Technical Ceramics: Alumina for Electronics, Medical, and More
Technical ceramics have emerged as vital materials in a wide array of high-performance applications, and alumina (aluminum oxide) stands out as a key player among them. Its unique combination of properties makes it indispensable in electronics, medical devices, and beyond. This article delves into the world of alumina ceramics, exploring their properties, processing techniques, applications, and advantages, especially in the electronics and medical fields.
What are Technical Ceramics?
Engineers design technical ceramics as advanced ceramic materials with specific performance characteristics. Unlike traditional ceramics, manufacturers precisely control their composition, microstructure, and processing, resulting in enhanced mechanical, thermal, electrical, and chemical properties. Industries widely use alumina as one of the most versatile and cost-effective technical ceramics.
Why Alumina? Key Properties
Alumina ceramics offer a compelling array of properties that make them ideal for technical applications:
High Hardness and Wear Resistance: Alumina exhibits excellent resistance to abrasion and wear, making it suitable for components subjected to friction and erosion.
Excellent Electrical Insulation: Alumina is an excellent electrical insulator, crucial for electronic components and devices requiring electrical isolation.
High Mechanical Strength: Alumina possesses high compressive strength and flexural strength, enabling it to withstand significant loads and stresses.
Exceptional Chemical Inertness: Alumina is highly resistant to chemical attack, even at elevated temperatures, ensuring its integrity in harsh environments.
Good Thermal Conductivity: Alumina can dissipate heat effectively, making it suitable for heat sinks and thermal management applications.
Biocompatibility: Alumina is biocompatible and non-toxic, making it ideal for medical implants and devices that come into contact with bodily fluids and tissues.
High-Temperature Stability: Alumina can withstand high temperatures without significant degradation, suitable for applications where high heat is a factor.
Applications of Alumina Ceramics
Electronics:
Substrates for integrated circuits: Alumina provides a stable and insulating platform for mounting electronic components.
High-voltage insulators: Alumina’s electrical insulation properties make it ideal for high-voltage applications.
Electronic packaging: Alumina protects sensitive electronic components from environmental factors.
Capacitor components: Alumina is used as a dielectric material in capacitors.
Medical:
Orthopedic implants (hip and knee replacements): Alumina’s biocompatibility and wear resistance make it suitable for joint replacements.
Dental implants: Alumina provides a strong and biocompatible foundation for dental restorations.
Bioceramics: Alumina is used in various bioceramic applications due to its non-toxic and biocompatible nature.
Surgical instruments: Alumina’s hardness and sterilizability make it suitable for surgical instruments.
Aerospace and Defense:
High-temperature components: Manufacturers use alumina in rocket nozzles and other high-temperature applications because of its thermal stability.
Radomes: Alumina’s dielectric properties make it suitable for radomes, which protect radar antennas.
Armor: Alumina is used in body armor and vehicle armor due to its high hardness.
Industrial:
Cutting tools: Alumina-based cutting tools offer high hardness and wear resistance.
Industries use alumina to line pipes and other equipment with wear-resistant linings to protect them from abrasion.
They use alumina balls and powders as grinding media in various industrial processes.
Manufacturers include alumina as a key component in refractory materials to line furnaces and other high-temperature equipment.
Processing Alumina Ceramics
Manufacturing alumina ceramic components involves several key steps:
Powder Processing:
Raw Material Selection: High-purity alumina powder with controlled particle size distribution is crucial.
Milling and Mixing:Manufacturers mill the powder to achieve uniform particle size and mix it with binders and additives.
Forming:
Dry Pressing: Manufacturers compact the powder in a mold under high pressure to create a green body.
Isostatic Pressing: They apply uniform pressure to the powder in all directions, resulting in a more homogeneous green body.
Slip Casting: They pour a slurry of alumina powder into a porous mold and draw out the liquid, leaving behind a solid alumina body.
Extrusion: Manufacturers use extrusion to produce tubes and other geometrically simple shapes.
