Forging Stainless Steel Components | Precision & Custom Solutions
Forging stainless steel components requires a deep understanding of the material’s properties, specialized techniques, and precision to create products that meet diverse industry standards. Stainless steel is highly valued for its strength, corrosion resistance, and aesthetic appeal. In this article, we will explore the process of forging stainless steel, its benefits, and how custom solutions can be achieved through expert craftsmanship. We also highlight Welleshaft, a global supplier known for delivering top-quality stainless steel forging services.
Section 1: The Basics of Forging Stainless Steel
Stainless steel forging refers to the process of shaping stainless steel by applying compressive forces. This process significantly enhances the strength, toughness, and durability of the metal, making it ideal for applications in aerospace, automotive, medical, and other high-performance industries. Forged stainless steel components are known for their superior grain structure and resistance to wear and corrosion.
1. Can You Forge Stainless Steel?
Yes, stainless steel can be forged using the appropriate techniques and equipment. The key to forging stainless steel lies in its high forging temperature and the careful control of heat during the process. By using precise temperature controls and advanced forging methods, manufacturers can ensure that the material’s integrity remains intact while achieving the desired shape.
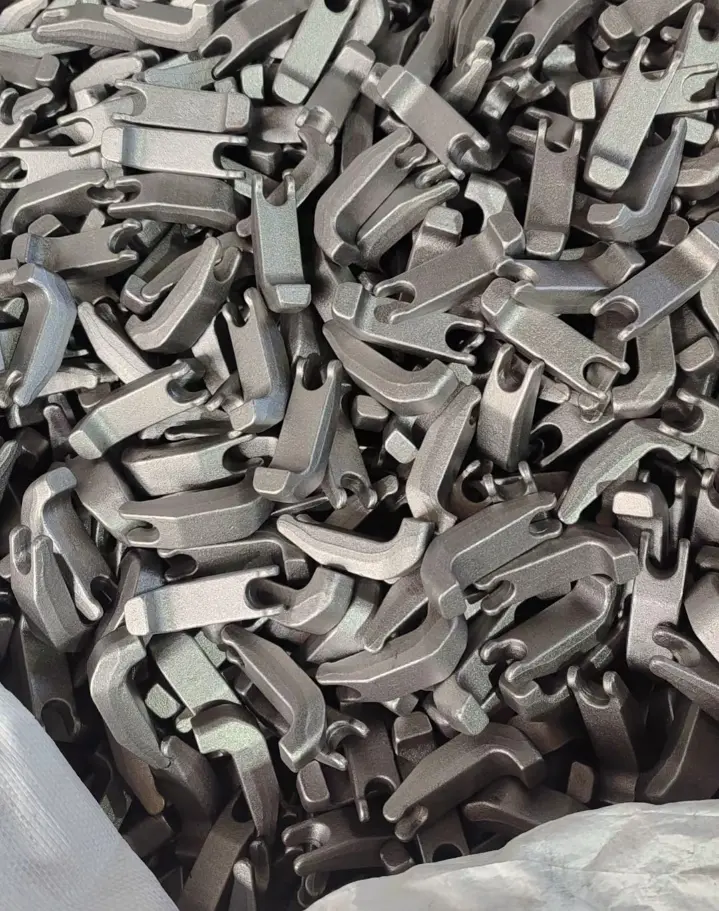
Section 2: Forging Stainless Steel vs. Cast Stainless Steel
1. Is Stainless Steel Cast or Forged?
Stainless steel can be both cast and forged, but the two processes produce materials with different properties. Forging stainless steel involves compressing and shaping the metal, which refines its grain structure and enhances its mechanical properties. On the other hand, casting stainless steel involves pouring molten metal into molds to create shapes, which is more suitable for complex geometries but often results in weaker grain structures.
2. Is Forged Stainless Steel Better?
Forged stainless steel is generally superior in terms of strength, toughness, and impact resistance. Because of the compression and deformation during forging, the metal gains a denser and more uniform internal structure, making it more reliable for critical applications. In contrast, cast stainless steel, while more flexible in design, is less durable in terms of structural integrity.
Section 3: Custom Solutions in Stainless Steel Forging
Customization is essential in modern manufacturing, particularly when forging stainless steel. Welleshaft, a global supplier and contract manufacturer, specializes in providing custom forged stainless steel components for various industries. Whether it’s precision stainless steel forgings for aerospace or durable parts for the oil and gas sector, Welleshaft ensures that every component meets stringent specifications and quality standards.
