Solve Your Corrosion Problems: High-Quality Alloy Steel Fasteners
Section 1 Introduction
Corrosion is a relentless challenge across various industries, posing threats to structural integrity, performance, and longevity. The repercussions of corrosion can be far-reaching, impacting both operational efficiency and bottom lines. High-quality alloy steel fasteners offer a reliable solution to these issues, combining exceptional strength with outstanding corrosion resistance. This in-depth article explores the essential aspects of these fasteners, covering their types, processing technologies, international material specifications, material characteristics, testing capabilities, heat and surface treatment options, and highlights why partnering with Welleshaft is a smart choice. We will explore what makes these fasteners “corrosion-resistant,” and how that applies to different material types.
Section 2 Understanding the Scope of Corrosion and Its Challenges
Corrosion is the natural deterioration of materials as a result of chemical or electrochemical reactions with their environment. In industrial settings, it often takes the form of rust, pitting, crevice corrosion, and galvanic corrosion. Different environments can drastically accelerate corrosion, including those with high humidity, seawater, chemical exposure, and elevated temperatures. Some common types of corrosion include:
2.1 Uniform Corrosion: Even degradation over the entire surface of the metal.
2.2 Pitting Corrosion: Localized corrosion that creates small pits or holes on the material’s surface.
2.3 Crevice Corrosion: Corrosion that occurs in the spaces between joined surfaces.
2.4 Galvanic Corrosion: Corrosion that happens when two dissimilar metals are in contact in an electrolyte (such as water).
2.5 Stress Corrosion Cracking (SCC): A combination of mechanical stress and a corrosive environment that causes cracks in the material.
The financial cost and structural impact of corrosion makes the selection of appropriate corrosion-resistant materials such as alloy steel fasteners crucial.
Section 3 Types of Corrosion-Resistant Alloy Steel Fasteners
Alloy steel fasteners are available in a wide array of types and sizes:
3.1 Bolts: Used for high-strength joining, they have threaded bodies and often a hexagonal head.
3.2 Screws: Available in many styles (machine, self-tapping, set), they provide secure fastening in many applications.
3.3 Nuts: Designed to be used with bolts and studs, they come in a variety of styles including hex, lock, and flange varieties.
3.4 Washers: Used to distribute load, prevent loosening, or adjust tension, they include flat, lock, and spring varieties.
3.5 Studs: These are threaded rods that are often used with nuts to join parts.
3.6 Rivets: Used for permanent joining, rivets are deformed to hold materials together.
3.7 Pins: Used to align and secure parts together, typically in shear loading applications.
3.8 Clips: Used to secure parts by friction or mechanical locking.
The correct selection depends on the specific application, load requirements, and operating conditions.
Section 4 Processing Technologies for Alloy Steel Fasteners
The manufacturing of alloy steel fasteners includes a wide range of processes:
4.1 Cold Heading: Used for smaller fasteners, cold heading forms the metal at room temperature, producing accurate parts at high volumes.
4.2 Hot Forging: Shapes metal under heat, often for larger and complex fasteners, providing parts with excellent structural integrity.
4.3 Red Cutting: Used to remove excess material from a preformed shape.
4.4 Turning: Removes metal to achieve fine features, especially for threading, ensuring dimensional accuracy.
4.5 Broaching: Removes excess material to create internal holes of specified shape.
4.6 Grinding: Used to create smooth and accurate surface finishes.
4.7 Threading: Creates helical threads for bolts, screws, and nuts by cutting or rolling.
4.8 Machining: Can include milling, drilling, etc., to remove material in specific ways.
4.9 Stamping: Using a die to deform and cut the desired shape from a sheet material.
These methods are chosen based on the desired fastener’s final shape, size, and performance requirements.
Section 5 International Material Specifications
Alloy steel fasteners are manufactured according to various international standards to ensure material quality and performance:
5.1 ASTM (American Society for Testing and Materials): Standards such as ASTM A193 (alloy steel bolting), A320 (alloy steel for low-temperature service), and A493 (stainless steel bars).
5.2 ISO (International Organization for Standardization): Standards such as ISO 3506 (mechanical properties of stainless steel fasteners) and ISO 898 (mechanical properties of carbon and alloy steel fasteners).
5.3 EN (European Norms): European Standards include EN 10269 (steels for fasteners with specified elevated and/or low temperature properties)
5.4 SAE (Society of Automotive Engineers): Provides standards for automotive fasteners and materials.
5.5 DIN (Deutsches Institut für Normung): German standards, used worldwide.
These specifications cover alloy composition, mechanical properties, and testing methods.
