Precision Zirconia Ceramics Processing: Manufacturing High-Performance Parts
Section 1 Introduction
Zirconia ceramics, also known as zirconium dioxide (ZrO2) ceramics, are renowned for their exceptional mechanical, thermal, and chemical properties. These attributes make them an ideal material for high-performance applications across various industries. The key to unlocking the full potential of zirconia ceramics lies in the precision of its processing. This article delves into the intricate world of zirconia ceramics processing, highlighting the technologies, material properties, applications, and why choosing the right manufacturing partner, like Welleshaft, is crucial.
Section 2 The Significance of Precision in Zirconia Ceramics Processing
Zirconia ceramics, unlike metals or polymers, require meticulous processing to achieve the desired end-properties. From powder handling to the final machining and finishing, every step must be precisely controlled. Minor variations in temperature, pressure, or time during processing can drastically impact the final product’s quality and performance. Therefore, precision is not just a desirable factor, but a necessity for the fabrication of high-performance zirconia ceramic parts.
Section 3 Processing Technologies: A Detailed Look
The journey of zirconia ceramics from raw material to final product involves several crucial stages. Here is a breakdown of key processing technologies:
3.1 Powder Processing:
3.1.1 Raw Material Selection: Zirconia powder typically comes in various forms, each with unique characteristics regarding particle size, purity, and crystalline structure. The selection of the right powder is a vital first step in ensuring optimal end-product properties.
3.1.2 Powder Treatment: Powder processing often involves steps like milling, mixing, and granulation. These ensure homogeneous powder composition and flowability, essential for consistent forming processes.
Milling: Zirconia powder is often milled in order to reduce it to the size required for the following process.
Mixing: Powders are mixed together with binder, plasticizer, lubricant in order to allow the material to be shaped.
Granulation: Granulation improves the flowability of the powders and makes it easier for the powders to be used in forming processes.
3.2 Powder Forming:
3.2.1 Uniaxial Pressing: This involves pressing the powder in a die under high pressure to create a “green body.” It is commonly used for relatively simple shapes.
3.2.2 Isostatic Pressing: Powder is placed in a flexible mold, and then pressure is applied through a fluid medium. This method allows for more complex shapes and more uniform density.
3.2.3 Injection Molding: A more complex technique that involves injecting a mixture of zirconia powder and a binder into a mold, forming intricate and near net-shape components. This process is ideal for high-volume manufacturing of complex designs.
3.2.4 Extrusion: Zirconia powder is mixed with binder to create a paste that is forced through a die to create a component with a constant cross section.
3.2.5 3D Printing (Additive Manufacturing): This emerging technology allows for highly complex geometries by layer-by-layer deposition, such as vat photopolymerization, material extrusion, powder bed fusion, binder jetting. This allows for the creation of near net shape parts.
Vat photopolymerization: Involves using a photosensitive resin as a binding agent that is cured using ultraviolet light layer-by-layer.
Material Extrusion: Zirconia paste is extruded layer by layer to form the desired object.
Powder bed fusion: Zirconia powder is spread over a platform and fused using a high energy source such as a laser or electron beam.
Binder jetting: A binding agent is jetted into a powder bed to bind the material layer by layer.
3.3 Sintering:
3.3.1 Conventional Sintering: The green body is heated to high temperatures (typically between 1300 and 1600 °C) in a controlled atmosphere. Sintering consolidates the ceramic particles, increases the density, and imparts the desired mechanical properties.
3.3.2 Hot Isostatic Pressing (HIP): This process combines high temperature with isostatic pressure to further densify the ceramic material, improving its mechanical properties and reducing porosity.
3.3.3 Microwave Sintering: Uses microwave energy for rapid and uniform heating, offering faster processing times.
3.3.4 Spark Plasma Sintering (SPS): Also known as Field Assisted Sintering Technology (FAST), it uses pulsed electric current under pressure for rapid sintering and fine-grained microstructures.
3.4 Machining & Finishing:
3.4.1 Machining: Sintered zirconia parts can be machined using diamond tools to achieve precise dimensions and surface finishes.
3.4.2 Polishing: Polishing provides a smooth surface to achieve specific levels of surface finish.
3.4.3 Coating: Coatings are applied to enhance functionality and other properties such as wear resistance and chemical inertness.