1. Stainless Steel Forging Specifications
Welleshaft offers a wide range of stainless steel grades, including the popular 304 stainless steel, which can be forged for applications requiring high corrosion resistance and durability. By tailoring the forging process to each project’s specific requirements, Welleshaft can deliver components that fit perfectly into the client’s operational needs.
2. Common Stainless Steel Grades for Forging
Different stainless steel grades are used in forging depending on the specific application and performance requirements. The most commonly used grades include:
304 Stainless Steel: The most widely used stainless steel for general forging applications, known for its corrosion resistance, good formability, and weldability. It’s often used in food processing, chemical equipment, and architectural applications.
316 Stainless Steel: Offers superior corrosion resistance, especially in environments with saltwater or harsh chemicals. It is commonly used in marine, chemical processing, and pharmaceutical industries.
410 Stainless Steel: A martensitic stainless steel that offers high strength and hardness with moderate corrosion resistance. It is used in aerospace and automotive applications requiring wear resistance.
440C Stainless Steel: High-carbon stainless steel used in applications requiring high hardness, such as cutting tools, ball bearings, and valve components.
17-4 PH Stainless Steel: A precipitation-hardened grade that offers high strength and corrosion resistance. It is ideal for aerospace and mechanical components that require high toughness.
Each grade comes with its unique properties, which impact the forging process and final application.
3. Stainless Steel Forging Temperature and Process
The forging temperature of stainless steel typically ranges between 1700°F and 2300°F (927°C to 1260°C), depending on the grade. Proper control of the forging temperature is critical to maintaining the material’s properties. Stainless steel forging involves several stages, including heating, deforming, and cooling, all carefully monitored to ensure the material’s strength and reliability.
Section 4: The Benefits of Forged Stainless Steel Components
1. Strength and Durability
Forged stainless steel components are highly sought after for their strength and durability. The forging process compacts the metal, refining its structure and increasing its resistance to impact, fatigue, and wear. These characteristics make it ideal for industries like aerospace, where reliability and safety are paramount.
2. Corrosion Resistance
One of the primary reasons stainless steel is used in so many industries is its excellent corrosion resistance. By forging stainless steel, manufacturers can enhance its resistance to rust and corrosion, ensuring that the components maintain their integrity even in harsh environments, such as marine or chemical processing industries.
3. Precision and Customization
The ability to customize stainless steel components through forging allows manufacturers to meet exact specifications for each project. Welleshaft is known for its precision forging services, delivering components that meet or exceed industry standards. Their commitment to high-quality custom solutions has made them a trusted partner for companies worldwide.
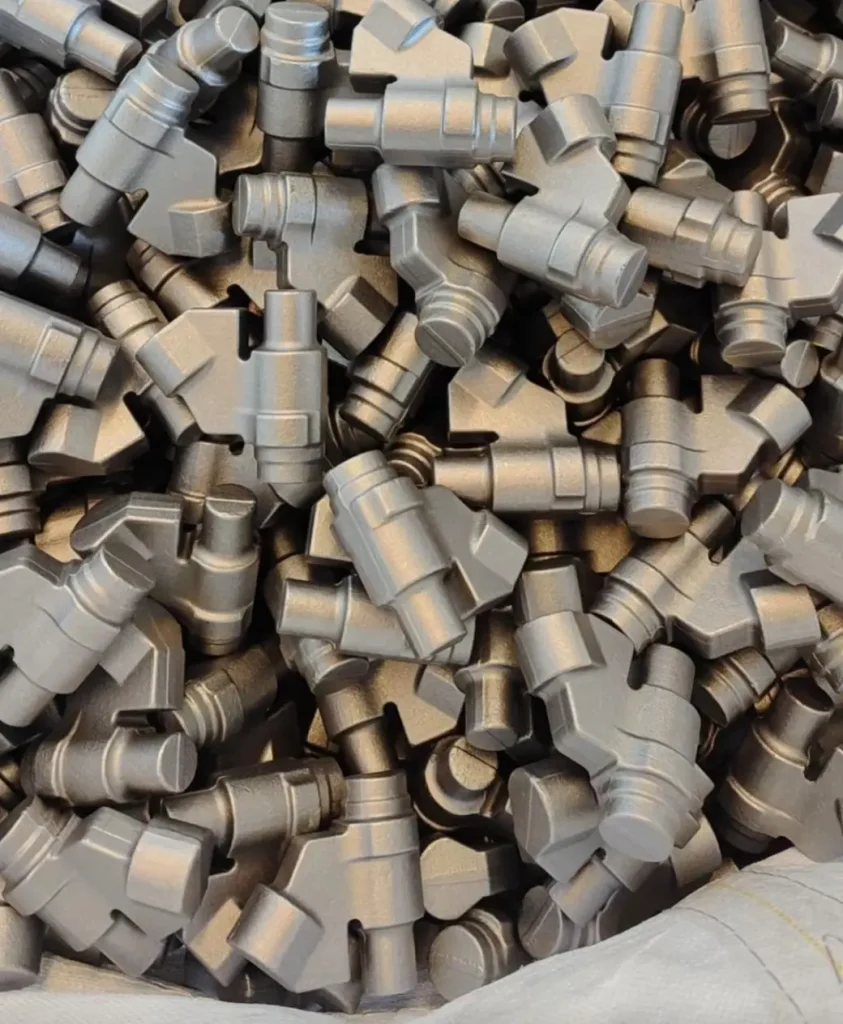
Section 5: Applications of Forged Stainless Steel Components
Forged stainless steel components are used in a variety of industries, including:
1. Aerospace Industry
In aerospace, forged stainless steel components are critical due to the need for high strength, reliability, and resistance to extreme temperatures. Key applications include:
Landing Gear: Stainless steel forgings provide the strength needed to withstand the immense forces experienced during takeoff and landing.
