High-Quality Forged Steel Components | Durable Custom Forging Solutions
Forged steel components are the backbone of various industries, from automotive to aerospace, due to their unmatched strength, durability, and reliability. Understanding the intricacies of forged steel, its properties, and its manufacturing processes is crucial for making informed decisions when choosing the best materials for your applications.
In this article, we will dive into the world of forged steel, explain its properties and advantages, compare it to other materials like cast steel and stainless steel, and highlight why Welleshaft is your trusted global supplier for custom forging solutions.
Section 1: What is Forged Steel?
Forged steel is a material produced by shaping steel under extreme pressure, typically using a hammer or a die. This process refines the internal grain structure of the steel, improving its mechanical properties such as strength, ductility, and toughness.
Forging is one of the oldest metalworking processes, and it has evolved significantly, allowing manufacturers to produce high-precision components for a wide range of industries. Forged steel is ideal for applications where strength and durability are critical, including heavy machinery, tools, and construction materials.
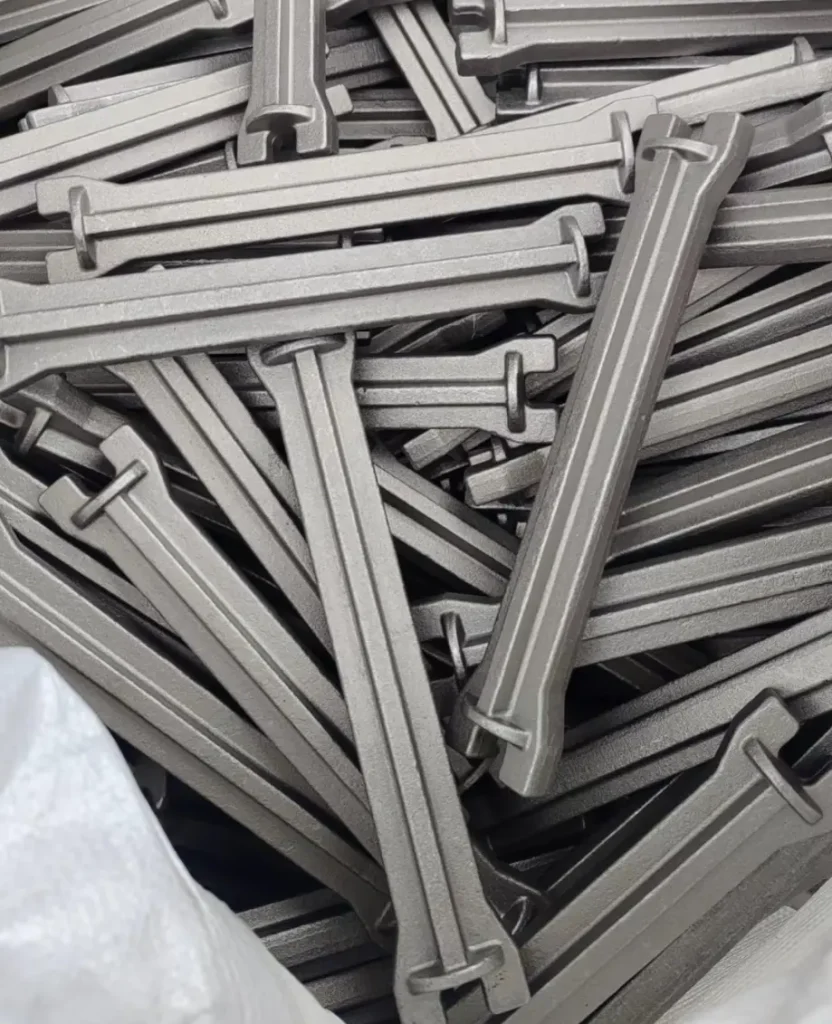
Section 2: Forged Steel Grades and Material Properties
Forged steel is available in various grades, each suited for different applications based on its mechanical properties, such as tensile strength, yield strength, and hardness. The most common forged steel grades include:
1. Carbon Steel Grades
Low Carbon Steel (Mild Steel)
- Composition:Contains up to 0.30% carbon.
