Reliable Ceramic Component Grinding and Processing Services | Solving Your Machining Challenges
Section 1 Introduction
In today’s advanced engineering landscape, ceramic materials are increasingly vital for their exceptional properties: high hardness, thermal resistance, chemical inertness, and electrical insulation. However, these very attributes make them notoriously difficult to machine. The precision grinding and processing of ceramic components demand specialized expertise, cutting-edge equipment, and a deep understanding of material behavior. This article explores the challenges associated with ceramic machining and introduces a trusted solution: Welleshaft, a global leader in reliable ceramic component manufacturing. Whether you require tight tolerances, complex geometries, or customized material processing, Welleshaft is your go-to partner for overcoming your most demanding machining challenges.
Section 2 The Unique Challenges of Ceramic Machining
Ceramics, unlike metals, are brittle and possess limited tensile strength. This characteristic makes them highly susceptible to cracking, chipping, and surface damage during machining processes. Traditional metalworking techniques are often inadequate or even detrimental to ceramics. Furthermore, the extreme hardness of ceramics necessitates the use of specialized tooling and grinding processes with precise control parameters. The complexity deepens when considering the diverse range of ceramic materials available: aluminum oxide (alumina), zirconia, beryllium oxide, aluminum nitride, silicon nitride, gallium nitride, silicon carbide, machinable ceramics, and ceramic matrix composites, each with unique properties and machining requirements.
Here are some critical challenges engineers face when working with ceramics:
2.1 Maintaining Tight Tolerances: Achieving dimensional accuracy, often in the micrometer range, is paramount for ceramic components used in precision applications.
2.2 Surface Integrity: Scratches, micro-cracks, and residual stresses can significantly impact component performance and longevity.
2.3 Material Selection and Compatibility: Choosing the right ceramic material for a specific application and ensuring its compatibility with the chosen machining process is critical.
2.4 Tooling and Process Optimization: Finding the right tools, abrasive materials, grinding parameters, and coolant strategies to maximize efficiency and quality.
2.5 Complex Geometries: Machining intricate shapes and internal features without damaging the material requires sophisticated techniques and skilled operators.
2.6 Cost-Effectiveness: Developing cost-effective solutions without compromising on quality and precision is vital for high-volume production.
Section 3 Welleshaft: Your Partner in Ceramic Precision Machining
Welleshaft stands out as a premier global supplier and contract manufacturer specializing in solving complex ceramic machining challenges. Their integrated approach, coupled with decades of experience, ensures high-quality components tailored to meet even the most demanding specifications. They have developed innovative methods that address the key challenges in ceramic machining.
Welleshaft’s Key Strengths:
3.1 Cutting-Edge Technology: Welleshaft employs state-of-the-art CNC grinding, lapping, polishing, and ultrasonic machining equipment, designed specifically for ceramic materials.
3.2 Material Expertise: With extensive experience in machining a broad range of ceramics, including alumina, zirconia, silicon nitride, silicon carbide, beryllium oxide, and ceramic composites, Welleshaft possesses in-depth knowledge of their characteristics and machining requirements.
3.3 Customized Solutions: Welleshaft does not believe in a one-size-fits-all approach. They work closely with clients to understand their unique requirements and develop customized solutions.
3.4 Rigorous Quality Control: From raw material inspection to final component testing, Welleshaft employs stringent quality control measures to ensure dimensional accuracy, surface finish, and structural integrity.
3.5 Global Reach: As a leading global supplier and contract manufacturer, Welleshaft has the capability to handle both small prototype runs and large-scale production volumes, ensuring timely delivery.
3.6 Engineering Support: A dedicated team of experienced engineers provides comprehensive support, including material selection, design for manufacturability, and process optimization.
3.7 Testing Capabilities: Non-contact measurement, roughness measurement, 2D imager and other testing equipment can ensure high quality, high precision machining.
Section 4 Welleshaft Processing and Testing Capabilities
4.1 High-Precision Grinding: Using advanced CNC grinding machines with ultra-fine diamond and CBN wheels, Welleshaft achieves exceptionally tight tolerances and superior surface finishes.
