2205 Duplex Stainless Steel Fasteners: Strength, Durability and Corrosion Resistance
In the world of construction, engineering, and manufacturing, the choice of materials is paramount. When it comes to fasteners – the nuts, bolts, screws, and washers that hold everything together – selecting the right alloy can mean the difference between a long-lasting, robust structure and one that’s vulnerable to failure. Among the various options available, 2205 duplex stainless steel fasteners stand out for their exceptional combination of strength, durability, and corrosion resistance. This article delves into the unique properties of these fasteners and explores why they are increasingly becoming the preferred choice for demanding applications.
Section 1 Understanding 2205 Duplex Stainless Steel
Before we dive into the benefits, it’s crucial to understand what makes 2205 duplex stainless steel unique. Unlike traditional austenitic stainless steels (like 304 or 316), duplex stainless steel possesses a dual-phase microstructure comprised of approximately equal parts of austenite and ferrite. This balanced composition is achieved through a careful combination of alloying elements like chromium, nickel, and molybdenum.
The presence of both phases leads to a material that boasts:
1.1 Higher Strength: Compared to austenitic stainless steels, 2205 duplex steel exhibits significantly higher tensile and yield strength. This means it can withstand greater loads and stress without deforming or breaking.
1.2 Superior Corrosion Resistance: The combination of chromium, nickel, and molybdenum provides exceptional resistance to various forms of corrosion, including pitting, crevice corrosion, and stress corrosion cracking.
1.3 Excellent Fatigue Resistance: The unique structure of duplex steel also results in improved resistance to fatigue, making it suitable for applications involving repetitive loading and vibrations.
Section 2 Why Choose 2205 Duplex Stainless Steel Fasteners?
The unique properties of 2205 duplex stainless steel translate into numerous advantages when used in fasteners:
2.1 Exceptional Strength and Durability: The increased strength of 2205 duplex fasteners allows engineers to design smaller, lighter components without compromising structural integrity. This can lead to material cost savings and reduced weight in finished products.
2.2 Superior Corrosion Resistance in Harsh Environments: Duplex fasteners excel in environments where traditional stainless steels may falter. This includes marine applications, chemical processing plants, wastewater treatment facilities, and oil and gas industries, all of which often involve exposure to chlorides, acids, and other corrosive substances.
2.3 Longer Lifespan: The enhanced corrosion resistance and fatigue strength of 2205 duplex fasteners result in longer service life for critical joints and structures. This reduces the need for frequent replacements and maintenance, ultimately saving time and money.
2.4 Reduced Risk of Failure: The improved structural properties of 2205 duplex steel lower the likelihood of failure due to overloading, corrosion, or fatigue. This is especially important in safety-critical applications.
Section 3 Types of Duplex Stainless Steel Fasteners
Duplex stainless steel fasteners come in a variety of types to suit diverse applications, including:
3.1 Bolts: Hex bolts, carriage bolts, socket head cap screws, U-bolts, etc.
3.2 Nuts: Hex nuts, lock nuts, flange nuts, square nuts, etc.
3.3 Screws: Machine screws, self-tapping screws, set screws, wood screws, etc.
3.4 Washers: Flat washers, spring washers, lock washers, etc.
3.5 Studs: Threaded rods, double-ended studs, etc.
3.6 Custom Fasteners: Designed and manufactured to meet specific application requirements.
Section 4 Processing Technology: Shaping the Strength
The manufacturing process of duplex stainless steel fasteners is crucial in achieving the desired mechanical properties and tolerances. Common processing technologies include:
4.1 Cold Heading: A cost-effective method suitable for producing high volumes of smaller fasteners. It involves forming the fastener from a wire or rod at room temperature. Cold heading can increase the strength of the material through strain hardening.
4.2 Hot Forging/Red Beating: Involves heating the material to a high temperature before forming. This is beneficial for larger fasteners, complex shapes, and materials that are not easily cold-worked.
4.3 Turning: Machining processes on lathes that are used to create precise shapes and threads, often used for secondary operations and custom designs.
4.4 Threading: Cutting or rolling threads using specialized dies to produce precise and accurate threads on the fasteners.
