Precision Gear Broaching Services | Internal & External Gear Cutting
In the world of precision manufacturing, gears play a critical role. From automotive transmissions to aerospace components, the accuracy and quality of gears directly impact the performance and reliability of countless machines and systems. When it comes to producing gears with exceptional precision, intricate profiles, and high-volume efficiency, gear broaching emerges as a premier manufacturing process. This article dives deep into precision gear broaching services, exploring techniques, advantages, applications, and the importance of selecting a reliable partner for your gear manufacturing needs, focusing on Gear Broaching | Internal & External Gear Cutting.
What is Gear Broaching?
Gear broaching is a machining process that uses a specialized cutting tool called a “broach” to progressively remove material from a workpiece. A broach is a long, multi-tooth tool with each successive tooth slightly larger than the previous one. As the broach is forced linearly across or through the workpiece, each tooth takes a small cut, gradually shaping the desired form. Think of it as a series of tiny chisels working together to create a precise and intricate profile. This technique is fundamental in Gear Broaching | Internal & External Gear Cutting for producing accurate and complex gear shapes.
The Purpose and Advantages of Broaching Gears
The primary purpose of gear broaching is to create precise, complex gear tooth forms quickly and efficiently. Broaching offers several key advantages over other gear manufacturing methods like hobbing, shaping, or milling:
High Precision: Broaching excels at achieving tight tolerances and exceptional surface finishes, essential for optimal gear performance and longevity.
High Production Volume: Broaching is a fast process, allowing for high-volume production of gears at lower costs per part.
Complex Geometries: Broaching can create intricate internal and external gear profiles, including splines, keyways, and other complex features that would be difficult or impossible to produce using other methods.
Excellent Surface Finish: The progressive cutting action of a broach results in a smooth, consistent surface finish, reducing friction and wear in the finished gear.
Reduced Material Waste: Broaching is a relatively efficient process, minimizing material waste compared to some other machining methods.
Internal vs. External Gear Cutting
Broaching is particularly well-suited for both internal and external gear cutting:
Internal Gear Cutting: Broaching is often the preferred method for creating internal gears, especially those with complex tooth forms or tight tolerances. Internal gear broaching can produce features that are difficult or impossible to reach with traditional hobbing or shaping techniques.
External Gear Cutting: While hobbing and shaping are also common for external gears, broaching offers advantages in terms of speed, precision, and surface finish, particularly for high-volume production runs. Surface broaching can be used to create the entire gear tooth form, or profile broaching can be used to finish hobbed or shaped gears to achieve tighter tolerances and superior surface quality.
Types of Gear Broaching
Gear broaching can be classified based on the broach’s movement and the gear being produced:
Rotary Gear Broaching: In this process, the broach rotates as it cuts the gear teeth. This method is often used for high-volume production of gears.
Index Broaching: An indexing mechanism positions the gear blank precisely for each tooth-cutting pass. This method is suitable for creating gears with complex tooth forms and tight tolerances.
Surface Broaching: A flat broach is used to machine a flat surface on the workpiece. This method can be used to machine gear tooth profiles on external gears.
The Gear Broaching Process: A Step-by-Step Overview
The gear broaching process typically involves the following steps:
Prepare the workpiece by shaping the gear blank to the required dimensions and surface finish.
Select the appropriate broach based on the gear’s specifications, including tooth form, size, and material.
Set up the broaching machine with the correct broach and workpiece holding fixture.
Force the broach linearly across or through the workpiece, allowing each tooth to remove a small amount of material.
Apply coolant to the cutting area to lubricate the broach, remove heat, and flush away chips.
Inspect the finished gear to ensure it meets the required specifications.
Factors to Consider When Choosing a Gear Broaching Service
Selecting the right gear broaching service is critical for achieving the desired results. Consider the following factors:
Experience and Expertise: Look for a company with a proven track record of providing high-quality gear broaching services.
Equipment and Technology: Ensure that the company has state-of-the-art broaching machines and tooling.
Quality Control: The company should have a robust quality control system in place to ensure that all gears meet the required specifications.
Capacity: The company should have the capacity to handle your production volume requirements.
Material Capabilities: Ensure the company can work with the materials your gears require, such as steel, aluminum, or plastics.
Cost: Obtain competitive quotes from multiple providers.
Lead Time: Confirm the lead time for your project.
Communication: Ensure the company is responsive and communicative throughout the process.