Injection Molding: They mix the powder with a binder and inject it into a mold under pressure.
Sintering:
Manufacturers heat the green body to a high temperature (typically 1400-1700°C) in a controlled atmosphere during high-temperature firing.
Sintering causes the alumina particles to bond together, increasing the density and strength of the ceramic.
They carefully control the sintering atmosphere to prevent oxidation or reduction of the alumina.
Machining and Finishing:
Manufacturers grind alumina ceramic parts to achieve precise dimensions and surface finishes.
They use fine abrasives to lap the ceramic parts, improving surface finish and flatness.
They polish alumina parts to create a smooth, reflective surface.
Technical Specifications
Property | Value | Test Method |
Density | 3.9 – 4.0 g/cm³ | ASTM C20 |
Hardness (Vickers) | 1100 – 1500 HV | ASTM C1327 |
Flexural Strength | 200 – 400 MPa | ASTM C1161 |
Compressive Strength | > 2000 MPa | ASTM C133 |
Thermal Conductivity | 20 – 30 W/m·K | ASTM E1225 |
Dielectric Strength | 10 – 15 kV/mm | ASTM D149 |
Dielectric Constant | 9 – 10 (at 1 MHz) | ASTM D150 |
Sintering Temperature | 1500 – 1700 °C | |
Grain Size | 1-10 µm (controlled by processing) | Microscopy |
Surface Finish (Ra) | Can be ground to < 0.1 µm, polished to < 0.01 µm | Profilometry |
Dimensional Tolerance | Can be machined to +/- 0.01 mm | Coordinate Measuring Machine |
Parts Processing and Processing Technology
Process | Description |
Powder Preparation | High-purity alumina powder is mixed with binders and additives to create a homogeneous mixture suitable for forming. This process involves milling, mixing, and granulation to ensure uniform particle size and distribution. |
Forming Methods | Various techniques are employed, including dry pressing (uniaxial or isostatic), slip casting, extrusion, and injection molding, depending on the part’s complexity and required properties. |
Sintering | Green bodies are subjected to high-temperature sintering in controlled atmospheres to achieve densification, grain growth, and desired mechanical and physical properties. Manufacturers optimize sintering parameters, such as temperature and time, to minimize porosity and maximize strength. |
Machining & Finishing | Alumina ceramics can be machined using diamond grinding, lapping, and polishing to achieve precise dimensions, smooth surfaces, and tight tolerances. These processes are crucial for applications requiring high precision and surface quality. |
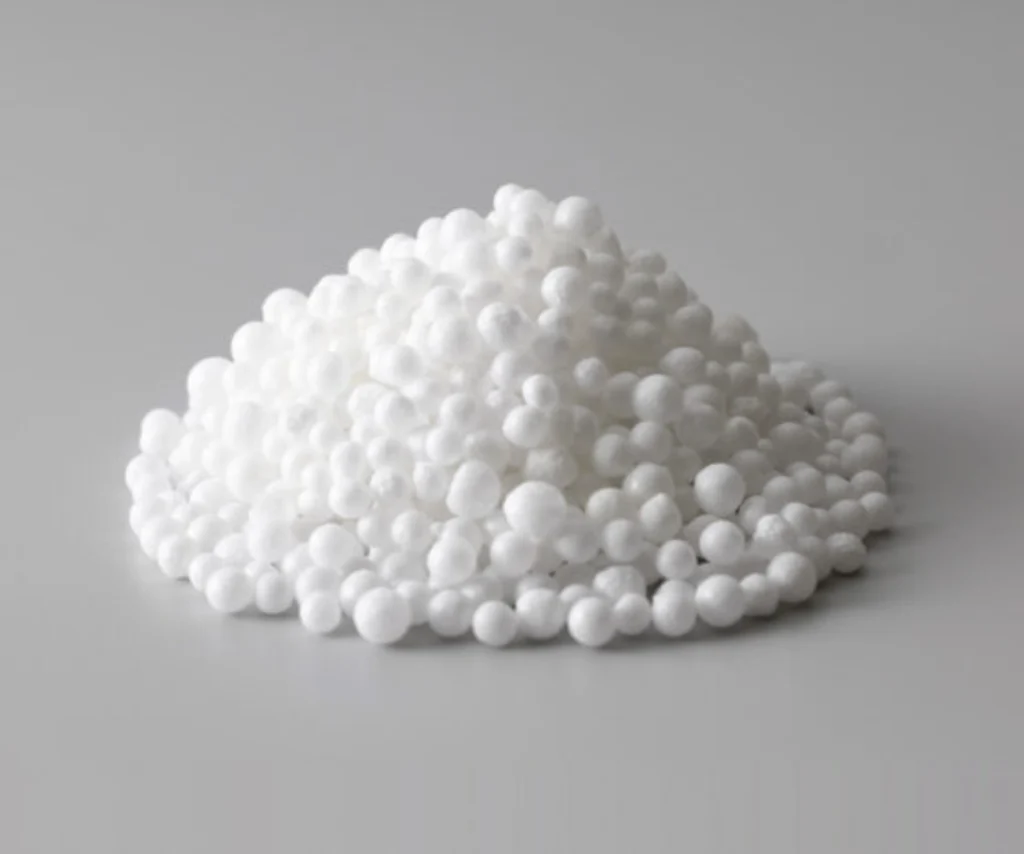
Alumina Ceramics: Dimensional Tolerance and Scope of Application
Feature | Alumina Tolerance Range | Scope of Application |