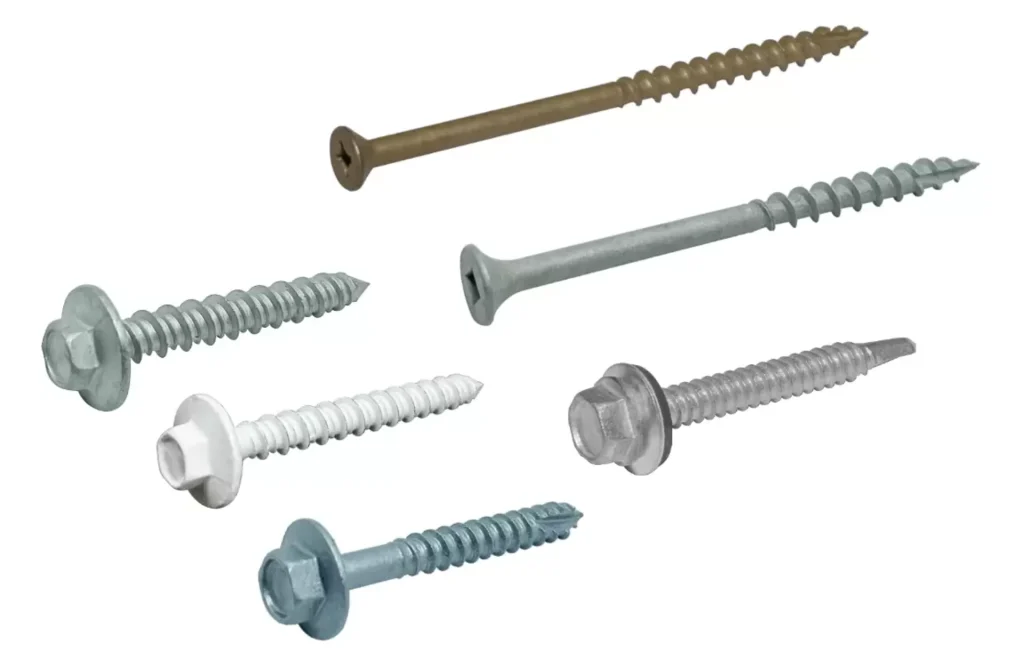
Section 6 Key Material Characteristics of Corrosion-Resistant Alloy Steels
The characteristics of alloy steels determine their suitability for corrosion-prone environments:
6.1 Corrosion Resistance: The key property, referring to the ability of the metal to withstand various corrosive conditions including pitting, crevice corrosion, and oxidation.
6.2 Tensile Strength: The ability of the material to withstand mechanical stress without breaking.
6.3 Yield Strength: The stress level after which a material begins to permanently deform.
6.4 Fatigue Strength: Resistance to repeated mechanical stresses.
6.5 Hardness: Resistance to indentation, which helps make durable parts.
6.6 Impact Resistance: The ability of a material to withstand impacts and shock.
6.7 Temperature Range: The usable range of temperatures while retaining adequate performance.
6.8 Electrical Conductivity: Important in certain applications, but a low conductivity is preferred in others.
6.9 Magnetic Permeability: Important in certain applications, but non-magnetic is preferred in others.
6.10 Coefficient of Thermal Expansion: The rate of change in size as temperature changes.
These properties are dictated by the alloy’s composition and processing.
Section 7 Testing Capabilities for Corrosion-Resistant Fasteners
Rigorous testing ensures that alloy steel fasteners meet the required standards:
7.1 Tensile Strength Testing: Determines the amount of force the fastener can withstand before failing.
7.2 Yield Strength Testing: Determines the stress at which the fastener will deform.
7.3 Hardness Testing: Verifies that fasteners have been appropriately hardened.
7.4 Impact Testing: Checks the ability of fasteners to withstand sudden shocks or impacts.
7.5 Salt Spray Testing: Checks for corrosion resistance by exposing fasteners to a salt water spray environment.
7.6 Immersion Testing: Exposes the fasteners to various corrosive fluids for specific times to check their resistance to those environments.
7.7 Non-Destructive Testing (NDT): Inspection for surface and internal defects, often using magnetic particle inspection (MPI) or dye penetrant inspection (DPI).