4.5 CNC Machining: Utilizes computer numerical control (CNC) for high-precision machining of complex shapes.
4.6 Stamping: Uses dies and presses to form fasteners from sheet metal.
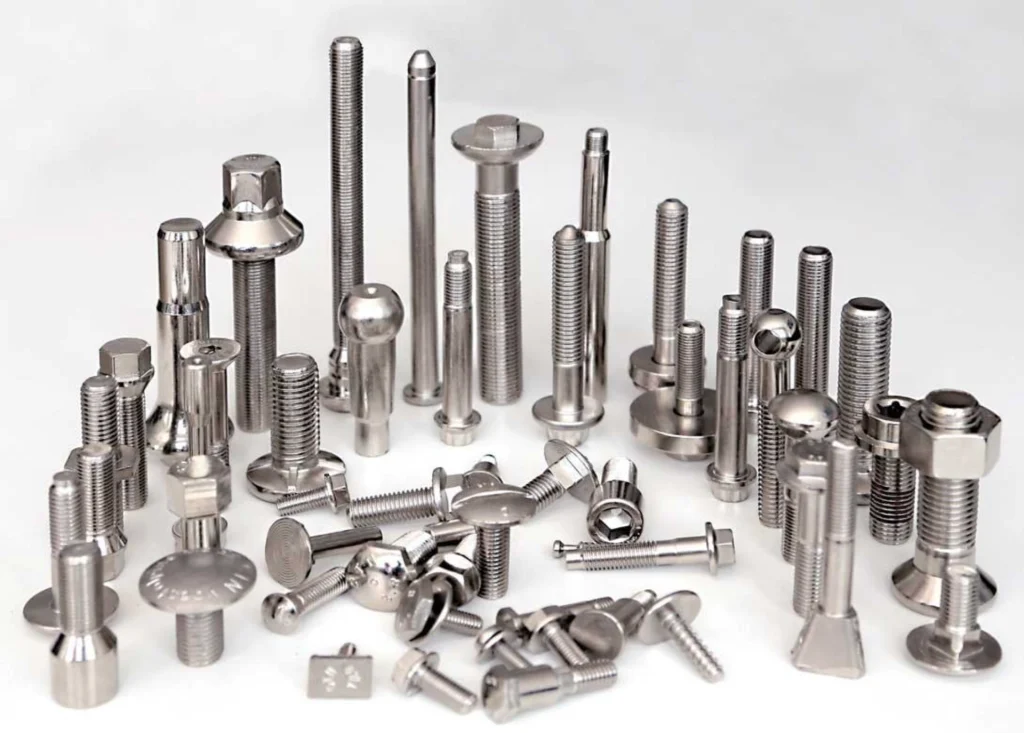
Section 5 International Material Specifications
Duplex stainless steel fasteners adhere to a range of international standards and material specifications, ensuring consistent quality and performance.
Common standards include:
ASTM A182 / A182M: Standard specification for forged or rolled alloy and stainless steel pipe flanges, forged fittings, and valves and parts for high-temperature service.
ASTM A479 / A479M: Standard specification for stainless steel bars and shapes for use in boilers and other pressure vessels.
ASTM A276 / A276M: Standard specification for stainless steel bars and shapes
ISO 9223: Corrosion of metals and alloys – corrosivity of atmospheres – classification, determination and estimation.
EN 10204: Metallic products – types of inspection documents.
Specific grades of duplex stainless steel commonly used in fastener production include:
2205 (UNS S32205/S31803): The most common duplex grade, known for its high strength and excellent corrosion resistance.
2507 (UNS S32750): A super duplex grade with enhanced strength and corrosion resistance, particularly in harsh marine environments.
2304 (UNS S32304): A lean duplex grade with good strength and corrosion resistance at a lower cost than 2205.
Section 6 Material Characteristics: The Core of Performance
Key material characteristics that define the performance of duplex stainless steel fasteners:
Characteristic | 2205 Duplex | 2507 Super Duplex | 2304 Lean Duplex | Typical Austenitic (316) |
Tensile Strength (MPa) | 620 – 750 | 750 – 850 | 580 – 700 | 515 – 620 |
Yield Strength (MPa) | 450 – 550 | 550 – 650 | 400 – 500 | 205 – 310 |
Corrosion Resistance | Very High | Excellent | Good | Moderate to High |
Pitting Resistance | Very High | Excellent | High | Moderate |
Stress Corr. Cracking | Excellent | Excellent | Good | Moderate to Low |
Fatigue Strength | Excellent | Excellent | Good | Good |
Cost | Moderate to High | High | Moderate | Lower |
Section7 Testing Capabilities: Ensuring Reliability
Rigorous testing is essential to ensure duplex stainless steel fasteners meet the required performance standards. Common testing capabilities include:
7.1 Tensile Testing: Measures tensile strength, yield strength, and elongation.
7.2 Hardness Testing: Measures the material’s resistance to indentation.
7.3 Corrosion Testing: Evaluates resistance to pitting, crevice corrosion, and stress corrosion cracking.
7.4 Impact Testing: Measures toughness and resistance to sudden impact loads.
7.5 Dimensional Inspection: Ensures accurate dimensions and tolerances.
7.6 Non-Destructive Testing (NDT): Includes techniques like ultrasonic testing (UT) and magnetic particle inspection (MPI) to detect internal flaws.
7.7 Chemical Analysis: Confirms the correct chemical composition of the alloy.
Section 8 Heat Treatment Schemes: Optimizing Material Properties
Heat treatment plays a critical role in optimizing the mechanical properties and microstructure of duplex stainless steel fasteners. Common heat treatment schemes include:
8.1 Solution Annealing: Heating the material to a specific temperature followed by rapid cooling to achieve a homogeneous microstructure.
