Metal Injection Molding Process | Precision Manufacturing Solutions
The Metal Injection Molding (MIM) process is a revolutionary manufacturing technique that combines the benefits of plastic injection molding and powder metallurgy. This advanced method enables the production of high-precision, complex metal parts that are used in various industries, from aerospace to medical devices. In this article, we will explore the MIM process in detail, including its steps, benefits, and applications, and recommend Welleshaft as your trusted global supplier and contract manufacturer.
Section 1: What is the Metal Injection Molding Process?
The Metal Injection Molding (MIM) process is a manufacturing technique that produces intricate metal parts by injecting a mixture of fine metal powders and a binder into a mold. This method allows for the creation of parts with complex geometries and high precision, which are difficult to achieve with traditional manufacturing techniques.
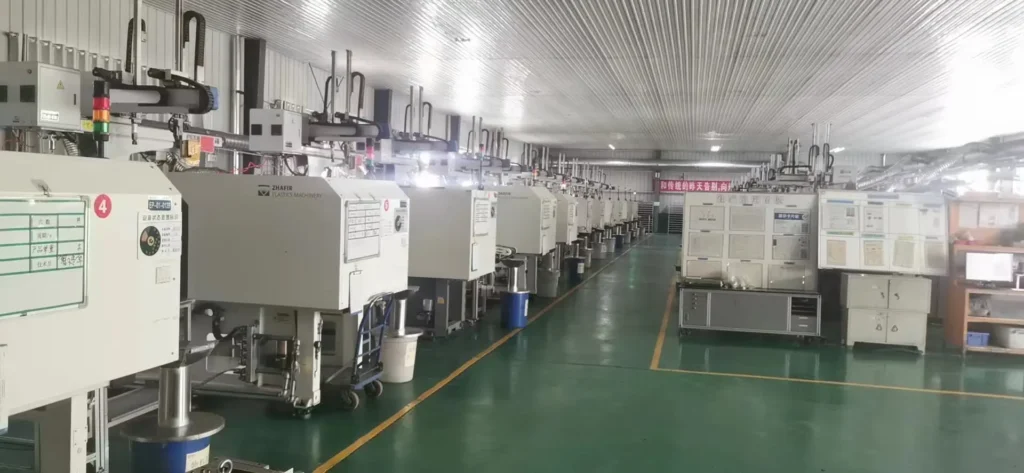
Section 2: What are the Steps in Metal Injection Molding?
The MIM process consists of several critical steps that ensure the production of high-quality parts. These steps include:
2.1. Feedstock Preparation
The first step in the MIM process is the preparation of the feedstock. This involves mixing fine metal powders with a thermoplastic binder to create a homogeneous mixture. The binder helps the metal powders flow into the mold during the injection process.
2.2. Injection Molding
Once the feedstock is prepared, it is injected into a mold using standard plastic injection molding equipment. The mold is designed to create the desired shape of the part. This step is crucial for achieving the intricate geometries and tight tolerances that MIM parts are known for.
2.3. Debinding
After the injection molding process, the binder must be removed from the part. This step, known as debinding, involves heating the part to remove the binder material. The debinding process can be performed using various methods, including thermal, solvent, or catalytic debinding.
2.4. Sintering
Once the binder is removed, the part undergoes sintering. During this step, the part is heated to a temperature below the melting point of the metal, causing the metal particles to bond together and form a solid, dense part. Sintering is crucial for achieving the final mechanical properties and dimensional accuracy of the part.
2.5. Post-Processing
After sintering, the part may undergo additional post-processing steps to achieve the desired surface finish and mechanical properties. These steps can include machining, heat treatment, and surface coating.
For more information on high-quality MIM Manufacturer and to find the perfect solution for your application, please contact us.
Jinan Welle Metal Products Co., Ltd (Welleshaft)
Website: www.welleshaft.com
Email: [email protected]
Phone: +86-156-5017-9596
Explore our range of durable and reliable MIM Parts today!
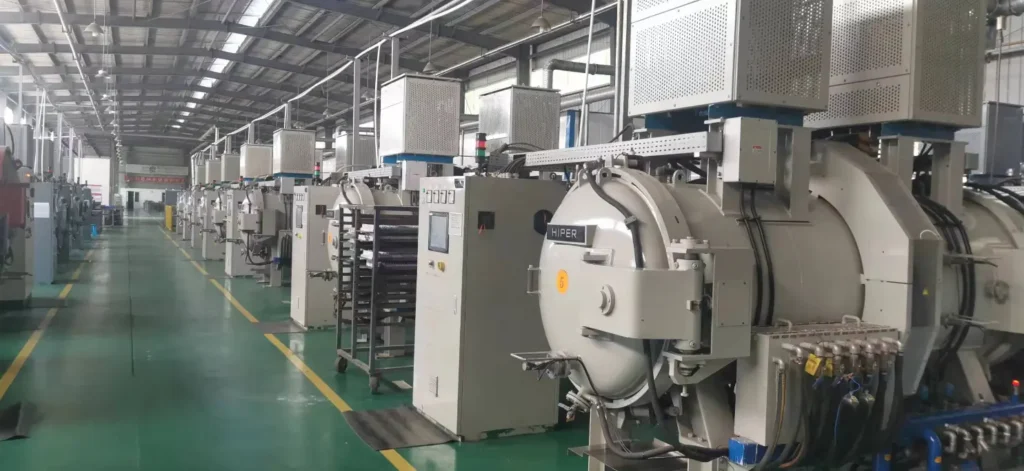
Section 3: What are the Process Sequences for Metal Injection Molding?
