Gear manufacturing offers competitive advantages through new ways to enhance performance, all while ensuring lower costs in business operations. Let’s discuss gear manufacturing processes, benefits, applications, and factors to consider when contracting a gear manufacturer.
Section 1: What is Gear Manufacturing?
Gear manufacturing is the process of developing mechanical parts that transmit power and motion between machine parts. Different shapes and sizes of gears are made to suit specific functions in machines, such as those applied in car machines and industrial equipment. Materials selection at the design stage includes advanced methods so that the gears can meet the required standards and work properly.
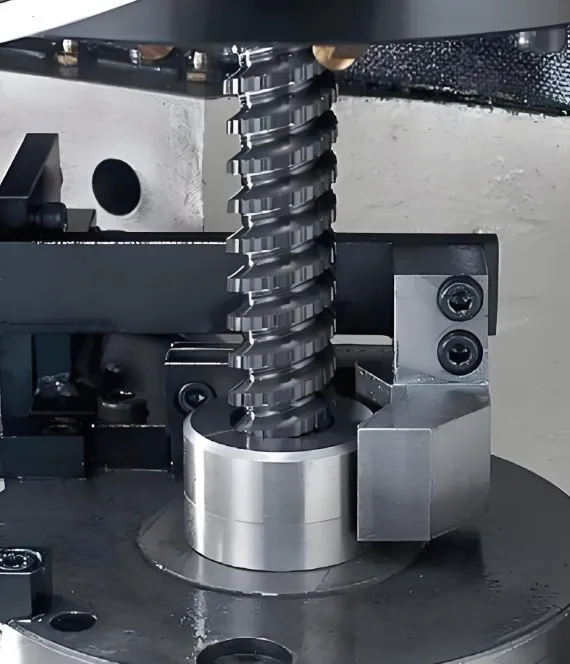
Section 2: Key Steps in Gear Manufacturing
Design Engineering
The application of the gear is strategised before manufacturing. It would decide on a spur, helical, bevel, or worm gear and its size, material, and tooth shape. These complex gears are designed with sophisticated CAD technologies.
Material selection
It is vital for the life and working of the gear. Material examples are steel, aluminium, brass, and plastic. Of course, these materials have very different properties for various applications. Where one material could be solid and hard-wearing, such as steel, another, like plastic gears, shall be light and noncorroding for light loads and less demanding applications.
Cut and Shape
This is followed by design, material selection, gear cutting, and shaping. All these methods have their advantages, and the choice of one depends on the gear specifications and the precision required. Hobbing spur and helical gears to attain efficiency and accuracy in the finished product, and grinding completes the finish for precision and surface quality.
Heat treatment
Strengthening and providing wear resistance for gears is essential. Quenching, tempering, and carburising are ways to modify material properties. This process imparts carbon into steel gears to give them the desired hardness and wear resistance; quenching cements these desirable properties quickly.
Finishing
This is the last process in gear manufacturing that improves performance and life. Honing, polishing, and lapping reduce friction, which eventually leads to an increase in the gear’s performance. Good finishing greatly reduces wear, noise, and inefficiency in gears.
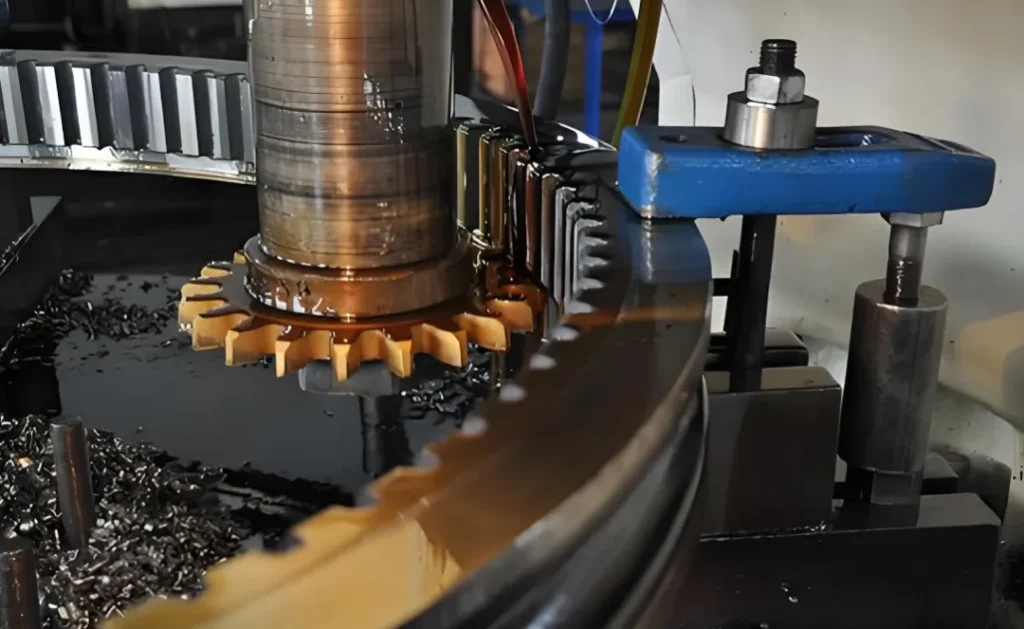
Section 3: Benefits of Modern Gear Manufacturing
Modern methods of gear manufacturing have several benefits that can leverage business. Of these benefits:
Accuracy and Precision
Advanced manufacturing methods enhance the performance and reliability of gears through accuracy and precision. This precision is also demanded by the aerospace and automotive industries since even a small variation may trigger big problems.