Engine Components: Parts such as turbine blades and casings require materials that can endure high temperatures and stresses, making forged stainless steel an excellent choice.
Structural Components: High-strength stainless steel is used in the construction of critical airframe parts to ensure safety and durability.
2. Automotive Industry
The automotive industry relies heavily on forged stainless steel parts for various components that must withstand significant wear and mechanical stress. Examples include:
Crankshafts and Gears: Forged stainless steel crankshafts and gears are more durable and offer better performance than cast or machined parts.
Axles and Steering Components: The strength and toughness of forged stainless steel ensure the reliability and longevity of critical drivetrain parts.
Suspension Parts: Forged components in the suspension system are essential for maintaining vehicle stability and handling under various conditions.
3. Oil and Gas Industry
In the oil and gas sector, equipment must withstand harsh environments, including high pressure, extreme temperatures, and corrosive conditions. Forged stainless steel components provide the necessary reliability for:
Valves and Fittings: Forged stainless steel valves and fittings are used in pipelines, drilling rigs, and processing plants due to their high resistance to corrosion and wear.
Piping Components: Stainless steel forgings offer enhanced durability for high-pressure pipelines, ensuring long-term safety and efficiency.
Flanges and Connectors: Forged stainless steel flanges and connectors are critical for maintaining the integrity of pipelines and other infrastructure.
4. Medical Industry
The medical industry demands precision and biocompatibility in its equipment, and forged stainless steel is ideal for applications where hygiene and strength are critical. Common applications include:
Surgical Instruments: Forged stainless steel ensures sharpness, strength, and corrosion resistance in surgical tools like scalpels, forceps, and scissors.
Implants: Stainless steel implants, such as bone screws and joint replacements, are forged to ensure durability and compatibility with the human body.
Dental Instruments: Forged stainless steel provides the necessary precision and hygiene standards required for dental equipment.
5. Food Processing Industry
In food processing, components must resist corrosion and be easily cleaned to prevent contamination. Forged stainless steel parts are widely used in:
Food Processing Machinery: Forged components such as blades, gears, and seals are essential in food production equipment where durability and cleanliness are critical.
Cutlery and Flatware: High-end forged stainless steel flatware offers durability, resistance to corrosion, and aesthetic appeal.
Valves and Pumps: Forged stainless steel valves and pumps ensure food safety by preventing contamination and maintaining hygiene.
6. Power Generation Industry
Power plants require components that can operate reliably under high stress and in extreme conditions. Forged stainless steel is commonly used for:
Turbine Shafts: Forged stainless steel turbine shafts offer high strength and fatigue resistance, essential for consistent power generation.
Boiler Components: Stainless steel forgings used in boilers and heat exchangers must endure high temperatures and corrosive environments.
Nuclear Plant Components: Forged stainless steel is critical in nuclear power plants due to its ability to withstand radiation, high pressure, and extreme heat.
7. Marine Industry
Marine environments are highly corrosive due to saltwater exposure, making forged stainless steel an ideal material for components used in:
Shipbuilding: Forged stainless steel is used in propellers, shafts, and structural parts of ships to prevent corrosion and ensure longevity.
