Lightweight 30mm Tubular Shafts – High Strength, Hollow Construction
In today’s engineering landscape, the demand for lightweight components that don’t compromise on strength is paramount. The 30mm tubular shaft, characterized by its hollow construction, has emerged as a versatile solution across various industries. This article explores the benefits of lightweight 30mm tubular shafts, focusing on their high strength, hollow construction advantages, material options, and applications. We’ll also highlight Welleshaft as a trusted global supplier and contract manufacturer.
What are 30mm Tubular Shafts?
A 30mm tubular shaft is a cylindrical component with an outer diameter of 30 millimeters and a hollow core. This hollow design distinguishes it from solid shafts, offering a unique combination of strength, weight reduction, and functionality. The “tubular” nature of the shaft implies a continuous, open passage through its center, often referred to as a bore or inner diameter. This bore can serve multiple purposes, such as reducing weight, accommodating internal components, or facilitating the passage of fluids or cables. They are commonly used for transmitting torque, supporting rotating components, or as structural elements in various mechanical systems.
Key Characteristics
Outer Diameter: Precisely 30mm.
Hollow Core: A defining feature enabling weight reduction and functional integration.
Material Variety: Manufactured from a range of materials, including steel, aluminum, stainless steel, and composites.
Length: Available in custom lengths to suit specific application requirements.
Machining Capabilities: Can be machined with keyways, splines, threads, and other features.
Hollow Construction Advantages
The hollow construction of 30mm tubular shafts offers several distinct advantages:
Weight Reduction: The primary benefit is a significant reduction in weight compared to solid shafts of the same diameter. This weight reduction is crucial in applications where minimizing mass is essential, such as aerospace, automotive, and robotics.
Increased Strength-to-Weight Ratio: Hollow shafts can achieve a higher strength-to-weight ratio than solid shafts of the same material and diameter. This is because the material is concentrated at the outer perimeter, where it contributes most to torsional stiffness and bending strength.
Cable and Fluid Routing: The hollow core provides a convenient pathway for routing cables, wires, or fluids through the shaft. This eliminates the need for external routing, simplifying design and improving aesthetics. This is especially useful in applications like medical devices and automated machinery.
Thermal Management: The hollow core can be used to circulate cooling fluids, helping to manage heat generated by friction or other sources.
Reduced Inertia: Lower weight translates to reduced inertia, making the shaft easier to accelerate and decelerate. This is beneficial in dynamic applications where rapid changes in speed or direction are required.
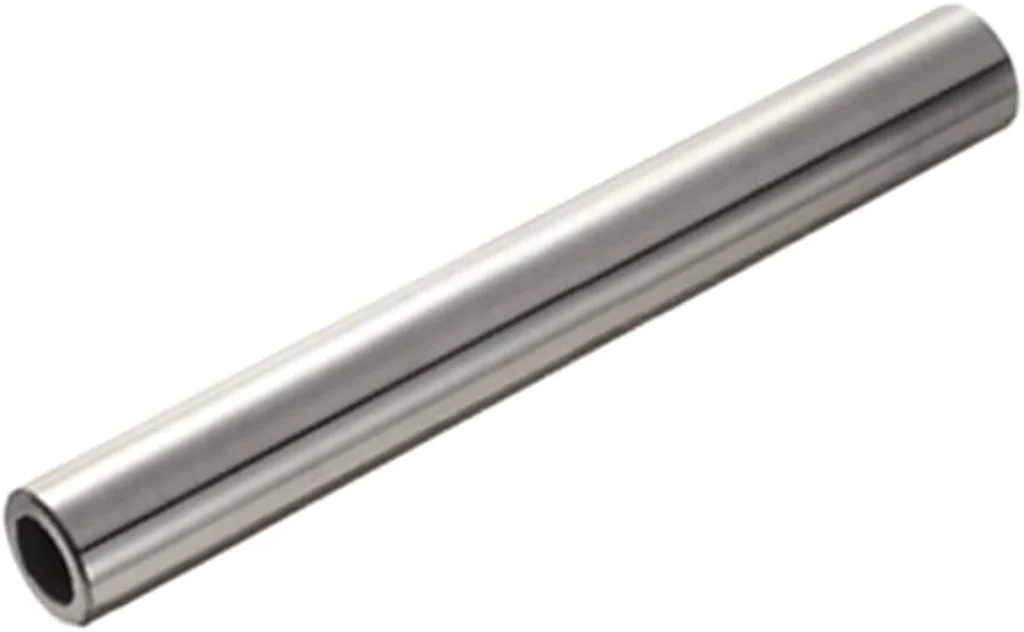
High Strength Considerations
While the hollow construction offers numerous benefits, concerns about strength are valid. The key to maintaining high strength in a 30mm tubular shaft lies in careful material selection and optimized design:
Material Selection: Choosing a material with high tensile strength and yield strength is critical. Steel alloys, such as high-carbon steel or alloy steel, offer excellent strength but are heavier. Aluminum alloys provide a good balance of strength and weight. Stainless steel offers corrosion resistance in addition to strength.