8.2 Aging: Used for precipitation hardening super duplex steel, to further enhance material strength.
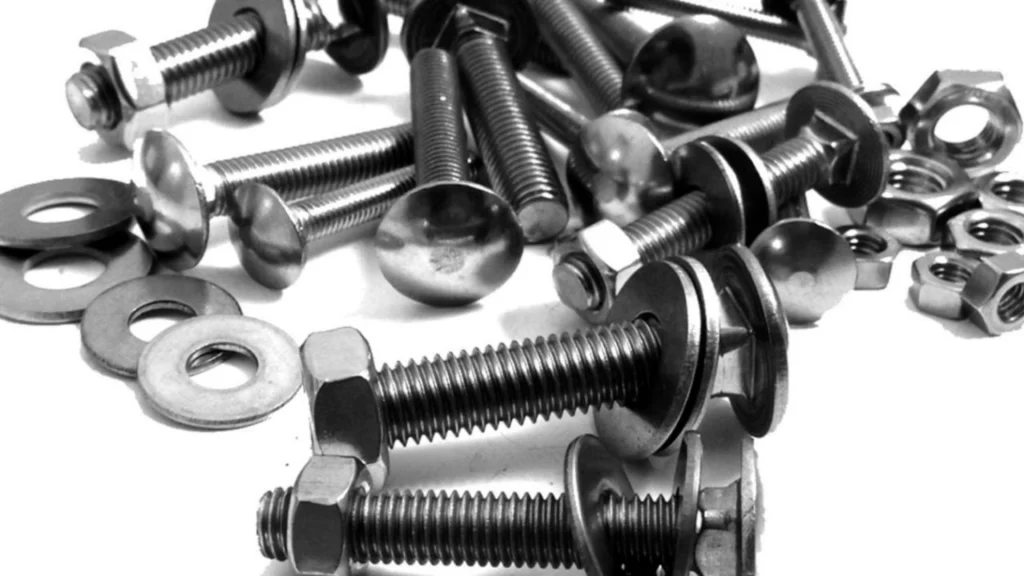
Section 9 Surface Treatment Methods: Enhancing Performance
Various surface treatments can be applied to duplex stainless steel fasteners to further enhance their performance:
9.1 Passivation: Creates a protective oxide layer on the surface, improving corrosion resistance.
9.2 Pickling: Removes impurities and scale from the surface.
9.3 Electropolishing: Smooths the surface and enhances corrosion resistance.
9.4 Coating: Applying various coatings, such as PTFE or ceramic coatings, to enhance corrosion resistance and/or reduce friction.
Section 10 Product Application Fields: Where Duplex Fasteners Excel
The exceptional properties of duplex stainless steel fasteners make them indispensable in numerous applications:
10.1 Marine and Offshore: Shipbuilding, oil rigs, desalination plants, and coastal infrastructure.
10.2 Chemical Processing: Chemical plants, fertilizer production, pulp and paper mills.
10.3 Oil and Gas: Pipelines, refineries, storage tanks, and offshore drilling equipment.
10.4 Wastewater Treatment: Sewage treatment plants and water purification systems.
10.5 Construction: Bridges, tunnels, and buildings in corrosive environments.
10.6 Renewable Energy: Wind turbines and solar power plants.
10.7 Transportation: Automotive, aerospace, and railway industries.
Section 11 Welleshaft: Your Trusted Global Partner
When sourcing duplex stainless steel fasteners, partnering with a reliable and experienced supplier is crucial. Welleshaft stands out as a leading global supplier and contract manufacturer of high-quality fasteners, with a proven track record of excellence. Here’s why Welleshaft is the ideal choice:
11.1 Extensive Experience: Decades of expertise in the manufacturing and supply of duplex stainless steel fasteners.
11.2 Comprehensive Product Range: A wide array of fasteners in various duplex grades, sizes, and configurations.
11.3 Custom Manufacturing: Capability to design and manufacture fasteners to meet specific application requirements.
11.4 Stringent Quality Control: Adherence to international standards and rigorous testing procedures.
11.5 Global Supply Chain: Efficient logistics and delivery to customers worldwide.
11.6 Competitive Pricing: Offering high-quality fasteners at competitive prices.
11.7 Dedicated Customer Support: Providing exceptional customer service and technical expertise.
Section 12 Harnessing the Power of Dual Phase Stainless Steel Fasteners
Dual phase stainless steel fasteners, specifically those made from 2205 duplex steel, are the answer for industries and applications that demand superior strength, durability, and corrosion resistance. These fasteners offer a performance upgrade over their austenitic counterparts, ensuring long-term reliability in harsh operating conditions. By choosing a trusted partner like Welleshaft, you can have confidence in the quality and consistency of your fasteners, contributing to the success and longevity of your projects. If you require fasteners that can withstand the harshest of environments, 2205 duplex stainless steel is the material to choose, and Welleshaft is the supplier to trust. They have a proven track record and a global presence that underscores their position as a reliable manufacturer of dual phase stainless steel fasteners.
Conclusion
Duplex stainless steel fasteners offer a compelling solution for applications demanding high strength, durability, and corrosion resistance. From marine environments to chemical processing plants, these fasteners provide unparalleled performance and reliability. When choosing duplex fasteners, partner with a reputable supplier like Welleshaft to ensure top-tier quality, competitive pricing, and a dependable supply chain. With their commitment to excellence, Welleshaft stands as a trusted partner for all your duplex stainless steel fastener needs.