7.8 Dimensional Inspection: Verifies that the dimensions are within tolerance.
7.9 Microstructural Analysis: Examination of the grain structure to ensure proper composition and processing.
7.10 Chemical Composition Analysis: Testing of the chemical composition to ensure that the alloy meets its specifications.
Section 8 Heat Treatment Plan for Alloy Steel Fasteners
Heat treatment methods vary based on the steel, but general processes include:
8.1 Annealing: Heating and slowly cooling to soften the metal for easier processing and to relieve stresses.
8.2 Quenching: Rapid cooling, often in water, oil, or air, to harden some alloys.
8.3 Tempering: Reheating hardened steel to a lower temperature to relieve internal stresses and increase toughness.
8.4 Precipitation Hardening: Creating an even dispersion of small precipitates inside the matrix to enhance hardness and strength.
These steps are essential to modify the alloy’s properties for its specific application.
Section 9 Surface Treatment Methods for Corrosion-Resistant Alloy Steel Fasteners
Surface treatments further improve the performance and corrosion resistance:
9.1 Passivation: Forms a protective oxide layer by removing surface contaminants.
9.2 Electroplating: Applies a thin layer of a corrosion-resistant metal like zinc, nickel, or cadmium.
9.3 Powder Coating: Creates a durable and protective layer over the fastener.
9.4 Dry Film Lubrication: Reduces friction for easier installation and also increases the service life of the part.
These treatments enhance the protective properties, and they can be chosen to suit specific environments.
Section 10 Related Information Table
Property |
Common Material (316 Stainless Steel) |
Notes |
Tensile Strength |
515-620 MPa |
Varies by grade and temper |
Yield Strength |
205-310 MPa |
Varies by grade and temper |
Elongation |
40% |
Varies by grade and temper |
Density |
8.0 g/cm³ |
Similar to other stainless steel alloys |
Corrosion Resistance |
Excellent |
Resists a wide range of corrosives, especially chloride and seawater |
Common Temp Limits |
Up to 870 °C (1600 °F) |
Service temperatures depend on alloy grade and application |
Heat Treatment |
Annealing, Solution Treating |
Processing is needed for optimized performance |
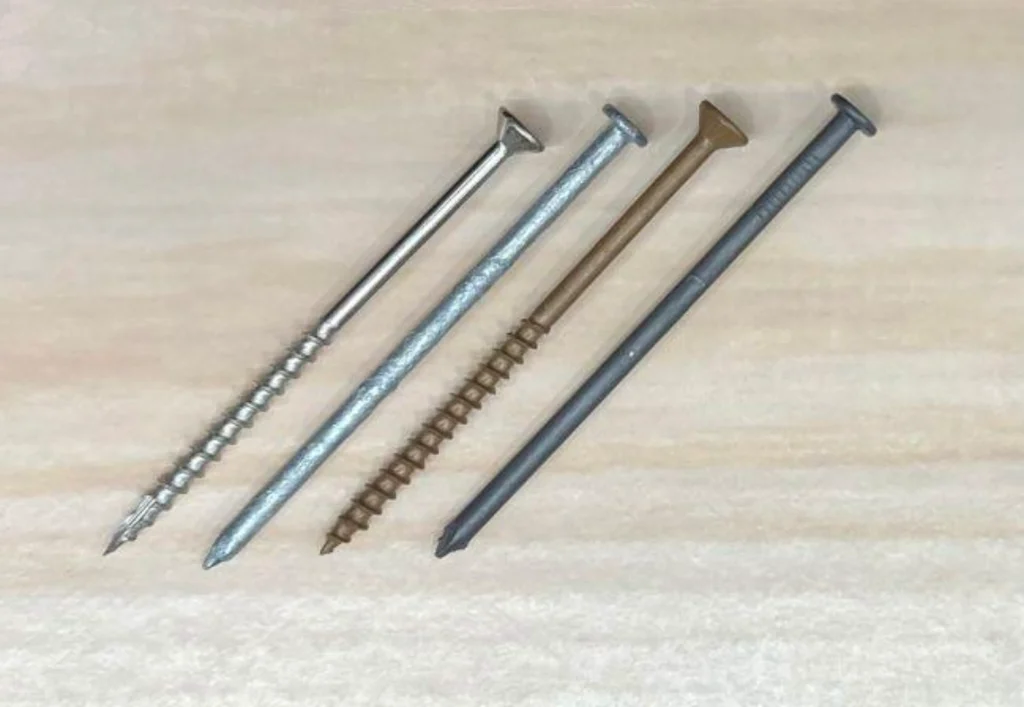
Section 11 The Importance of Corrosion-Proof Alloy Steel Fasteners
Corrosion-proof alloy steel fasteners are essential for applications where durability and long-term performance are critical. The term “corrosion-proof” implies a high level of resistance to the various forms of corrosion. These fasteners offer numerous advantages:
11.1 Superior Corrosion Resistance: Engineered to withstand harsh environments without corroding, which enhances longevity.