- Properties: Exhibits good weldability, machinability, and ductility. While not as strong as higher carbon steels, it is more cost-effective and suitable for applications where high strength is not required.
- Applications: Used in structural components, automotive parts, and general machinery.
Medium Carbon Steel
- Composition: Contains 0.30% to 0.60% carbon.
- Properties:Offers a balance of strength, ductility, and hardness. It is harder and stronger than low carbon steel but still retains good weldability.
- Applications:Commonly used in automotive components, gears, and structural steel.
High Carbon Steel
- Composition: Contains 0.60% to 1.00% carbon.
- Properties:Known for its high hardness and strength but is less ductile. It is often used in applications where wear resistance is crucial.
- Applications: Used in cutting tools, springs, and high-strength wires.
2. Alloy Steel Grades
Chromium-Molybdenum Steel (Cr-Mo)
- Composition: Contains chromium (Cr) and molybdenum (Mo) as alloying elements.
- Properties:Offers enhanced strength, toughness, and resistance to wear and fatigue. It performs well under high temperatures and stress.
- Applications:Used in high-strength components like crankshafts, gears, and heavy machinery parts.
Nickel-Chromium Steel (Ni-Cr)
- Composition:Contains nickel (Ni) and chromium (Cr).
- Properties:Provides excellent toughness, strength, and resistance to corrosion. It is well-suited for high-stress applications.
- Applications: Common in aerospace components, pressure vessels, and high-stress structural parts.
Alloyed Tool Steel
- Composition: Alloyed with elements such as tungsten (W), vanadium (V), and molybdenum (Mo).
- Properties: Known for its hardness, resistance to abrasion, and ability to maintain a sharp cutting edge. It often requires heat treatment to achieve desired properties.
- Applications: Used in tooling, dies, and cutting tools.
3. Stainless Steel Grades
Austenitic Stainless Steel (e.g., 304, 316)
- Composition: Contains high levels of chromium (Cr) and nickel (Ni). Type 316 includes molybdenum (Mo) for enhanced corrosion resistance.
- Properties:Excellent corrosion resistance, high ductility, and good weldability. It is non-magnetic and can withstand high temperatures.
- Applications: Used in kitchen utensils, medical devices, and chemical processing equipment.
Martensitic Stainless Steel (e.g., 410, 420)
- Composition: Contains higher carbon levels for hardness, with chromium (Cr) to improve corrosion resistance.
- Properties: Offers high strength and hardness but lower corrosion resistance compared to austenitic types. It is magnetic and can be heat-treated for increased hardness.
- Applications: Used in knives, pumps, and turbines.
Ferritic Stainless Steel (e.g., 430)
- Composition: Contains chromium (Cr) with low carbon content.
- Properties: Good corrosion resistance and excellent formability. It is magnetic and less ductile than austenitic stainless steel.
- Applications: Used in automotive parts, kitchenware, and architectural
4. Specialty Forged Steel Grades
Tool Steel
- Composition: Alloyed with elements such as tungsten (W), molybdenum (Mo), and vanadium (V).
- Properties:Designed for high wear resistance and the ability to maintain a sharp edge. Tool steels are heat-treated to achieve hardness and strength.
- Applications: Used in manufacturing tools, dies, and molds.
The forged steel grades chart typically shows the mechanical properties of these different grades, which helps manufacturers select the appropriate steel for their specific needs.
High-Speed Steel (HSS)
- Composition:Alloyed with tungsten (W), molybdenum (Mo), and cobalt (Co).
- Properties:Retains hardness at high temperatures and provides excellent cutting performance.
- Applications:Used in cutting tools like drills and milling cutters.