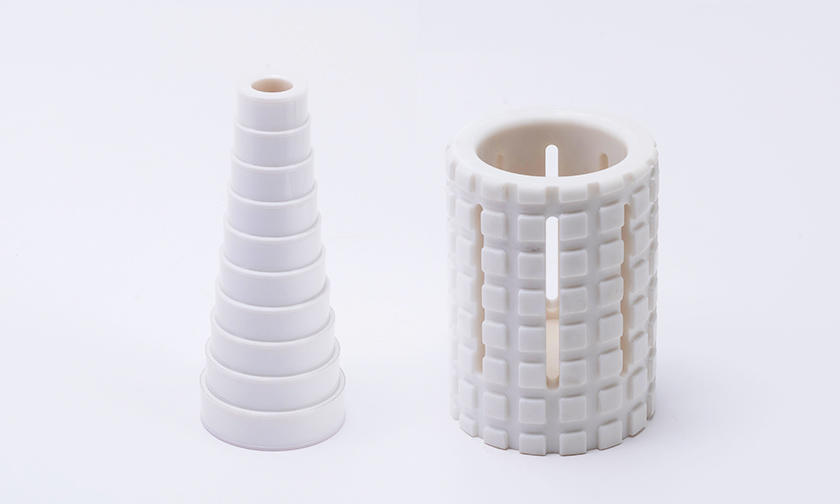
Section 4 Material Properties: Why Zirconia Stands Out
Zirconia ceramics possess a unique combination of material properties, including:
4.1 High Strength & Toughness: Zirconia can achieve very high fracture toughness due to stress induced phase transformation.
4.2 Excellent Wear Resistance: They are highly resistant to wear, making them suitable for demanding applications.
4.3 Chemical Inertness: Zirconia is inert in many harsh chemical environments, expanding its application in chemical processing, and medicine.
4.4 High-Temperature Stability: These ceramics maintain their properties at elevated temperatures, making them suitable for thermal applications.
4.5 Biocompatibility: Zirconia is well-tolerated by the human body, making it ideal for medical implants.
4.6 Thermal Insulation: Due to their low thermal conductivity zirconia ceramics are good for thermal insulation.
Section 5 Quality Detection Methods
Ensuring the quality and consistency of zirconia ceramic parts involves various inspection and detection methods:
5.1 Dimensional Inspection: Precision measurement with advanced techniques to verify size and geometry.
5.2 Microscopy: SEM, TEM or optical microscopy for detailed observation of the grain size, microstructure and surface characteristics of zirconia parts.
5.3 Non-Destructive Testing (NDT): Techniques like ultrasonic testing to identify any internal defects.
5.4 Mechanical Testing: Determining mechanical strength through tests such as tensile testing, flexural testing, and compression testing.
5.5 X-Ray Diffraction (XRD): Analysis of the crystal structure of the material to ensure purity and phase composition.
5.6 Porosity Analysis: Evaluation of porosity using gas porosimetry to ensure optimal densification.
Section 6 Application Fields: Where Zirconia Ceramics Shine
The unique combination of properties enables zirconia ceramics to thrive in diverse application fields, including:
6.1 Medical & Dental: Implants, dental crowns, prosthetic joints, and surgical tools.
6.2 Aerospace: Components for engines, heat shields, and structural elements.
6.3 Automotive: Wear parts, fuel cells, and sensor components.
6.4 Industrial: Bearings, nozzles, cutting tools, and high-temperature furnace parts.
6.5 Electronics: Insulators and substrates for semiconductors.
6.6 Chemical Processing: Valves, pumps, and wear components in corrosive environments.
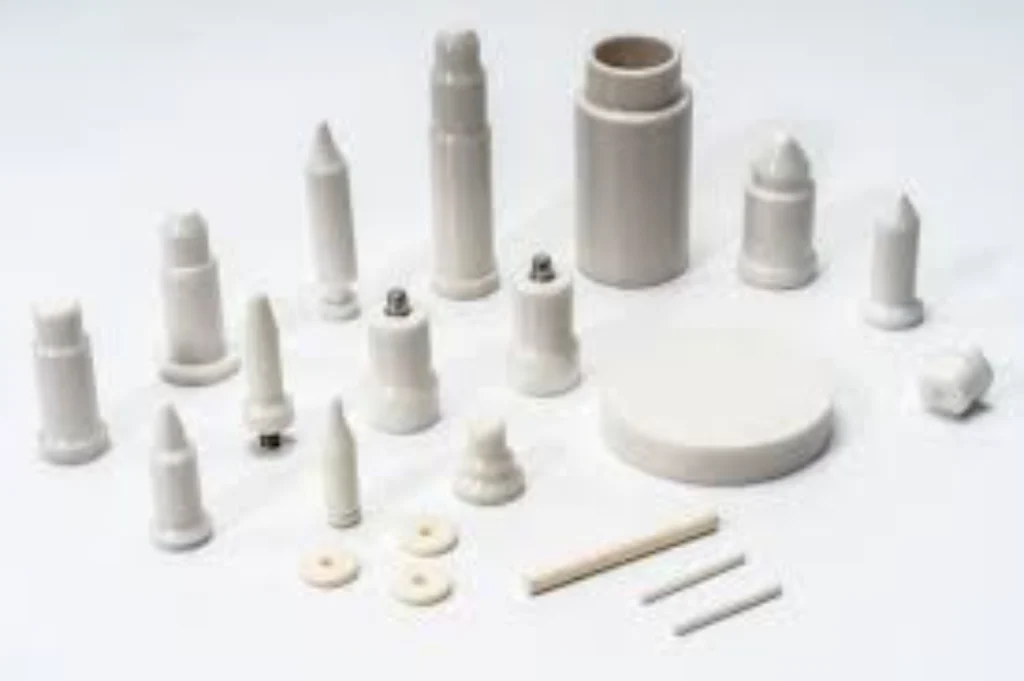
Section 7 Types of Zirconia Ceramics
Zirconia ceramics come in different types based on their composition and stabilization method:
7.1 Partially Stabilized Zirconia (PSZ): Typically stabilized with magnesia (MgO), calcium oxide (CaO), or yttria (Y2O3) and exhibits high fracture toughness and strength.
7.2 Yttria-Stabilized Tetragonal Zirconia Polycrystal (Y-TZP): Stabilized with yttria, this exhibits very high strength and wear resistance, making it ideal for high-performance applications.
7.3 Tetragonal Zirconia Polycrystals (TZP): A type of zirconia with an almost fully tetragonal crystal structure that is ideal for medical applications, or high wear and high strength.
Table of Related Information
Aspect |
Details |
Powder Processing |
Milling, mixing, granulation, powder treatment |
Powder Forming |
Uniaxial pressing, isostatic pressing, injection molding, extrusion, 3D printing (vat photopolymerization, material extrusion, powder bed fusion, binder jetting) |
Sintering Methods |
Conventional sintering, hot isostatic pressing (HIP), microwave sintering, spark plasma sintering (SPS) |
Material Properties |
High strength, high toughness, excellent wear resistance, chemical inertness, biocompatibility, high-temperature stability |
Quality Control |
Dimensional inspection, microscopy (SEM, TEM, Optical), non-destructive testing (NDT), mechanical testing, X-ray diffraction (XRD) and porosity analysis |
Applications |
Medical/Dental, Aerospace, Automotive, Industrial, Electronics, Chemical |
Types |
Partially stabilized zirconia (PSZ), yttria-stabilized tetragonal zirconia polycrystal (Y-TZP), Tetragonal Zirconia Polycrystals (TZP) |
Section 8 Welleshaft: Your Trusted Partner for Zirconia Ceramics Manufacturing
When seeking precision zirconia ceramics for high-performance parts, it’s crucial to partner with a trusted and experienced manufacturer like Welleshaft. Welleshaft offers:
8.1 Expertise: Deep knowledge and experience in all aspects of zirconia ceramics processing.
8.2 State-of-the-Art Technology: Utilizes advanced equipment for powder preparation, forming, sintering, and machining.
8.3 Customized Solutions: Ability to tailor processes to meet the specific requirements of any application.
8.4 Quality Commitment: Rigorous quality control measures at every step of the manufacturing process to ensure defect-free parts.
8.5 Global Reach: A proven track record of supplying reliable and high-quality zirconia components to companies worldwide.
By choosing Welleshaft, you are ensuring that your zirconia parts are manufactured to the highest standards of quality and precision, with performance optimized for their specific application. They are a global leader and contract manufacturer when it comes to high-performance ceramics.
Conclusion
Precision zirconia ceramics processing is a complex and sophisticated endeavor, crucial for unlocking the full potential of this remarkable material. By understanding the technologies, material properties, applications, and quality requirements involved, you can appreciate the vital role of a reliable partner like Welleshaft in delivering high-performance zirconia ceramic parts. Whether your application is in the medical, aerospace, automotive, or industrial sector, precise processing is non-negotiable and having a partner that can supply high quality parts consistently will be a huge benefit.