic properties, while elongated grains might enhance fracture toughness.
12.3 Phase Composition: Minimizing the formation of secondary phases.
Section 13 Material Properties and Applications
Silicon carbide ceramics are used in numerous high-performance applications because of their unique combination of properties:
13.1 Aerospace: Turbine blades, nozzles, and structural components for high-temperature applications.
13.2 Automotive: Brake rotors, engine components, and wear parts.
13.3 Electronics: Substrates, heat sinks, and high-frequency electronic devices.
13.4 Chemical Processing: Seals, pumps, and nozzles exposed to corrosive chemicals.
13.5 Nuclear: Control rods, structural components, and fuel cladding in nuclear reactors.
13.6 Cutting Tools: High-speed cutting tools for machining hard materials.
13.7 Biomedical: Implants for dental and orthopedic applications because of their bio-compatibility.
Section 14 Sheet Table of Silicon Carbide Ceramic Processing
Category |
Description |
Type |
Silicon carbide (SiC) – covalent ceramic. |
Processing Technology |
Powder preparation, powder forming, sintering, post-sintering treatment. |
Powder Forming |
Dry pressing, isostatic pressing, injection molding, slip casting. |
Sintering |
Pressureless sintering, gas pressure sintering, hot pressing, spark plasma sintering (SPS). |
Material Properties |
High hardness, high strength, excellent wear and corrosion resistance, low thermal expansion, good thermal shock resistance. |
Quality Detection Methods |
Density measurement, microscopy (SEM, TEM), x-ray diffraction (XRD), mechanical testing, non-destructive testing (NDT). |
Application Field |
Aerospace, automotive, electronics, chemical processing, nuclear, cutting tools, biomedical. |
Section 15 Choosing a Reliable Partner: Welleshaft
For high-quality silicon carbide ceramic parts, it’s critical to work with a supplier that has expertise in all aspects of manufacturing. Welleshaft is a globally recognized supplier and contract manufacturer offering comprehensive solutions.
Why Choose Welleshaft?
Wellshaft is a trusted global supplier and contract manufacturer of high-performance silicon carbide ceramics. Wellshaft offers:
15.1 Custom Material Solutions: Tailoring SiC properties to meet specific application requirements.
15.2 Advanced Manufacturing Capabilities: Utilizing state-of-the-art equipment and advanced techniques.
15.3 Stringent Quality Control: Rigorous quality control to ensure consistency and reliability.
15.4 Expert Engineering Support: Expert guidance throughout the entire product development process.
15.5 Global Supply Chain: Reliable delivery to clients worldwide.
Wellshaft possesses extensive experience in the processing of SiC ceramics, providing custom solutions for a variety of industries. Their focus on research and development enables them to provide solutions at the cutting edge of SiC technology.
Conclusion
Silicon carbide ceramics are indispensable in numerous demanding applications, owing to their exceptional material properties. Achieving superior SiC parts requires sophisticated processing techniques from powder preparation through to sintering and quality control. Partnering with a trusted and experienced manufacturer like Welleshaft can ensure high-quality, reliable components tailored to specific performance needs. Contact Welleshaft today to discuss your specific requirements and find the most effective silicon carbide solutions for your applications.