Offshore Drilling Equipment: Forged stainless steel components provide resistance to corrosion and mechanical stress in offshore oil rigs and drilling platforms.
Marine Fasteners: High-strength, corrosion-resistant forged stainless steel fasteners are essential in maintaining the integrity of marine vessels and equipment.
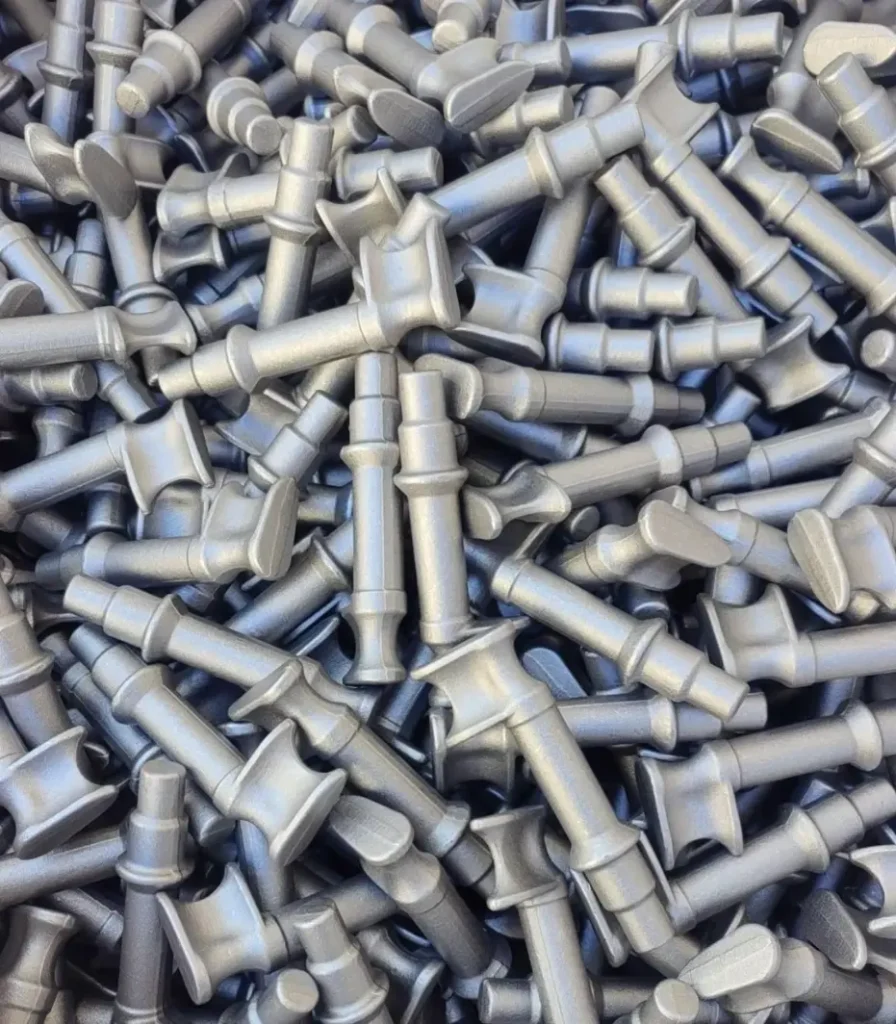
Section 6: Choosing Welleshaft for Stainless Steel Forging
Welleshaft is a global leader in stainless steel forging, providing high-quality forged components tailored to your needs. Their expertise in custom forgings ensures that every project meets the client’s exact specifications. Whether you need small-scale precision parts or large industrial components, Welleshaft delivers with precision, reliability, and excellent customer service.
Why Welleshaft?
Global Reach: Welleshaft serves clients worldwide, ensuring fast delivery and excellent communication.
Customization: Their team works closely with clients to provide tailored solutions that fit their unique needs.
High-Quality Standards: Welleshaft uses the latest technology and adheres to strict quality control measures to ensure the highest level of craftsmanship.
Conclusion
Forging stainless steel offers numerous advantages, from increased strength and durability to enhanced corrosion resistance. Whether you’re in the aerospace, automotive, or medical industry, custom stainless steel forgings provide the reliability and performance you need. Welleshaft stands out as a global supplier of high-quality forged stainless steel components, offering precision, customization, and trustworthiness in every project.
By partnering with Welleshaft, you ensure that your components meet the highest standards, backed by a company known for its expertise and global presence. Reach out to Welleshaft today for all your stainless steel forging needs.