17-4PH Steel Fasteners for Aerospace & Marine
Section 1 Introduction
The aerospace and marine industries demand components that can withstand extreme environments and deliver unwavering performance. Among the critical elements of these structures are fasteners, and 17-4PH stainless steel stands out as a superior material choice. Its ability to combine high strength, exceptional corrosion resistance, and versatile heat treatment options make it ideal for the demanding requirements of aerospace and marine applications. This article will delve into the specifics of 17-4PH steel fasteners, focusing on their types, processing technologies, international material specifications, key characteristics, testing capabilities, heat and surface treatment options, and why Welleshaft is your trusted global supplier and contract manufacturer.
Section 2 Understanding 17-4PH Steel and Its Unique Properties
17-4PH stainless steel is a martensitic precipitation-hardening stainless steel. This means it combines the high strength of martensitic steels with the corrosion resistance of stainless steel, while also having the ability to undergo precipitation hardening. This hardening process is critical for enhancing its mechanical properties. This process makes it stronger and more resistant to corrosion than ordinary steels. Its nominal composition includes around 17% chromium, 4% nickel, and other alloying elements like copper and niobium, which are key to its performance. Its unique composition allows it to achieve a unique combination of mechanical properties after heat treatment, which makes it perfect for demanding applications.
Section 3 Types of 17-4PH Steel Fasteners
17-4PH steel can be formed into various types of fasteners, each designed for specific applications in aerospace and marine:
3.1 Bolts: Available in various head styles (hex, socket head, etc.) and thread types (UNC, UNF, metric), bolts are used for robust and reliable joining.
3.2 Screws: Self-tapping screws, machine screws, and set screws offer different fastening capabilities, and are available in multiple sizes and styles.
3.3 Nuts: Hex nuts, lock nuts, and flange nuts are available in 17-4PH and used in conjunction with bolts to secure connections.
3.4 Washers: Flat washers, lock washers, and spring washers distribute loads, prevent loosening, and are available in 17-4PH for optimal performance.
3.5 Studs: Threaded rods, often used with nuts to fasten materials.
Section 4 Processing Technologies for 17-4PH Fasteners
The manufacturing of 17-4PH fasteners involves several processing technologies, each contributing to the final quality:
4.1 Cold Heading: For smaller fasteners like screws and bolts, cold heading is a process used to form the metal into the desired shape at room temperature. This is a cost-effective process for high-volume production and ensures good mechanical properties.
4.2 Hot Forging: This process shapes the metal at high temperatures, primarily used for larger and more complex fasteners. It results in robust parts with high structural integrity.
4.3 Red Cutting: A method where excess material is removed from a part after an initial forming process.
4.4 Turning: Used for the precision machining of fastener threads and other fine features, turning ensures accurate dimensions. This is essential to ensure a proper fit and performance.
4.5 Threading: This process creates the helical threads required for many fasteners, ensuring consistent and reliable fastening. Threading can be done either by rolling or cutting.
Section 5 International Material Specifications for 17-4PH
17-4PH steel is produced to meet various international material specifications, which ensure consistency and quality:
5.1 ASTM A693: Standard specification for precipitation-hardening stainless and heat-resisting steel plate, sheet, and strip.
5.2 ASTM A564: Standard specification for hot-rolled and cold-finished age-hardening stainless steel bars and shapes.
5.3 AMS 5643: Aerospace material specification for 17-4PH corrosion resistant steel bars and forgings.
5.4 EN 1.4542 / Werkstoff 1.4542: The European standard for 17-4PH stainless steel.
5.5 UNS S17400: The Unified Numbering System designation for 17-4PH stainless steel.
These standards ensure consistent chemical composition, mechanical properties, and quality for materials used in demanding applications.