4.2 Lapping and Polishing: Advanced lapping and polishing techniques are utilized to achieve mirror-like surface finishes for components requiring exceptional smoothness.
4.3 Ultrasonic Machining: Utilizing ultrasonic vibration machining for complex 3D shapes and fine structures, minimizing damage to brittle materials.
4.4 Non-destructive Testing: To ensure part quality, Welleshaft utilizes advanced non-destructive testing techniques such as microscopic inspection, visual inspection, surface roughness and profile measurements.
4.5 Dimensional Measurement: Sophisticated 2D imager equipment is used to conduct highly accurate dimensional measurements.
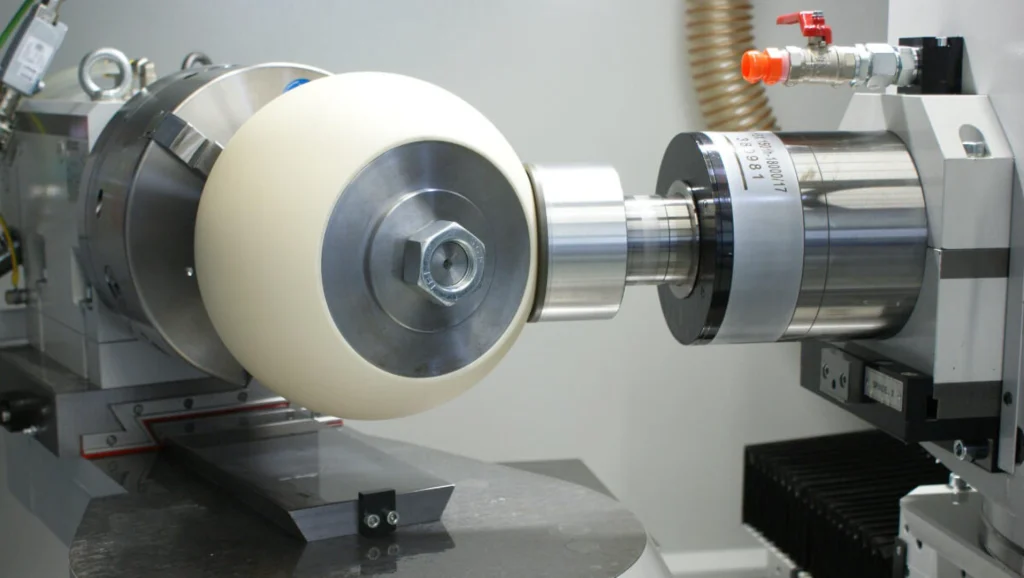
Section 5 Material Specifications and Manufacturing Parameters
Specification | Details |
Type | Precision ceramic component grinding and processing |
Manufacturing Requirements | High-precision grinding, lapping, polishing, ultrasonic machining |
Manufacturing Size Range (mm) | Diameter: 1≤1000 |
Height (mm) | ≤500 |
Manufacturing Accuracy (mm) | 0.001 |
Materials | Aluminum oxide, zirconia, beryllium oxide, aluminum nitride, silicon nitride, gallium nitride, silicon carbide, machinable ceramics, and ceramic matrix composites |
Surface Finish | Ra <0.01um |
Testing Equipment | Non-contact measurement, roughness measurement, 2D imager, etc. |
Section 6 Key Processes in Ceramic Component Grinding and Processing
Reliable ceramic component processing services encompass various techniques, often including:
6.1 Precision Grinding: This is the primary method for material removal and shaping, using abrasive wheels to achieve the desired dimensions and surface finish. Different grinding methods include surface grinding, cylindrical grinding, and centerless grinding.
6.2 Lapping and Polishing: These finishing techniques are used to achieve extremely smooth surface finishes, often down to nanometer levels. They remove minor surface imperfections left by grinding.
6.3 Ultrasonic Machining: Uses high-frequency sound waves to remove material, suitable for cutting complex shapes in hard and brittle materials.