Wall Thickness: The wall thickness of the tubular shaft significantly impacts its strength. Thicker walls provide greater resistance to bending and torsion, but also increase weight. Finite Element Analysis (FEA) can be used to optimize wall thickness for a specific application.
Heat Treatment: Heat treatment processes, such as hardening and tempering, can significantly increase the strength and hardness of steel tubular shafts.
Surface Treatment: Surface treatments, such as coatings and plating, can improve corrosion resistance and wear resistance, extending the lifespan of the shaft.
Stress Concentrations: The design should minimize stress concentrations, particularly at the ends of the shaft and around any features like keyways or holes.
Materials Used in 30mm Tubular Shafts
The selection of the appropriate material for a 30mm tubular shaft depends on several factors, including:
Strength Requirements: How much load will the shaft be subjected to?
Weight Constraints: How critical is weight reduction?
Environmental Conditions: Will the shaft be exposed to corrosive elements or high temperatures?
Cost: What is the acceptable cost for the material?
Common materials include:
Steel Alloys: Offer high strength, stiffness, and durability. Commonly used for demanding applications where weight is not the primary concern. Various steel alloys can be used to further customize strength, hardness, and weldability. Examples: 1045 Steel, 4140 Steel.
Aluminum Alloys: Provide a good balance of strength and weight. Ideal for applications where weight reduction is critical. Aluminum alloys are also corrosion resistant. Examples: 6061 Aluminum, 7075 Aluminum.
Stainless Steel: Offers excellent corrosion resistance and strength. Suitable for applications in harsh environments, such as marine or chemical processing. Examples: 304 Stainless Steel, 316 Stainless Steel.
Composites: Offer the highest strength-to-weight ratio but are generally more expensive. Carbon fiber reinforced polymers (CFRP) are used in aerospace and high-performance applications.
Titanium Alloys: Provide exceptional strength-to-weight ratio and corrosion resistance but are very expensive. Used in highly specialized applications.
Applications of 30mm Tubular Shafts
30mm tubular shafts find applications across a wide range of industries:
Robotics: Lightweight arms and joints in robots.
Automation: Linear motion systems, conveyors, and automated machinery.
Aerospace: Actuator shafts, landing gear components, and structural supports.
Automotive: Driveshafts, steering columns, and suspension components.
Medical Devices: Endoscopic instruments, surgical tools, and medical imaging equipment.
Printing: Printing rollers
Textile Manufacturing: Textile rollers
Customization Options for 30mm Tubular Shafts
To meet the diverse needs of various applications, 30mm tubular shafts can be customized in several ways:
Length: Cut to specific lengths.
Material: Selection of the most appropriate material based on strength, weight, and environmental requirements.
Coatings: Application of coatings to improve corrosion resistance, wear resistance, or lubricity. Examples include chrome plating, nickel plating, and anodizing.
Machining: Integration of features like keyways, splines, threads, holes, and flanges.
Tolerances: Tight tolerances can be achieved through precision machining processes.
Surface Finish: Polishing, grinding, and honing can be used to achieve specific surface finishes.