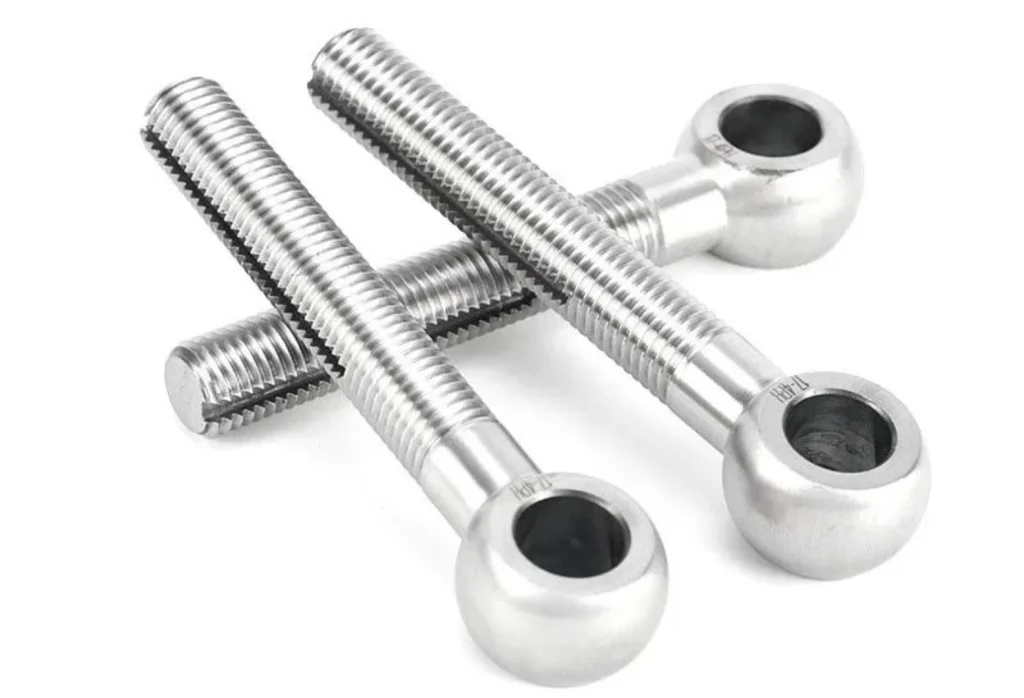
Section 6 Key Material Characteristics of 17-4PH
17-4PH is highly favored for its unique combination of properties:
6.1 High Tensile and Yield Strength: 17-4PH achieves very high strength after heat treatment, essential for withstanding high loads and stresses in aircraft and marine vessels.
6.2 Excellent Corrosion Resistance: Its high chromium content offers superior protection against pitting and crevice corrosion, vital in harsh marine and some aerospace environments.
6.3 Good Fatigue Strength: It has good resistance to repeated stresses from vibrations and cyclic loading.
6.4 High Hardness: Achieved through precipitation hardening, the hardness helps withstand demanding applications.
6.5 Good Impact Resistance: Resistance to impacts, vital for some components that are exposed to shock.
6.6 Dimensional Stability: Minimal changes in dimensions during hardening leading to high precision.
6.7 Temperature Performance: Usable in elevated and cryogenic temperatures
Section 7 Testing Capabilities for 17-4PH Fasteners
Rigorous testing is essential to verify the quality and reliability of 17-4PH fasteners. Common testing methods include:
7.1 Tensile Testing: Measures the tensile strength and yield strength of fasteners, ensuring they meet required specifications.
7.2 Hardness Testing: Determines the hardness of the material, confirming proper heat treatment.
7.3 Impact Testing: Checks the ability of the material to resist impact and shock.
7.4 Corrosion Testing: Salt spray and other tests verify resistance to corrosive environments.
7.5 Dimensional Inspection: Ensures that fasteners meet precise dimensional requirements.
7.6 Non-Destructive Testing (NDT): This includes methods like magnetic particle inspection (MPI) or dye penetrant inspection (DPI) to detect surface cracks and flaws.
7.7 Microstructural Analysis: Analysis of the grain structure of the material to ensure quality and to check for proper heat treatment.
Section 8 Heat Treatment Plan for 17-4PH Fasteners
The heat treatment plan for 17-4PH is essential to achieve its desired mechanical properties. Here is a simplified outline:
8.1 Solution Annealing: The material is heated to around 1040 °C (1900 °F) and then quenched, usually in water or oil. This makes the metal more machinable and also creates a more homogeneous structure.