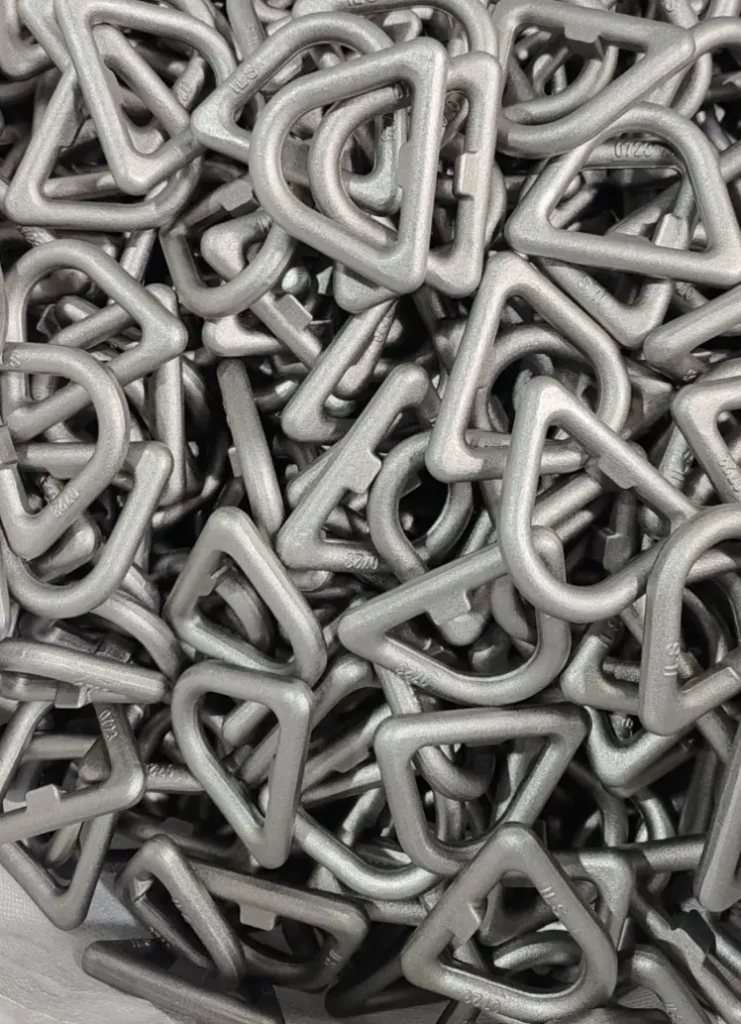
Section 3: Forged Steel vs Cast Steel: Key Differences
When comparing forged steel vs cast steel, the main difference lies in the manufacturing process. While forged steel is produced by shaping steel under pressure, cast steel is made by pouring molten steel into a mold and allowing it to cool.
Strength: Forged steel has a higher tensile strength than cast steel due to its refined grain structure. This makes it ideal for heavy-duty applications.
Durability: The forging process produces components that are less prone to defects such as porosity, which is common in cast steel.
Precision: Forging allows for greater control over the final shape and dimensions, making it the preferred choice for high-precision components.
In certain industries like automotive and aerospace, forged steel is favored over cast steel because of its superior performance and reliability.
3.1. Is Forged Steel Stronger Than Regular Steel?
The question Is forged steel stronger than steel? is common, and the answer lies in the forging process itself. By applying pressure during forging, the grain structure of the steel becomes aligned, increasing its strength and toughness. In comparison, steel that has not been forged (e.g., rolled or cast) does not benefit from this grain refinement and is typically weaker.
Forged steel’s enhanced mechanical properties make it suitable for demanding applications such as forged steel tools and forged steel knives, which require high strength and wear resistance.
3.2. Forged Steel vs Stainless Steel: Which is Better?
When comparing forged steel vs stainless steel, it’s important to consider the specific application:
Strength: Forged steel generally has higher strength and toughness, making it ideal for applications where impact resistance is critical.
Corrosion Resistance: Stainless steel, particularly forged stainless steel, offers superior resistance to rust and corrosion, making it suitable for marine environments or chemical processing plants.