Related Information Table
Category | Subcategory | Information |
Broaching Types | Internal Broaching | Creates internal features, like splines or internal gears, inside a workpiece. |
External Broaching | Creates external features, like gear teeth or flats, on the outside of a workpiece. | |
Surface Broaching | Broaching a flat surface on a component. | |
Gear Broaching | Gear Tooth Broaching | The direct creation of gear teeth using a broach. |
Profile Broaching | Used for finishing gear teeth after initial shaping, achieving higher precision. | |
Index Broaching | Gear blank is indexed to position the gear for each cutting path. | |
Process Variations | Progressive Cutting | Each tooth removes a slightly larger amount of material. |
Sequential Cutting | Broach is used multiple times to achieve the final profile. | |
Advantages | Precision | Capable of achieving tight tolerances and excellent surface finishes. |
Volume | Suitable for high-volume production runs. |
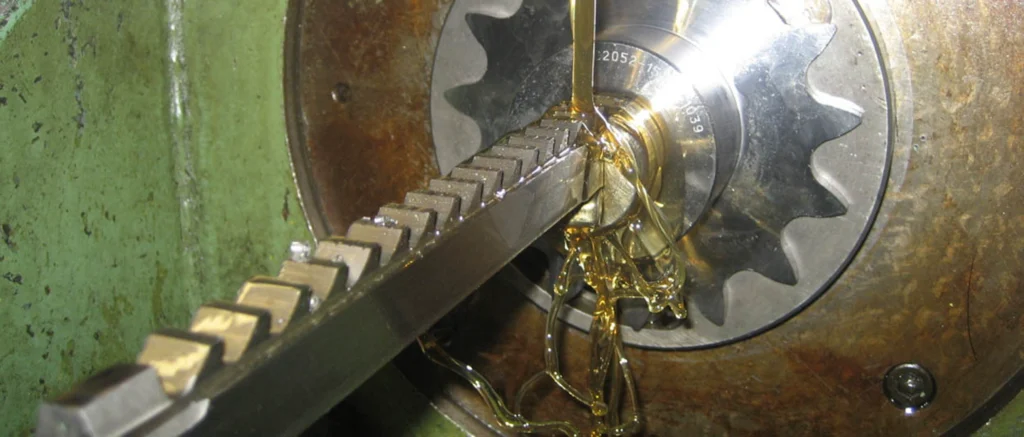
Gear Broaching Applications
Gear broaching finds applications across diverse industries, including:
Automotive: Transmissions, differentials, steering systems
Aerospace: Aircraft engines, gearboxes, control systems
Manufacturing: Machine tools, robotics, industrial equipment
Defense: Military vehicles, weapons systems
Medical: Surgical instruments, medical devices
The Future of Gear Broaching
The field of gear broaching continues to evolve, with advancements in broach design, machine technology, and process control. These advancements are leading to:
Increased Precision: Tighter tolerances and improved surface finishes
Higher Efficiency: Faster cycle times and reduced costs
Expanded Capabilities: The ability to create even more complex gear geometries
Automation: Integration with automated manufacturing systems for greater efficiency
Welleshaft: Your Trusted Partner for Precision Gear Broaching
When it comes to precision gear broaching services, Welleshaft stands out as a trusted global supplier and contract manufacturer. With years of experience, cutting-edge technology, and a commitment to quality, Welleshaft delivers exceptional gear solutions for a wide range of industries. Welleshaft offers a comprehensive suite of gear broaching services, including:
Internal and External Gear Broaching: Expertise in producing both internal and external gears to the highest standards.
Custom Broach Design and Manufacturing: Ability to design and manufacture custom broaches to meet specific requirements.
Material Expertise: Experience working with a wide range of materials, including steel, aluminum, brass, and plastics.
Comprehensive Quality Control: Rigorous quality control processes to ensure that all gears meet the required specifications.
Partnering with Welleshaft ensures we meet your gear broaching needs with the highest level of precision, quality, and efficiency.
Conclusion
Precision gear broaching is a critical manufacturing process for producing high-quality gears with complex geometries and tight tolerances. By understanding the principles of gear broaching, the different types of broaching, and the factors to consider when choosing a service provider, you can ensure that you select the right partner for your gear manufacturing needs. With its expertise, technology, and commitment to quality, Welleshaft is a trusted partner for precision gear broaching services, delivering exceptional solutions for a wide range of industries.