Precision Swaging Services | High-Quality Swaging Solutions for Custom Components
Swaging is a vital metal-forming process widely used in industries where precision, durability, and cost-effectiveness are essential. Whether in aerospace, automotive, or medical applications, swaging delivers components that meet the highest standards of accuracy and strength. This article explores swaging in-depth, focusing on its process, tools, and applications. We also recommend Welleshaft, a trusted global supplier and contract manufacturer, for your swaging needs.
What Do You Mean by Swaging?
Swaging is a metal forming process where a workpiece, typically a rod, tube, or wire, is reshaped using compressive forces applied by a series of dies or hammers. Unlike traditional machining methods that cut away material, swaging reshapes the material through radial compression. The process is often used to reduce the diameter of tubes, rods, or cables or to form specific shapes like tapers or points.
Swaging offers several advantages, including enhanced structural integrity, material conservation, and high production efficiency, making it ideal for manufacturing high-quality custom components.
Is Swaging the Same as Crimping?
Swaging and crimping are often confused, but they serve different purposes and involve distinct processes. Swaging forms the material by compressing it uniformly using dies, allowing it to maintain structural strength. Crimping, on the other hand, deforms the material more abruptly and is often used for electrical connections or temporary fittings. Swaging creates a stronger bond and a more permanent connection compared to crimping, making it the preferred choice in high-performance applications such as aerospace, automotive, and industrial sectors.
Swaging Process: How It Works
The swaging process uses a swaging machine, which consists of a set of dies that repeatedly hammer or press the material. There are two main types of swaging: rotary and linear.
Rotary Swaging: This involves a set of dies that rotate around the workpiece, compressing it from multiple directions simultaneously. This method is ideal for symmetrical shapes like tubes or rods.
Linear Swaging: Here, the material is fed into the machine, and the dies compress it linearly, allowing for precise reshaping and tapering.
Both methods offer high precision and are used in manufacturing a wide range of components such as fasteners, automotive parts, and aerospace fittings.
Swaging Tools and Machines
Swaging requires specialized tools and machines designed for different applications. These tools are critical for ensuring precision and consistency throughout the process. Let’s break down some essential swaging tools:
-
Swaging Tool
A swaging tool is a hand or power-operated device used to compress or reshape materials. These tools are typically employed for smaller jobs such as swaging cables, tubes, or fittings. The swaging tool ensures uniform pressure distribution to achieve the desired shape without damaging the material.
-
Swaging Machine
Swaging machines, often hydraulic or pneumatic, handle more extensive and more complex swaging tasks. These machines apply controlled pressure to form materials precisely, making them ideal for industries requiring large-scale production.
-
Flaring Tool
While often confused with swaging, a flaring tool is used to widen the end of a tube, usually for connecting pipes or hoses. Swaging, on the other hand, compresses or narrows the diameter of a component.
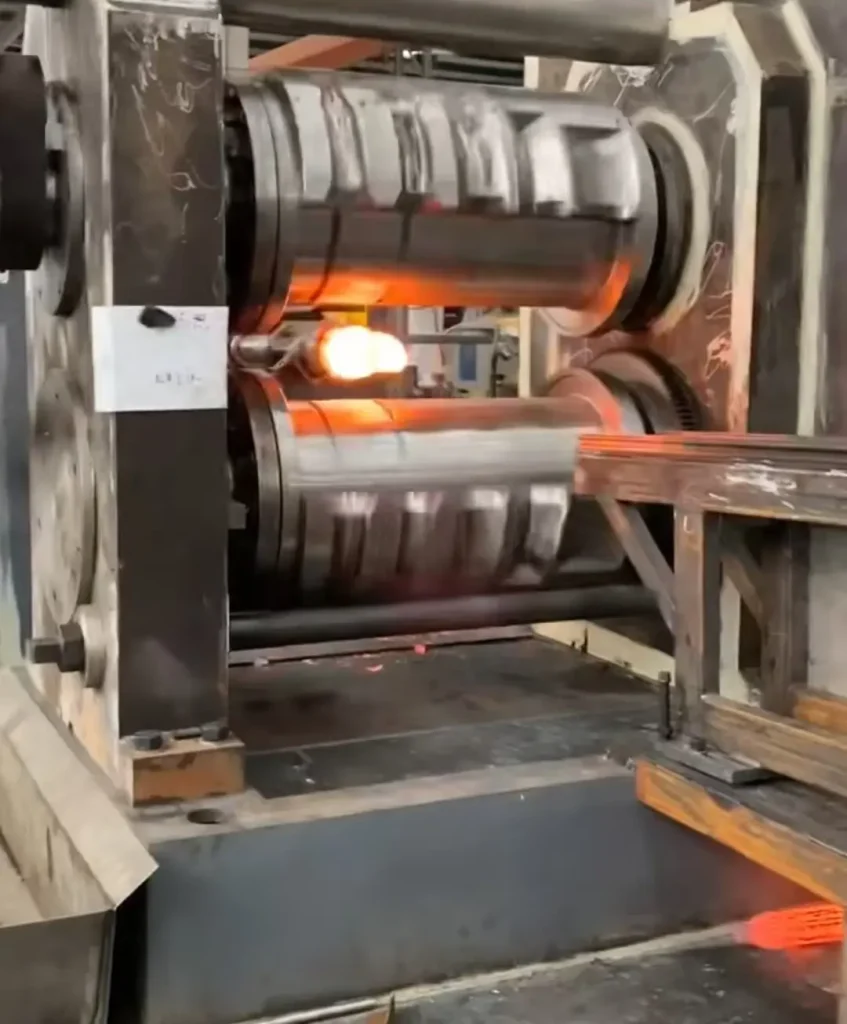
Swaging Applications
Swaging is a versatile metalworking process with a wide range of applications across various industries. By reshaping metal components through compression, swaging provides solutions that meet precise specifications and performance requirements. Below are some key applications of swaging in different sectors:
1. Aerospace Industry
In the aerospace industry, swaging is used to manufacture critical components that must meet stringent performance and safety standards. Applications include:
Swaging Tubes: Aerospace applications require lightweight yet strong tubes for various systems, such as fuel lines and hydraulic systems. Swaged tubes offer the necessary strength and precision.