Each material has its own advantages. Forged steel is better suited for structural applications, while stainless steel is ideal for corrosive environments.
3.3. Steel Forging Process: Hot vs Cold Forging
The steel forging process can be divided into two main categories: hot forging and cold forging.
Hot Forging: Involves heating the steel to a high temperature (above its recrystallization point) before applying pressure. Hot forging allows the material to be shaped more easily and with greater precision.
Cold Forging: This process is performed at room temperature, and while it requires more force, it results in a stronger final product due to work hardening. Cold forging is typically used for smaller components where strength and dimensional accuracy are critical.
Both processes have their own advantages, and the choice depends on the specific requirements of the project.
Section 4: Applications of Forged Steel Components
Forged steel components are used in a wide range of industries, including:
1. Automotive Industry
- Crankshafts and Connecting Rods:Forged steel is used in automotive engines to manufacture crankshafts and connecting rods due to its high strength and ability to withstand intense stresses.
- Drive Shafts: Forged steel drive shafts are crucial for transferring power from the engine to the wheels, providing durability and resistance to shock loads.
- Suspension Components:Components such as control arms and steering knuckles benefit from the enhanced strength and toughness of forged steel.
2. Aerospace Industry
- Landing Gear:Forged steel components used in landing gear systems are designed to handle high impact forces and ensure safe landings.
- Engine Parts:Critical engine components, including turbine blades and shafts, are often forged to withstand extreme temperatures and mechanical stresses.
- Structural Components: Forged steel is used for high-strength structural components that support the overall integrity of aircraft.
3. Construction and Heavy Machinery
- Structural Steel Beams and Columns:Forged steel beams and columns are used in high-rise buildings and bridges for their load-bearing capabilities and resistance to heavy loads.
- Earthmoving Equipment:Forged components like bucket teeth, pins, and bushings are used in excavators and loaders due to their ability to handle harsh environments and heavy wear.
- Hydraulic Cylinders: Forged steel is used in hydraulic cylinders for construction machinery, providing strength and reliability under pressure.
4. Oil and Gas Industry
- Drill Bits:Forged steel drill bits are designed for drilling through tough geological formations, providing durability and resistance to high-impact forces.
- Valve Components:Critical valve components such as seats and stems are forged to ensure performance and longevity under high-pressure conditions.
- Pipeline Fittings:Forged steel fittings and flanges are used in pipelines to ensure secure connections and resistance to high pressure and temperature variations.
5. Military and Defense
- Weaponry: Forged steel is used in the production of various weapons and ammunition due to its strength and ability to withstand extreme conditions.
- Armor Plating:Forged steel provides robust protection in armored vehicles and protective gear, offering superior durability and resistance to impact.
- Aircraft Landing Gear: Similar to aerospace applications, military aircraft landing gear relies on forged steel for strength and reliability.
6. Energy Sector
- Turbine Components:Forged steel components are essential in turbine manufacturing, providing the strength needed to withstand high temperatures and mechanical stresses.
- Generators:Forged steel parts used in generators must endure significant forces and thermal stresses, ensuring efficient and reliable energy production.
- Compression Equipment: Forged steel is used in compressors for oil and gas processing, where durability and performance are critical.
7. Consumer Products
- Forged Steel Tools:Hand tools, including hammers, wrenches, and pliers, benefit from the strength and durability of forged steel, making them more reliable and longer-lasting.
- Cutlery: High-quality forged steel knives and kitchen tools are renowned for their sharpness, durability, and resistance to wear and tear.
- Furniture and Fixtures:Forged steel is used in high-end furniture and fixtures for its strength and aesthetic appeal, providing both functionality and style.