8.2 Age Hardening: The material is heated to a lower temperature, usually between 480-620 °C (900-1150 °F) for a specified time. This allows the precipitation of copper-rich phases which leads to high strength and hardness.
8.3 Cooling: Controlled cooling to obtain the final product.
Adjustments to this process and the holding temperatures dictate specific material properties, including varying strength and hardness requirements.
Section 9 Surface Treatments for 17-4PH Fasteners
Surface treatments for 17-4PH fasteners include:
9.1 Passivation: This process removes surface contaminants and forms a protective layer of chromium oxide to improve corrosion resistance.
9.2 Dry Film Lubrication: Improves fastener performance by reducing friction, which increases the life of a fastener and makes installation easier.
9.3 Plating: Coatings such as zinc, nickel, or cadmium can be applied for additional corrosion protection and to provide other properties to the part.
9.4 Electropolishing: Improves corrosion resistance and removes surface defects via electrochemical means.
Section 10 The Role of 17-4PH in Aerospace & Marine
The demanding conditions of aerospace and marine applications require fasteners that can reliably perform, with 17-4PH being able to provide superior performance in these settings:
10.1 Aerospace Applications: 17-4PH fasteners are used in critical airframe, engine, control system, and interior assemblies due to their high strength and reliability.
10.2 Marine Applications: These fasteners provide the required strength and corrosion resistance for hull structures, deck fittings, propulsion systems, and offshore platforms.
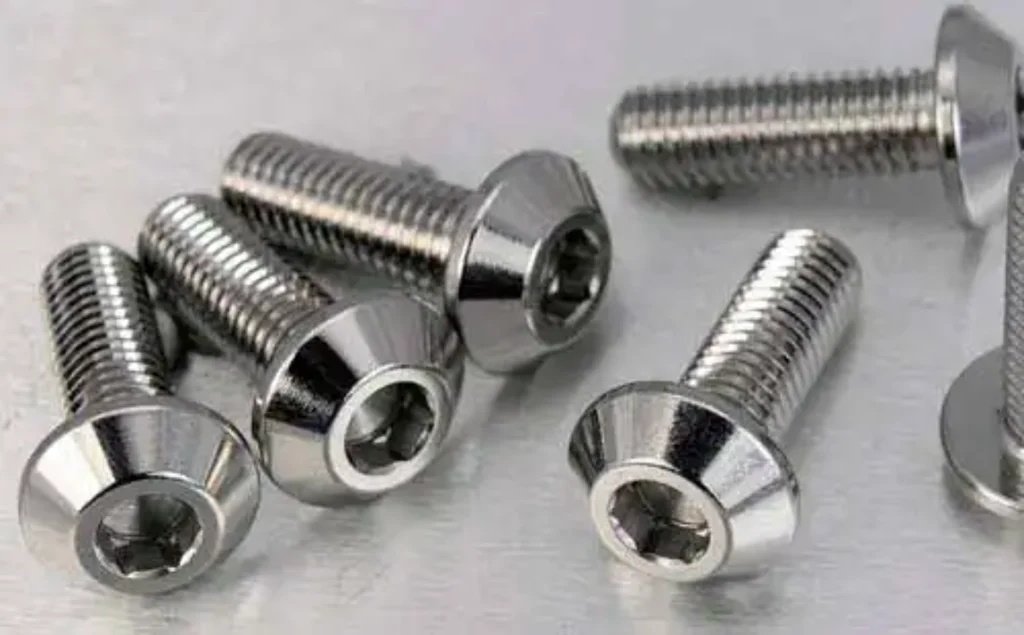
Section 11 The Importance of PH Stainless Steel Fasteners
As mentioned earlier, 17-4PH fasteners fall into the broader category of PH Stainless Steel Fasteners. These fasteners get their exceptional properties from the precipitation hardening process. This process allows the materials to achieve very high strength and also improves corrosion resistance. Other popular PH Stainless Steels are 15-5PH and 17-7PH, all of which find use in demanding applications. PH Stainless Steel Fasteners are also favored for the following reasons:
11.1 Superior Strength-to-Weight Ratio: Compared to other fasteners, PH Stainless Steel fasteners are able to maintain higher strength while being lower in weight.
