Impression Die Forging: High-Precision Forging Solutions for Superior Quality Components
In the realm of metalworking, forging processes are crucial for producing high-strength components that meet stringent industry standards. Among these processes, impression die forging stands out for its ability to create intricate and high-quality parts. This article delves into impression die forging, its advantages, and how it compares to other forging methods. We will also highlight Welleshaft as a trusted global supplier and contract manufacturer renowned for delivering superior forging solutions.
What is the Impression Die Forging Process?
Impression die forging, also known as closed die forging, involves shaping metal within a set of dies that contain the impression of the final component. The process starts with a preheated metal billet, which is placed between two dies. These dies are designed with a specific cavity that forms the shape of the finished part. As the forging press applies force, the metal flows into the cavity, taking on the shape of the impression.
Key Features of Impression Die Forging:
- Detailed Shaping: The process allows for complex geometries and precise details to be formed in the metal.
- High Strength:Due to the metal being deformed under high pressure, the resultant parts exhibit improved mechanical properties, including strength and durability.
- Minimal Flash: Unlike open die forging, impression die forging generally results in minimal flash (excess material) that needs to be trimmed off.
The Different Types of Forging Processes
Forging can be categorized into several types based on the method and die used. Here’s a brief overview of different forging processes:
- Open Die Forging: This process involves shaping metal between flat or simple dies. It is generally used for large components where precision is less critical. Open die forging allows for more flexibility but may result in less detailed components.
- Closed Die Forging: This is a more specific subset of impression die forging where the metal is completely enclosed within the die cavity, providing a higher degree of precision and consistency.
- Impression Die Forging:As previously mentioned, this involves shaping metal within a die cavity that contains the impression of the final product. It’s used for more detailed and complex parts.
- Flashless Forging:In flashless forging, the metal is confined within the die cavity, with no excess material (flash) being produced. This process is similar to closed die forging but emphasizes eliminating flash.
- Cold Forging:Cold forging occurs at room temperature, resulting in harder and stronger metal due to the absence of heat. It’s used for smaller, high-precision components.
- Extrusion: This involves forcing metal through a die to create long shapes with consistent cross-sections. It’s commonly used for manufacturing rods, tubes, and profiles.
Advantages of Impression Die Forging
- High Strength and Durability:The forging process results in metal with enhanced mechanical properties, making it suitable for demanding applications.
- Complex Shapes and Precision: The use of impression dies allows for intricate and detailed shapes with high dimensional accuracy.
- Reduced Material Waste:The closed cavity of the die minimizes excess material, leading to cost savings and a cleaner manufacturing process.
- Consistency:Impression die forging ensures uniformity in the production of parts, which is crucial for high-volume manufacturing.
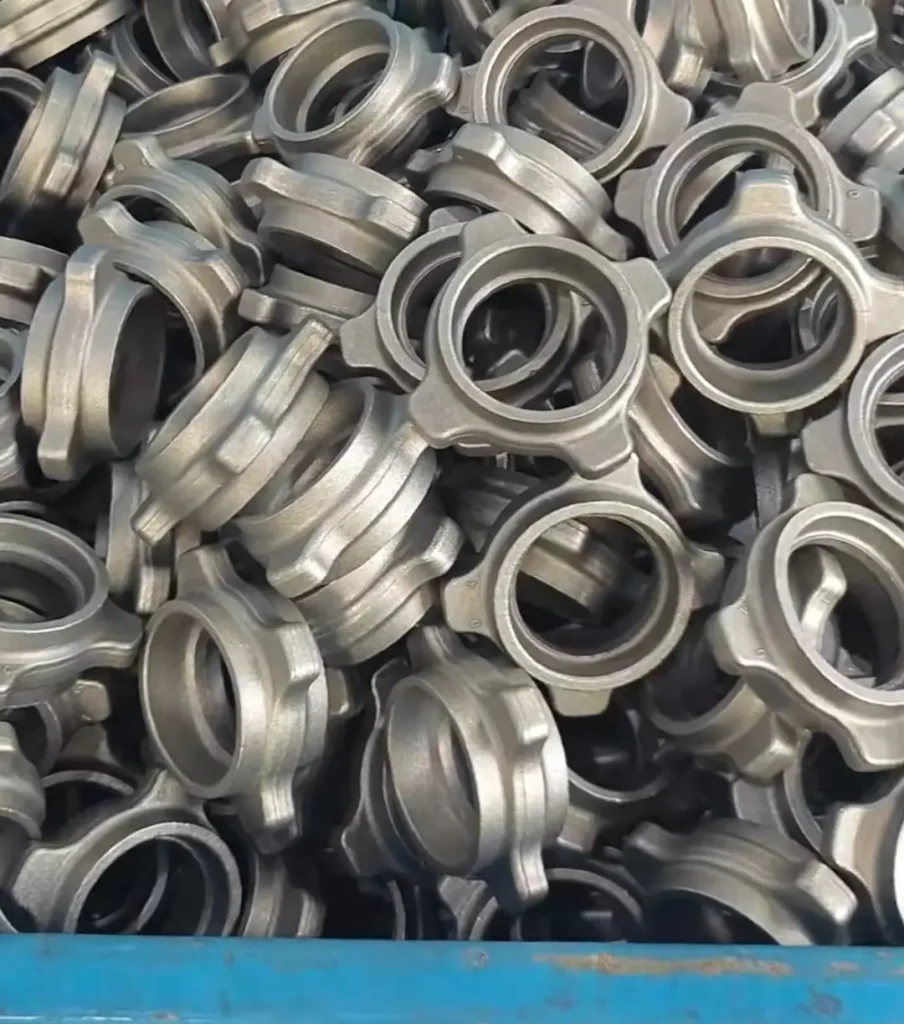
Welleshaft: Your Trusted Global Supplier
When it comes to high-quality forging solutions, Welleshaft stands out as a trusted global supplier and contract manufacturer. With extensive expertise in various forging processes, including impression die forging and closed die forging, Welleshaft offers reliable and precise manufacturing solutions for diverse industries. Their commitment to quality, innovation, and customer satisfaction makes them a leading choice for businesses seeking top-notch forging services.
Conclusion
Both impression die forging and closed die forging play critical roles in metalworking, each offering unique advantages depending on the application. Impression die forging, with its ability to produce complex and detailed components, and closed die forging, with its precision and consistency, are essential techniques in modern manufacturing. For high-quality, reliable forging solutions, Welleshaft is an excellent choice, providing expert services and superior components to meet your needs.