6.4 Laser Machining: Utilizes high-energy lasers for cutting, drilling, or etching ceramics, suitable for producing very fine features.
6.5 Honing: A precision abrasive machining process used to refine surface finish and geometrical accuracy by removing material with very low speeds.
Section 7 Choosing the Right Ceramic Component Machining Partner
Selecting the right partner for ceramic component machining is crucial for success. Consider the following factors:
7.1 Experience and Reputation: Look for a provider with a proven track record in processing various ceramic materials.
7.2 Equipment Capabilities: Ensure they have the necessary machinery and equipment for the specific grinding and processing techniques you need.
7.3 Quality Control Processes: Inquire about their quality assurance procedures and certifications.
7.4 Customer Service and Communication: Choose a provider that offers responsive and transparent communication throughout the process.
7.5 Lead Times and Pricing: Verify their lead times and pricing structure to meet your project needs and budget.
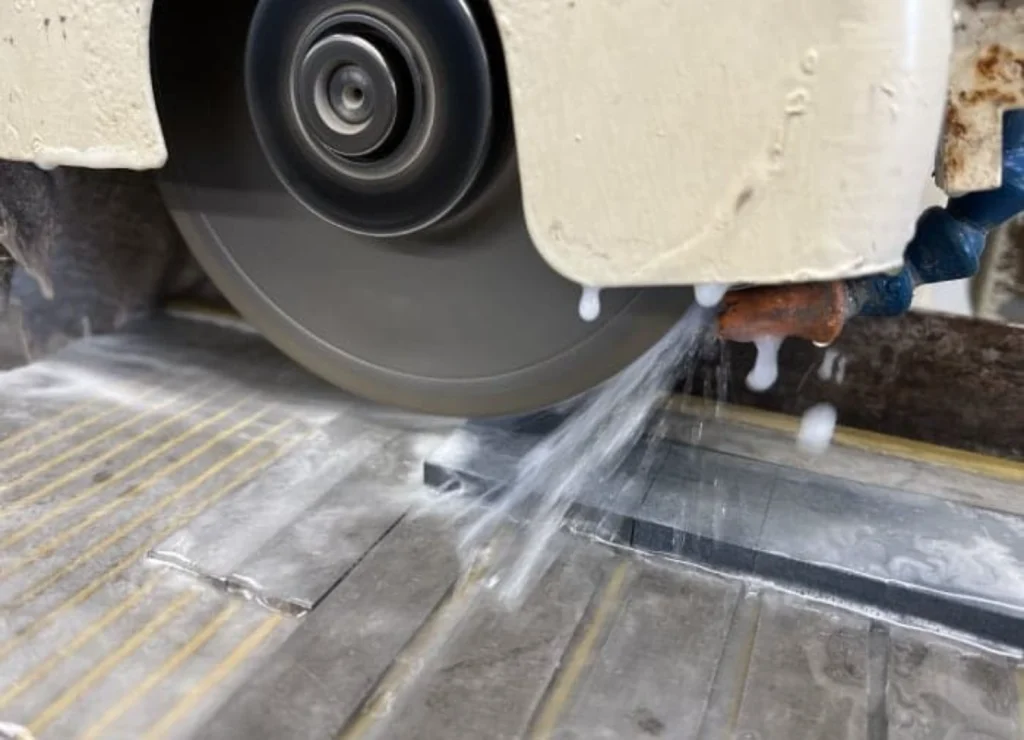
Section 8 Key Considerations for Ceramic Component Grinding and Processing
Characteristic | Description | Importance |
Material Type | Different ceramics (e.g., Alumina, Zirconia, Silicon Carbide) require specific processing parameters. | Selection of correct grinding wheels and parameters to prevent surface defects. |
Component Geometry | Intricate shapes and fine details demand precise machinery and skilled operators. | Ensures the components meet the intended designs and specifications. |
Surface Finish | The desired surface quality is a key factor in determining the chosen finishing techniques. | Influences component performance (e.g., friction reduction, sealing capabilities). |
Dimensional Accuracy | High-precision ceramic components necessitate tight tolerance control during processing. | Crucial for proper fit and function within the final assembly. |
Production Volume | Whether you need prototypes, small batches, or large volumes affects the chosen processing approach. | Affects cost-effectiveness, scalability and process planning. |
Grinding Wheel Choice | Appropriate abrasive wheels are essential to remove material without introducing cracks and defects. | Selecting the right wheel is crucial for efficient and accurate grinding. |
Coolant | Use of proper coolants helps to dissipate heat and minimizes thermal stress in components. | Prevents overheating, which can induce defects. |
Feed Rates and Speeds | Proper adjustment of feed rates and speeds reduces the possibility of chipping or fracturing during grinding. | Optimizes material removal while ensuring quality. |
Section 9 Applications of High-Precision Ceramic Components
The versatility of ceramic materials, coupled with Welleshaft’s precision machining capabilities, enables components used across a wide range of applications. Here are a few examples:
9.1 Semiconductor Manufacturing: Ceramic components are crucial for thermal management, wafer handling, and gas distribution in semiconductor processing equipment.