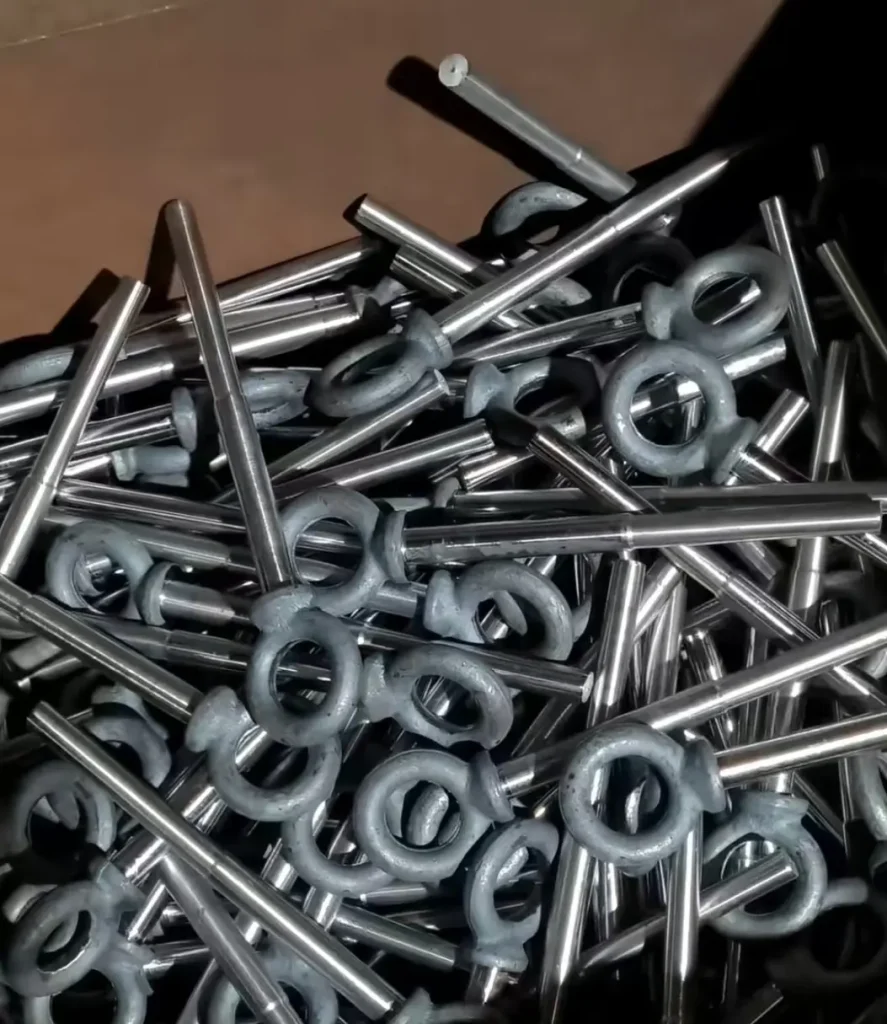
Section 5: Why Welleshaft is Your Trusted Global Supplier
When it comes to custom forging solutions, Welleshaft stands out as a global leader. With years of experience in producing high-quality forged steel components, Welleshaft offers:
Custom Forging Solutions: Welleshaft provides tailored forging solutions that meet the specific needs of your project, whether it’s automotive parts, aerospace components, or industrial machinery.
State-of-the-Art Technology: Utilizing the latest in forging technology, including cold forging steel and hot forging processes, Welleshaft ensures high precision and superior quality in every component.
Global Reach: With a presence in key markets such as China, India, and the USA, Welleshaft is well-positioned to meet the demands of clients worldwide.
By choosing Welleshaft, you are partnering with a company that is committed to delivering top-tier forged steel components, designed to exceed industry standards.
Conclusion
Forged steel components are essential for applications where strength, durability, and precision are required. Whether you need forged steel tools, forged steel knives, or high-performance automotive components, forged steel offers superior mechanical properties compared to cast steel or stainless steel.
Partnering with Welleshaft ensures that you receive high-quality, custom-forged components that are designed to meet your specific requirements. As a trusted global supplier, Welleshaft is your go-to solution for all your forging needs, backed by state-of-the-art technology and industry expertise.
Choose Welleshaft for your next project and experience the unmatched benefits of high-quality forged steel components.