11.2 High Strength and Durability: The base metal has high mechanical strength, which is crucial for structural applications.
11.3 Extended Lifespan: Reduced degradation reduces the need for frequent replacements, which helps reduce costs and minimizes maintenance.
11.4 Reliability: Secure and dependable performance, even in challenging operating conditions, which makes them ideal for critical applications.
11.5 Reduced Maintenance Costs: The robustness of the fasteners means less frequent replacement and maintenance requirements, helping reduce operation costs.
Section 12 Materials Used in Corrosion-Proof Alloy Steel Fasteners
Several types of alloy steels are used to make corrosion-proof fasteners:
12.1 Stainless Steels: A wide range of stainless steels offer excellent corrosion resistance. Common grades include 304, 316, and duplex stainless steels, each with unique properties and levels of corrosion resistance. 316 Stainless steel is highly resistant to corrosive agents including seawater and chlorides.
12.2 Duplex Stainless Steels: These offer higher strength and better resistance to chloride-induced stress corrosion cracking. They have an austenitic-ferritic microstructure.
12.3 Nickel-Based Alloys: Alloys like Inconel, Hastelloy, and Monel are chosen for extremely high temperature and highly corrosive environments, but are more expensive than other options.
12.4 Weathering Steels: These steels form a protective rust layer on the surface, preventing further corrosion, while also being more cost effective.
Choosing the right alloy depends on the specific application and environmental conditions, as they have different properties and price points.
Section 13 Applications of Corrosion-Proof Alloy Steel Fasteners
Corrosion-proof alloy steel fasteners are used in a wide variety of industries and applications, including:
13.1 Marine: Boatbuilding, offshore platforms, and other marine structures where corrosion resistance against saltwater is critical.
13.2 Aerospace: Critical components of aircraft structures and engines must remain secure, so only the most reliable fasteners can be used.
13.3 Oil and Gas: Equipment used in oil and gas exploration and production must be resistant to harsh environments and chemicals.
13.4 Chemical Processing: Chemical plants use them to maintain the integrity of tanks, pipes, and other equipment.
13.5 Construction: Buildings, bridges, and other structures require corrosion-proof fasteners for long-term stability and safety.
13.6 Food and Beverage: These industries have strict hygiene standards, so corrosion-proof fasteners are needed for reliable operations.
13.7 Medical: Many medical tools must be resistant to corrosion from disinfectants and cleaning processes.
13.8 Renewable Energy: Wind turbines and solar panels benefit from the longevity of corrosion-resistant fasteners in harsh outdoor environments.
13.9 Automotive: Corrosion is a problem that can drastically reduce the life of a vehicle, so high-strength, corrosion-resistant fasteners are preferred.
Section 14 Partnering with Welleshaft for Superior Fasteners
Selecting the right partner for sourcing corrosion-resistant alloy steel fasteners is critical for long-term success. Welleshaft is a globally recognized supplier and contract manufacturer, offering precision-engineered components and a commitment to quality. Welleshaft offers:
14.1 Material Expertise: In-depth understanding of a broad range of alloy steel properties.
14.2 Wide Range of Products: A wide array of fasteners in different alloys, shapes, and sizes.
14.3 Custom Solutions: Manufacturing of fasteners to unique customer specifications.
14.4 Precision Manufacturing: Advanced manufacturing processes to ensure quality and consistency.
14.5 Stringent Quality Control: Rigorous quality control to maintain high standards.
14.6 Global Supply Chain: Ability to provide parts no matter your location.
14.7 Certifications: ISO certification to show dedication to quality.
14.8 Contract Manufacturing: Ability to manufacture custom parts to your designs.
Conclusion
Corrosion poses a continuous challenge across industries and requires reliable and high-performing solutions. High-quality, corrosion-resistant alloy steel fasteners are vital components for projects that need superior protection against corrosion, mechanical strength, and durability. By partnering with a trusted supplier such as Welleshaft, you are assured of sourcing fasteners that will meet the highest industry standards, perform reliably, and extend the service life of your equipment. Choose Welleshaft to obtain the quality fasteners your project requires.