Powder Forming: Advanced Techniques & Applications in Metal Sintering
In the evolving world of manufacturing, powder forming has emerged as a cornerstone technique, particularly in metal sintering processes. This advanced method allows for the precise shaping of metal powders into robust and intricate parts, making it a preferred choice in industries that demand high-quality, high-performance components. This article delves into the advanced techniques and applications of powder forming, highlighting its significance in modern manufacturing.
Section 1: What is Powder Forming?
Powder forming is a manufacturing process that involves the compaction of metal powders into a desired shape, followed by sintering to form a solid piece. This process enables the creation of components with complex geometries that would be challenging to achieve through traditional methods such as casting or forging. Powder forming is particularly useful for producing small, intricate parts with excellent material properties.
1.1.The Powder Forming Process
The powder forming process consists of several stages, each critical to achieving the desired outcome. The stages include:
Powder Preparation: High-quality metal powders are selected and prepared, ensuring the right particle size and distribution for optimal compaction and sintering.
Compaction: The metal powder is compressed in a die under high pressure to form a compacted shape. This step is crucial for defining the final geometry of the part.
Sintering: The compacted powder is heated to a temperature below its melting point, allowing the particles to bond together without liquefying. This results in a dense and strong final product.
Secondary Operations: Depending on the application, the sintered part may undergo additional processes such as machining, heat treatment, or surface finishing to achieve the required specifications.
Section 2: Advanced Powder Forming Techniques
Several advanced techniques have been developed to enhance the powder forming process, making it more efficient and versatile. These include:
1. Hot Isostatic Pressing (HIP)
Hot Isostatic Pressing (HIP) involves applying both heat and pressure uniformly to a metal powder compact. This technique improves the density and mechanical properties of the final product, making it ideal for critical applications in aerospace and medical industries.
2. Metal Injection Molding (MIM)
Metal Injection Molding (MIM) combines the benefits of plastic injection molding with powder forming. This method allows for the mass production of small, complex parts with excellent dimensional accuracy. MIM is commonly used in the automotive, consumer electronics, and medical device sectors.
3. Additive Manufacturing (AM)
Additive Manufacturing (AM), or 3D printing, has revolutionized powder forming by enabling the creation of parts layer by layer directly from a digital model. This technique offers unparalleled design flexibility and is used in industries ranging from aerospace to biomedical engineering.
Section 3: Applications of Powder Forming
Powder forming is employed across various industries due to its ability to produce high-quality parts with complex geometries and excellent material properties. Some notable applications include:
1. Automotive Industry
In the automotive industry, powder forming is used to manufacture components such as gears, bearings, and engine parts. These components require high strength, wear resistance, and precision, all of which can be achieved through powder forming.
2. Aerospace Industry
The aerospace industry demands lightweight and strong materials. Powder forming is utilized to produce turbine blades, structural components, and fasteners that meet these stringent requirements.
3. Medical Industry
In the medical industry, powder forming is used to create implants, surgical tools, and other critical components. The ability to produce parts with biocompatible materials and intricate designs makes powder forming a valuable technique in this field.
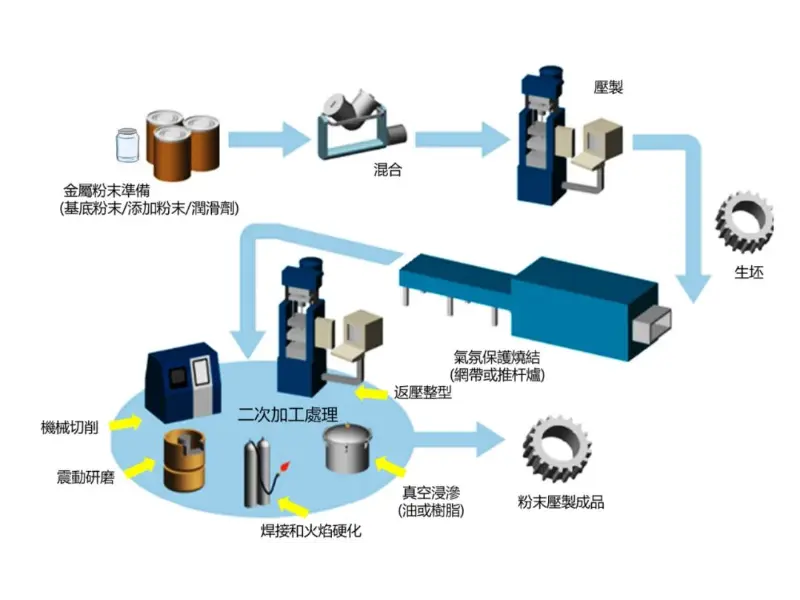
Section 4: Frequently Asked Questions
What is Powder Processing?
Powder processing refers to the broader set of techniques used to handle, modify, and transform metal powders into functional products. This includes processes such as mixing, milling, and classification, which are essential for achieving the desired properties in the final product.
What is the Meaning of Powder Form?
The meaning of powder form pertains to the physical state of a material when it is composed of fine particles. In the context of metal sintering, powder form allows for easy compaction and shaping into desired geometries, making it a crucial starting point for the powder forming process.
What is Powder Formed Steel?
Powder formed steel is a type of steel that is produced through the powder forming process. This method allows for the creation of steel components with enhanced properties such as uniform microstructure, improved strength, and superior wear resistance. Powder formed steel is commonly used in high-performance applications where these attributes are essential.
What is Powder Formulation?
Powder formulation involves the precise combination of different metal powders to achieve specific characteristics in the final product. This process requires a deep understanding of material science and is critical for tailoring the properties of components to meet specific application requirements.
Why Choose Powder Forming?
Powder forming offers numerous advantages over traditional manufacturing methods. These include:
- Precision and Complexity: Powder forming allows for the creation of highly intricate parts with tight tolerances, which would be difficult to achieve through other methods.
- Material Efficiency: The process minimizes material waste, making it a cost-effective solution for producing small to medium-sized components.
- Enhanced Material Properties: Components produced through powder forming often exhibit superior mechanical properties, such as higher strength and better wear resistance.
Section 5: Welleshaft: Your Trusted Global Supplier and Contract Manufacturer
When it comes to powder forming and metal sintering, Welleshaft stands out as a trusted global supplier and contract manufacturer. With years of experience and expertise in the field, Welleshaft offers a comprehensive range of services, from powder preparation to final component production. Whether you require custom metal parts or large-scale production runs, Welleshaft delivers high-quality solutions tailored to your specific needs.
Conclusion
Powder forming is a critical process in modern manufacturing, enabling the production of high-quality, complex parts with excellent material properties. With advanced techniques such as Hot Isostatic Pressing, Metal Injection Molding, and Additive Manufacturing, the possibilities for innovation are endless. Whether in automotive, aerospace, or medical industries, powder forming continues to play a pivotal role in shaping the future of manufacturing.
For reliable and efficient powder forming solutions, trust Welleshaft as your global supplier and contract manufacturer. With our expertise and commitment to quality, we ensure that your components meet the highest standards of performance and durability.