9.2 Aerospace: Ceramic parts are valued for their lightweight, high-temperature strength and wear resistance for engines, sensors, and thermal protection systems.
9.3 Medical Devices: Biocompatible ceramics play a vital role in prosthetics, implants, and surgical instruments.
9.4 Automotive: Ceramic parts are used in sensors, engine components, and brake systems to enhance performance and efficiency.
9.5 Telecommunications: Ceramic substrates and housings provide high-frequency insulation and thermal stability for communication devices.
9.6 Industrial Equipment: Ceramic components offer wear resistance, corrosion resistance, and precise dimensions for pumps, valves, and bearings.
9.7 Optical Instruments: Ceramics contribute to high precision and minimal wear in optical systems such as lenses and mirrors.
9.8 High-Frequency RF: Ceramic components with excellent dielectric properties are used in high-frequency applications like satellite communication, radar system and high-frequency medical devices.
9.9 Oil and Gas: Ceramic components are used in harsh conditions for their chemical inertness and wear resistance in pumps, valves and flow control.
Section 10 Why Choose Welleshaft?
Partnering with Welleshaft for your ceramic component grinding and processing needs provides numerous advantages:
10.1 Reduced Costs: Welleshaft helps clients achieve cost-effective solutions by optimizing material usage, improving manufacturing processes, and minimizing waste.
10.2 Faster Turnaround Times: Welleshaft ensures timely completion of your projects by utilizing efficient production planning and experienced operators.
10.3 Higher Quality: With advanced equipment and meticulous quality control, Welleshaft delivers precision-engineered ceramic components that meet or exceed stringent quality standards.
10.4 Reduced Risk: By leveraging Welleshaft’s expertise in ceramic machining, clients minimize the risk of costly errors and project delays.
10.5 Peace of Mind: Welleshaft handles all aspects of the ceramic machining process from design to final testing, allowing you to focus on your core competencies.
10.6 Reliable Supplier: Welleshaft is a global leader in ceramic component manufacturing with decades of experience and a strong track record of successful projects.
10.7 Integrated Approach: Welleshaft’s integrated approach, including process design, tooling, machining, cleaning, finishing and metrology ensures all critical steps are considered to meet requirements.
10.8 Engineering Support: Welleshaft’s engineers provide valuable assistance during design, material selection, process optimization and even failure analysis.
Conclusion
Ceramic component grinding and processing require specialized expertise and advanced equipment, not available to every machining facility. Welleshaft has made it their mission to overcome these challenges and deliver high-quality ceramic components that meet even the most stringent demands. With a dedication to innovation, quality, and customer satisfaction, Welleshaft is your trusted partner for reliable, precise, and cost-effective ceramic machining solutions. Whether you require small prototype runs or high-volume production, you can rely on Welleshaft to provide exceptional components tailored to your specific application. Contact Welleshaft today to discuss your next project and experience the difference in ceramic machining excellence.