11.2 Corrosion Resistance: The high levels of chromium and other alloying elements in PH Stainless Steels give them excellent resistance to corrosive environments.
11.3 Low Maintenance: Due to their robustness, PH Stainless Steel Fasteners have very low maintenance costs and requirements.
11.4 Wide Range of Applications: PH Stainless Steel Fasteners are favored for many applications in Aerospace, Marine, Nuclear, Chemical, Food, Medical, and other industries.
Section 12 17-4PH Fasteners in Aerospace Applications
In aerospace, fasteners must meet extremely stringent requirements for strength, reliability, and weight. 17-4PH steel fasteners are ideal for various critical aerospace components, including:
12.1 Airframe Structures: Wing assemblies, fuselage sections, and landing gear components require robust fasteners to withstand tremendous forces.
12.2 Engine Components: 17-4PH fasteners are used in engine assemblies due to their high-temperature resistance, strength, and fatigue resistance.
12.3 Control Systems: Components of flight control systems rely on high-precision, reliable fasteners to ensure safe and accurate operation.
12.4 Interior Assemblies: 17-4PH fasteners are also used in aircraft interiors to provide strong and durable connections.
Section 13 17-4PH Fasteners in Marine Applications
The marine environment poses significant challenges due to constant exposure to seawater, humidity, and the risk of corrosion. 17-4PH steel fasteners are chosen for their superior resistance to these conditions, and they are found in a range of marine applications:
13.1 Hull Structures: The high-strength and corrosion-resistant properties of 17-4PH are ideal for boat and ship hull assemblies.
13.2 Deck Hardware: 17-4PH fasteners are used in deck fittings, railing, and other hardware that is exposed to harsh marine conditions.
13.3 Propulsion Systems: Components of marine propulsion systems, like propellers and shaft connections, utilize 17-4PH for reliability and performance.
13.4 Offshore Structures: Oil rigs and other offshore structures rely on the strength and corrosion resistance of 17-4PH to withstand harsh conditions.
Section 14 Choosing the Right 17-4PH Fasteners
When selecting 17-4PH fasteners, it’s important to consider several factors:
14.1 Material Condition: Ensure the fasteners are properly heat-treated to achieve the required strength and hardness. The material can be obtained in the solution annealed “Condition A”, or in various “Condition H” states.
14.2 Size and Type: Choose the appropriate fastener size and type (bolts, screws, nuts, etc.) to meet the specific application requirements.
14.3 Thread Type: Select the correct thread type and tolerances for the application.
14.4 Corrosion Protection: Ensure additional corrosion protection is applied if necessary for extreme environments.
14.5 Supplier Certification: Only source from reputable suppliers with proper quality control and certification.
Section 15 Related Information Table
Property |
Typical Value (17-4PH) |
Notes |
Tensile Strength (Condition A) |
900 MPa |
Depends on heat treatment, Can go up to >1300 MPa after hardening |
Yield Strength (Condition A) |
620 MPa |
Depends on heat treatment, Can go up to >1100 MPa after hardening |
Elongation |
10-20% |
Varies depending on heat treatment |
Density |
7.8 g/cm³ |
Similar to other stainless steels |
Corrosion Resistance |
Excellent |
High resistance to pitting and crevice corrosion |
Heat Treatment |
Precipitation Hardening |
Solution annealed material requires age hardening for full properties. |
Common Application Temperature |
Up to 300 °C (570 °F) |
Specific temperature limits depend on grade and application |
Conclusion
17-4PH steel fasteners are essential components for aerospace and marine industries due to their unique combination of strength, corrosion resistance, and versatile performance. Understanding their types, processing technologies, material specifications, and testing is critical for selecting the right components. Partnering with a trusted global supplier and contract manufacturer like Welleshaft ensures you receive the highest quality 17-4PH fasteners. With Welleshaft, you can be assured that your fasteners will be reliable and high performing.