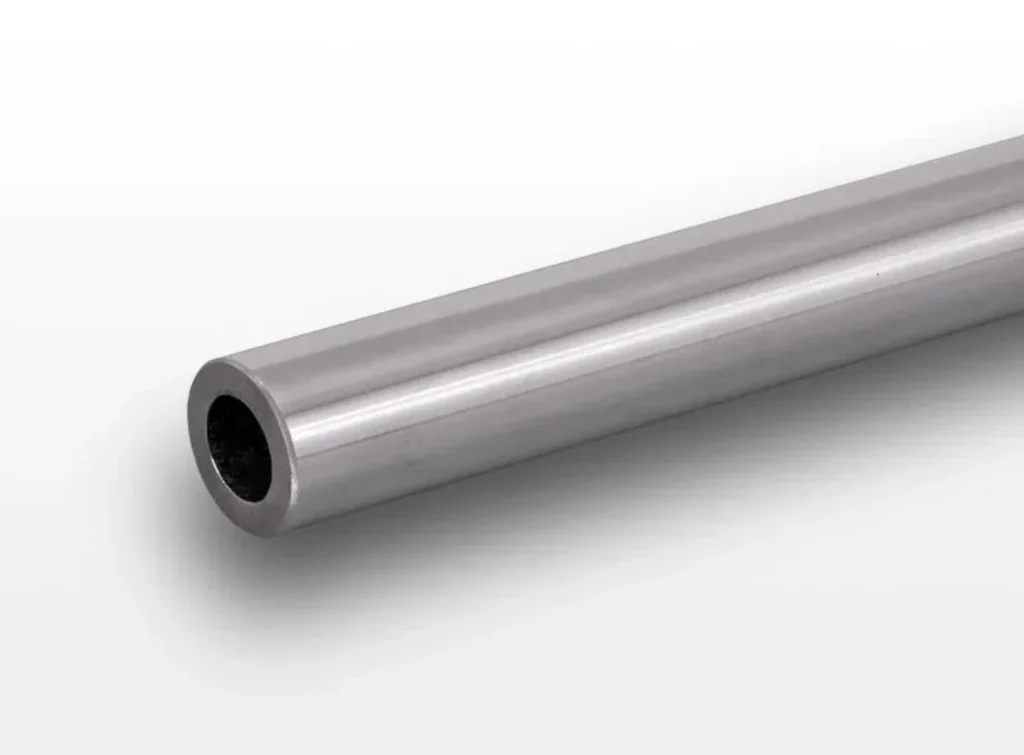
The Benefits of Lightweighting with Hollow Shafts
The move toward lightweighting, leveraging the design features of hollow shafts, brings significant advantages:
Improved Efficiency: Lower weight translates to reduced energy consumption, improving overall efficiency. This is particularly important in transportation and mobile equipment.
Enhanced Performance: Reduced inertia allows for faster acceleration and deceleration, improving system responsiveness and performance.
Reduced Stress: By reducing total weight, the stress on other mechanical components is minimized, resulting in longer service life.
Cost Savings: Although the initial cost of lightweight materials may be higher, the long-term cost savings from reduced energy consumption and improved performance can be significant.
Example Related Informations Sheet table
Property | Steel (AISI 1045) | Aluminum (6061-T6) | Stainless Steel (304) |
Tensile Strength | 600 MPa | 310 MPa | 520 MPa |
Yield Strength | 340 MPa | 276 MPa | 210 MPa |
Density | 7.85 g/cm³ | 2.70 g/cm³ | 8.00 g/cm³ |
Corrosion Resistance | Low | Medium | High |
Cost | Low | Medium | High |
Weight (per meter, 30mm OD, 5mm wall) | 2.75 kg | 0.945 kg | 2.8 kg |
Why Choose Welleshaft for Your 30mm Tubular Shaft Needs?
Welleshaft stands out as a trusted global supplier and contract manufacturer of high-quality 30mm tubular shafts. With years of experience and a commitment to excellence, Welleshaft offers:
Extensive Material Options: A wide range of steel, aluminum, stainless steel, and composite materials to choose from.
Custom Machining Capabilities: In-house machining capabilities to create custom shafts with keyways, splines, threads, and other features.
Precision Manufacturing: State-of-the-art equipment and skilled technicians ensure precise dimensions and tight tolerances.
Quality Control: Rigorous quality control procedures to guarantee consistent performance and reliability.
Global Reach: Worldwide shipping and support to meet the needs of customers around the globe.
Engineering Support: Experienced engineers to assist with material selection, design optimization, and application support.
Competitive Pricing: Cost-effective solutions to fit any budget.
Welleshaft excels in manufacturing precision shafts to customers’ exact specifications. Whether you need standard 30mm tubular shafts or highly customized solutions, Welleshaft can deliver high-quality products on time and within budget. Visit their website or contact them directly to discuss your specific requirements.
Conclusion
Lightweight 30mm tubular shafts offer a compelling combination of high strength, weight reduction, and functional versatility. Their hollow construction provides advantages in various applications, from robotics and automation to aerospace and medical devices. By carefully selecting materials, optimizing design, and leveraging customization options, engineers can harness the full potential of these shafts. With a trusted supplier like Welleshaft, organizations can acquire high-quality 30mm tubular shafts that meet their exact needs and contribute to improved performance, efficiency, and cost savings.