Cost-effectiveness
Automation and optimisation reduce manufacturing costs and lead time. CNC machines can produce at high speed without generating waste, hence saving costs.
Customisation
Modern technologies allow the making of a variety of customised gears. That flexibility enables companies to develop gears that best suit their applications, making their machines more versatile and adaptable.
Durability
Gears made with improved materials and heat treatment are more durable and require less maintenance than traditional ones. Suitable gears can support enormous loads and rugged operating conditions, decreasing downtime and maintenance.
Environmental Impact
Greener modern gear manufacture is due to energy-efficient machinery and waste reduction. These practices save money and boost a company’s green image.
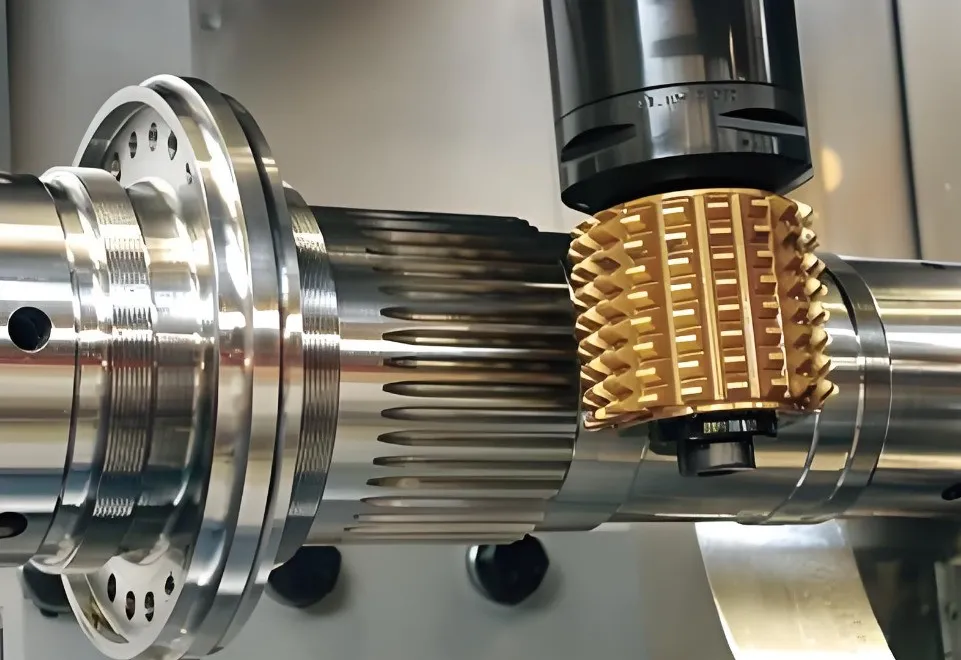
Section 4: Uses of Gear Manufacturing
Modern methods of gear production are essential in various industries. The following benefit immensely from enhanced gear production:
The Automobile industry
Gears play a very important role in this field, particularly in gearbox systems. Modern-day techniques for making car gears make them strong, more accurate, and stress-resilient, thus improving vehicle performance and reliability. Steering systems, differentials, and power trains are other vehicle parts that use gears.
Aerospace Industry
The gears required in an aircraft have to be high-precision, reliable, and light. In fact, gears are used even in engines, landing gear systems, and controls inside a plane. With the modern ways of manufacturing gears, the aerospace industry’s safety and performance criteria are utterly achievable, making aircraft operations safer and more efficient.