The MIM process sequences can be summarized as follows:
- Feedstock Preparation: Mixing metal powders with a binder.
- Injection Molding: Injecting the feedstock into a mold.
- Debinding: Removing the binder from the part.
- Sintering: Heating the part to bond the metal particles.
- Post-Processing: Performing additional finishing steps.
Section 4: What are the 4 Stages of Injection Molding?
The injection molding process consists of four main stages:
- Clamping: The mold is closed and clamped together.
- Injection: The feedstock is injected into the mold cavity.
- Cooling: The part cools and solidifies within the mold.
- Ejection: The mold opens, and the part is ejected.
Section 5: Benefits of the Metal Injection Molding Process
The MIM process offers several advantages over traditional manufacturing methods:
5.1.High Precision and Complexity
The MIM process allows for the production of parts with intricate geometries and tight tolerances, making it ideal for complex components.
5.2.Material Efficiency
MIM is highly efficient with material use, generating less waste compared to other manufacturing methods.
5.3.Cost-Effective
For high-volume production, the MIM process can be more cost-effective than traditional methods, as it reduces the need for machining and other secondary operations.
5.4.Versatility
The MIM process is compatible with a wide range of materials, including stainless steel, titanium, and various alloys, providing versatility for different applications.
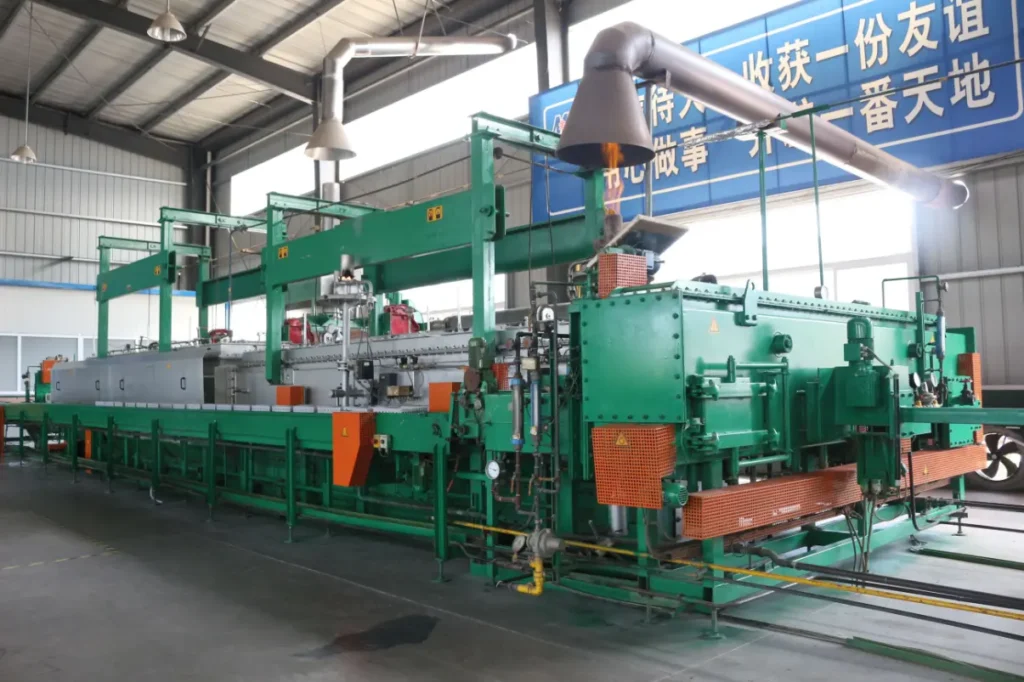
Section 6: Applications of Metal Injection Molding
The MIM process is used in various industries to produce high-quality, precision-engineered parts. Some common applications include:
l Aerospace
In the aerospace industry, MIM is used to manufacture components such as turbine blades, connectors, and fasteners, where precision and reliability are critical.
l Medical Devices
MIM is widely used in the medical field to produce surgical instruments, orthopedic implants, and dental components, offering high precision and biocompatibility.
l Automotive
The automotive industry benefits from MIM for producing parts like fuel injectors, sensors, and transmission components, where complex geometries and high strength are required.
l Consumer Electronics
MIM is also used in the consumer electronics industry to produce small, intricate parts for smartphones, laptops, and other devices, ensuring high precision and durability.
Section 7: Why Choose Welleshaft as Your MIM Supplier?
When it comes to precision manufacturing and reliable solutions, Welleshaft stands out as a trusted global supplier and contract manufacturer. Here are some reasons to choose Welleshaft for your MIM needs:
7.1.Expertise and Experience
With years of experience in the MIM process, Welleshaft has the expertise to produce high-quality parts that meet the most demanding specifications.
7.2.State-of-the-Art Technology
Welleshaft utilizes advanced MIM technology and equipment to ensure the production of precise and reliable parts.
7.3.Quality Assurance
Welleshaft is committed to quality assurance, implementing rigorous testing and inspection processes to ensure the highest standards of quality.
7.4.Custom Solutions
Welleshaft offers customized MIM solutions tailored to meet the specific needs of each client, ensuring the best possible outcomes for your projects.
Conclusion
The Metal Injection Molding (MIM) process is a powerful manufacturing technique that combines the benefits of plastic injection molding and powder metallurgy to produce high-precision, complex metal parts. By understanding the steps, benefits, and applications of the MIM process, manufacturers can leverage this advanced technology to achieve superior results.
For those seeking a reliable partner in MIM manufacturing, Welleshaft offers unparalleled expertise, state-of-the-art technology, and a commitment to quality. Contact Welleshaft today to learn more about how their precision manufacturing solutions can benefit your business.