Dimensions | ±0.5% (typical), ±0.1% (precision machining) | Components requiring precise fit and integration in assemblies; electronics housings, medical implants |
Flatness | < 1 μm (lapping and polishing) | Substrates for microelectronics, sealing surfaces, high-precision instruments |
Surface Finish | Ra < 0.05 μm (polishing) | Optical components, wear-resistant parts, biocompatible surfaces |
Angle Accuracy | ±0.1° (precision machining) | High-precision fixtures, complex tooling |
Applications | Varies depending on the grade of material used | Components with a requirement for mechanical strengh, corrosion, chemical and high temperature resistance. |
Application Field
Field | Applications | Components Used | Requirements/Characteristics |
Electronics | IC Substrates, High Voltage Insulators | Insulators, Substrates, Packages | High electrical resistance, low dielectric loss, high strength |
Medical | Implants, Dental Restorations | Hip and Knee Replacements, Dental Implants | Biocompatibility, wear resistance, non-toxicity |
Aerospace | Radomes, High-Temperature Components | Radomes, Nozzles, Heat Shields | Thermal stability, high strength, low thermal expansion |
Automotive | Spark Plugs, Sensors | Insulators, Sensor Housings | Thermal shock resistance, chemical resistance |
Industrial | Cutting Tools, Wear Parts | Inserts, Liners, Seals | Wear resistance, hardness, high-temperature stability |
Welleshaft: Your Trusted Alumina Ceramic Partner
For high-quality alumina ceramic components, look no further than Welleshaft. We are a global supplier and contract manufacturer specializing in advanced ceramic materials. Welleshaft can help you design and manufacture components suitable for different application fields.
Why Choose Welleshaft?
Extensive Material Expertise: Deep understanding of alumina properties and processing techniques.
Custom Manufacturing Capabilities: Ability to produce parts with complex geometries and tight tolerances.
Quality Assurance: Rigorous quality control processes to ensure consistent performance.
Global Reach: Serving customers worldwide with reliable supply chain management.
Competitive Pricing: Providing cost-effective solutions without compromising on quality.
Conclusion
Alumina ceramics are essential materials in numerous technical applications, offering a unique combination of properties that enable high performance and reliability. From electronics and medical devices to aerospace and industrial equipment, alumina ceramics play a critical role in advancing technology. By partnering with a trusted supplier like Welleshaft, engineers and designers can leverage the full potential of alumina ceramics to create innovative and high-performing products.