Industry Equipment
Gears are utilised in manufacturing machinery, conveyor systems, and heavy equipment. High-quality gears allow machines to move smoothly while increasing production with less downtime. Modern manufacturing processes fabricate strong, precise gears that support heavy loads while also challenging the most extreme operation situations.
Robotics and Automation
In robotics and automation systems, gears transfer motion and precisely position robotic arms, actuators, and other mechanical parts. New gear production methods may create special gears for particular robotics uses, drastically improving their potential and performance.
Renewable Energy
Modern gear manufacturing supports renewable energy, especially wind energy. Windmill gears are applied in the transmission box and turned around with the blades to convert movement into power. High-quality gears must be effective and long-lasting for windmills; thus, renewable energy can survive and prosper.
Medical Equipment
Gears are used with most medical equipment, from surgical instruments and image devices to patient care gadgets. Modern methods of manufacturing gears ensure that they are precise, reliable, and medical grade. Good-quality gears not only mean better patient care but also assures the outcome by ensuring that the medical equipment works safely and effectively.
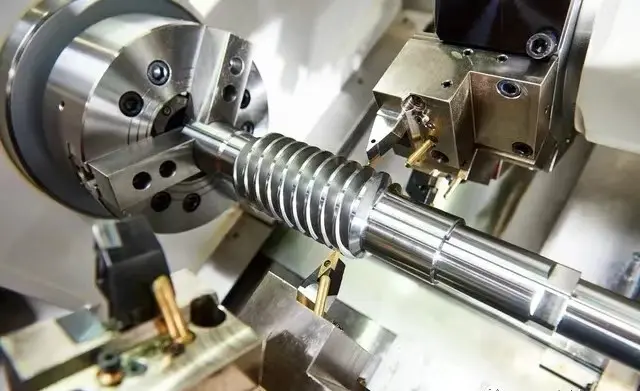
Section 5: How to Choose the Right Gear Manufacturer
One should choose the proper manufacturer to have quality and reliability in gear. The variables that must be accommodated while picking gear manufacturer include:
Skill and Experience
Look for a manufacturing company with experience in the industry. An experienced manufacturer can clearly understand your requirements and thus develop high-quality solutions.
Technology and Innovation
Be sure that it uses state-of-the-art technology and the latest methods available. Only those manufacturers who apply the most modern technology can produce exact and quality gears.
Protection of quality
The manufacturer should have a quality assurance process ensuring the gears meet all the required standards and specifications.
Ability to customise
Special gears for your application are crucial. A manufacturer that is flexible enough to design and produce these gears that meet your requirements should be necessary.
Customer Support
A reputable manufacturer comes with reputable customer and after-sale support services. These include technical support, effective problem-solving, maintenance, and repair.
Section 6: Best Practices in Gear Manufacturing
Best practices in gear manufacturing can lead to improved quality and productivity. Some of the best practices that a manufacturer can adapt to include, but not limited to:
Maintenance Regularly
This maintenance will assist you in running the machinery. Regular maintenance averts malfunction and smooths production.
Training and Development
Training and development of the workforce are indispensable for high-quality gear production. A skilled workforce can use the latest production technologies to produce high-quality gear.
Quality Control
Every process involved in the production has to pass a quality control stage. This includes material inspection, monitoring of the manufacturing process, and final gear inspection to ensure the standards are met.
Sustainability
Steps towards sustainability can be taken to lower the environmental impact of gear manufacturing and enhance the energy efficiency of the machinery used, reducing waste. The sustainability strategy decreases costs and also improves the company’s reputation.
Continuously improve
The need to stay competitive always remains, so a culture of continuous improvement is needed. This has to include reviewing and assessing manufacturing processes for upgrading and embracing new technology. It also includes asking customers for input, which will help improve products and services.
Conclusion
Modern gear manufacturing provides a solid industrial base for precision, efficiency, and innovation tools. One can use such strides in business activity to increase growth rates by pointing to the most principal and advantageous signs in gear-making.
See what today’s gear manufacturing does for businesses. Contact us for additional information and the best advice.
Frequently Asked Questions
- How does modern gear manufacturing benefit my business?
Modern gear manufacturing methods enhance precision, reduce costs, and enhance resistance, enhancing overall business productivity.
- What industries can utilise the advanced gear manufacturing technique?
Gear manufacturing advancements are applied in industries such as automotive, aerospace, industrial equipment, robotics, renewable energy, and medical equipment.
- What should I look for in a gear manufacturer?
Look for experience, technology adoption, quality assurance, customisation ability, and customer support in a gear manufacturer.
- What are the significant process steps in manufacturing gears?
The process’s primary steps include design engineering, material selection, cutting and shaping, heat treatment, and finishing.