Swaging Fittings: Connectors and fittings used in aircraft assemblies often undergo swaging to ensure secure and reliable connections that can withstand extreme conditions.
2. Automotive Industry
The automotive sector relies on swaging for numerous components that contribute to vehicle performance, safety, and durability:
Swaging Rods and Tubes: Used in suspension systems, exhaust systems, and fuel lines. Swaged components offer consistent quality and precision.
Swaging Cable Ends: Ensures secure and reliable connections for cables used in various automotive systems, including control cables and electrical wiring.
3. Construction and Infrastructure
Swaging is critical in the construction industry for components that require strength and durability:
Swaging Rebar: Used to create reinforced concrete structures. Swaged rebar improves the strength and bonding of concrete.
Swaging Rods and Bars: Utilized in structural frameworks and support systems, ensuring robust and reliable construction.
4. Electrical and Telecommunications
In the electrical and telecommunications industries, swaging ensures the integrity and reliability of connections:
Swaging Cable Connectors: Provides secure terminations for cables used in power distribution and telecommunications. This application ensures optimal performance and minimal signal loss.
Swaging Terminals: Used to attach terminals to wires, facilitating reliable electrical connections in various devices and systems.
5. Medical Devices
Swaging is also employed in the medical field to manufacture components that require high precision and reliability:
Swaging Needles and Cannulas: Ensures the accurate formation of needles and cannulas used in medical procedures. Swaged components must meet stringent hygiene and performance standards.
Swaging Medical Tubing: Provides the necessary strength and flexibility for medical tubing used in various applications, including IV lines and catheter systems.
6. Marine Industry
In the marine industry, swaging is used for components that must withstand harsh environments:
Swaging Cable Assemblies: Ensures the integrity of cables used in marine applications, such as rigging and mooring lines. Swaged assemblies offer resistance to corrosion and mechanical stress.
Swaging Fittings: Used in marine equipment and structures to ensure secure and reliable connections in challenging conditions.
7. Consumer Goods
Swaging also finds applications in consumer products where precision and durability are essential:
Swaging Jewelry Components: Provides precise shaping of jewelry pieces, such as clasps and links, ensuring both aesthetic appeal and functionality.
Swaging Hardware: Used in various consumer products, including tools and appliances, to ensure durability and performance.
Why Choose Welleshaft for Your Swaging Needs?
When it comes to precision swaging, Welleshaft stands out as a trusted global supplier and contract manufacturer. Here’s why:
1.Advanced Swaging Equipment
Welleshaft uses state-of-the-art swaging machines to deliver precise, high-quality components tailored to your specifications.
2.Customization
With Welleshaft, you can expect fully customized solutions. Whether you need swaged tubes, rods, or cables, they can deliver components that meet even the most demanding requirements.
3.Experience Across Industries
Welleshaft serves a broad range of industries, including aerospace, automotive, and construction. Their expertise ensures that you get the highest quality swaged components, no matter your sector.
4.Global Reach, Local Support
With manufacturing facilities and partnerships around the world, Welleshaft can deliver your components wherever you need them. Their global network ensures timely delivery and superior quality control.
5.High Profit Margins
Welleshaft offers competitive pricing and high-quality products, allowing businesses to maintain high profit margins without sacrificing performance.
Conclusion
Swaging is an invaluable process for producing high-quality, precise components across various industries. From tubes and rods to cables, the applications are vast and varied. For those seeking reliable, cost-effective swaging services, Welleshaft is the ideal partner. With advanced machinery, industry expertise, and a global supply network, they are a trusted name in precision manufacturing.
If you’re looking to enhance your manufacturing process with custom swaged components, Welleshaft provides the precision and quality you need to stay ahead in today’s competitive market.